生平簡歷
1954年,出任豐田汽車公司董事。
1964年升任常務董事,1970年,任專務董事。
1975年,開始擔任豐田汽車公司副社長。
1973年,榮獲藍綬帶獎章。
1990年5月28日去世。
豐田生產方式
樹立目標
1942年豐田紡織解散,大野耐一第二年轉到豐田自動車工業株式會社,為豐田創始人豐田佑吉之子、豐田汽車創始人豐田喜一郎效力。
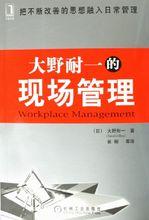
據原豐田工程技術公司董事長堀切俊雄對《中外管理》介紹:第二次世界大戰後,豐田曾陷入非常危險的境地,年汽車銷量下降到了區區3275輛。
汽車銷售不出去,工人開始罷工,而且持續相當長時間,豐田幾乎瀕臨破產。為了挽救豐田,日本銀行組成一個銀行團為豐田提供資金,但是提出的條件是:解僱3000名員工,經營層全部換班,公司一分為二:豐田銷售公司、豐田汽車公司。這等於豐田重新從原點再來一遍。
那時的豐田不但面臨資金短缺,還面臨著原材料供應不足,而且日本汽車製造業的生產率與美國差距巨大。在如此嚴峻的現實面前,豐田喜一郎提出:降低成本,消除不必要的浪費。用三年時間趕上美國!否則,日本的汽車產業將難以為繼!
“三年趕超美國”,創業者的雄心壯志與迫在眉睫目標讓大野耐一這位職業經理人刻骨銘心。由於這樣的追趕意識,大野耐一從此把眼睛死死盯住現場管理。他日思夜想:為什麼美國的生產率比日本高出幾倍?一定是日本存在著大量的浪費!那么如何能找到更好的生產方式呢?
準時化
眾所周知,豐田生產方式的兩大原則是準時化和自動化。先看看這兩個原則的雛形。
關於消除浪費,豐田喜一郎有過這樣一種構想,他說:“像汽車生產這種綜合工業,最好把每個必要的零部件,非常準時地集中到裝配線上,工人每天只做必要的數量。”
大野耐一把豐田喜一郎這個思路套用到汽車的生產現場,形成了一套嚴謹成熟的“準時生產”體系。
首先是生產線的整流化:大野耐一學習福特的流水線工作方式,將“以設備為中心進行加工”的生產方式改變為“根據產品的加工工藝來擺放設備”,形成專線生產,並計算出每個產品的節拍時間。所謂節拍時間,即如生產A產品,一天需要480個,一天的勞動時間是480分鐘,那么就可以計算出,生產一個A 產品的節拍時間是1分鐘。有了這個節拍時間概念,生產線只要按節拍時間持續流動生產即可。節拍時間是TPS中最重要的概念。
其次是拉動式生產。TPS之前的生產方式是生產計畫部門把計畫發給各個工序。由於各個工序發生故障時間不同,導致有的工序生產的部件多,有的生產的部件少,不僅導致生產線運轉不流暢,而且循環往復地造成庫存。為了解決這些問題,大野耐一從美國超市的取貨受到了啟發——其實,大野耐一根本就沒有見過美國超市,只是聽說而已。但這一點也沒有妨礙他的思考和獲益——他開始產生了一種沒有浪費的流程假設。基於這種假設,大野耐一創造了後工序到前工序取件的流程,從而使推動式生產變成了拉動式生產。最後一道工序每拉動一下,這條生產繩就緊一緊,帶動上一道工序的運轉,從而消除了庫存。
自動化
自動化,是在出現問題時讓生產線 自動停止。自動停線的自働化,才能在 現場、 現物根據 現實找到問題的根因,才能從源頭上消除質量問題。
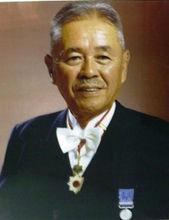
戰後,日本從歐美進口了很多自動化設備。儘管是自動機械,實際上在每台工具機邊還需配備一名工人看管,當發生故障時,再去叫修理人員來修理。
大野耐一認為:這種事真是愚蠢到極點,買來了自動機械,一點好處沒發揮出來,於是就開始考慮如何做到不靠人監視也行呢?
