概述
2008年下半年,受國際國內巨觀經濟形勢影響,國內供電負荷增長趨緩,在相當數量火電機組出力受限的情況下,風電發展勢頭依然迅猛,風電葉片投資呈現逆市上揚的良好發展勢頭。葉片是風電部件中確定性較高、市場容量較大、盈利模式清晰的行業。隨著供需緊張形勢的緩解,葉片行業將經歷從紛亂到寡頭、從短缺到均衡、從暴利到薄利的過程,市場將形成數個1000套以上規模的寡頭,這些企業將獲得高於行業平均水平的盈利能力,而其他廠商將逐漸被邊緣化。隨著風電葉片市場規模的擴大,成本和售價都將下降,但具備規模、技術和成本優勢的企業成本下降速度將超過售價降低速度,盈利超過平均水平。未來的行業競爭格局要求廠商規模擴大、成本降低、並在技術上保持一定優勢。
設計
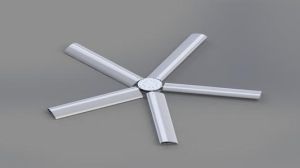
葉片的設計初衷是獲得動力學效率和結構設計的平衡。材料和工藝的選擇決定了葉片最終的實際厚度和成本。結構設計人員在如何將設計原則和製造工藝相結合的工作中扮演著重要角色,必須找出保證性能與降低成本之間的最優方案。
葉片受力分析:葉片上承受的推力驅動葉片轉動。推力的分布不是均勻的而是與葉片長度成比例分布。葉尖部承受的推力要大於葉根部。
大梁設計:由於葉片自重和外部推力產生的彎曲變形是葉片的最主要載荷,為了提高彎曲性能,在葉片的長度方向上採用單向纖維布,且中間通過抗剪腹板將上下兩層梁帽儘可能分隔開,抗剪腹板採用對角鋪放的雙向纖維布加泡沫(PET)芯材構成,起到增加整體剛性的作用。
內部梁結構:為了降低生產成本,設計中可以去除一些不必要的材料,常見的葉片都採用中空式設計。
葉殼:葉殼的作用主要是提供空氣動力學外形。葉殼的夾芯結構增加了剛性,夾芯結構由玻璃鋼表層中間加泡沫(PET)芯材或巴沙輕木(BALTEK)芯材構成。夾芯結構具備足夠的剛性承擔彎曲載荷同時防止脫粘。葉殼中的對角分布的纖維提供了必要的抗扭剛性。
葉根設計:葉根部分通常設計為圓形。同時為了滿足維護等需要,葉片根部多以螺栓連線以便於拆裝。對於金屬大梁可以採用焊接的法蘭連線。
幾何尺寸最佳化設計:在不改變葉片幾何外形的條件下,通過調整梁帽的薄厚來改變葉片性能,降低生產成本。厚度較薄的葉片需要配以更厚的梁帽,但會增加生產成本。同時腹板強度也需提高,但因為厚度變薄所以總的材料用量沒有明顯變化。綜上所述,幾何尺寸的最佳化設計需要從風機設計,載荷分析,結構設計和製造成本等多方面綜合考量才能獲得最佳的結果。
問題原因
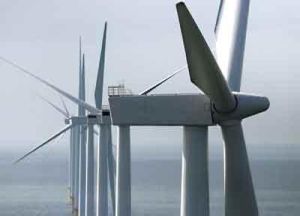
1設計不完善
1.1面對降低成本的壓力
為了追求更高的利潤,管理層要求設計出低廉的部件,以便使企業有更大的空間。設計部門有時不得不做出妥協,比如,減小葉片的葉根直徑的方式來減少輪轂和葉片的成本,但是葉根尺寸減小後會導致葉片強度不夠,再如,選擇質量不佳但價格便宜的原材料,這往往導致葉片出現致命的缺陷。
1.2擅自更改生產工藝
1.3極限設計
葉片的設計需要考慮到機組其他部件的要求與配合,例如,塔架與葉片的間距通常是設計葉片強度時需要考慮的一個原因,主軸和軸承也對葉片的重量提出要求,如果這些參數考慮不周就會使葉片設計達到極限值。
1.4安全質量降低
2生產缺陷
2.1使用不合理的材料
2.2不嚴格的質量控制
2.3生產工工藝過程過於複雜,很難生產質量一致的產品
3自然原因
主要包括:雷擊、空氣中的顆粒、高速風、剪下風、惡劣氣候、疲勞壽命
4運行和維護不當
4.1超額定功率運行
4.2失控
當機器変槳系統出現故障,機器上的剎車不會使葉輪停止轉動,葉片出現失控,會繼續快速鏇轉,嚴重會導致葉片拋出,造成風機災難性事故。
4.3缺少預防性維護
在風機的日常運行維護時,葉片往往得不到重視。可是葉片的老化卻在陽光,酸雨,狂風,自振,風沙,鹽霧等不利的條件下隨著時間的變化而發生著變化。在地面一旦發現問題,就意味著問題很嚴重。葉片的日常維護很難檢查和維護到葉片,在許多風場葉片都會因為老化而出現自然開裂,沙眼,表面磨損,雷擊損壞,橫向裂紋等。這些問題如果日常維護做到位,就可以避免日後高額的維修費用、減少停機中造成的經濟損失。
損壞類型
主要有以下幾種:普通損壞型、前緣腐蝕、前緣開裂、後緣損壞、葉根斷裂、表面裂縫、雷擊損壞等。
葉片裂紋維護
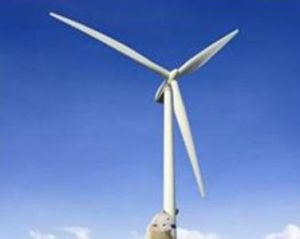
裂紋產生的原因應力集中。採用有限元計算分析得出,轉輪在水壓力及離心力的作用下,大應力區主要分布在轉輪葉片周邊上,按第三強度理論計算的相當應力沿葉片周邊分布。一般轉輪葉片存在四個高應力區,他們的位置在葉片進水邊正面(壓力分布面)靠近上冠處;葉片出水邊正面的中部;葉片出水邊背面靠近上冠處;葉片與下環連線區內。鑄造缺陷及焊接缺陷。鑄造氣孔、鑄造砂眼等在外部應力的作用下可能會成為裂紋源,造成裂紋的產生。由於轉輪葉片與上冠、下環的厚度相差大,在冷卻過程中易產生縮孔、疏鬆等。鑄焊結構的轉輪,若焊接工藝不當或焊工沒有按照焊接工藝的要求進行焊接,在焊縫及熱影響區也會出現裂紋。
原設計問題,轉輪葉片與上冠、下環間的過渡R角設計較小,引起應力集中。運行上的原因,長期低負荷、超負荷或在振動區運行會使葉片在交變應力作用下產生裂紋或裂紋情況加劇。裂紋無損探傷檢查在大修時對轉輪進行無損探傷檢查,及時處理缺陷,消除事故隱患是十分必要的。嚴重的裂紋等缺陷用肉眼和放大鏡外觀檢查即可發現,但較細小的缺陷和內部的缺陷必須用無損探傷檢查。
常用的無損檢測方法有以下幾種:磁粉探傷、滲透探傷、超音波探傷、金屬磁記憶、射線檢測等。