印製電路板部件
正文
以印製電路板為安裝基板,在其上安裝電子和機電元件、器件或其他印製電路板部件,並借板上的印製線路(也可做成電阻、電容、電感等無源電子元件)實現電氣互連的部件。在小型電子設備中,如電子手錶、單板微處理機和小型半導體收音機等,所有元件、器件都裝在一塊印製線路板上。而大型設備(如大型計算機)則由幾十塊到幾千塊印製電路板構成的外掛程式和相應的印製線路底板構成。各種印製電路板部件見圖1。每塊印製電路板部件通常都是一個功能單元。早期的電子設備、電子和機電元件、器件裝在金屬薄板製成的底盤上,用導線實現電氣互連。第二次世界大戰後,隨著印製線路技術的發展,電子設備特別是電子計算機,逐漸形成了以印製電路板部件為基礎的結構體系。其優點是電性能好,可靠性高,體積小,成本低,並可實現自動化生產。
印製電路板部件屬於第二、第三級組裝(見電子組裝級),其組裝方式有兩種。①平面組裝或二維組裝:元件、器件安裝在一個平面上(圖1),用印製電路板進行互連。為了提高組裝密度,在印製電路板正、反兩面均可安裝元件、器件,或在印製電路板中間夾一層金屬板,以提高冷卻能力等。②模組式組裝或三維組裝:為了提高組裝密度,一般用相互平行的兩塊印製電路板部件組成一個空間,在空間內安裝元件、器件,或在印製板的正、反兩面安裝元件、器件,板間用線纜或連線器互連;也可像架橋一樣,元件、器件的腿分別架在兩塊印製電路板上,稱夾心式模組(圖2)。印製電路板部件結構設計必須考慮電路區劃與標準化、組裝型式、元件和器件的合理布局、組裝結構、冷卻方式、機械動態特性等問題。
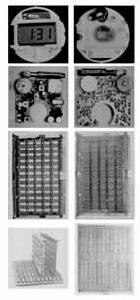
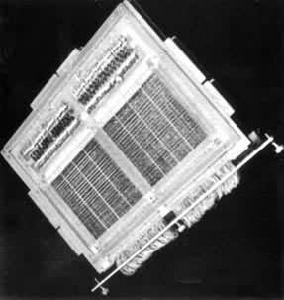
組裝型式 根據功能、元件和器件的數量、組裝密度、環境要求、冷卻、外連引出線數目以及工藝和材料的要求選擇組裝型式。
元件和器件的合理布局 必須符合電氣性能、工藝、散熱和機械要求。
組裝結構 根據需要,在印製線路部件上增加不同的附加結構,如骨架、加強筋、各種結構件、面板、手把、插拔附屬檔案、禁止及連線器等。
冷卻方式 常用的冷卻方法有:自然冷卻、強迎通風冷卻、液體冷卻、蒸發冷卻及半導體致冷等(見電子設備熱控制)。
機械動態特性 要適應運動狀態下工作和運輸的要求。
除上述要求外,在設計中還必須考慮人-機聯繫和可靠性問題。
印製電路板部件組裝,從元件、器件準備到部件檢驗,均已實現機械化和自動化。印製電路板部件組裝的設備有元件、器件老化和自動檢測分類,元件、器件引線整形,清洗,浸錫等設備,元件、器件自動插裝機(圖3),自動和半自動繞接機以及各種自動錫焊設備等。電子元件、器件一般都是插入式安裝。為提高組裝密度,直接用晶片或晶片載體組裝。
發展
近十幾年來,我國印製電路板(PrintedCircuitBoard,簡稱PCB)製造行業發展迅速,總產值、總產量雙雙位居世界第一。由於電子產品日新月異,價格戰改變了供應鏈的結構,中國兼具產業分布、成本和市場優勢,已經成為全球最重要的印製電路板生產基地。印製電路板從單層發展到雙面板、多層板和撓性板,並不斷地向高精度、高密度和高可靠性方向發展。不斷縮小體積、減少成本、提高性能,使得印製電路板在未來電子產品的發展過程中,仍然保持強大的生命力。
未來印製電路板生產製造技術發展趨勢是在性能上向高密度、高精度、細孔徑、細導線、小間距、高可靠、多層化、高速傳輸、輕量、薄型方向發展。
據前瞻網《中國印製電路板製造行業市場前瞻與投資機會分析報告前瞻》調查數據顯示,2010年中國規模以上印製電路板生產企業總計908家,資產總計2161.76億元;實現銷售收入2257.96億元,同比增長29.16%;獲得利潤總額94.03億元,同比增長50.08%。
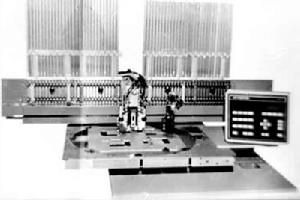