工藝流程
直接淬火低溫回火
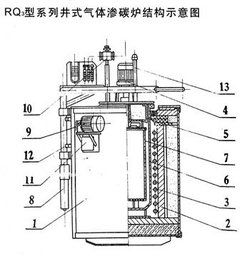
組織及性能特點:不能細化鋼的晶粒。工件淬火變形較大,合金鋼滲碳件表面殘餘奧氏體量較多,表面硬度較低
適用範圍:操作簡單,成本低廉用來處理對變形和承受衝擊載荷不大的零件,適用於氣體滲碳和液體滲碳工藝。
預冷直接淬火低溫回火
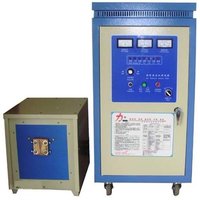
淬火溫度800-850℃ 。組織及性能特點:可以減少工件淬火變形,滲層中殘餘奧
氏體量也可稍有降低,表面硬度略有提高,但奧氏體晶粒沒有變化。
適用範圍:操作簡單,工件氧化、脫碳及淬火變形均小,廣泛套用於細晶粒鋼製造的各種工具。
一次加熱淬火低溫回火
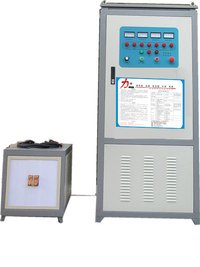
淬火溫度820-850℃或780-810℃ 。組織及性能特點:對心部強度要求較高者,採用820-850℃淬火,心部為低碳M,表面要求硬度高者,採用780-810℃淬火可以細化晶粒。
適用範圍: 適用於固體滲碳後的碳鋼和低合金鋼工件、氣體、液體滲碳的粗晶粒鋼,某些滲碳後不宜直接淬火的工件及滲碳後需機械加工的零件。
滲碳高溫回火,一次加熱淬火,低溫回火
淬火溫度840-860℃ 。組織及性能特點:高溫回火使M和殘餘A分解,滲層中碳和合金元素以碳化物形式析出,便於切削加工及淬火後殘餘A減少。
適用範圍:主要用於Cr—Ni合金滲碳工件
二次淬火低溫回火
組織及性能特點:第一次淬火(或正火),可以消除滲碳層網狀碳化物及細化心部組織(850-870℃),第二次淬火主要改善滲層組織,對心部性能要求不高時可在材料的Ac1—Ac3之間淬火,對心部性能要求高時要在Ac3以上淬火。
適用範圍:主要用於對力學性能要求很高的重要滲碳件,特別是對粗晶粒鋼。但在滲碳後需經過兩次高溫加熱,使工件變形和氧化脫碳增加,熱處理過程較複雜。
二次淬火冷處理低溫回火
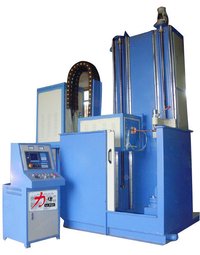
組織及性能特點:高於Ac1或Ac3(心部)的溫度淬火,高合金表層殘餘A較多,經冷處理(-70℃/-80℃)促使A轉變從而提高表面硬度和耐磨性。
適用範圍:主要用於滲碳後不進行機械加工的高合金鋼工件。
滲碳後感應加熱淬火低溫回火
組織及性能特點:可以細化滲層及靠近滲層處的組織。淬火變形小,不允許硬化的部位不需預先防滲。
適用範圍:各種齒輪和軸類
發展趨勢
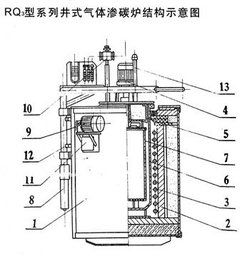
滲碳工藝是一個十分古老的工藝,在中國,最早可上溯到2000年以前。起先是用固體滲碳介質滲碳。在20世紀出現液體和氣體滲碳並得到廣泛套用。後來又出現了真空滲碳和離子滲碳。到現在,滲碳工藝仍然具有非常重要的實用價值,原因就在於它的合理的設計思想,即讓鋼材表層接受各類負荷(磨損、疲勞、機械負載及化學腐蝕)最多的地方,通過滲入碳等元素達到高的表面硬度﹑高的耐磨性和疲勞強度及耐蝕性﹐而不必通過昂貴的合金化或其它複雜工藝手段對整個材料進行處理。這不僅能用低廉的碳鋼或合金鋼來代替某些較昂貴的
高合金鋼,而且能夠保持心部有低碳鋼淬火後的強韌性﹐使工件能承受衝擊載荷。因此,完全符合節能、降耗,可持續發展的方向。
近年來,出現了高濃度滲碳工藝,與傳統工藝在完全奧氏體區(溫度在900~950℃,滲碳後表面碳質量分數為0.85%~1.05%)進行滲碳不同,它是在Ac1~Accm之間的不均勻奧氏體狀態下進行,其滲層表面碳濃度可高達2%~4%。其結果可獲得細小顆粒碳化物均勻、彌散分布的滲層。其滲碳溫度降至800℃~860℃溫度範圍,可實現一般鋼材滲碳後直接淬火;由於高濃度滲碳層含有很高數量(20%~50%)的彌散分布的碳化物,故顯示出比普通滲碳更優異的耐磨性、耐蝕性,更高的接觸與彎曲疲勞強度,較高的衝擊韌度、較低的脆性及較好的回火穩定性。該工藝還具有適用性廣、對設備無特殊要求等優點,具有較高的經濟效益和實用價值,近年來在國內外獲得競相研究與開發。
