介紹
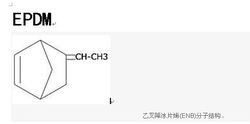
EPDM中文名:三元乙丙橡膠
英文全稱:Ethylene-Propylene-Diene Monomer(簡稱:EPDM)
三元乙丙橡膠介紹
三元乙丙橡膠是乙烯、丙烯以及非共軛二烯烴的三元共聚物,1963年開始商業化生產。每年全世界的消費量是80萬噸。EPDM最主要的特性就是其優越的耐氧化、抗臭氧和抗侵蝕的能力。由於三元乙丙橡膠屬於聚烯(PA66)烴家族,它具有極好的硫化特性。在所有橡膠當中,EPDM具有最低的比重。它能吸收大量的填料和油而影響特性不大。因此可以製作成本低廉的橡膠化合物。
分子結構和特性
三元乙丙是乙烯、丙烯和非共軛二烯烴的三元共聚物。二烯烴具有特殊的結構,只有兩鍵之一的才能共聚,不飽和的雙鍵主要是作為交鏈處。另一個不飽和的不會成為聚合物主鏈,只會成為邊側鏈。三元乙丙的主要聚合物鏈是完全飽和的。這個特性使得三元乙丙可以抵抗熱,光,氧氣,尤其是臭氧。三元乙丙本質上是無極性的,對極性溶液和化學物具有抗性,吸水率低,具有良好的絕緣特性。
在三元乙丙生產過程中,通過改變三單體的數量,乙烯丙烯比,分子量及其分布以及硫化的方法可以調整其特性。
EPDM第三單體的選擇
第三二烯烴類型的單體是通過乙烯和丙烯的共聚,在聚合物中產生不飽和,以便實現硫化。第三單體的選擇必須滿足以下要求:
最多兩鍵:一個可聚合,一個可硫化
反應類似於兩種基本的單體
主鍵隨機聚合產生均勻分布
足夠的揮發性,便於從聚合物中除去
最終聚合物硫化速度合適
目前工業化生產三元乙丙橡膠用第三單體只有如下三種:
乙叉降冰片烯(ENB)
雙環戊二烯(DCPD)
1,4-己二烯(HD)
CH3-CH=CH-CH2-CH=CH2
(此種單體目前只有美國Du Pont公司一家使用)
二烯烴類型和含量對聚合物特性的影響
三元乙丙生產中主要是用ENB和DCPD。
三元乙丙中最廣泛使用的是ENB,它比DCPD產品硫化要快得多。在相同的聚合條件下,第三單體的本質影響著長鏈支化,按以下順序遞增:EPM
三元乙丙其他的受二烯烴第三單體影響的還有:
ENB-快速硫化,高拉伸強度,低永久形變
DCPD-防焦性,低永久應變,低成本
隨著二烯烴第三單體的增加,將會有下列影響發生:更快硫化率,更低的壓縮形變,高定伸,促進劑選擇的多樣性,減少的防焦性和延展,更高的聚合物成本。
乙烯丙烯比
乙烯丙烯比可以在硫化階段進行改變,商業的三元乙丙聚合物乙烯丙烯比由80/20到50/50。當乙烯丙烯比由50/50變化到80/20時,正面的影響有:更高的壓坯強度,更高的拉伸強度,更高的結晶化,更低的玻璃體轉化溫度,能將原材料聚合物轉化成丸狀,以及更好的擠出特性。不好的影響就是不好的壓延混合性,較差的低溫特性,以及不好的壓縮形變。
當丙烯比例更高時,好處就是更好的加工性能,更好的低溫特性以及更好的壓縮形變等。
分子量和分子量分布
彈性體的分子量通常用門尼粘度表示。在三元乙丙的門尼粘度中,這些值是在高溫下得到的,通常為125℃,這樣做的主要原因是要消去由高乙烯含量所產生的任何影響(結晶化),由此會掩蓋聚合物的真正分子量。三元乙丙的門尼粘度範圍在20到100之間。也有更高分子量的商用三元乙丙也有生產,但一般都充油,以便混煉。
