介紹
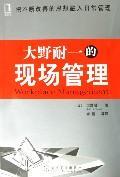
書中講述的內容正是豐田汽車公司從全球汽車業的不景氣以及日本汽車業落後於美國同行業水平10倍的困境中脫穎而出、迅速達到世界領先水平過程的全記錄,因此,對處於同樣境遇和機遇的中國企業有很高的參考價值。
內容
現在,中內外企業都在進行生產管理改革,“豐田生產方式”很自然地成為一門“必修課”。可是,閱讀本書之後發展,現行的“豐田生產方式”與當時的“大野方式”有許多方面已經有所差異,甚至背道而馳,現行的“豐田生產方式”被賦予了更多的日本的文化以及民族精神的內涵,對中國的企業不能100%地適用。因此,本書的最大意義在於使中國的企業以及中國的生產管理者能夠看到原始、最樸實的“豐田生產方式”,取其精華,去其糟粕,探索出適合我國國情的管理方法。
目錄
推薦序
譯者序
再版序言
初版序言
1 君子豹變
2 出現錯誤,坦誠承認
3 錯覺降低效率
4 失敗要以眼見為實
5 潛藏在常識中的錯覺
6 數學計算的誤區
7 不要害怕損失機會
8 限量經營即低成本生產
9 庫存減少,半成品反增
10 量產就是低成本的錯覺
11 無效率的動作不是工作
12 農耕民族更偏好庫存
13 減產也可以提高生產率
14 景氣時也應該考慮合理化
15 準時化生產
16 豐田佐吉翁的“自慟化”思想
17 以提高10倍以上的生產率為目標
18 超級市場方式
19 豐田獨刨的“看板方式”
20 從巴西工廠學來的換模鍛造方法
21 合乎道理才能稱為“合理化”
22 機器應該能夠隨時被停止
23 怎樣以低成本生產
24 不引進時下流行的機器人設備
25 工作就是和下屬比智慧
26 沒有主管的事務現場
27 合理化要不斷地進行
28 困境激發智慧
29 成為值得信賴的“親人”
30 整理·整頓·清掃·清潔·教養
31 改善應該按順序進行
32 可動率與稼動率
33 生產技術與製造技術的差異
34 成本計算的陷阱
35 “豆沙餡餅”方式
36 降低成本唯有依靠生產現場
37 應以最短時問為標準時間
作者簡介
大野耐一,著名的豐田生產方式的創始人。1912年出生於中國大連。1932年從名古屋高等工業學校畢業之後,進入豐田紡織公司,1943年,轉入豐田汽車工業公司。1964年擔任常務董事,1970年擔任專務董事,1975-1978年擔任豐田汽車公司副社長。此後又先後擔任豐田汽車工業公司顧問、全並後的豐田汽車公司顧問、豐田紡織協會會長等職務,於1990年去世。著作有,《豐田生產方式》(鑽石出版社)等。
序言
作為豐田生產方式的創始人,大野耐-先生被譽為“日本復活之父”、“穿著工裝的聖賢”。他一生所著並不繁多,本書就是其經典代表作之一。本書語言質樸,沒有華麗的辭藻,但生動形象的比喻隨處可見。所謂“大道至簡”,通過閱讀不難體會到先生的良苦用心,他力求用最直接的表達和舉例,讓每位讀者都能充分、準確地理解文中所提概念和名詞。
戰後初期的日本,無論從經濟還是技術上,都遠遠落後於歐美已開發國家。但憑藉著強烈的追趕意識和逐步完善的科學管理體系,日本僅僅用了20餘年,便以製造大國的面貌重新矗立於世人面前。“日本製造”也逐步獲得“高品質”的美譽。本書就是來源於那個崛起時代的“日本生產管理教父”的真知灼見。雖然本書成書於1982年,但是對今天正處於從製造大國向製造強國轉型的中國製造,仍具有重要的借鑑和指導意義。
文摘
若是能夠自己親眼證實一下,然後再說同意,並表示“啊,這點我怎么沒想到”,那樣不是有助於更好地展開工作嗎?我認為如果只是一味地研究鑽頭、車床,或者說一味地研究某種特定的技術,不可能提高整體的工作效率,因此,應該採取“集中研磨”。的方式。不過,當我說出“集中研磨”這個詞的時候,有經驗的人一定會說:“不行,那是戰爭時期的做法,已經有過失敗的教訓,因此才改成現今這樣,不能再重蹈覆轍了。”但是,我並沒有見到過戰爭時期的失敗,於是我說只有讓我親眼見到這種失敗,我才能夠徹底地弄明白,我才能夠真正地認同現行的工作方法。
我認為,之所以失敗,一定是有其不可行的因素。那些所謂的失敗發生在供應軍需品的非常時期,技術人員們在軍隊的命令下進行“集中研磨”,必然很不情願,因此結果注定失敗。可是這次是出於我的提議,成功失敗都無所謂,因此,技術人員們沒有壓力,結果卻成功了,任何失敗的跡象都沒有。
在“集中研磨”的過程中,專家們提出了一些我不是很熟悉的細節問題,比如打磨方法應該根據材料的特質有所差別,如果鑄造某種金屬應該在第二次更換鑄造條件,如果鑄造的材料是鐵應該怎樣做等等。其實他們說的這些細節問題我不是十分關心,也不會影響到“集中研磨”的進展。我們需要做的是在工作開始前,讓所有參與“集中研磨”的技術人員都了解這項工作的目的,例如這把軍刀要用來做什麼。至於他們使用什麼機器來製造、使用什麼材料來打磨以及以怎樣的角度去切割,這些只需要確定一個標準,然後大家統一使用這個標準去工作即可。相反,如果要求好幾百個作業員都必須成為研磨專家,那么結果必然是無效率的。
因此,在項目已經失敗或者即將失敗的時候,如果能夠從最基本的工序來仔細地逐一檢查,我認為一定可以阻止失敗的再次發生,也必然會將生產效率提高許多倍。