背景介紹
經濟的快速發展對能源需求急速增加,各種石油資源被廣泛開採利用,劣質原油的產量和加 工量也逐年上升。加工劣質原油給煉化企業帶來 了經濟效益,同時也帶來了許多亟待解決的問題。 近年來,對劣質原油的加工多有研究,包括有:全 廠加工總流程、裝置的配置;設備和工藝管道的選材;原油蒸餾裝置的一脫三注;低溫部位腐蝕監測;注入高溫緩蝕劑等,煉油生產裝置已能夠更好地適應加工劣質原油的需要。
針對高硫、含酸等劣質原油的加工,煉油及石 油化工企業往往採用渣油加氫處理和延遲焦化並存的重油加工技術路線,以達到提高輕質油收率,減少項目投資的目的。在原油加工總流程對各生產裝置的要求中, 常減壓蒸餾裝置大多是生產石腦油、煤油、柴油、輕蠟油、重蠟油和渣油的方案。為了滿足全廠原油加工總體方案的需要,常減壓蒸餾裝置多採用 初餾(閃蒸)→常壓蒸餾→減壓蒸餾的技術路線。 原油常減壓蒸餾的工藝過程是加熱、汽化、冷 凝、冷卻、傳質、傳熱密切結合的物理過程。換言之,裝置需要消耗一定的能量,通過上述過程把原油分離成滿足二次加工裝置需要的各種餾分。
恰如其分地分離原油各餾分段,是常減壓蒸餾裝置的基本任務,也是必須重視的首要問題。任何分餾的不足都會影響到目標產品的收率和質量,並直接影響到下游裝置的生產和全廠的經濟效益。而任何過分的分餾,都將會增加不必要的投資並消耗過多的能量。因此,原油常減壓蒸餾的工藝流程和設備配置必須在滿足生產任務要求的同 時,恰如其分地分離原油。這直接關係到目標產品的收率和質量,也與裝置的建設投資、能量消耗緊密關聯。
兩段蒸餾技術
採用兩段減壓蒸餾技術,滿足目標產品的質量和數量要求,同時實現恰當地分離原油,達到常減壓蒸餾裝置投資和 能量消耗的最小化。兩段減壓蒸餾的基本流程見下圖:
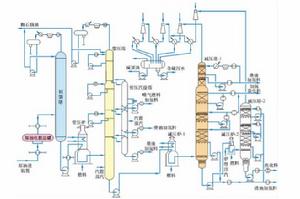
與常減壓蒸餾的一般流程相比,兩段減壓蒸餾技術的流程主要特點如下:一是取消了外甩常壓重油流程,可以使原油中的柴油組分得以全部回收;二是第一段減壓蒸餾的目的是生產加氫裂化原料,切割點在 510 ℃左右,產品質量很好,操作條件也較為緩和,可以採用乾式減壓蒸餾技術,有利於裝置節能;三是第二段減壓蒸餾的目的是生產焦化原料,採用減壓深拔技術,可以根據焦化裝置的技術和生產情況靈活調節拔出深度和第二段減壓蒸餾的進料量,以滿足焦化裝置的生產需 要,實現生產劣質焦化原料,改善渣油加氫處理裝 置原料質量的意圖。
在兩段減壓蒸餾技術流程中,第一段減壓蒸餾的減壓渣油除作為第二段減壓蒸餾的原料外,剩餘渣油經換熱後直接送出裝置作渣油加氫處理 裝置的原料,不存在渣油加氫處理原料被過分蒸餾又兌回去的現象。避免了由此帶來的設備投資的增加和加工能耗的浪費。第二段減壓蒸餾塔內 可根據具體項目情況,僅設定 2~3 段填料,全塔 壓力降可以達到 800Pa 以下,有利於減壓深拔。 第二段減壓蒸餾塔僅設定2 個側線抽出(包括過汽化油),作為渣油加氫處理原料, 可以在適當的位置 併入渣油加氫處理原料參與換熱,流程簡單。
兩段減壓蒸餾技術的減壓塔頂抽真空系統採用“2-1-1”形式,即減頂一級抽空系統設定兩組並聯,分別用於一段和二段減壓塔頂抽真空,兩路塔頂氣體在經過一級抽空系統後混合,之後依次進入減頂二、三級抽空系統,實現兩點抽真空技術, 簡化了抽真空流程和投資。 與常減壓蒸餾一般流程相比,兩段減壓蒸餾技 術僅增加了一台減壓深拔加熱爐、一座設有2~3段 填料床層的減壓塔和5~7 台機泵,第一段減壓蒸餾的減壓塔和減壓加熱爐的規格尺寸也較一般流程減壓蒸餾塔和減壓加熱爐的尺寸明顯減小。
廢水處理
在釷的純化和四氟化釷晶體製備過程中所產生的工藝廢水含有硝酸、氟離子及較強的放射性(總放射性強度為n×10居里/升)。對這種廢水處理提出了兩段蒸餾-水泥固化處理方案,收到了良好的效果。
兩段蒸餾的第一段是在精餾設備中進行,此過程是將釷射氣與其他長壽命的放射性同位素分離。餾出液的放射性強度比原液降低了兩個數量級(由n×1 0居里/升降到n×10居里/升),這種餾出液無需另行處理,只要放置八天以上,其放射性強度即可衰減至排放標準(n×10居里/升)。
第二段蒸餾是將精餾得到的中間濃縮液在簡單蒸餾設備中進行減壓蒸餾回收硝酸。最後,蒸餾殘液(其放射性強度為n×1 0居里/升)經石灰中和後採用水泥固化方法將放射性固定在水泥塊中,這種水泥塊表面再塗上一層瀝清,以防止放射性遇水被遷移。此種含放射性的水泥塊可適當地貯存起來,這樣就較好地防止了放射性的擴散與污染(工藝過程見流程圖)。
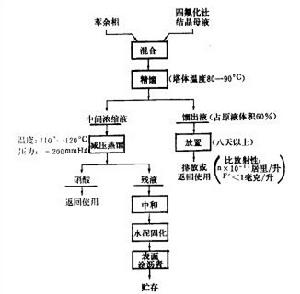