分子量以及在三元乙丙中的分布可以在聚合過程中通過以下途徑聚合:
催化劑以及共催化劑的類型和濃度
溫度
改性劑,如氫的濃度
三元乙丙的分子量分布可以通過凝膠滲透色譜法使用二氯苯作為溶劑在高溫下(150℃)測量而得。分子量分布通常被稱為是重量平均分子量與數量平均分子量的比例。根據普通和高度支化的結構,這個值在2到5之間變化。由於有分鍵,含有DCPD的三元乙丙橡膠更寬的分子量分布。
通過增加三元乙丙的分子量,正面影響有:更高的拉伸和撕裂強度,在高溫情況下更高的生坯強度,能夠吸收更多的油和填料(低成本)。隨著分子量分布的增加,正面的影響有:增加的混煉和碾磨加工性。但是,較窄的分子量分布可以改進硫化速度,硫化狀態以及注塑行為。
硫化類型
三元乙丙可以利用有機過氧化物或者硫來進行硫化。但是,相比與硫磺硫化,過氧化物交鏈的三元乙丙用於電線電纜工業時具有更高的溫度抗性,更低的壓縮形變以及改進的硫化特性。過氧化物硫化的不好的地方就在於更高的成本。
正如前面所提到的,三元乙丙的交鏈速度和硫化時間隨著硫化類型和含量而改變。當三元乙丙與丁基,天然橡膠,丁苯橡膠混合時,在選擇合適的三元乙丙產品時,必須要考慮到下列因素:
當與丁基進行混合時,由於丁基具有較低的不飽和度,為適應丁基的硫化速度,最好選擇相對較低含量的DCPD和ENB含量的三元乙丙。
當與天然橡膠和丁苯橡膠混合時,最好選擇8%到10%ENB含量的三元乙丙,以滿足其硫化速度。
三元乙丙橡膠是由乙烯、丙烯經溶液共聚合而成的橡膠,再引入第三單體(ENB)。三元乙丙橡膠基本上是一種飽和的高聚物,耐老化性能非常好、耐天候性好、電絕緣性能優良、耐化學腐蝕性好、衝擊彈性較好。乙丙橡膠的最主要缺點是硫化速度慢;與其它不飽和橡膠並用難,自粘和互粘性都很差,故加工性能不好。
根據乙丙橡膠的性能特點,主要套用於要求耐老化、耐水、耐腐蝕、電氣絕緣幾個領域,如用於輪胎的淺色胎側、耐熱運輸帶、電纜、電線、防腐襯裡、密封墊圈、建築防水片材、門窗密封條、家用電器配件、塑膠改性等。乙丙橡膠的性質與用途。
乙丙橡膠以乙烯和丙烯為主要原材料合成,耐老化、電絕緣性能和耐臭氧發能突出。乙丙橡膠可大量充油和填充碳黑,製品價格較低,乙丙橡膠化學穩定性好,耐磨性、彈性、耐油性和丁苯橡膠接近。乙丙橡膠的用途十分廣泛,可以作為輪胎側、膠條和內胎以及汽車的零部件,還可以作電線、電纜包皮及高壓、超高壓絕緣材料。還可製造及鞋、衛生用品等淺色製品。乙丙橡膠的性能與改進:
一、1、低密度高填充性
乙丙橡膠的密度是較低的一種橡膠,其密度為0.87。加之可大量充油和加入填充劑,因而可降低橡膠製品的成本,彌補了乙丙橡膠生膠價格高的缺點,並且對高門尼值的乙丙橡膠來說,高填充後物理機械能降低幅度不大。
2、耐老化性
乙丙橡膠有優異的耐天候、耐臭氧、耐熱、耐酸鹼、耐水蒸汽、顏色穩定性、電性能、充油性及常溫流動性。乙丙橡膠製品在120℃下可長期使用,在150- 200℃下可短暫或間歇使用。加入適宜防老劑可提高其使用溫度。以過氧化物交聯的三元乙丙橡膠可在苛刻的條件下使用。三元乙丙橡膠在臭氧濃度 50pphm、拉伸30%的條件下,可達150h以上不龜裂。
