簡介
玻璃瓶一般根據口徑尺寸,成型方法分為2種:吹吹法及壓吹法 。
玻璃膏流入模具,頂桿和底模將料液擠成初胚形狀,此時瓶口成型,瓶身需再經過一次吹制才能成型。整個過程分為兩步,因加工過程中料液溫度會降低,瓶身成型時易產生厚度不均勻現象,整個瓶子的強度取決於最薄弱的部分,影響整個瓶子的強度。為了達到瓶子的設計強度,通過提升材料厚度來實現,瓶子較重。吹吹法適用於製作口徑低於28mm的玻璃瓶。
另一個就是壓吹法制瓶,其中壓吹法為玻璃膏掉入模具後通過壓制,瓶身與瓶口同步成型。瓶身比較均勻,不易出現皺紋等現象,吹制的瓶子重量輕,比同等強度吹吹法制瓶要輕20-50%。普通壓吹法無法製作瓶口低於28mm產品,這種壓吹法制瓶工藝如圖所示。
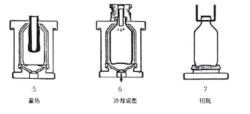
壓吹機
壓吹機是使用壓吹法成型製品的設備,一般先用壓制的方法成型玻璃製品的雛形,然後再用壓縮空氣吹製成成品。生產玻璃瓶的行列機就是常用的一類壓吹法成型機,其特點是:成型速度快、生產效率高、產品質量好。然而在玻璃器皿生產中很少採用 。
基本結構
(1)雛形模側
一個可迴轉的雛形模、壓力氣缸、帶兩瓣口模可迴轉的轉塔機構,以便把雛形模中的料坯帶到吹制工位。
(2)成型模側
吹制工位安裝著兩個兩瓣水冷吹制模(或風冷固定模)、吹氣頭機構、可迴轉及開合的口鉗機構,並裝備有燃燒器以及成型模底部的可迴轉機構。
(3)取出機構
取出成型後的產品,並可對產品進行風冷。
成型工藝過程
當剪刀將玻璃料滴剪下後,可迴轉的雛形模從裝料位置旋進壓制工位,口模合上並下降到雛形模中,根據產品設計的壓制沖頭形成雛形料坯的各種不同的玻璃分布。
可迴轉的轉塔機構將壓好的料坯懸掛在口模上,並帶動其迴轉進吹制工位的吹氣頭下,轉塔轉回壓制工位吹氣頭下,壓在口環上,燃燒器移進料坯下,口鉗機構開始迴轉。此時轉塔在等待雛形模的下一次循環,以便將毛坯帶到第2個吹制工位,同時料坯的預吹和延展開始。
如果是較大的厚底產品,特殊編程的可迴轉模底機構旋進吹制工位中,並可與口鉗迴轉同步,然後成型模合上,同時料坯邊迴轉邊吹氣,同樣的,新的壓制周期開始,並且將料坯懸掛迴轉進第2個工位。
吹制完成後,成型模打開,帶鉗爪的取出機構將產品卸下並旋出到取出工位,經過充分的風冷後將製品放到輸送機構直接進退火爐或者送到注射機上粘上底盤及梃(酒杯)。
相關研究
使用壓吹法製作玻璃瓶中的冷卻問題
玻璃瓶的成形過程是一個逐漸降溫的過程,適度地施以玻璃模具的冷卻是成形控制的重要環節。冷卻不足或冷卻過度或冷卻位置不合理均可引發各類玻璃瓶缺陷。欲求高質量的玻璃瓶和理想的合格率,必須重視和研究玻璃模具的冷卻。
緣於玻璃模具冷卻而產生的玻璃瓶缺陷分為兩種情形,其一為冷卻不足導致玻璃模具溫度高;其二為冷卻過度導致玻璃模具溫度低。
玻璃模具的冷卻歷經水冷、風冷,又演進為垂直氣流冷卻。目前,成形時玻璃模具冷卻仍以風嘴式風冷為主,且此種冷卻方式也較為經濟實用。
“冷卻最需要冷卻的部位”是成形操作過程中對玻璃模具冷卻應掌握的基本原則。初模的上方和成模的下方要強制冷卻,而初模的頸部有時需要減少或避免冷卻甚至施以保溫措施。在使用壓吹法生產時,沖頭和口模的冷卻比較關鍵。端肩的瓶型和長頸的瓶型在肩部和頸部的適當位置施以冷卻。特種玻璃瓶的冷卻應以特殊方式進行。一般初模的冷卻相對要小,成模的冷卻相對較大。
根據玻璃瓶成形操作的多年實踐經驗,筆者總結出玻璃模具冷卻的通用原則:吹吹法生產玻璃瓶時,初形側的冷卻位置在從初模上平面以下50~75mm處為必加吹風口部位,成形側的冷卻位置在從成模下平面以上25~50mm處為必加吹風口位置。
壓吹法生產玻璃瓶時,除沿用吹吹法的上述原則外,在初形側增加的冷卻位置在以不妨礙初模開的調節高度處設異型加長吹口風嘴為宜;在成形側增加的冷卻位置在以不妨礙成模開的高度處設壓帽型加長吹口風嘴為宜。這是壓吹法生產時為防止口部變形所必須的冷卻方式 。
小口壓吹法生產中的一些重要要求
目前,國內對於啤酒瓶的生產工藝可分為吹吹法和小口壓吹法生產工藝,OI和華興兩大玻璃制瓶企業已經開始嘗試小口壓吹法生產啤酒瓶 。
小口壓吹法需要做好以下幾點:
(1)行列機必須要有有效的模具冷卻系統;
(2)加工原料及持續確保玻璃質量的全自動配料間;
(3)熔爐內玻璃液高度水平應該維持在1.0 mm的波動範圍內;料滴重量維持在小於1%的偏差範圍內。
成模和初模需要採用合金鑄鐵材料或者更好的材料,來承受更高的成形溫度、溫度的驟變和耐磨度。口模需要採用銅合金材料或者更好的材料。沖頭一般不能做較大維修,損壞嚴重的要作做報廢處理,材料應採用司太立#12或者碳化鎢。沖頭、初模和悶頭的容量必須控制在極小的公差範圍內。需要通過熱端噴塗及冷端處理,來增加較薄啤酒瓶壁表面的強度及減少其摩擦。