概念
在鑄造工藝中,進料口將各分流道門末端熔體引入到個型腔的小尺寸通道;在大型化工機械中,如球磨機、混合機等,進料口為投料入口,是物料入口管道與機械腔體的狹小通口。
鑄鋼件進料口的鑄造工藝模擬及改進
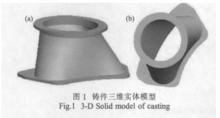
進料口的三維實體見圖1,根據該零件的結構特點,對該鑄件進行鑄造工藝分析可知:該零件屬於中型鑄鋼件,其結構相對比較複雜,壁厚分布比較均勻。
初始工藝方案
(1)分型面和澆注位置的設計
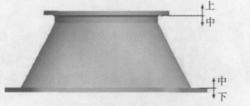
確定進料口鑄造方法為砂型鑄造,選用水玻璃自硬砂。根據澆 注位置的確定原則及鑄件的結構,所選用的澆注位置、分型面如圖2所示。根據零件尺寸輪廓大小,確定為三箱造型。
(2)澆注系統的設計
考慮到鑄件的尺寸的大小和生產批量,結合鑄件結構及設計原則,採用底注式半開放澆注系統,轉包澆注。澆注系統截面比為F內:F橫:F直=1.0:(0.8~0.9):(1.1~1.2),經計算F內為28.3cm2,F橫為25.5cm ,F直為34cm 。澆道從鑄件對稱的兩個方向同時引入。
(3)冒口的設計
運用模數法計算冒口。求得鑄件進料口體積V=36.4dm ,表面積S=3.02m ,鑄件模數Mc=V/S=1.2cm。查參考資料後確定,冒口的形狀如圖3,共有4個,在鑄件頂端對稱分布。
(4)冷鐵的設計
在鑄鋼件進料口的兩肋上與底面上放置與其尺寸接近的冷鐵,造成人為末端區,其厚度20mm,其形狀如圖4,放置位置如圖5。
鑄造工藝最佳化及模擬
(1)消失模鑄造工藝簡介
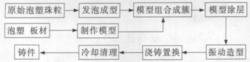
傳統的鑄造工藝鑄出的進料口鑄件產生的缺陷太多,不能滿足性能 要求。經過仔細分析和慎重選擇,為了方便起模並達到理想的效果,決定採用消失模鑄造工藝。工藝流程如圖6,結合進料口鑄件的特點,採用頂注式澆注系統。帶有澆注系統的鑄件實體圖如圖7,冒口是一個圓環柱,內圓的直徑為準500mm,外圓的直徑為準800mm,高為250mm。
(2)預發泡處理
用戊烷(C5H12)作為發泡劑來對泡沫塑膠的珠粒進行預發泡,戊烷的沸點36.07℃,凝固點-129.72℃,採用蒸汽式連續預發泡。內型採用鋁合金造型,外型採用鑄鋼,可以永久使用。
(3)內外型的設計
消失模鑄造鑄件的吃砂量為100mm,結合鑄件和澆注系統的尺寸,外型尺寸為1400mm×900mm×850mm(長×寬×高)。內型採用鋁合金,為了能取出內芯,將內芯分為如圖8所示的五部分。
(4)模型塗層和振動造型
為了提高EPS模型的強度、剛度及表面抗型砂沖刷能力,防止加砂過程中模型及負壓定型時模型的變形,確保鑄件的尺寸精度;在實型鑄造泡塑模型表面塗一層1.5mm厚度的專用塗料,連塗兩遍,在40~50℃下烘乾,形成鑄型內殼。將帶有抽氣室的砂箱放在振動台上,底部放入100mm厚度的底砂,其為無粘結劑、不含水的乾石英砂,振動緊實;在上面放置EPS模型組,並培砂固定;加入乾砂,同時施以x、y、z三個方向振動,振動時間50s,砂箱表面用塑膠薄膜密封,用真空泵將砂箱內抽成一定真空,靠大氣壓力與鑄型內壓力之差將砂粒“粘結”在一起,維持鑄型澆注過程不崩散,稱之為“負壓”定型。
(5)澆注置換
鑄件澆注時,在液體金屬的熱作用下,EPS模型發生熱解氣化,產生大量氣體,不斷通過塗層型砂,向外排放,在鑄型、模型及金屬間隙內形成一定氣壓,液體金屬不斷地占據EPS模型位置,向前推進,發生液體金屬與EPS模型的置換過程,置換的最終結果是形成鑄件。澆注操作過程採用慢-快-慢的連續澆注,防止澆注過程斷流,澆後鑄型真空維持5min後停泵,澆注溫度比砂型鑄造的溫度高40℃。
(6)凝固過程模擬分析