他想到了豐田創始人豐田佐吉的發現。
以前的織布機在織造過程中,如果一根經線斷了,或者是緯線用完了,必須靠人巡迴檢查發現停車處理,不然就會出現大量的不合格品。能不能給設備賦予類似人的“智慧型”,給它裝上判斷設備運行狀態是否正常的裝置,使之在出現上述情況時自動停車,從而提高勞動效率又減少不合格品。自働化思想的誕生和發展,就是在上述大背景下產生的。因此,它與設備本身沒有什麼關係,而是直接針對問題的管理體系。
大野耐一認為,“一切問題都歸結於機器”是一件需要高度警惕的事情。因為機器沒有能力辨別是非,更不可能發現問題和解決問題。於是大野在“自働化”時代中提出了自己的“自働化”的概念:讓機器也有人的智慧——當機器生產出了不合格的產品時,就會“自動”停下來。
機器本身當然做不到這一點,能做到這一點的還是人——機器的操作者。其實,“自働化”不同於“自動化”的核心也正是這一點,即由操作機器的人去發現和解決問題。
大野耐一在其所著的《豐田生產方式》一書中這樣評價“準時化”和“自働化”之間的關係: “準時化”和“自働化”是豐田生產方式的兩大支柱。如果用棒球比賽來打比方的話,那么準時化就相當於團隊協作,也就是通過團隊密切而巧妙地配合,將其實力發揮到極致。而自働化則是要求每一位選手的個人技術要越來越高超,並且進一步使得團隊的整體實力在個人技術提高的基礎上得到更充分的體現。準時化可以讓問題明確化,自働化可以讓解決問題的努力更有效。自働化——讓每一個人提高自己的水平,整個團隊也會因為每一位選手的高超技藝,相互之間的配合變得更加默契,戰法也更加成熟和豐富起來。當然,由此帶來的結果就是:比賽的成績越來越好,也就是企業的經營業績越來越優異。
自動化要追求什麼樣的目標?很多人從不同的角度給出過很多描述。大野耐一所羅列的主要內容有:“明確問題”、“為問題得到順利的解決創造條件”、“確保產品和工作的品質”、“提高對改善必要性的理解”、“持續挑戰更高標準”、“圍繞‘異常’實施有效管理”……
推進自働化需要考慮的問題?
與推進準時化生產的過程一樣,推進自働化也是一個非常艱苦的過程。大野耐一認為,在這個過程中至少需要考慮下列問題:何時以何種方式停止生產線、目視管理、實現自働化的工作邏輯(也就是推導責任的順序)、定義問題的標準、消除故障的方法、從根本上解決問題的方法、返修不良品的方法…… 如果說準時化可以讓問題變得更加明確,那么自働化則可以讓解決問題的努力更富效果。
自動織機
在當時的條件下,豐田佐吉既沒有顧問也沒有助手,既沒有專門的研究室又沒有參考資料,他有時連續幾天從早到晚把自己關在居室里,仰視著“塌塌米”,沉靜地苦想、切磋琢磨,耗費了整整25年的光陰,終於在1926年研製成功了具有類似人的“智慧型”的自動織機。
大野耐一受豐田佐吉的啟發,想到了把感測器裝到機械上。
然而雖然感測器裝上了,卻不知道哪裡的機械停了,這下組長可忙壞了,來回在生產線中奔跑。
這時,大野耐一又想出了一個辦法,裝了一個燈光顯示板——指示燈,這個指示燈與各個工具機相連線,放在一個地方,哪裡發出異常可以馬上知道,大大地提高了組長及修理科的工作效果,有效地保證了生產正常進行。
如果一道工序出現故障所有的工序都要停止,問題就會立刻被表面化,被及時發現,所有的人就都會想辦法及時解決這一問題。改善由此開始。結果,生產線的有效運轉率提升到了95%!
改變世界
大野耐一總是愛在車間走來走去,停下來向工人發問。他反覆地就一個問題,問“為什麼”,直到回答令他滿意,被他問到的人也心裡明白為止——這就是後來著名的“五個為什麼”。
大野耐一推廣TPS的生產方式近似殘酷,他的辦事方法也前所未聞。由於TPS改變了工人們的生產習慣,所以在初期階段沒有人願意跟他合作。
堀切俊雄回憶說:“當時,我和大野耐一在一起工作。說實話,他讓人害怕。當時大野耐一到哪個工廠,哪個工廠的領導就會躲起來!”