3、耐腐蝕性
由於乙丙橡膠缺乏極性,不飽和度低,因而對各種極性化學品如醇、酸、鹼、氧化劑、製冷劑、洗滌劑、動植物油、酮和脂等均有較好的抗耐性;但在脂屬和芳屬溶劑(如汽油、苯等)及礦物油中穩定性較差。在濃酸長期作用下性能也要下降。在ISO/TO 7620中匯集了近400種具有腐蝕性的氣態和液態化學品對各種橡膠性能作用的資料,並規定了1-4級表示其作用程度,腐蝕性化學品對橡膠性能的影響:
等級體積溶脹率/% 硬度降低值對性能影響
1<10 <10 輕微或無
2 10-20 <20 較小
3 30-60 <30 中等
4 >60 >30 嚴重
4、耐水蒸汽性能
乙丙橡膠有優異的耐水蒸汽性能並估優於其耐熱性。在230℃過熱蒸汽中,近100h後外觀無變化。而氟橡膠、矽橡膠、氟矽橡膠、丁基橡膠、丁腈橡膠、天然橡膠在同樣條件下,經歷較短時間外觀發生明顯劣化現象。
5、耐過熱水性能
乙丙橡膠耐過熱水性能亦較好,但與所有硫化系統密切相關。以二硫化二嗎啡啉、TMTD為硫化系統的乙丙橡膠,在125℃過熱水中浸泡15個月後,力學性能變化甚小,體積膨脹率僅0.3%。
6、電性能
乙丙橡膠具有優異的電絕緣性能和耐電暈性,電性能優於或接近於丁苯橡膠、氯磺化聚乙烯、聚乙烯和交聯聚乙烯。
7、彈性
由於乙丙橡膠分子結構中無極性取代基,分子內聚能低,分子鏈可在較寬範圍內保持柔順性,僅次於天然商榷和順丁橡膠,並在低溫下仍能保持。
8、粘接性
乙丙橡膠由於分子結構缺少活性基團,內聚能低,加上膠料易於噴霜,自粘性和互粘性很差。
二、乙丙橡膠改性品種.
三元乙丙和三元乙丙橡膠從20世紀50年代末,60年代初開發成功以來,世界上又出現了多種改性乙丙橡膠和熱塑性乙丙橡膠(如EPDM/PE),從而為乙丙橡膠的廣泛套用提供了眾多的品種和品級。改性乙丙橡膠主要是將乙丙橡膠進行溴化、氯化、磺化、順酐化、馬來酸酐化、有機矽改性、尼龍改性等。乙丙橡膠還有接枝丙烯腈、丙烯酸酯等。多年來,採用共混、共聚、填充、接枝、增強和分子複合等手段,獲得了許多綜合性能好的高分子材料。乙丙橡膠通過改性,也在性能方面獲得很大的改善,從而擴大了乙丙橡膠套用範圍。
溴化乙丙橡膠是在開煉機上以經溴化劑處理而成。溴化後乙丙橡膠可提高其硫化速度和粘合性能,但機械強度下降,因而溴化乙丙橡膠僅適用於作乙丙橡膠與其他橡膠粘合的中介層。
氯化乙丙橡膠是將氯氣通過三元乙丙橡膠溶液中而製成。乙丙橡膠氯化後可提高硫化速度以及與不飽和商榷的相容性,耐燃性、耐油性,粘合性能也所改善。
磺化乙丙橡膠是將三元乙丙橡膠溶於溶劑中,經磺化劑膠中和劑處理而成。磺化乙丙橡膠由於具有熱塑性彈性體的體質和良好的粘著性能,在膠粘劑 、塗復織物、建築防水瘦肉、防腐襯裡等方面將得到廣泛的套用。
丙烯腈接枝的乙丙橡膠以甲苯為溶劑,過氯化苯甲醇為引發劑,在80℃下使丙烯腈接枝於乙丙橡膠。丙烯腈改性乙丙橡膠不但保留了乙丙橡膠耐腐蝕性,而且獲得了相當於丁腈-26的耐油性,具有較好的物理機械性能和加工性能。
