概念
換熱系統是化工過程中必不可少的子系統,屬於工業輔助系統,工業中通常會採用換熱系統來為核心工藝單元提供能量和將產品冷卻到規定溫度,降低化工過程的能耗、提高能效。例如在硫酸生產過程中如何實現SO氧化過程的連續化換熱,幾十年來一直是硫酸行業注重的研究課題之一。實現過程連續換熱的好處顯而易見。探討一種採用熱管構成傳熱微元段,實現SO氧化過程連續換熱的方法,從而使整個反應過程貼近最佳反應溫度曲線。並作了設計方案的比較,結果表明,採用連續換熱的SO轉化系統,催化劑用量、設備總投資及操作總年費明顯優於普通轉化系統。
採用熱管實現SO2氧化過程連續換熱
隨著近20年來熱管技術的興起與發展,採用熱管技術實現SO氧化過程連續換熱將成為可能。熱管的最大優點在於,它是依靠管內介質的相變熱移送熱量,不但移送熱流率大,而且溫度均勻,冷熱兩端溫差僅1℃左右,有利於反應氣體的均勻冷卻。此外,熱管的外部可加高翅片強化傳熱,總傳熱係數可達100W/(m ·℃)以上,比現有管殼式換熱器的總傳熱係數提高數倍,可大大縮小換熱面積,簡化生產流程,降低設備造價,減少系統氣阻,因此,熱管將成為一種很有前途的SO氧化過程連續換熱元件。
SO2氧化過程的連續換熱方法討論
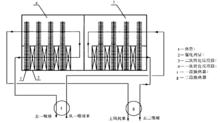
實施該過程的流程示意圖見圖1。該過程將熱管與觸媒沿反應氣流方向分割為有限多個傳熱—反應微元段,每經過一微元(絕熱)反應段,氣溫就沿絕熱線有一小階梯躍升,而緊接一微元傳熱段,將氣體沿水平線冷卻降溫一小階梯,整個反應過程是以反應氣溫度小階梯式跳躍貼近最佳反應溫度曲線,見圖2。
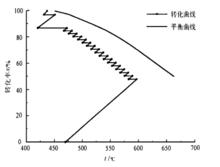
該反應過程比硫酸生產中使用的絕熱反應—分段外部換熱過程相比,能調節控制反應微元段的溫度波動範圍在最佳反應溫度曲線附近,避免絕熱反應溫度波動過大、偏離最佳反應溫度曲線過遠的缺點,可有效提高反應過程的平均轉化溫度,增大轉化速率。由於熱管是一種高效傳熱元件,結構簡單,使用方便,氣阻小,與轉化反應器可構成微縮化的SO氧化反應轉化系統,能省去複雜龐大的外部換熱器,減小設備材耗,降低設備投資,並節省系統風機的操作電耗,是一舉多得的改進方案。
硫酸轉化系統設計方案比較
對年產4萬噸硫酸轉化系統進行了設計比較,在相同的產酸量及8.5%SO入口氣體濃度的條件下,採用外部換熱式的普通兩轉兩吸SO轉化系統,觸媒用量為31.08m ,換熱面積為1077m ,設備總費用為100.5萬元,總年費為48.9萬元。而採用內部換熱式連續換熱兩轉兩吸SO轉化系統,觸媒用量僅為17.37m ,轉化器外換熱器面積為 782.57m ,設備總費用為76.35萬元,總年費為44.6萬元。設計方案的比較結果表明,採用連續換熱的SO轉化系統在設備投資與操作費用上都顯著低於普通兩轉兩吸SO轉化系統。
管式連續換熱催化反應器的設計
研究背景
反應器是食品添加劑、芳香除臭劑、脂肪酸及其衍生物等行業生產中的關鍵設備,是生產過程中一系列設備中的核心設備,反應器的型式、尺寸大小等,在很大程度上決定著產量和質量,因此反應器的選型、設計計算和選擇最最佳化的操作條件,是化工生產中極為重要的課題。
反應器多種多樣,根據結構型式可分為塔式反應器、管式反應器和釜式反應器。根據操作方式可分為間歇、連續、半連續(或半間歇)三種方式。管式反應器是套用較多的一種連續操作反應器,常用的管式反應器有水平管式反應器、立管式反應器、盤管式反應器和U形管式反應器等型式。由於管式反應器結構簡單、加工方、便耐高壓、傳熱面積大,特別適用於強烈放熱和加壓下的反應,易實現自動控制、節省動力、生產能力高等特點,因此廣泛用於氣相、均液相、非均液相、氣液相、氣固相、固相等反應。為保證式反應器內具有良好的傳熱與傳質條件,使之接近於理想置換反應器,一般要求流體在管內作高速湍流運動。管式連續換熱催化反應器設計的基本內容是:選擇合適的反應器型式;確定最佳的工藝條件;計算需要的反應器體積。設計計算中所套用的基本方程式是物料衡算式、熱量衡算式和反應動力學方程式,反應過程如有較大的壓力降並影響反應速度時,還要加上動量衡算式。管式連續換熱催化反應器的設計計算也就是上述方程組的求解。
物料衡算
由於反應器內溫度和反應物濃度等參數隨空間或時間而變,化學反應速度也隨之改變,因而必須選取上述參數不變的微元體積和微元時間作為物料衡算的空間基準和時間基準。
對理想管式流動反應器建立物料衡算式,可以得到理想管式流動反應器的基礎設計方程式。物料在管式流動反應器內進行理想置換流動時,物料衡算式有如下特點:
(1)物料流動處於穩定狀態,反應器內各點物料濃度、溫度和反應速度均不隨時間而變,故可取任意時間間隔進行衡算。
(2)沿流動方向物料濃度、溫度和反應速度的改變。
(3)穩定狀態下,微元時間、微元體積內反應物的積累量為零。
物料衡算式給出了反應物濃度或轉化率隨反應器內位置或時間變化的函式關係。
熱量衡算
反應均有顯著的熱效應,因此隨著化學反應的進行,物系的溫度也有所變化,而溫度變化又會影響反應速度,必須通過熱量衡算計算反應器內各點溫度(或各個時間的溫度),進而確定該點(或該時間)的化學反應速度。
與物料衡算一樣,應選取溫度和濃度等參數不變的微元時間和微元體積為基準。計算熱量時,同一熱量衡算式內各項熱量應取同一基準溫度。
熱量衡算式給出了溫度隨反應器內位置或時間變化的函式關係式。物料衡算式、熱量衡算式和反應動力學方程式是相互依存、緊密聯繫的。在物料衡算和熱量衡算聯立方程時,必須知道反應器內物料流動混合狀況,因為
流動混合狀況影響著反應器內的濃度和溫度分布。生產實際中,細長型的管式流動反應器,可以近似地看成理想置換反應器。
研究結論
進行一個特定的化學反應,採用數學模擬法完成反應器的放大設計後,還需結合反應特點通過對反應器的性能進行比較而選擇適宜的反應器型式和操作方式。比較的依據為:第一,生產能力,即單位時間單位體積反應器所能得到的產物量,也就是在得到同等產物量時所需反應器體積大小的比較。第二,反應的選擇性,即主副反應產物的比例。副產物的多少影響著原料的消耗量、分離流程的選擇及分離設備的大小,因此應選擇能提高主反應產物的操作方式。反應的選擇性往往是複雜反應的主要矛盾,採用數學模擬法可使這一反覆過程變得相對簡單些。 必須指出,採用數學模擬法並不是說可以完全脫離實驗數據,相反,它需要更為精確的實驗數據驗證模擬計算過程和結果正確性,只是需要的實驗量較小。