簡介
煤高壓加氫工藝可分為煤高壓加氫液化和煤高壓加氫氣化。其中,煤的氣化在煤化工中占有重要地位,用於生產各種氣體燃料,是潔淨的能源,有利於提高人民生活水平和環境保護;煤氣化生產的合成氣是合成液體燃料、化工原料等多種產品的原料。煤直接液化,即煤高壓加氫液化,可以生產人造石油和化學產品。在石油短缺時,煤的液化產品將替代天然石油。
煤高壓加氫液化
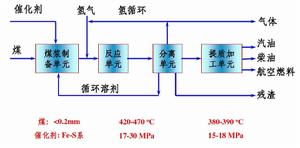
煤高壓加氫液化是指在較高溫度(>400℃)、高壓(>6MPa)、氫氣(或CO+H、CO+HO)、催化劑和溶劑作用下將煤進行解聚、裂解加氫,直接轉化為液體油的加工過程。
煤高壓加氫液化機理:煤與石油在化學組成上最明顯的差別是煤的氫含量低、氧含量高,即H/C原子比低、O/C原子比高。兩者的分子結構也不同,煤有機質是由2~4個或更多的芳香環構成、呈空間立體構造的高分子縮聚物,且煤中存在大量無機礦物;石油主要是由烷烴、芳烴和環烷烴等烴類化合物組成的混合物。因此,將煤轉化為液體產物,只需要將煤的大分子縮聚物裂解為較小的分子,提高其H/C原子比,降低O/C原子比,並脫除礦物質即可。
煤高壓加氫氣化
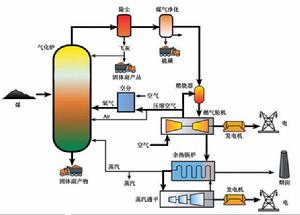
煤高壓加氫氣化是指在一定溫度(800~1000℃)和壓力(3~10MPa)條件下,將粉煤和氫氣同時加入氣化爐內,依靠氫氣對煤熱解階段釋放自由基的穩定作用和氣化階段與半焦中活性的碳的反應得到富含甲烷的氣體,以及高附加值的BTX(苯、甲苯、二甲苯)和PCX(苯酚、甲酚、二甲酚)等液態有機產品。
煤高壓加氫氣化以煤和氫氣為原料,在高溫高壓的條件下反應,其產物中甲烷濃度高,減少了進一步提升甲烷濃度的工作量; 煤高壓加氫氣化反應過程的能源利用效率較高,其熱效率接近80%,而且在生產天然氣的過程中只排放較少的CO,因此,煤加氫氣化是一種比較理想的煤制天然氣技術。
煤高壓加氫氣化包括煤在氫氣氣氛下的熱分解和煤焦與氫氣的氣化反應兩個過程。氫氣氣氛下煤受熱分解產生的揮發分自由基和分子碎片與氫結合被穩定化,從而更容易從顆粒內部逃逸,與惰性氣氛相比,氣體和焦油的產率提高,特別是CH4的產率提高了。另外,煤脫揮發分後形成的半焦具有較高的活性,使煤焦加氫氣化經歷一個初始反應速率較高的階段,而且煤焦加氫氣化反應速率隨著煤焦活性的降低而逐漸減小。其中,氫氣壓力是影響煤加氫氣化過程的重要因素,提高氫氣壓力能使揮發分總產率和焦油產率增加。
煤高壓加氫工藝發展情況
煤炭高壓加氫液化早在20世紀30年代首先在德國實現了工業化,進入20世紀50年代,由於石油的大量開採以及工業化套用,煤液化工業曾一度中斷;直到1973年,西方世界爆發了“石油危機”後,德國、美國、英國及日本等已開發國家又開始了對煤液化技術的研究和開發,比較典型的工藝有:德國液化新工藝(IGOR),美國溶劑精練法Ⅰ和Ⅱ,氫煤法(H-Coal),供氫溶劑法(EDS),HTI工藝,日本的NEDOL工藝以及煤油共煉(UOP)工藝等。我國煤炭液化的研究工作始於20世紀50年代,在1978年國家科委將其列入“六五”、“七五”攻關項目之後,煤炭科學研究總院和國內有關大學開展了煤的直接液化技術研究。二十多年來,通過國際合作引進了三套煤直接液化連續實驗裝置,進行了中國煤種的液化特性評價和煤液化工藝技術研究,取得了一批具有先進水平的研究成果。
煤高壓加氫氣化技術經歷了近半個世紀的時間,從美國的IGT流化床工藝發展到日本的ARCH氣流床氣化工藝。IGT採用4段流化床進行煤加氫氣化反應,在低溫段實現煤的裂解,高溫段實現半焦的加氫氣化,但是由於流化床本身對原料粒度的限制,導致加氫氣化反應速度較慢,煤粉在爐內易發生粘聚而失流態化。Rockwell公司採用了氣流床反應器進行煤加氫氣化,克服了煤粉粘聚的現象,但是氫氣的預熱需要消耗大量的氧氣,同時水蒸氣的製備也耗資很大。日本大阪煤氣公司與英國煤氣公司聯合開發的BG-OG煤加氫氣化工藝採用帶氣體循環的氣流床加氫氣化反應器,氣體的快速循環,煤和氫反應釋放的熱量充分用於氫氣的預熱,不需要氧氣和氫氣部分燃燒預熱氫氣,減少了氫氣的消耗,降低了設備成本,但是帶氣體循環的爐型結構複雜,工業規模下氣體循環所需驅動力大,依靠氣體噴入的動量能否實現所需循環比仍需要進一步試驗進行驗證。