換熱系統簡介
換熱系統是化工過程中必不可少的子系統,屬於工業輔助系統,工業中通常會採用換熱系統來為核心工藝單元提供能量和將產品冷卻到規定溫度,降低化工過程的能耗、提高能效。換熱系統通常由吸熱器、回熱器和冷卻器組成,也可由多個換熱器(每個換熱器的傳熱方式與布置形式可各不相同)按照一定的方式組合而成用於流體之間熱量的傳遞,例如在要求兩種低流速的流體的溫度變化較大時, 可採用多台換熱器的逆流組合的方案 , 這樣一方面可使換熱器系統整體的平均溫壓較大 ,另一方面由於使用了多個較小的換熱器,對換熱器的製造與布置也帶來了方便。因此 ,作為與能源的合理利用密切相關的換熱器系統的合理設計和性能改善也是工程上經常遇到的問題。換熱系統回收的能量往往具有較高的能級,但利用環節自身已沒有能阱可以消化,如分餾塔的過剩熱等。
換熱系統可以分為高溫換熱系統(用於工質降溫)和餘熱利用換熱系統。兩者在工藝參數上存在著較大區別。高溫換熱系統由於用於工質或者產品降溫,對於出口溫度有一定的要求,而餘熱利用換熱系統則沒有限制。在結構材質方面,高溫換熱系統的換熱器一般在超溫受熱面處使用耐熱合金鋼,在溫度較低的部分使用普通碳鋼,形成複合結構。而對於餘熱利用換熱系統的換熱器,一般工業爐排出的煙氣溫度較低,換熱器普遍使用價格較低的碳鋼。
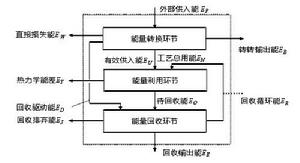
組成部件及其作用
吸熱器
吸熱器與化工上用的換熱器比較類似,一般採用管狀或肋片狀,主要解決吸熱管組的通流容積、工質的流阻損失和吸熱管傳熱能力之間的矛盾,同時吸熱管的尺寸和位置分布形式對發動機的性能影響很大。對吸熱熱管的要求是,保證必要的傳熱能力的情況下,管的通流容積和工質的流阻損失應儘可能小,用以保證發動機具有較高的功率和效率。
吸熱器的原理包括以下三個傳熱過程:
(1)外部熱源與吸熱管的外壁或翅片外表面之間的換熱過程(包括輻射換熱和對流換熱);
(2)吸熱管外壁向管內表面導熱或外部翅片向內部的導熱(熱傳導);
(3)吸熱管內壁或翅片內壁與工質的換熱(對流換熱)。
吸熱器熱交換效果計算:









式中 為熱腔內工質溫度,取900K; 為壁面溫度,取920K; 為對吸熱器供應的熱量,J; 為工質流經吸熱器的時間比例(%),可用吸熱器體積與整個循環體積比表示,設計中為管內腔容積與配氣活塞上端體積之和; 為吸熱器內工質對流換熱係數, ; 為吸熱器有效換熱面積, 。
回熱器




