特點
小高爐不同於“土高爐”,根本的不同點在於:①築爐方法不同。爐殼用鋼板製成,內砌耐火磚,形狀呈豎直圓筒狀。
②爐役長。一代高爐(從開爐到大修)可連續生產幾年到十幾年。

③生產機械化。從裝料、送風、排渣到出鐵,整個生產過程基本實現了機械操作,大大減輕了工人的勞動強度,縮短了冶煉時間,提高了生鐵產量和質量。
④容積大。由於採用了先進的送風加熱設備,為加大高爐容積提供了條件。
⑤燃料要求不同。“土高爐”除少數有條件的採用焦炭或煤外,絕大多數使用木炭;煉鐵高爐則由於容積大,料柱高,必須使用強度好、低灰、低硫的焦炭。
技術發展
1960年,全國冶金系統開展技術革新和技術革命,大部分小高爐經過技術改造,實現了風機並聯,多嘴燃燒,蒸汽清灰,高效率破碎焦炭、礦石、燒結礦,煤氣並聯等先進工藝。
1970年1月,一些地區小鋼鐵廠的小高爐,用鋼爐殼取代了過去的磚爐殼。
高爐原料
20世紀50年代,煉鐵小高爐基本“吃生料” ,原礦品位低,一般含鐵在30~40%。如:1971年9月,略陽鋼鐵廠選礦一系列工程竣工後,韓城鐵廠、黑木林鐵礦、漢中地區鋼鐵廠相繼建成選礦設備,到80年代入爐礦石品位提高到48%。1970年,略陽鋼鐵廠用土法生產燒結礦,為土燒結礦生產提供了一定的經驗。1978年,寶雞市紅光鐵廠在土燒結礦生產的基礎上,試驗成功“無煤燒結”,在國內推廣。1978年1月,略陽鋼鐵廠建成24立方米燒結機1台。該機採用兩台2000×4350圓筒混料機混料,SZK1500×4500熱振篩篩分,40立方米帶冷機冷卻。從此,略陽鋼鐵廠高爐結束了“吃”原礦和土燒結礦的狀況。1985年,冶金廳要求地縣小鐵廠變土燒為機燒,一些廠開始建設了燒結機;高爐熟料比從1970年的5.4%提高到77.6%。此外,各生產企業在煉鐵原料的高(品位高)、小(粒度小)、淨(雜質少)、勻(顆粒勻)、熟(提高熟料比)、穩(成分穩定)方面,還採取了其他一些措施。
風溫技術
1958年,陝西的高爐冶鐵採用管式熱風爐,風溫在400℃左右。1970年,一些小鋼鐵廠採用考貝式熱風爐,風溫在600~800℃間。1975年,西安冶金建築學院為涇陽鐵廠設計了球式熱風爐(銅川鐵廠也建設了這種熱風爐),建成投產後,風溫達1000℃左右。隨後,很快普及了這一技術。1980年10月,略陽鋼鐵廠將2號高爐的3座內燃式熱風爐改為馬琴式外燃熱風爐,風溫亦達1000℃左右。到1982年,全省煉鐵高爐的平均風溫為937℃。1985年,全省59立方米以下的高爐均採用球式熱風爐,59方米以上的高爐採用考貝式熱風爐。略陽鋼鐵廠則採用了外延式熱風爐,風溫在1000℃左右,最高達到1100℃。 煤氣淨化:小高爐在採用球式熱風爐的同時,還採用了煤氣除塵淨化技術。1976年,涇陽鐵廠和銅川鐵廠採用布袋除塵工藝。銅川鐵廠使用4個1985厘米的圓筒箱體,涇陽鐵廠採用4個方箱體,每個箱體內裝有玻璃纖維布袋。布袋除塵較濕法除塵節約用水,減少污染,除塵效率高。1981年,略陽鋼鐵廠在高爐煤氣除塵系統中增加了兩台電除塵器。 1985年,西安冶金建築學院和山東省有關單位共同研製成JX-I型蓄能反吹式高爐煤氣布袋除塵器,在寶雞紅光鐵廠、漢中地區鋼鐵廠試用,效果較好。方法是:向箱體反向供給淨煤氣,迫使布袋縮癟,灰塵脫落。
高爐壽命
1972年以前,高爐壽命一般在一年左右。1973年10月,略陽鋼鐵廠首先試用炭搗爐襯。先試驗熱炭搗,因炭固過程工作條件太差,後改為冷炭搗,高爐壽命延長了兩年左右。隨後,幾個地縣鐵廠也開始試用此法。1973年12月,略陽鋼鐵廠改進了爐襯結構,爐底內層採用兩層高鋁磚,其上為炭搗。爐缸自制不燒炭磚(風、鐵口除外),其餘用粘土磚;爐底自爐腹趵光面冷卻壁,爐腰一層支梁水箱。這一改進使高爐壽命延長到5~6年。1981年後,該廠先後用水冷綜合爐底,自焙炭磚內襯砌至爐身1/2處,其餘為粘土磚;爐底至爐缸為光面冷卻壁,其上至爐身1/2為鑲磚冷卻壁,高爐壽命延長到9~10年。
爐前鑄鐵
1972年以前,煉鐵廠都採用爐前沙型鑄鐵,型鐵表面粗糙,塊度大小不勻,事故多,損失大。1972年,略陽鋼鐵廠設計製造成一台單鏈鑄鐵機,從此結束了陝西省爐前沙型鑄鐵的歷史。1975年,該廠又把單鏈帶改為雙鏈帶。1974年,寶雞紅光鐵廠爐前小型鑄鐵機建成投產。
