簡史
從含釩鐵礦中回收釩是從19世紀初期開始的。德國和法國在第二次世界大戰時期,用高爐—托馬斯轉爐法從含釩0.06%~0.10%的洛林鐵礦中(不含鈦)回收釩。以含釩鐵礦作為高爐原料生產生鐵時釩也被還原,獲得含釩0.10%~0.15%的鐵水,用此生鐵煉鋼時釩又被氧化進入托馬斯爐渣中,爐渣含釩量可以達到0.5%,是一種無直接使用價值的低釩渣。德國赫爾曼·戈林鋼廠將這種低釩渣與轉爐鋼廠的其他產物(如廠房屋頂積灰,含0.8%~1.0%釩)在另一座高爐內冶煉成含釩和含磷較高的生鐵,再經托馬斯轉爐吹煉得到含釩量較高的釩渣,可直接作為化工廠生產釩的原料,但含釩鐵水提釩後含磷較高,給煉鋼帶來困難。
釩鈦磁鐵礦是一種含釩高的鐵礦石,由於其含鈦量高在本世紀初未能作煉鐵用原料,直到20世紀中期,釩鈦磁鐵礦的高爐冶煉技術獲得突破以後,才作為高爐煉鐵的原料。從釩鈦磁鐵礦回收釩的第一代工藝是用釩鈦磁鐵礦作為生產釩的原料,而提釩後副產品含有鈉鹽與大量TiO而不能單獨作為高爐原料使用,甚至作為廢料堆存,提釩與鋼鐵生產未能結合起來,此工藝只適合於釩鈦磁鐵礦含釩量高、化學藥品和礦石成本低的情況,1956年芬蘭建成了奧坦馬基釩廠。從釩鈦磁鐵礦回收釩的第二代工藝是釩渣提釩法,其特點是提釩與鋼鐵生產緊密結合在一起,60年代中期南非海維爾德鋼和釩公司採用迴轉窯—電爐—搖包提釩工藝流程生產釩渣。迴轉窯預還原、電爐熔煉生產含釩生鐵,在搖包中生產釩渣與半鋼,半鋼在頂吹氧轉爐內煉成鋼然後軋成鋼材。
60年代中期前蘇聯首先採用高爐一頂吹氧氣轉爐法工藝流程提釩。高爐以釩鈦磁鐵礦為原料生產含釩生鐵,在頂吹氧氣轉爐里使鐵水中釩氧化生成VO5進入爐渣與鐵水分離,半鋼移至另一座頂吹氧氣轉爐繼續吹煉成鋼。此法的各項技術經濟指標都優於托馬斯爐法,成為當今鐵水提釩的主要方法。中國釩鈦磁鐵礦資源豐富,從釩鈦磁鐵礦中回收釩的研究也最活躍。60年代中期馬鞍山鋼鐵公司、承德鋼廠採用高爐一側吹空氣轉爐法提釩,獲得了優質釩渣和半鋼。70年代初攀枝花鋼鐵公司開始了高爐—鐵水霧化法提釩試驗,成功後建成了年處理120萬的鐵水霧化提釩生產線。
進入80年代後,一些廠相繼用頂吹氧氣轉爐替代了側吹空氣轉爐。具有代表性的現代鐵水提釩生產的工藝流程如圖1所示。該流程從釩鈦磁鐵礦中回收釩時採用燒結機、高爐、轉爐等專用設備,將提釩與鋼鐵生產結合起來,生產能力高,可控性好,各項技術經濟指標穩定。
原理
含釩生鐵提釩工藝以選擇性氧化為理論基礎。向鐵水吹入空氣或氧氣,必須使鐵水中釩迅速、優先氧化,而其他組分少氧化,方能獲得含釩高的釩渣。吹煉過程中應使鐵水中的碳氧化最少,保證半鋼煉鋼時仍有足夠的化學反應熱。鐵的損耗要降至最低限度,即半鋼的收得率要高,以降低釩渣生產成本。
含釩鐵水的主要組分除Fe、C、V外,還有Ti、Cr、Si、Mn、P等,在氧化性氣氛下都能被氧化生成氧化物,但在一定溫度下的各組分與氧的親和力及氧化物標準生成自由能是有差異的,導致了各組分具有不同的氧化順序和氧化速度。在鐵水提釩過程中可以控制的主要熱力學參數是溫度、渣的氧化性和酸鹼度。
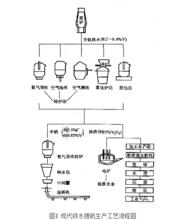
工藝方法
從含釩鐵水中提取釩的主要方法有轉爐提釩、搖包提釩、霧化提釩以及槽式爐提釩和鐵水罐提釩等。前3種是現代鐵水提釩法的主流,它們都採用專門設備,工藝可控性好,各項技術經濟指標穩定。
槽式爐法