熱塑性乙丙橡膠(EPDM/PP)是以三元乙丙橡膠為主體與聚丙烯進行混煉。同時使乙丙橡膠達到預期交聯程度的產物。化不但在性能上仍保留乙丙橡膠所固有的特性,而且還具有顯著的熱塑性塑膠的注射、擠出、吹塑及壓延成型的工藝性能。
除此之外,改性乙丙橡膠還有氯磺化乙丙商榷、丙烯酸酯接枝乙丙橡膠等。
橡膠歷史
人類使用天然橡膠的歷史已經有好幾個世紀了。哥倫布在發現新大陸的航行中發現,南美洲土著人玩的一種球是用硬化了的植物汁液做成的。哥倫布和後來的探險家們無不對這種有彈性的球驚訝不已。一些樣品被視為珍品帶回歐洲。後來人們發現這種彈性球能夠擦掉鉛筆的痕跡,因此給它起了一個普通的名字“擦子(rubber)”。這仍是這種物質的英文名字。這種物質就是橡膠。
但是直到1839年,美國人古德伊爾(CharlesGoodyear)成功地將天然橡膠進行了硫化後,橡膠才成為有使用價值的材料。通過與硫磺一起加熱進行硫化,實現了橡膠分子鏈的交聯,使橡膠具備了良好的彈性。為什麼橡膠會有彈性呢?讓我們分析一下橡膠的分子結構。天然橡膠分子的鏈節單體為異戊二烯。我們知道高分子中鏈與鏈之間的分子間力決定了其物理性質。在橡膠中,分子間的作用力很弱,這是因為鏈節異戊二烯不易於再與其他鏈節相互作用。好比兩個朋友想握手,但每個人手上都拿著很多東西,因此握手就很困難了。橡膠分子之間的作用力狀況決定了橡膠的柔軟性。橡膠的分子比較易於轉動,也擁有充裕的運動空間,分子的排列呈現出一種不規則的隨意的自然狀態。在受到彎曲、拉長等外界影響時,分子被迫顯出一定的規則性。當外界強制作用消除時,橡膠分子就又回原來的不規則狀態了。這就是橡膠有彈性的原因。由於分子間作用力弱,分子可以自由轉動,分子鏈間缺乏足夠的聯結力,因此,分子之間會發生相互滑動,彈性也就表現不出來了。這種滑動會因分子間相互纏繞而減弱。可是,分子間的纏繞是不穩定的,隨著溫度的升高或時間的推移纏繞會逐漸鬆開,因此有必要使分子鏈間建立較強固的聯接。這就是古德伊爾發明的硫化方法。硫化過程一般在攝氏140-150度的溫度下進行。當時古德伊爾的小火爐正好起了加熱的作用。硫化的主要作用,簡單地說,就是在分子鏈與分子鏈之間形成交聯,從而使分子鏈間作用力量增強。
在過去的幾千年間,人們所坐的車使用的一直是木製輪子,或者再在輪子周圍加上金屬輪輞。在古德伊爾發明了實用的硫化橡膠之後的1845年,英國工程師R.W.湯姆森在車輪周圍套上一個合適的充氣橡膠管,並獲得了這項設備的專利,到了1890年,輪胎被正式用在腳踏車上,到了1895年,被用在各種老式汽車上。儘管橡膠是一種柔軟而易破損的物質,但卻比木頭或金屬更加耐磨。橡膠的耐用、減震等性能,加上充氣輪胎的巧妙設計,使乘車的人覺得比以往任何時候都更加舒適。隨著汽車數量的大量增加,用於製造輪胎的橡膠的需求量也變成了天文數字。如此廣泛的套用使天然橡膠供不應求。面對橡膠生產的嚴峻形勢,各國競相研製合成橡膠。
人們首先想到的是用天然橡膠的結構單元--異戊二烯來製造合成橡膠。早在1880年,化學家們就發現,異戊二烯放置過久就會變軟發動,經酸化處理後則會變成類似橡膠的物質。
