發展過程
串聯耗能滅磁
磁最初就是直接利用耗能開關吸收發電機轉子中儲存的能量。比如俄羅斯生產的耗能開關利用弧間隔燃燒來耗能。但是這種方式存在如下缺點:
a.體積大
b.不易維護
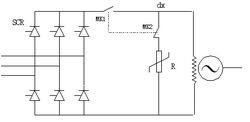
c.滅磁成功與否取決於弧的形成
d.容易引起事故
e.產品根據發電機機組容量需要特殊訂製,不易規模化,系列化
由於這些缺點的存在,採用耗能開關的滅磁方式逐漸被並聯移能滅磁方式代替。
機械開關並聯移能滅磁
機 械開關串聯於勵磁主迴路、滅磁耗能電阻並聯在轉子兩端是這類滅磁的接線方式。
ANSI/IEEEC37.18-1979標準規定,一般機械開關需要有至少一對主觸頭(MK1)、一對滅磁常閉觸頭(MK2)。20年來,隨著國內ZnO電阻耗能在滅磁系統中的套用,滅磁觸頭也並非必要了。但值得注意的是,在不採用滅磁觸頭的滅磁系統中,需認真核算ZnO的滅磁殘壓與荷電率。
這類滅磁方式在國內是主要的滅磁方式。主迴路有明顯的開斷觸頭,在勵磁系統內部故障時,可以開斷勵磁主迴路,切斷故障源,快速地消滅發電機主磁場,將發電機損失控制在最小範圍內。目前使用的機械開關主要有DM2、DM4、DMX、E3H、E4H、UR、PHB、MM74、CEX等。
這類滅磁方式的主要問題是滅磁開關選型比較困難。小機組選大的開關,成本比較高;選小開關滿足不了工況要求;大型尤其是巨型水力發電機機組開關選擇更為困難。
電子開關並聯移能滅磁
前 些年,國內一些廠家將滅磁開關建壓任務轉移到電力電子器件上來。其原理是利用電容的放電過程,使可控矽的電流降到零,並形成反壓使之關斷。
這類方式下開關動作時間短,因此開關在開斷過程中所需遮斷能容就小,並且建壓速度快,利於快速滅磁。但其缺點是開關動作的可靠性取決於電子迴路工作的可靠性。
與機械開關比較它沒有觸頭磨損,易於維護,成本也低。但目前在大電流系統中不宜採用。它存在兩個問題:發熱問題及器件選型問題。然而值得注意的是,隨著電力電子器件的快速發展,高電壓大電流的全控器件也會在不久投入商業運行。電力電子器件將在滅磁中發揮更大的作用。但是長期通流帶來的發熱仍是採用這種方法需解決的首要問題。
為克服上述兩種滅磁方式的缺點,人們開始在材料科學領域探索,尋找一種既不發熱,又可以建壓的材料。將PTC電阻或鉬棒與開關並聯,利用材料在溫度升高時電阻急劇增加的特點,建立比較高的電壓,打通滅磁電阻迴路,實現滅磁。也可以採用超導材料串入迴路,在需要滅磁時使超導材料失超。但是若要建立比較高的電壓,超導體的長度相應比較長,體積比較大。
由於以上滅磁方式的缺陷,業內人士希望能夠將可控矽整流橋直接關斷,將機械開關移至勵磁變低壓側。這樣解決了勵磁系統具有明顯開路點的問題、又解決了機械並聯滅磁方式開關難選擇的問題。
交流滅磁
與水輪發電機相比,滅磁對於汽輪發電機要相對容易一些。主要因為轉子電感值較小,阻尼繞組作用比較明顯,因此交流滅磁在汽輪發電機勵磁系統套用較多。交流滅磁是將直流開關難開斷、難建壓的問題轉移到勵磁源的交流側。
交流滅磁是利用可控矽陽極電源負半周輔助實現的一種滅磁方式,交流滅磁勵磁電壓波形如圖4-4所示。滅磁開關既可以安裝在交流側也可以安裝在直流側,但都必須配合封脈衝的措施(由於交流滅磁開關跳開過程中同步電源缺相而導致的自動封鎖脈衝等效於封脈衝),否則都不能實現交流滅磁。
當滅磁開關裝在交流側時,可以利用在滅磁開關打開的過程中一相無電流而自動分斷的特點,並藉助可控矽的自然續流將可控矽陽極的交流電壓引入到滅磁過程中去。即使在發電機轉子電流換流到滅磁電阻支路前,有可控矽的觸發脈衝使得某個橋臂的兩個可控矽直通,形成轉子迴路短接滅磁,仍然可以保證交流側滅磁開關的分斷而實現自然續流滅磁。當然這樣滅磁時間會比較長,按轉子時間常數Td0進行衰減,而且滅磁過程中最多只能利用滅磁開關兩個斷口的弧壓。
當滅磁開關安裝在直流側時,必須配合封脈衝措施,否則不能實現交流滅磁。滅磁開關安裝在直流側的好處是滅磁過程中可以充分利用滅磁開關串聯斷口的弧壓。事實上,封脈衝是一種簡便易行的方法,而其作用非常顯著,因此在採用交流滅磁的場合,封脈衝措施是必須的。
值得注意的是,交流滅磁需要考慮以下兩種情況:
第一,需要考慮機端三相短路。當發電機機端三相短路時,只能夠靠滅磁開關的斷口弧壓滅磁,如果滅磁電阻換流需要的電壓大於交流滅磁開關的斷口電壓,則不能成功滅磁,就會損壞交流開關。考慮到這種情況,一般在轉子兩端設定電子跨接器或機械跨接器,甚至兩者都設定。