此外,其他機械佬、自動化亦不斷實現。1958年,高爐冶鐵上料基本靠人挑車推,配料靠人工磅秤。1959年,西安八一鐵廠28立方米高爐率先採用皮帶輸送機上料,開始了上料機械化。到1985年,煉鐵高爐的上料系統基本實現了機械化、自動化,部分高爐還採用微機控制和自動稱量。
主要影響
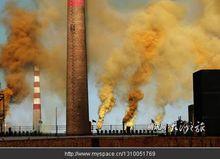
小高爐煙塵瀰漫,對周圍環境影響較大,嚴重干擾居民生活。小高爐在生產過程中,若無環保設備,排放大量有毒的廢氣、廢渣和廢水,直接威脅到人的健康和生命;其次,大部分非法冶煉企業高爐容積小,裝備比較落後,屬於淘汰產業之列。非法小高爐無煙氣淨化措施,氟污染嚴重,難以治理,“三廢”排放嚴重超標。另外,由於這些非法小高爐生產工藝沒有實現與正規冶煉工序的熱裝熱送,熱能利用效率低,浪費能源。
治理方法
氣體回收
河南治理小高爐使用了煤氣化,加設陶瓷熱風爐,然後對排放的餘熱進行有效回收利用。
煙氣餘熱回收途徑通常採用二種方法:一種是預熱工件;二種是預熱空氣進行助燃。煙氣預熱工件需占用較大的體積進行熱交換,往往受到作業場地的限制(間歇使用的爐窯還無法採用此種方法)。預熱空氣助燃是一種較好的方法,一般配置在加熱爐上,也可強化燃燒,加快爐子的升溫速度,提高爐子熱工性能。這樣既滿足工藝的要求,最後也可獲得顯著的綜合節能效果。
此外國內從五十年代開始在小高爐上採用預熱空氣的預熱器,其中主要形式為管式、圓筒輻射式和鑄鐵塊狀等形式換熱器,但交換效率較低。八十年代,國內先後研製了噴流式,噴流輻射式,復台式等換熱器,主要解決中低溫的餘熱回收。在100度以下煙氣餘熱回收中取得了顯著的效果,提高了換熱效率。但在高溫下仍因換熱器的材質所限,使用壽命低,維修工作量大或固造價昂貴而影響推廣使用。
21世紀初國內河南省鞏義市終於研製出了陶瓷換熱器。其生產工藝與窯具的生產工藝基本相同,導熱性與抗氧化性能是材料的主要套用性能。它的原理是把陶瓷換熱器放置在小高爐煙道出口較近,溫度較高的地方,不需要摻冷風及高溫保護,當小高爐溫度1250-1450℃時,煙道出口的溫度應是1000-1300 ℃,陶瓷換熱器回收餘熱可達到450-750 ℃,將回收到的的熱空氣送進窯爐與燃氣形成混合氣進行燃燒,這樣直接降低生產成本,增加經濟效益。
陶瓷換熱器在金屬換熱器的使用局限下得到了很好的發展,因為它較好地解決了耐腐蝕,耐高溫等課題,成為了回收高溫餘熱的最佳換熱器。經過多年生產實踐,表明陶瓷換熱器效果很好。它的主要優點是:導熱性能好,高溫強度高,抗氧化、抗熱震性能好。壽命長,維修量小,性能可靠穩定,操作簡便。是目前回收工業窯爐高溫煙氣餘熱的最佳裝置。
陶瓷換熱器可以用於冶金、有色、耐材、化工、建材等行業主要熱工窯爐,正在為世界的節能減排事業作出了巨大的貢獻。
提高質量
如何提高小高爐生鐵質量
根據張家口市的經驗,要從原料管理、爐前操作、設備維修三個方面下功夫,其中加強原料管理尤為重要。提高生鐵質量的中心要求就在於最大限度地降低生鐵中的含硫量。硫,來自焦炭,來自礦石,要消除它,首先應當把住原料關,限制它入爐。這同衛生工作貫徹“以預防為主”的方針一樣,防的工作做好了,治療的任務就大大減少了;從原料上把硫消除到最低限度,冶煉中的脫硫就比較好辦了。在冶煉前脫硫,矛盾是單一的,操作簡單,事半功倍;把大量硫分帶到爐內去處理,就要引起爐內造渣配料上一系列的變化,就比冶煉前脫硫複雜得多。許多地方小高爐的成功經驗表明:原料管理的基本要求是“粗糧細作”,“細糧精作”,讓高爐吃細糧、吃熟料。做到了這一些,生鐵質量的提高就有了最基本的保證。但這必須進行一系列的細緻的工作。
除了採煤、洗煤、煉焦、採礦、選礦、燒結各個環節上都要努力提高產品質量以外,從煉鐵廠來說,主要是抓住焙燒、破碎、洗選、過磅、上料五個環節,除掉泥、土、沫、雜(雜質)“四害”,實行粒度分級、質量分類、混勻儲存、以爐定料、加強爐料化驗。上面說的這些措施是提高生鐵質量、增加生鐵產量的根本措施。經過層層把關,層層採取措施,把原料中的硫分去掉了絕大部分,其餘的硫分要在冶煉過程中去處理。許多地方小高爐的成功經驗說明:在冶煉中提高脫硫效率,也就是提高生鐵產量的中心環節,是實行高冶煉強度、高風溫、大風量的操作方法;其次要加強技術管理,健全操作規程,建立責任制度,樹立良好的生產秩序。要保證小高爐持續優質高產,還必須加強設備維修工作,制訂合理的檢修規程,準備必要的備品、備件,千方百計向事故作鬥爭。做好了這些工作,就能使機器正常運轉,使高爐鐵水長流。