德皇威廉二世曾讓人用這種物質製成皇家汽車的輪胎,藉以炫耀德國化學方面的高超技藝。然而,用異戊二烯作為合成橡膠的原料,有兩個困難:一是異戊二烯的主要來源正是天然橡膠本身;二是在天然橡膠長鏈中,所有的異戊二烯單元都朝向同一方向;在固塔坡膠長鏈中,它們則是嚴格地按照一正一反的方向排列的,而人工聚合時異戊二烯單元往往是毫無規律地聚合在一起,得到的是一種既不是橡膠也不是固塔坡膠的物質。這種物質缺少橡膠的彈性和柔性,用不了多久就會變粘,所以不能用來製造汽車輪胎(僅用於國事活動的皇家汽車當然是個例外)。 在第一次世界大戰期間,迫於橡膠匾乏,德國人採用了二甲基丁二烯聚合而成甲基橡膠,這種橡膠可以大量生產,而且價格低廉。在第一次世界大戰期間,德國大約生產了2500噸甲基橡膠。儘管這種橡膠的耐壓性能不理想,戰後便被淘汰了,但它畢竟是第一種具有實用價值的合成橡膠。
大約在1930年,德國和蘇聯用丁二烯作為單體,金屬鈉作為催化劑,合成了一種叫做丁鈉橡膠。作為一種合成橡膠,丁鈉橡膠對於應付橡膠匾乏而言還算是令人滿意的。與其它單體共聚可以改善了鈉橡膠的性能。如與苯乙烯共聚得到丁苯橡膠(Buna-S),它的性質與天然橡膠極其相似。事實上,在第二次世界大戰期間,德國軍隊就是因為有丁苯橡膠,橡膠供應才沒有出現嚴重短缺現象。蘇聯也用同樣的方法向自己的軍隊提供橡膠。
美國在戰後大力研究合成橡膠。首先合成了氯丁橡膠,氯原子使氯丁橡膠具有天然橡膠所不具備的一些抗腐蝕性能。例如,它對於汽油之類的有機溶劑具有較高的抗腐蝕性能,遠不像天然橡膠那樣容易軟化和膨脹。因此,像導油軟管這樣的用場,氯丁橡膠實際上比天然橡膠更為適宜。氯丁橡膠首次清楚地表明,正如在許多其他領域一樣,在合成橡膠領域,試管中的產物並不一定只能充當天然物質的代用品,它的性能能夠比天然物質更好。
1955年美國人利用齊格勒在聚合乙烯時使用的催化劑(也稱齊格勒——納塔催化劑)聚合異戊二烯。首次用人工方法合成了結構與天然橡膠基本一樣的合成天然橡膠。不久用乙烯、丙烯這兩種最簡單的單體製造的乙丙橡膠也獲成功。此外還出現了各種具有特殊性能的橡膠,合成橡膠的總產量也是大大超過了天然橡膠。
主要用途
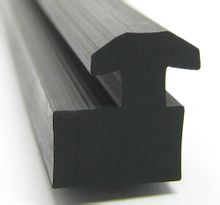
三元乙丙橡膠用途比較廣泛,主要套用於房屋建築、電線電纜、汽車工業等領域
。房屋建築方面,主要用於屋頂單層防水卷材等;電線電纜方面,主要用於民用和商用建築的輸入線、建築用電線、礦用電纜、核電站用電線、汽車點火線、控制及信號電纜等;汽車工業方面,主要用於汽車、卡車和公共汽車輪胎和非輪胎部件,包括汽車的水箱及加熱軟管、密封條、橡膠帶、車身及底盤的部件、擋雨條、底板和環管等。
分子結構
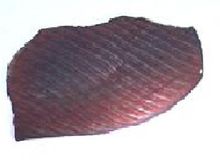
三元乙丙是乙烯、丙烯和非共軛二烯烴的三元共聚物。二烯烴具有特殊
的結構,只有兩鍵之一的才能共聚,不飽和的雙鍵主要是作為交鏈處。另一個不飽和的不會成為聚合物主鏈,只會成為邊側鏈。三元乙丙的主要聚合物鏈是完全飽和的。這個特性使得三元乙丙可以抵抗熱,光,氧氣,尤其是臭氧。三元乙丙本質上是無極性的,對極性溶液和化學物具有抗性,吸水率低,具有良好的絕緣特性。
在三元乙丙生產過程中,通過改變三單體的數量,乙烯丙烯比,分子量及其分布以及硫化的方法可以調整其特性。