回熱器在換熱系統中串聯在冷卻器和吸熱器之間,其功能就是當工質在熱腔吸熱後膨脹流經它時能吸收部分工質的能量,從而使工質能從循環的最高溫度 下降到循環的最低溫度 ,工質在冷卻器內壓縮做功後循環流到吸熱器的過程中流經回熱器時被加熱,使其循環溫度由 升高到 。因此,可以由此看出,回熱器不僅是充當熱氣機的一種節能裝置,同時還因為回熱器的存在而大大減少了吸熱器和冷卻器的工作容量,降低了整個換熱系統的無益容積。由於回熱器的功能類似於儲熱裝置,對回熱器設計和選材必須具備較高的熱容量。
回熱器的實際工作過程與理想情況有很大區別,主要存在兩個方面:
(1)由於發動機運轉速度較快,整個換熱系統內的實際工質沒有一個分子會完全從吸熱器走到冷卻器,其循環過程中往往還沒有走到回熱器的一半便折回,從而回熱器靠近吸熱器一端的溫度高,而靠近冷卻器一端的低;
(2)工質流經回熱器時存在摩擦損失、流阻損失和回熱損失。
冷卻器
冷卻器是換熱系統的重要組件之一,其性能優劣對換熱效果有很大影響,其功能就是將循環過程中的壓縮熱傳到外界,使壓縮過程能在理想的“等溫”條件下進行,且傳熱過程是在循環的最低溫度下進行的,通常所使用的冷卻劑為水或水與甘醇的混合液,其結構形式一般採取管式換熱器。對其設計的要求主要是冷卻效果要好,但冷卻器的冷卻能力和通流容積、流阻損失之間是相互矛盾的,在實際設計中要均衡三者之間的關係,一般的做法是採用許多內徑較小的毛細管組成,並形成一個圓形多層的冷卻器管籠。同時還需做好管端頭與配合面板之間的密封,使其耐受循環系統的最高壓力。
冷卻器設計的一般要求:
(1)結構緊湊、製造工藝性要好;
(2)運行可靠,安裝維護方便;
(3)通流容積(死體積)要儘可能小,流阻損失同時也要儘可能小;
(4)工質密封性要好,連線方式應保證製造工藝性和密封效能。
冷卻器的傳熱形式為對流傳熱,其基本方程式為:





式中, 為管內工質傳到管外冷卻介質的總傳熱量; 為冷卻器的傳熱係數; 為冷卻器管內工質溫度和管外冷卻介質溫度之溫差,取平均值; 為冷卻器的換熱面積,取圓管的外部面積。
三者對系統的影響
研究可知,熱端與冷端溫差越大,最後的熱效率會越高,而通過加快冷卻工質的流速會實現冷端溫度更低,同時冷卻管採用的紫銅,導熱能力很強,完全能保證冷卻器管壁溫度達到室溫。回熱器毎次循環中都會給工質補一次熱量,而且工質速度較快,則冷腔工質溫度會比冷卻器管壁高約10~50K左右。
換熱系統死體積
所謂“死體積”就是指循環過程中工質充盈的必須占用的整體體積,即在循環過程中必須要設定的部分,包括設備死體積、換熱系統死體積(吸熱器死體積、回熱器死體積、冷卻器死體積)和中間連線管體積等三部分。從理論上看,死體積不參與做功,其存在的作用主要是提供工質的流通,但不可取消,同時也不能一味減小,因為死體積太小會造成換熱不充分和流阻增大,反倒產生負面影響。因此,死體積應在四個部分分別最佳化設計,在保證一定換熱面積和低流阻的情況下儘可能小。
特殊加工工藝
換熱系統的設計中運用了大量毛細管,如果採用一般的弧焊或縫焊必然導致熱變形大,一方面容易造成泄漏,另一方面外觀尺寸變形嚴重會使工質的實際工作環境與理論相去甚遠,同時采雷射焊接又不太現實,因此,在吸熱器管與端板之間、冷卻管端板之問均採用了真空釺焊來完成。
真空釺焊,是指工件加熱在真空室內進行,主要用於要求質量高的產品和易氧化材料的焊接。真空釺焊爐包括具存圓簡形側壁和門的壓力容器,門的尺寸和位置設計成可封閉圓簡形側壁的一端。工件處理系統安裝在壓力容器門上,用來支承金屬工件進行熱處理或釺焊。工件處理系統包括使工件在處理過程中轉動的裝置。真空系統可連線到工件,使工件內部的壓力在釺焊過程中低於大氣壓。
真空釺焊技術從四十年代開始至今,已成為一種極有發展前途的焊接技術。最早出現在電子工業上釺焊銅和不鏽鋼的零件,後來又套用到航空工業、原子能工業,在1959年開始套用到製造不鏽鋼的板翅式換熱器上。現在,被廣泛套用於空氣分離設備、石油化工設備、工程機械、車、船和家電等工業部門的板翅式換熱器和冷卻器中。