含釩鐵水以恆定的流速流入槽式爐內,同時通過沿爐體特定部位的噴嘴以與鐵水相同的流速吹入空氣、氧氣或富氧,使Si、Mn、V等元素氧化並從鐵水中分離出來。槽式爐一般由三段組成:(1)鐵水流量控制段,即前膛或中間罐,藉以控制鐵水以恆定的流速流入下一段。(2)吹煉段,以側吹、底吹、頂吹或綜合吹的方式,向熔池吹入空氣、氧氣或富氧,並加入適量冷卻劑掌握熔池的吹煉溫度。(3)半鋼—釩渣分離段,半鋼與釩渣一起進入該段,用機械法將釩渣扒出回收。槽式爐法的主要工藝參數是供氣壓力和流量、噴嘴高度、熔池深度、吹煉時間。熔池溫度也應控制在1400℃以下。該法優點是不需高大廠房和大型起重設備,但可控性差,耐火材料蝕損嚴重。
鐵水罐法
含釩鐵水盛於鐵水罐內,將可升降的噴槍插入鐵水中進行吹釩。噴槍一般為管式,外部用耐火材料保護。噴槍的插入深度、吹入氣體的壓力和流量、吹煉時間、熔池溫度是鐵水罐法提釩的重要工藝參數。該法工藝可控性差,噴濺厲害,半鋼收得率低。鐵水罐提釩還可以由氧氣或空氣作載體通過插入式噴槍同時向鐵水噴吹NaCO。該法的工藝特點是鐵水中矽、錳、釩被氧化的同時,硫、磷也一起被氧化進入釩渣中,其優點是半鋼中余釩低,而且硫、磷雜質元素含量少,特別利於半鋼的冶煉。但NaCO在高溫下易揮發,對環境有污染,同時對設備及耐火材料的蝕損也很嚴重。
影響因素
溫度控制
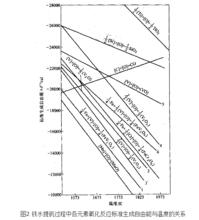
釩的氧化反應屬於放熱的多相複雜反應,但其熱效應值在數量上差別很大,反應產物的表示也各不相同。鐵水提釩過程中各元素的氧化反應的標準生成自由能與溫度的關係示於圖2。由圖可見,提釩初期熔池溫度比較低(約1300℃左右)時
(△F°)<(△F°)<(△F°)<(△F°)V<(△F°)<(△F°)C
即Ti、Si、Cr、V、Mn等元素都比碳優先氧化,這些元素的氧化放出大量的熱,使熔池溫度迅速上升,當溫度超過1400℃(1673K)時,碳與氧的親和力大於釩與氧的親和力,即(△F°)V>(△F°)C,碳即開始大量氧化並抑制釩的氧化,降低釩的回收率。同時碳的大量氧化又使半鋼中碳含量過低,給半鋼煉鋼帶來困難。故鐵水提釩過程為了達到“提釩保碳”的目的,需要嚴格控制好熔池溫度,將熔池溫度控制在1400℃以下。
釩渣的氧化性
鐵水提釩在適宜的熔池溫度下,釩在釩渣與金屬相間的分配係數(V)/[V]與釩渣中氧化鐵含量和二氧化矽含量之比(TFe)/(SiO)呈明顯的線性關係。
各種鐵水提釩法的生產實踐表明,釩渣中氧化鐵含量都很高,一般超過30%。若釩渣中氧化鐵含量過高就會降低VO含量,致使提釩時鐵耗增加,並使釩渣的後步加工變得複雜。因此,在保證釩有較高的氧化率下,釩渣中氧化鐵含量並不是越高越好。
釩渣鹼度
生產實踐證明釩渣的酸度或鹼度對釩的氧化有顯著影響。在合適的提釩溫度及釩渣中TFe/SiO之比一定時,釩在渣和金屬相間的分配係數(V)/[V]隨釩渣鹼度的增加而增加。如當由酸性渣R≤1.0提高到R≥2.0時,在相同的碳氧化率情況下,釩的氧化率提高約30%。為獲得鹼性釩渣,通常在鐵水提釩過程中外加適量的CaO之類鹼性物,能使FeO-SiO系中氧化鐵的活度值aFeO大大提高,有利於釩的氧化並從鐵水中分離出來。但另一方面卻導致釩渣量增加,釩渣中VO含量降低,同時,CaO與釩會生成不溶性的釩酸鈣而降低水法冶金提釩過程中釩的回收率;或者需要增加酸浸工序而使生產過程複雜化。其次,CaO與PO會生成磷酸鈣進入釩渣中,會大大降低釩渣的質量。