EPDM第三單體的選擇
第三二烯烴類型的單體是通過乙烯和丙烯的共聚,在聚合物中產生不飽和,以便實現硫化。第三單體的選擇必須滿足以下要求:
最多兩鍵:一個可聚合,一個可硫化
反應類似於兩種基本的單體
主鍵隨機聚合產生均勻分布
足夠的揮發性,便於從聚合物中除去
最終聚合物硫化速度合適
二烯烴類型和含量對聚合物特性的影響
三元乙丙生產中主要是用ENB和DCPD。
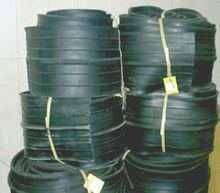
三元乙丙中最廣泛使用的是ENB,它比DCPD產品硫化要快得多。
在相同的聚合條件下,第三單體的本質影響著長鏈支化,按以下順序遞增:EPM
三元乙丙其他的受二烯烴第三單體影響的還有:
ENB-快速硫化,高拉伸強度,低永久形變
DCPD-防焦性,低永久應變,低成本
隨著二烯烴第三單體的增加,將會有下列影響發生:更快硫化率,更低的壓縮形變,高定伸,促進劑選擇的多樣性,減少的防焦性和延展,更高的聚合物成本。
乙烯丙烯比
乙烯丙烯比可以在硫化階段進行改變,商業的三元乙丙聚合物乙烯丙烯比由80/20到50/50。當乙烯丙烯比由50/50變化到80/20時,正面的影響有:更高的壓坯強度,更高的拉伸強度,更高的結晶化,更低的玻璃體轉化溫度,能將原材料聚合物轉化成丸狀,以及更好的擠出特性。不好的影響就是不好的壓延混合性,較差的低溫特性,以及不好的壓縮形變。
當丙烯比例更高時,好處就是更好的加工性能,更好的低溫特性以及更好的壓縮形變等。
性能
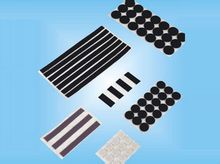
乙丙橡膠是密度較低的一種橡膠,其密度為0.87。加之可大量充油和
加入填充劑,因而可降低橡膠製品的成本,彌補了乙丙橡膠生膠價格高的缺點,並且對高門尼值的乙丙橡膠來說,高填充後物理機械能降低幅度不大。
耐老化性
乙丙橡膠有優異的耐天候、耐臭氧、耐熱、耐酸鹼、耐水蒸汽、顏色穩定性、電性能、充油性及常溫流動性。乙丙橡膠製品在120℃下可長期使用,在150- 200℃下可短暫或間歇使用。加入適宜防老劑可提高其使用溫度。以過氧化物交聯的三元乙丙橡膠可在苛刻的條件下使用。三元乙丙橡膠在臭氧濃度 50pphm、拉伸30%的條件下,可達150h以上不龜裂。
耐腐蝕性
由於乙丙橡膠缺乏極性,不飽和度低,因而對各種極性化學品如醇、酸、鹼、氧化劑、製冷劑、洗滌劑、動植物油、酮和脂等均有較好的抗耐性;但在脂屬和芳屬溶劑(如汽油、苯等)及礦物油中穩定性較差。在濃酸長期作用下性能也要下降。在ISO/TO 7620中匯集了近400種具有腐蝕性的氣態和液態化學品對各種橡膠性能作用的資料,並規定了1-4級表示其作用程度,腐蝕性化學品對橡膠性能的影響:
等級 體積 溶脹率/% 硬度降低值 對性能影響
1 <10 <10 輕微或無
2 10-20 <20 較小
3 30-60 <30 中等
4 >60 >30 嚴重
耐水蒸汽
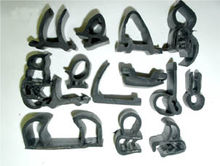
乙丙橡膠有優異的耐水蒸汽性能並估優於其耐熱性。在230℃過熱蒸汽中,
