簡介
海綿橡膠。海綿狀多孔結構的硫化橡膠。有開孔、閉孔、混合孔和微孔之分。可製成軟橡膠或硬橡膠製品。質輕、柔軟、有彈性、不易傳熱。具有防震、緩和衝擊、絕熱、隔音等作用。用合成橡膠製成的還具有耐油、耐老化、耐化學藥品等特點。廣泛用於汽車、飛機、化學、日用品等工業,用作保溫、隔音、防震材料,以及制座墊、床墊、醫療機械、衛生用品、體育用品等。可由生橡膠中加起泡劑(如碳酸銨、尿素、偶氮二異丁腈等)或上濃縮的膠乳經攪拌鼓入空氣,再經硫化而成。
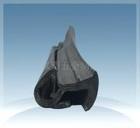
成分及材料選用
所有的橡膠,EVA(乙烯一醋酸乙烯醋),高苯乙乙烯,以及橡塑共混的熱塑性彈性體,均可用來製造海綿橡膠。具體膠種的選擇,應根據製品的使用條件、製品物化性能的指標、製造方法及加工性能等進行綜合考慮來確定。
普通的海綿橡膠主要選用天然橡膠、丁苯橡膠、丁二烯橡膠;檔次較低(如膠鞋普通中底)的可使用再生膠;高級無臭鞋墊使用EVA/橡膠並用,製造微孔鞋底可採用EVA或高苯乙烯與通用橡膠並用,或採用丁睛橡膠與聚氯乙烯共混;耐油的可選用丁睛橡膠、氯丁橡膠、丁睛橡膠/聚氯乙烯、環氧化天然橡膠等;要求耐熱、耐臭氧老化時,可選用三元乙丙橡膠和矽橡膠;輕質(相對密度小於1)且高硬度(不小於80)、彎折回彈性優異的發泡片材常要用塑膠/橡膠並用,單靠sBs或橡膠難以達到此綜合要求。
從使用壽命、工藝、成本等綜合考慮,較為理想的膠種是三元乙丙橡膠、氯丁橡膠;天然橡膠、丁苯橡膠、順丁橡膠及其與塑膠的共混料,多用於製造民用海綿橡膠製品。三元乙丙橡膠、氯丁橡膠多用於製造工業海綿橡膠製品。
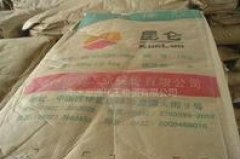
配方及製備
發泡劑的要求用於海綿橡膠的發泡劑,應滿足如下要求。
①貯存穩定性好,對酸、鹼、光、熱穩定。
②無毒、無臭、對人體無害,發泡後不產生污染,無臭味和異味。
③分解時產生的熱量小。
④在短時間內能完成分解作用,且發氣量大,可調節。
⑤粒度均勻、易分散,粒子形態以球形為好。
⑥在密閉的模腔中能充分分解。
選擇發泡劑時應該注意以下幾個特性:①分解溫度;②分解氣體的量;③分解時產生的熱量(放熱反應、吸熱反應);④分解氣體和分解生成物的異味、毒性等衛生性能;⑤混煉時的分散性能;⑥與生膠的相容性;⑦與硫化體系的匹配性;⑧對製品的污染性;⑨操作安全性;⑩貯存穩定性等。
海綿橡膠硫化體系的原則是,使膠料的硫化速度與發泡劑的分解速度相匹配。
不同的膠種選擇不同的硫化體系。通用橡膠,如天然橡膠、丁苯橡膠、順丁橡膠等,採用硫黃一促進劑硫化體系,硫黃的用量為1.5一3.0份。促進劑採用DM(或CZ)與TMTD,PZ,D,M等並用,促進劑M,DM,CZ,DZ,TMTD,PZ等單用或並用也可作海綿橡膠的促進劑,但用量較實心製品多一些。矽橡膠、三元乙丙橡膠、丁睛橡膠、EVA、聚氯乙烯/丁睛橡膠以及某些橡塑共混材料,可選用過氧化物硫化體系,此時應注意過氧化物的用量是按聚合物的交聯效率來計算的,其用量的增減只能控制交聯密度的大小。使用過氧化物硫化的硫化時間,應按它在硫化溫度下的半衰期來決定,一般取其硫化溫度下半衰期的5-10倍即可。
A為焦燒時間,AB為熱硫化的前期,BC為熱硫化的中期,CD為熱硫化後期,D為正硫化點。如果在A點前發泡,此時膠料尚未開始交聯,赫度很低,氣體容易跑掉,得不到氣孔。當在AB階段發泡時,這時薪度仍然較低,孔壁較弱,容易造成連孔。如果在BC階段發泡,這時膠料已有足夠程度的交聯,豁度較高,孔壁較強,就會產生閉孔海綿。若在D點開始發泡,這時膠料已全部交聯,赫度太高,也不能發泡。因此必須根據發泡劑的分解速度來調整硫化速度。
