恆功率自動調速系統
依據作用在截割滾筒上的 外界負載自動調節牽引速度,使截割電動機(主電動機)的實際平均功率始終保持在額定值附近,以獲得機 器能力最大發揮的系統。它包括負載環節在內的閉環 控制系統。從截割(主)電動機測取負載信號與額定值 比較後,經控制器調節牽引速度,牽引速度的變化使截 割滾筒上的負載相應變化,把負載功率限制在額定值 的95%至105%之間。系統還具有人為限定最高牽引 速度的功能,操作人員可根據採煤工藝和配套設備工 序銜接的要求,預先調定最高牽引速度。下頁圖1所示為恆功率自動調速系統原理。
自動調高系統
按頂板和底板起伏變化規律自動調節滾筒工作高度,使滾筒保持沿頂底板截割的系統。 採煤工作面的工作環境是煤塵多、能見度低、噪聲大、 操作人員很難準確判斷滾筒的截割狀態,經常會發生連續截割頂底板岩石而造成損壞截齒或導致其他機件故障,也可能因產生火花而引起工作面爆炸。過厚的頂煤和底煤,會使采高降低,推移輸送機和支架困難,回採率下降。自動調高技術是實現操作人員離開工作面 的關鍵技術,由於煤層厚度及頂底板的岩性和賦存條 件複雜多變,工作環境惡劣,雖然世界各國都在探索各種技術途徑,但大多處於試驗階段。
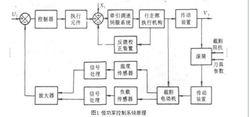
採煤機滾筒自動調高由煤岩分界識別和調高電液伺服系統構成。煤岩分界識別方法主要有自然γ射線探測、截割力制導和記憶數字程式控制三種。這三種滾筒自動調高系統都通過採煤機機載計算機實現。
自然γ射線探測
利用自然γ射線探測煤岩分界的滾筒自動調高系統。裝備這種系統的採煤機割煤時要求在頂底板上留150~200mm的煤皮。頂底板沿牽 引方向或推進方向發生起伏變化時,煤皮厚度也將隨之變化。賦存於頂底板中自然γ射線的衰減量與煤皮厚度成正比。安裝在採煤機上的γ射線探測器所接受的自然γ射線的劑量直接反映煤皮厚度,即煤岩分界的位置。自然γ射線自動調高系統只適用於頂底板岩層含有較強的γ射線,及一次采全高的採煤工作面。
截割力制導
利用滾筒截割力分析作為煤岩分界 識別原理的滾筒自動調高系統。被截割煤體由若干不 同物理性質 (特別是截割阻抗) 的煤分層和矸石層組 成。在有限的範圍內,各煤分層和矸石層的物理性質, 在沿層面方向是近似均勻的。各分層作用在滾筒測量 截齒上的截割阻力各不相同。採煤機工作時測量截齒 上的截割力信號直接反映滾筒在煤層中的截割位置。
記憶數字程式控制
在採煤機工作的第一個循環中,採用較慢的牽引速度,由人工操作調高系統,使滾筒沿煤岩分界線截割。同時採集沿工作面各坐標點x上對應的滾筒工作高度坐標z,構成煤岩分界坐標數組{x,z},存入計算機系統,作為滾筒調高的參考值。第二個工作循環開始,採用正常牽引速度,由計算機對調高系統進行數字程式控制,重複上一刀記憶的 煤岩分界。當頂底板起伏發生變化時,需由操作人員重新設定煤岩分界坐標數組。記憶 數字程式控制滾筒自動調高,是一種比較容易實現的方法,但只能減輕操作人員的勞動強度,而不能完全實現自動化。
工況監視系統
又稱運行狀 態監視系統。線上檢測主要運行參數和運行姿態,使機器各系統 不偏離正常功能的系統。當出現 故障偏離正常功能時,控制系統調整某些運行參數,恢復正常功能,或發出報警信號,由人工停止運行,排除故障。採煤機工況監視用機載計算機實現,由感測器及相應的變換器、數據采 集及傳輸裝置、數據處理、顯示器、報警裝置及鍵盤組 成。感測器多數為模擬量信號,部分為數字量和開關量信號,感測器及其變換器均設計成本安電路。由模數 (A/D)變換器、數模(D/A)變換器和I/O接口組成的信號輸入輸出系統,用於數據採集和變換、輸出控制 和報警信號。操作輸入系統是人與機器進行聯繫,監視運行狀態及設定運行參數極限值的設備,包括通訊接口、LCD液晶顯示器、操作鍵盤(一般為16鍵)及外 存貯器。採煤機機載計算機具有良好的抗干擾和抗震 性能,能適應採煤工作面工作環境。
採煤機工況監視系統的主要功能: ①監視系統故障自檢。採煤機每次重新啟動後,自動檢查感測器信 號、各通訊接口、顯示報警裝置及控制系統的工作狀 態,以及計算機系統的工作模式是否正常。②檢查並顯示採煤機主要運行參數(供電電壓、控制電壓、各液壓系統壓力、滾筒高度等)的實際值。只有當這些參數正常時,採煤機才進入工作狀態。③採煤機運行過程中在 線檢測各監視參數。在顯示器上巡迴顯示參數的實際值和設定的上、下極限值。當發生參數超限時,同時在 所有顯示螢幕上顯示超限參數及其實際值,並發出報 警信號,計算機發出控制指令,或改變運行參數,或停 止採煤機運行,待故障排除後,採煤機方可重新起動。 ④16鍵鍵盤具有人機對話、輸入自檢指令、選擇顯示方式和設定監視參數極限值等功能。
故障診斷
通過分析工況監視所獲得的信息,確 定採煤機故障的部位、性質、程度、類別、原因、故障 的發展趨勢和影響,以便作出控制和維修決策。目的是 防患於未然,提高採煤機可靠性和開機率。採煤機故障 診斷是一項發展中的技術,有待進一步完善提高。
採煤機故障診斷過程的基本環節包 括:①運行參數線上檢測。動態過程的振動、力、轉矩、 功率、位移、溫度等都可用作監視和診斷信號。線上檢 測反映故障症狀最敏感的物理量作為該參數的特徵信 號[x]。②特徵信號分析。所採集的運行參數特徵信 號經濾波、平滑、確定邊界等預處理後,進行歸納分析。 諸如幅域分析、頻域分析、統計分析、時間序列分析等。 ③特徵量選擇。選擇在類間邊界附近對工況狀態相關 性強、反映靈敏的特徵量構成模式向量[x]。併力求 壓縮[x] 的空間維數。④狀態識別。根據特徵參數, 參照某種規範,利用各種知識和經驗,對設備的狀態予 以識別、診斷,建立判別函式D[x]和規定判別準則。 ⑤故障分類及決策。按判別函式實時地對工況狀態進 行分類。運行正常時,計算機發出指令,採煤機繼續運 行。如果故障形成,計算機實時進行故障分析,顯示分 析結果和維修決策,或發出報警信號,或發出停機指 示。