近100h後外觀無變化。而氟橡膠、矽橡膠、氟矽橡膠、丁基橡膠、丁腈橡膠、天然橡膠在同樣條件下,經歷較短時間外觀發生明顯劣化現象。
耐過熱水
乙丙橡膠耐過熱水性能亦較好,但與所有硫化系統密切相關。以二硫化二嗎啡啉、TMTD為硫化系統的乙丙橡膠,在125℃過熱水中浸泡15個月後,力學性能變化甚小,體積膨脹率僅0.3%。
耐電性
乙丙橡膠具有優異的電絕緣性能和耐電暈性,電性能優於或接近於丁苯橡膠、氯磺化聚乙烯、聚乙烯和交聯聚乙烯。
彈性
由於乙丙橡膠分子結構中無極性取代基,分子內聚能低,分子鏈可在較寬範圍內保持柔順性,僅次於天然商榷和順丁橡膠,並在低溫下仍能保持。
粘接性
乙丙橡膠由於分子結構缺少活性基團,內聚能低,加上膠料易於噴霜,自粘性和互粘性很差。
分子量
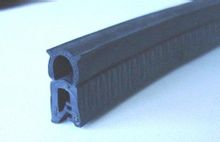
彈性體的分子量通常用門尼粘度表示。在三元乙丙的門尼粘度中,這些
值是在高溫下得到的,通常為125℃,這樣做的主要原因是要消去由高乙烯含量所產生的任何影響(結晶化),由此會掩蓋聚合物的真正分子量。三元乙丙的門尼粘度範圍在20到100之間。也有更高分子量的商用三元乙丙也有生產,但一般都充油,以便混煉。
分子量以及在三元乙丙中的分布可以在聚合過程中通過以下途徑聚合:
催化劑以及共催化劑的類型和濃度
溫度
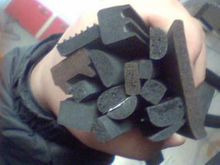
改性劑,如氫的濃度,三元乙丙的分子量分布可以通過凝膠滲透色譜法
使用二氯苯作為溶劑在高溫下(150℃)測量而得。分子量分布通常被稱為是重量平均分子量與數量平均分子量的比例。根據普通和高度支化的結構,這個值在2到5之間變化。由於有分鍵,含有DCPD的三元乙丙橡膠更寬的分子量分布。
通過增加三元乙丙的分子量,正面影響有:更高的拉伸和撕裂強度,在高溫情況下更高的生坯強度,能夠吸收更多的油和填料(低成本)。隨著分子量分布的增加,正面的影響有:增加的混煉和碾磨加工性。但是,較窄的分子量分布可以改進硫化速度,硫化狀態以及注塑行為。
硫化類型
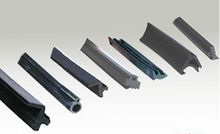
三元乙丙可以利用有機過氧化物或者硫來進行硫化。但是,相比與硫磺
硫化,過氧化物交鏈的三元乙丙用於電線電纜工業時具有更高的溫度抗性,更低的壓縮形變以及改進的硫化特性。過氧化物硫化的不好的地方就在於更高的成本。
正如前面所提到的,三元乙丙的交鏈速度和硫化時間隨著硫化類型和含量而改變。當三元乙丙與丁基,天然橡膠,丁苯橡膠混合時,在選擇合適的三元乙丙產品時,必須要考慮到下列因素:
當與丁基進行混合時,由於丁基具有較低的不飽和度,為適應丁基的硫化速度,最好選擇相對較低含量的DCPD和ENB含量的三元乙丙。
當與天然橡膠和丁苯橡膠混合時,最好選擇8%到10%ENB含量的三元乙丙,以滿足其硫化速度。
生產工藝
合成橡膠的生產工藝大致可分為單體的合成和精製、聚合過程以及橡膠後處理三部分。
精製方法
合成橡膠的基本原料是單體,精製常用的方法有精餾、洗滌、乾燥等。
聚合過程