為了防止滲碳過程中奧氏體晶粒的粗化,一般都在鋼材中添加適量的鈦,通過形成碳氮化鈦粒子釘扎晶界而阻止晶粒長大。國家標準規定滲碳鋼中鈦添加量為0.04~0.08wt%。然而,最近有研究工作表明,當鈦含量超過0.032%,就會在滲碳鋼冶煉鑄錠凝固時析出氮化鈦。這種氮化鈦尺寸達到微米數量級,起不到阻止奧氏體晶粒長大的作用,反而由於這種呈立方體的粒子的尖角效應以及與基體組織的不連續性而成為微裂紋的策源地和裂紋擴展的中繼站,嚴重損害鋼材的韌塑性。工作還表明,將鈦含量降至0.02~0.032%,仍然能夠同樣有效地起到控制奧氏體晶粒長大的作用,而又可避免有害氮化鈦粒子的形成,因此是值得推薦的合理的選擇範圍。
常見缺陷
碳濃度過高
⒈產生原因及危害:如果滲碳時急劇加熱,溫度又過高或固體滲碳時用全新滲碳劑,或用強烈的催滲劑過多都會引起滲碳濃度過高的現象。隨著碳濃度過高,工件表面出現塊狀粗大的碳化物或網狀碳化物。由於這種硬脆組織產生,使滲碳層的韌性急劇下降。並且淬火時形成高碳馬氏體,在磨削時容易出現磨削裂紋。
⒉防止的方法
①不能急劇加熱,需採用適當的加熱溫度,不使鋼的晶粒長大為好。如果滲碳時晶粒粗大,則應在滲碳後正火或兩次淬火處理來細化晶粒。
②嚴格控制爐溫均勻性,不能波動過大,在反射爐中固體滲碳時需特別注意。
③固體滲碳時,滲碳劑要新、舊配比使用。催滲劑最好採用4—7%的BaCO3,不使用Na2CO3作催滲劑。
碳濃度過低
⒈產生的原因及危害:溫度波動很大或催滲劑過少都會引起表面的碳濃度不足。最理想的碳濃度為0.9—1.0%之間,低於0.8%C,零件容易磨損。
⒉防止的方法:
①滲碳溫度一般採用920—940℃,滲碳溫度過低就會引起碳濃度過低,且延長滲碳時間;滲碳溫度過高會引起晶粒粗大。
②催滲劑(BaCO3)的用量不應低於4%。
滲碳後表面局部貧碳
⒈產生的原因及危害:固體滲碳時,木炭顆粒過大或夾雜有石塊等雜質,或催滲劑與木炭拌得不均勻,或工件所接觸都會引起局部無碳或貧碳。工件表面的污物也可以引起貧碳。
⒉防止的方法
①固體滲碳劑一定要按比例配製,攪拌均勻。
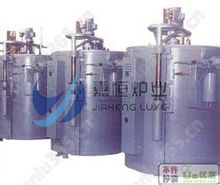
②裝爐的工件注意不要有接觸。固體滲碳時要將
滲碳劑搗實,勿使滲碳過塌而使工件接觸。
③卻除表面的污物。
滲碳濃度加劇過渡
⒈產生的原因及危害:滲碳濃度突然過渡就是表面與中心的碳濃度變化加劇,不是由高到低的均勻過渡,而是突然過渡。產生此缺陷的原因是滲碳劑作用很強烈(如新配製的木炭,舊滲碳劑加得很少),同時鋼中有Cr、Mn、Mo等合金元素是促使碳化物形成強烈,而造成表面高濃度,中心低濃度,並無過渡層。產生此缺陷後造成表里相當大的內應力,在淬火過程中或磨削過程中產生裂紋或剝落現象。
⒉防止的方法:滲碳劑新舊按規定配比制,使滲碳緩和。用BaCO3作催滲劑較好,因為Na2CO3比較急劇。
磨加工時產生回火及裂紋
⒈產生的原因:滲碳層經磨削加工後表面引起軟化的現象,稱之為磨加工產生的回火。這是由於磨削時加工進給量太快,砂輪硬度和粒度或轉速選擇不當,或磨削過程中冷卻不充分,都易產生此類缺陷。這是因為磨削時的熱量使表面軟化的緣故。磨削時產生回火缺陷則零件耐磨性降低。
表面產生六角形裂紋。這是因為用硬質砂輪表面受到過份磨削,而發熱所致。也與熱處理回火不足,殘餘內應力過大有關。用酸浸蝕後,凡是有缺陷部位呈黑色,可與沒有缺陷處區別開來。這是磨削時產生熱量回火。使馬使體轉變為屈氏體組織的緣故。其實,裂紋在磨削後肉眼即可看見。
⒉防止的方法:
①淬火後必須經過充分回火或多次回火,消除內應力。
②採用40~60粒度的軟質或中質氧化鋁砂輪,磨削進給量不過大。
③磨削時先開冷卻液,並注意磨削過程中的充分冷卻
注意事項
(1)滲碳前的預處理正火--目的是改善材料原始組織、減少帶狀、消除魏氏組織,使表面粗糙度變細,消除材料流線不合理狀態.正火工藝;用860--980C空冷、179--217HBS.
(2)滲碳後需進行機械加工的工件,硬度不應高於30HRC.
(3)對於有薄壁溝槽的滲碳淬火零件,薄壁溝槽處不能先於滲碳之前加工.
(4)不得用鍍鋅的方法防滲碳.