刀角來源
車刀的組成
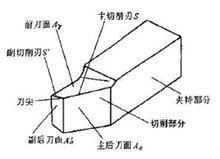
刀由刀體和刀柄兩部分組成,刀體擔負切削任務,因此又叫切削部分。刀柄的任務是把車刀裝夾在刀架上。如下圖所示:
1、前刀面:切屑排出時經過的表面。
2、後刀面:後刀面又分主後刀面和副後刀面。主後刀面是和工件上過渡表面相對的車刀刀面;副後刀面是和工件上已加工表面相對的車刀刀面。
3、主切削刃:前刀面和主後刀面相交的部位,它負擔著主要切削任務。
4、副切削刃:前刀面和副後刀面相交的部位,它負擔著車刀次要的切削任務。
5、刀尖:主切削刃和副切削刃相交的部位。為提高刀尖的強度,常把刀尖部分磨成圓弧型或著直線型,圓弧或直線部分的刀刃叫過渡刃。
6、修光刀:副切削刃前段近刀尖處的一段平直刀刃叫修光刀。裝夾車刀時只有把修光刃與進給方向平行,且修光刃的長度大於進給量時才能起到修光工件表面的作用。
刀角標註的輔助平面
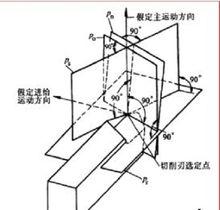
測量車刀角度的輔助平面 ,為較準確測量車刀的幾何角度,假設了三個輔助平面,即切削平面,基面和截面。如圖所示:
1、切削平面:過車刀主切削刃上一個選定點,並與工件過渡表面相切的平面叫切削平面。
2、基面:過車刀主切削刃上一個選定點,並與該點切削速度方向垂直的平面叫基面。
3、截面:截面有主截面P和副截面P´之分。過車刀主切削刃上一個選定點,垂直於過該點的切削平面與基面的平面叫主截面。
切削平面,基面和截面互相垂直,構成一個空間直角坐標系。
刀角分類
前角
影響切削變形和切削力的大小、刀具耐用度和加工表面的質量。增大前角能使刀刃變得鋒利,使切削更為輕快,可以減小切削變形和摩擦,從而減小切削力和切削功率,切削熱也少,加工表面質量高。但增大前角會使刀刃和刀尖強度下降,刀具散熱體積減小,影響刀具的耐用度。前角的大小對表面粗糙度、排屑及斷屑等也有一定影響。
后角
減小後刀面與工件的摩擦和後刀面的磨損,其大小對刀具耐用度和加工表面質量都有很大影響。后角增大,摩擦減小,刀具磨損減少,也減小了刀具刃口的鈍圓弧半徑,提高了刃口鋒利程度,易於切下薄切屑,從而可減小表面粗糙度,但后角過大會減小刀刃強度和散熱能力。
主、副偏角
主偏角和副偏角對刀具耐用度影響很大。減小主偏角和副偏角可使刀尖角er增大,刀尖強度提高,散熱條件改善,因而刀具耐用度高。還可降低加工表面殘留面積的高度,故可減小加工表面的粗糙度。主偏角和副偏角還會影響各切削分力的大小和比例。如車削外圓時,增大主偏角,可使背向力減小,進給力增大,因而有利於減小工藝系統的彈性變形和震動。
刃傾角
刃傾角主要影響切屑流向和刀尖強度。刃傾角為正值,切削開始時刀尖與工件先接觸,切屑流向待加工表面,可避免纏繞和劃傷已加工表面,對精加工和半精加工有利,刃傾角為負值時,切削中切屑流向已加工表面,容易纏繞和劃傷已加工表面。負刃傾角有利於提高刀尖強度。刃傾角為負值時,切削運動中刀具與工件接觸的瞬間,刀具切削刃中部先接觸工件,刀尖後接觸工件,尤其是斷續切削時,切削刃承受刀具與工件接觸瞬間的衝擊力,可避免刀尖受衝擊,起保護刀尖的作用,且負刃傾角利於刀尖散熱。刃傾角為正值時,刀具與工件接觸的瞬間是刀尖先接觸工件,刀尖承受刀具與工件接觸瞬間的衝擊力,容易受衝擊損壞。
刀角選擇原則
材料原則
1、根據工件材料選擇前角。加工塑性材料時,特別是硬化嚴重的材料(如不鏽鋼等),為了減小切削變形和刀具磨損,應選用較大的前角;加工脆性材料時,由於產生的切屑為崩碎切屑,切削變形小,因此增大前角的意義不大,而這時刀屑間的作用力集中在切削刃附近,為保證切削刃具具有足夠的強度,應採用較小的前角。
工件強度和硬度低時,切削力不大,為使切削刃鋒利,可選用較大的甚至很大的前角。工件材料強度高時,應選用較小的前角;加工特別硬的工件材料(如淬火鋼)時,應選用很小的前角,甚至選用負前角。因為工件的強度、硬度愈高,產生的切削力愈大,切削熱愈多,為了使刃具有足夠的強度和散熱,防止崩刃和磨損,應選用較小的前角。
2、根據加工性質選擇前角。粗加工時,特別是斷續切削或加工有硬皮的鑄、鍛件時,不僅切削力大,切削熱多,而且承受衝擊載荷,為保證切削刃有足夠的強度和散熱面積,應適當減小前角。精加工時,為使切削刃鋒利、減小切削變形和獲得較高的表面質量,前角應取得較大一些。
數控工具機、自動工具機和自動線用刀具,為保證刀具工作的穩定性,使其不易發生崩刃和破損,一般選用較小的前角。
力學原則
(1)根據切削厚度選擇后角。合理后角大小主要取決於切削厚度(或進給量),切削厚度h愈大,則后角應愈小;反之亦然。如進給量較大的外圓車刀后角為6°~8°,而每齒進刀量不超過0.01mm的圓盤銑刀后角為30°。這是因為切削厚度較大時,切削力較大,切削溫度也較高,為了保證刃口強度和改善散熱條件,所以應取較小的后角。切削厚度愈小,切削層上被切削刃的鈍圓半徑擠壓而留在已加工表面上並與主後刀面擠壓摩擦的這一薄層金屬占切削厚度的比例就越大。若增大后角,就可減小刃口鈍圓半徑,使刃口鋒利,便於切下薄切屑,可提高刀具耐用度和加工表面質量。
(2)適當考慮被加工材料的力學性能。工件材料的硬度、強度較高時,為保證切削刃強度,宜選取較小的后角;工件材料的硬度較低、塑性較大以及易產生加工硬化時,主後刀面的摩擦對已加工表面質量和刀具磨損影響較大,此時應取較大的后角;加工脆性材料時,切削力集中在刀刃附近,為強化切削刃,宜選取較小的后角。
(3)考慮工藝系統的剛性。工藝系統剛性差,易產生震動,為增強刀具對震動的阻尼,應選取較小的后角。
(4)考慮加工精度。對於尺寸精度要求高的精加工刀具(如鉸刀等),為減小重磨後刀具尺寸的變化,保證有較高的耐用度,后角應取得較小。車削一般鋼和鑄鐵時,車刀后角常選用4°~8°。