第二,需要考慮到可控矽整流橋臂是否存在可控矽損壞,是否有橋臂短路的情況,以及在交流側短路的異常情況下可否可靠滅磁。
當然,採用封閉母線的發電機組發電機機端短路可以認為基本不存在,一般勵磁變到整流橋之間短路幾率也比較小。若整流裝置交流側故障,只要整流橋臂熔斷器選擇合理,是能夠降低此類故障幾率的,所以這些異常工況也不必考慮。即使機端短路也能夠利用短路點比較低的電壓進行電流轉移,實現滅磁。
由於汽輪發電機轉子儲能比較小,電感比較小,加之阻尼比較大,參與滅磁過程作用比較大,採用短接轉子滅磁,也是能夠接受的。所以在配備了跨接器的情況下,可以單獨採用交流滅磁。然而通常建議在水輪發電機滅磁中不選擇單獨的交流滅磁。而是選擇機械開關並聯移能滅磁或下面介紹的冗餘滅磁方案。
冗餘滅磁
所謂冗餘滅磁,是同時採用兩種及兩種以上的方法滅磁,如在交流、直流側分別設定開關,在滅磁過程中同時分斷,共同建壓,在跳滅磁開關的同時封鎖脈衝,利用封脈衝後可控矽續流形成的交流電壓輔助滅磁等等,這類滅磁方式的好處是,當一種滅磁不能正常工作時,另外的滅磁方式仍然能夠可靠地實現滅磁,當多種滅磁都正常時,可以大大降低對開關的要求。如三峽滅磁設計甚至可以在兩重以上故障情況下可靠滅磁。
實現交直流冗餘滅磁可以採用多種方法[2],不同的方法結果可能相差很大,或者需要高性能的交/直流滅磁開關作為必要的保障。
採用以下的滅磁時序可以最大限度地降低對交/直流滅磁開關的要求,實現多種工況下的可靠滅磁,即:正常情況下採用逆變滅磁;故障時首先採用約1-2個調節器控制周期的逆變滅磁,然後採用硬體封脈衝手段閉鎖調節器輸出脈衝,如果有交流滅磁開關可以同時跳交流滅磁開關(一般情況交流滅磁並非必須設定交流滅磁開關,但對於大型發電機配備交流滅磁開關是有益的),最後延時6到7毫秒(對於50赫茲而言)跳直流滅磁開關.
設計原則
由於當今大多採用氧化鋅非線性電阻滅磁,所以以下的討論都是基於氧化鋅非線性電阻。採用碳化矽滅磁時與氧化鋅非線性電阻滅磁設計的原則類似。而對於線性電阻的滅磁,所要考慮的僅僅是滅磁電阻以及電阻功率的選取,標準中有確切規定。
滅磁系統設計考慮工況
滅磁系統設計所需考慮的工況,目前在國內有些爭議。一是建議按照額定負載下,發電機機端三相短路的工況考核滅磁系統電流、能容以及需要建立的弧壓。二是認為在空載發電機勵磁失控誤強勵的工況來考核。
通常認為最危險的工況是空載勵磁失控誤強勵。此時開關面臨應對整流輸出直流電壓和滅磁殘壓的疊加,並且電流也上升到失控強勵的電流(此電流值不會比三相短路電流小),而且可以證明此時發電機儲存的能量比三相短路的能量要大。因而採用此工況是合適的。
滅磁設計需要考慮的幾個問題
ZnO(這裡以及文中其他地方所提到的ZnO均是指低場強高能量的非線性ZnO電阻)與SiC相比有較強的非線性特性,在滅磁過程中磁場電壓幾乎不變,滅磁速度快,可以使發電機的滅磁更接近於理想滅磁,因此在我國得到了廣泛的套用。本文主要針對ZnO滅磁設計中值得注意的問題展開討論。
在滅磁主迴路確定的前提下,ZnO滅磁的設計中主要考慮的問題包括:滅磁能容的估算、滅磁閥片最大允許通流能力、滅磁裝置最大允許電流、滅磁電阻的殘壓、滅磁電阻正反向荷電率、並聯支路滅磁電阻的均流和均能等。
滅磁容量的計算
事 實上根據ZnO閥片的試驗結果,ZnO閥片的最大能容遠遠大於其標稱容量。ZnO非線性電阻的能容量不是設計中最重要的因素,因為ZnO容量基本能夠滿足滅磁支路最大允許電流時的能容,而非線性滅磁電阻的損壞主要是由短時過電流以及長期老化引起。以火電135MW自並激機組為例,根據能容的計算,一般都在2MJ以下,而發電機的額定勵磁電流一般在1300A以上。IEC37.18標準規定,發電機最大可能產生的勵磁電流為額定勵磁電流的3倍,即3900A以上。一般非線性滅磁電阻的並聯支路數在32路以上,甚至不少於40支路,當採用兩個閥片串聯時,則閥片數量不少於80片。而閥片的實際能容都在30KJ以上,大多數閥片的最大能容在50-60KJ以上。也就是說,當ZnO並聯支路數滿足要求時,一般閥片的總能容都遠遠在滅磁能容的計算值之上。
這裡有兩點值得大家注意:第一,在我們在考慮最危險滅磁工況時,滅磁閥片的能容不應該簡單地考慮閥片的標稱能容,而應該考慮閥片的最大能容,在此基礎上考慮均能、均流因素以及一定的裕量。也就是說,在考慮發電機最危險滅磁工況時,閥片的每片能容按30KJ計算是可行的。第二,理論上同樣配比的材料燒制出的閥片的能容與閥片的體積成正比,所以同樣截面的ZnO閥片,殘壓較高的閥片應該具有較大的能容。