改進方案模擬結果如圖9所示。當凝固時間t=30s時,在型腔內金屬液的邊緣部分有一定厚度的鋼液已經凝固;t=40s時,壁厚相對較小或熱節較小的的部分已經完全凝固;t=60s時,加強筋已經完全凝固,底面開始凝固;t=80s時,液態金屬進一步凝固,底面已基本凝固;t=120s時,底面完全凝固,補縮通道開始凝固;t=180s時,薄壁部分進一步凝固,一些補縮通道已關閉;t=340s時,壁厚和熱節較大的部分仍然存在液體,其餘的部位已基本凝固,澆注系統進一步凝固,補縮通道關閉;t=3200s時,除冒口中心外,鑄件完全凝固。雖然該過程和初始方案相同,但效果更好。如圖10,相對於初始方案,鑄件的縮孔和縮松缺陷明顯減少,底面和頂面沒有缺陷;壁是非加工面,為非重要面,壁上的細微缺陷不影響使用性能,故最終決定採用此方案。
研究結論
(1)運用V-Cast模擬軟體,通過對鑄鋼件進料口原始工藝進行凝固過程模擬,準確預測了產生的縮孔、縮松缺陷,為設計合理的鑄造工藝提供了參考。
(2)藉助V-Cast軟體,採用消失模鑄造工藝進行澆注,在鑄件兩側設計了半開放式澆注系統,採用了頂注式澆注系統;在鑄件的頂面上放置了環形冒口,以對進料口壁進行補縮;設計了製造泡沫塑膠消失模的內型和外型,設計了消失模鑄造的工藝過程。最終模擬結果證明,消失模鑄造工藝能得到滿足使用要求的鑄件。
圓筒混合機進料口漏料及揚塵的防治
改造前的狀況
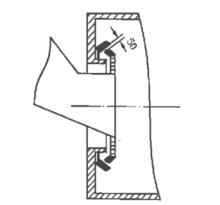
圓筒混合機進料口密封如圖11所示,採用的是正反喇叭口 互密封結構。正喇叭口通過M14螺栓固定在筒體上,可隨筒體一起轉動;反喇叭口焊固在進料漏斗上,為不可轉動部分。正反喇叭口之間留有50mm間隙,保證混合機正常運轉時,相對運轉的正反喇叭口兩部分不會發生摩擦、碰撞。這種密封結構存在的問題是:①因混合機筒體中心隨負荷變化及驅動輪胎磨損而發生變化,造成正反兩喇叭口不同心,其間隙很難達到一致,致使相對運轉的兩部分在某些部位產生滑動摩擦,最終導致正喇叭口邊緣部分被切斷。②正、反喇叭口上部受物料沖刷,磨損嚴重,使用壽命短。③大量粉塵從兩喇叭口之間的間隙泄漏,嚴重污染環境。
改進措施
(1)第一次改進
將原密封裝置全部拆除,採用了如圖12所示的內迷宮式密封。其進料漏斗末端及混合機進口部分尺寸如圖所注。採用厚10mm的A3鋼板割制一個1760mm的圓板,再在圓板中心割制一個1150×970mm的方孔,將其切割成對稱的兩塊後焊固在進料漏斗的出料口末端,並要求該圓板與筒體端面基本平行。然後將已加工好的內徑為1760mm、寬為150mm、厚4mm的圓筒切割成段,焊固在圓板的外側,並保持與筒體內側端面的間隙為50mm。內迷宮式密封大大降低了漏料量及揚塵,但也存在著筒體更換不便,更換輪胎及調整聯軸器時筒體可上升的距離受到限制,圓弧密封板和筒體止口之間間隙較大,密封效果不理想等問題。
(2)第二次改進
割除內迷宮式密封結構中的圓弧密封板,將進料漏斗出料口末端焊固的1760mm圓板的直徑縮至1654mm;在筒體止口部位均勻割制14mm圓孔16個。再用廢運輸膠帶割制一段長5250mm,寬230mm的密封膠皮,在密封膠皮上打孔後用M12螺栓固定在止口部位,製成如圖13所示的軟聯接密封。這種密封方式有效地減小了接觸間隙,1654mm圓板與膠皮之間的間隙僅為5mm,大大提高了密封效果,而且膠皮使用壽命長,更換方便。這一改進徹底解決了漏料問題,粉塵泄漏也大大減少,但仍有一定揚塵。
揚塵治理
為解決進料口部位的揚塵問題,採取了在該部位適量加水降塵的方案(混合、制粒所需水量的不足部分由流量計控制補充),但加水造成漏斗內壁粘料、堵料,影響料流穩定,導致生產波動。為此,我們又進行了兩次改進。
(1)改進之一
在混合機進料漏斗內壁落料點處安裝1個860mm×950mm吊掛振動板,其一端與漏斗壁鉸接,可繞鉸支座轉動。在漏斗外部的相應部位安裝兩台振動器,啟動振動器,吊掛振動板則隨之產生高頻微幅擺動,將粘結的物料振落,使料流通暢、穩定。改進後,使用效果不錯,但存在振動器易燒壞,振動板磨損嚴重,振動噪音大等問題,且增加了日修、定修工作量和維修成本。
(2)改進之二
去掉振動器和吊掛振動板,設計製作了一塊860mm×950mm的工業陶瓷襯板,將該襯板安裝在漏斗內壁落料點部位,漏斗其餘部位則貼上鑄石襯板,要求各襯板連線部位保持光滑、平整。由於陶瓷襯板和鑄石襯板具有不粘料,耐磨損、使用壽命長等特點,尤其是工業陶瓷襯板還具有一定的抗衝擊能力,而鑄石襯板價格低廉,很好地解決了粘、堵料問題,從而解決了混合機進料口部位的揚塵。