聚合過程是單體在引發劑和催化劑作用下進行聚合反應生成聚合物的過程。有時用一個聚合設備,有時多個串聯使用。合成橡膠的聚合工藝主要套用乳液聚合法和溶液聚合法兩種。採用乳液聚合的有丁苯橡膠、異戊橡膠、丁丙橡膠、丁基橡膠等。
後處理
後處理是使聚合反應後的物料(膠乳或膠液),經脫除未反應單體、凝聚、脫水、乾燥和包裝等步驟,最後製得成品橡膠的過程。乳液聚合的凝聚工藝主要採用加電解質或高分子凝聚劑,破壞乳液使膠粒析出。溶液聚合的凝聚工藝以熱水凝析為主。凝聚後析出的膠粒,含有大量的水,需脫水、乾燥。
近期走勢
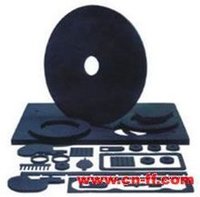
衡水市場,三元乙丙膠行情平穩,市場上貨源穩定,交投較清淡。吉化4045市場主流報價在28500元/噸左右,4090市場主流報價在25000元/噸左右,2070市場主流報價三元乙丙在22000元/噸左右;埃克森正牌8800、8700市場主流報價在24500元/噸左右,副牌5601市場主流報價在22000-22500元/噸;杜邦副牌3640市場主流報價在22000元/噸左右,4570市場主流報價在25000元/噸左右;俄羅斯7505市場主流報價在21000元/噸左右;日本EP33、35市場主流報價在32000元/噸左右;荷蘭DSM正牌5508市場主流報價在26500元/噸左右,4703市場報價在27000元/噸左右,4802市場報價在27000元/噸左右;實際成交價格略低。
天津市場,吉化三元乙丙膠行情平穩,吉化4045市場主流報價在28200-28500元/噸;4090市場主流報價在24800元/噸左右;市場上貨源穩定,成交情況一般。
華東市場,三元乙丙橡膠行情較平穩,杜邦5565副牌市場報價在24000-24500元/噸,3640副牌市場報價在22000-22500元/噸,4570副牌市場報價在25000-25500元/噸;埃克森5601副牌市場主流報價在21500-22000元/噸,3702市場主流報價在21000元/噸左右;俄羅斯7505市場主流報價在21500元/噸左右;錦湖乙丙330、350市場主流報價在28000-28500元/噸之間,960、980等充油膠報價略低在28000元/噸左右;實際成交價格略低。
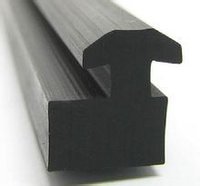
廣東市場,韓國SK三元乙丙正牌膠行情平穩,一級代理商對S505和S505A市場報價在26800元/噸,對S501A、S512F、S552市場報價在26500元/噸;貨源穩定,成交情況一般。
華南市場,三元乙丙膠行情較平穩,市場上貨源穩定,交投相對清淡。日本JSR的EP33、35市場主流報價在29000元/噸左右;荷蘭DSM4703市場主流報價在三元乙丙28500-29000元/噸左右,4802市場主流報價在28000元/噸左右;韓國錦湖KEP330、350市場主流報價在28500元/噸左右;實際成交價格略低。
受吉化廠家連續上調4045出廠報價的影響,市場上的4045價格也一路走高,但是其他牌號的三元乙丙膠價格走勢依舊較平穩。由於下游廠家開工率不高,對乙丙膠需求較清淡,市場成交疲軟。預計短期內三元乙丙膠難有起色,還將以平穩走勢為主。