海綿橡膠硫化速度和發泡速度的平衡發泡早於硫化時,大量氣體分解出來時,橡膠分子仍處於未交聯的自由狀態,形成的氣孔在分解出來的氣體的猛烈地衝擊下孔壁塌陷或破裂,部分氣體由橡膠表面跑掉,造成發泡不足和表面不光滑,形成不均勻的大孔及表皮非常薄的製品;若硫化早於發泡時,當發泡劑開始分解產生氣體時,膠料已產生相當程度的交聯,膠料薪度增大,發泡劑分解出來的氣體受硫化橡膠的束縛難以使橡膠起泡,發泡困難,造成發泡不足。其結果是所生產出來的海綿為厚表皮的小孔製品,發泡程度低、硬度高、彈性低。因此,適當調節硫化速度很重要,因它對海綿橡膠的密度(發泡倍率)、吸水率(開孔氣泡增加而吸水率增大)和表皮狀態是否良好有極大影響。
加工方法
塑煉所謂塑煉,就是從外部向生膠畢加機械剪下力,解開分子間的凝聚力,切斷分子鏈,降低生膠的6性,使之具有一定的可塑度,使配合劑的混合和混煉加工容易進行的一道工序。塑煉分為低溫塑煉和高溫塑煉兩種。對於EPDM等合成橡膠而言,橡膠供應商在聚合階段就已經調整了適用於製造海綿橡膠的各種ARF33P度。因此,不需要進行塑煉。但是,對於天然橡膠,塑煉還是必需的,塑煉膠的可塑度應保持在0.56以上,這主要基於以下幾點考慮:a.生膠充分的塑煉,使它便於混煉,各種配合劑能很好地分散到橡膠中去,使發泡均勻;b.高的可塑性,便於膠料發磯,在發泡的過程中阻力降低;c.能減少硫化製品的收縮性。可逸塑性的大小,對海綿底的收縮影響很大。在海綿橡膠的製造過程中,橡膠a度越低,膠料越容易膨脹,越能夠製得泡孔均勻,收縮率小的海綿橡膠。
混煉混煉膠的熟化製造海綿橡膠的技術關鍵就是混煉膠的熟化。;在海綿橡膠生產過程中,混煉膠熟化極為重要。所謂熟化就是在生膠中加人配合劑混煉後,使混煉膠停放一段時間,可緩愛和其在加工等過程中產生的殘餘變形,增進配合劑(發泡劑、硫黃、促進劑等)的溶解和遷移穩定性,使其物理性能、加工性能等得到改善。
發泡劑的分散性海綿橡膠製造過程中最重要的工序之一就是想方設法讓發泡劑分散均勻。炭黑的分散用導電方法和炭黑分散儀進行測定。但是,發泡劑的分散性能還沒有比較容易的評估方法,仍在繼續沿用過去的方法,即將混煉膠片拉長,用目測的老方法進行評價。提高分散性可採用先加發泡劑方法。
海綿橡膠的成型和硫化海綿橡膠的成型方法有擠出成型、模壓成封,平板成型等各種方法。EPDM海綿最常用用的一般是擠出方法(汽車零部件)。多半採用連續擠出的熱空氣硫化發泡的UHF法(微波和熱空氣並用)進行加工。製造海綿橡膠,除採用連續擠出硫化發泡法外,還有平板硫化發泡法。該方法很早以前就用於海綿橡膠的製造,其特點是能夠製得含有微孔的海綿製品。當使用平板硫化機製造橡膠海綿時,一般採用二段硫化法(一段硫化,二段硫化)。一段硫化以發泡劑的分解為主要目的,一段硫化裝膠量為模具容積的105℃,經低溫短時間〔(100-120)℃X(5一10)min〕硫化後,把所製得的半硫化海綿橡膠裝到二段硫化模具內,再高溫長時間仁(120-160)℃X(10一15)min〕硫化,完成發泡過程。這樣所得到的海綿橡膠製品的尺寸與模具的形狀一樣。一段硫化條件和二段硫化條件因橡膠海綿的硬度、大小、厚度以及膠種、配方的不同而不同。
套用
海綿橡膠密度小,彈性和屈撓性優異,具有較好的減震、隔音、隔熱性能。海綿橡膠被廣泛地套用於密封、減震、消音、絕熱、服裝、製鞋、家電、印染、健身器材和離子交換等許多方面。如汽車的擋風條、緩衝膠墊、建築工程用密封墊片、弱電部件的絕熱材料、減震材料、簡易潛水服及鞋等製品。