當時的大野耐一也非常痛苦。但是,令他慶幸的是,豐田的掌門人支持他,保證了這種變革沒有夭折。
為了實施成功,達到目的,大野耐一不斷地鼓動那些高級經理們。在鼓動和壓力下,人們開始慢慢地接受這種改變。“看板生產”至少花了10年以上的時間才得以在豐田推行成功——直到1973年的第一次石油危機,整個汽車行業出現大量的庫存,這時的豐田不但沒虧本,反而贏利。這才讓那些罵他的人開始相信而接受了他的思想。
生產方式
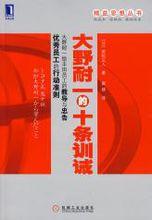
大野耐一在豐田工作了一輩子,在屢經挫折和失敗之後,創造了一套完整的、超常規的、具有革命性的全新生產方式——豐田生產方式(TPS)。
正是1990年,一個周末的清晨。麻省理工學院教授詹姆斯·沃麥克被急促的電話聲驚醒,電話的另一頭是出版社編輯興奮的聲音:“沃麥克博士,書取名叫做《改變世界的機器》,你覺得如何?”這本書,是全球第一本由西方人深入探討豐田汽車管理模式的書籍,是1985年美國麻省理工學院籌資500萬美元的研究項目,是美國人第一次把豐田生產方式定名為Lean Production,即精益生產方式。這個研究成果掀起了一股學習精益生產方式的狂潮。
據《豐田創業史》所述:大野耐一所創始的精益生產方式受到來自各方面的讚揚,但他從不炫耀自己的理念。大野耐一不為創立豐田生產方式而沽名釣譽、邀功請賞,反而一再聲稱其思想精髓來自於豐田佐吉和豐田喜一郎並對他們大加歌頌。
總動員
截止到目前,我們看到的大量資料還是大野耐一時代的豐田生產方式。事實上,自上而下的強壓式的推廣曾招致豐田工人們的不斷反抗。直到上世紀80 年代,豐田內部開始出現了自主研發活動,工人們要自主研究現場管理的改善方法。TPS的基本思想開始滲透到業務的各個環節。於是全面的TPS誕生了。其誕生標誌著豐田生產方式出現了另一個偉大的原則——活性化原則。
活性化
活性化原則的本質是調動員工的上進心及積極性。和美國工廠最大的不同是:美國公司給作業標準,工人們按標準做就行了。而豐田的TOTAL TPS充分相信工人們的智慧,實現現場的活性化,提倡“現場現物”。
現在的豐田,一個產品進入量產前,都有製造準備活動。以前由技術人員進行的改善活動,現在,由一線工人提出思路,參與完成。豐田會抽調出大量的人力和精力來做量產前的改善,充分發揮一線工人的聰明才智。
在豐田汽車所屬主辦工廠之一的岐阜車體工業株式會社MIC生產性研究所和豐田海獅車製造工廠 ,《中外管理》記者一行看到現場到處都有著醒目的“改善看板”。看板的內容分成兩部分,一邊是改善前的狀況,一邊是改善後的狀況。改善效果產生的經濟效益、改善承擔者的姓名及得到的獎勵都寫在看板上公布於眾。
思考空間
在豐田眼裡,沒有消極的員工。只要方法正確,員工都能煥發活力。因為,人都希望有歸屬感,個別人的落後也會在集體向上的帶動下,發生變化。只不過,時間不同而已。讓員工做事情,不求100%的改善或者達到,只要有50%的可能,就開始去行動,在行動中現場現物,持續改善到100%.不要給員工過高的壓力和期望,最好只要讓他伸伸手就能夠到。然後,員工產生一種成就感,進而充實感,大腦才能開始活性化,才能不斷地進取向上。
當然,發揮一線員工的智慧進行改善,並不表示改善目標是自下而上,而是每年度公司都有改善方針,從質量、成本、安全等多個角度制定改善目標,然後,把目標層層分解到每個班組。
不愧為“穿著工裝的聖賢”,晚年的大野耐一在書中留下了感人的反思:“沒有人喜歡自己只是螺絲釘,工作一成不變,只是聽命行事,不知道為何而忙,豐田做的事很簡單,就是真正給員工思考的空間,引導出他們的智慧。員工奉獻寶貴的時間給公司,如果不妥善運用他們的智慧,才是浪費。”