簡介
機器視覺檢測的特點是提高生產的柔性和自動化程度。在一些不適合於人工作業的危險工作環境或人工視覺難以滿足要求的場合,常用機器視覺來替代人工視覺;同時在大批量工業生產過程中,用人工視覺檢查產品質量效率低且精度不高,用機器視覺檢測方法可以大大提高生產效率和生產的自動化程度。而且機器視覺易於實現信息集成,是實現計算機集成製造的基礎技術。
典型結構
一個典型的機器視覺系統包括以下五大塊:
照明
照明是影響機器視覺系統輸入的重要因素,它直接影響輸入數據的質量和套用效果。由於沒有通用的機器視覺照明設備,所以針對每個特定的套用實例,要選擇相應的照明裝置,以達到最佳效果。光源可分為可見光和不可見光。常用的幾種可見光源是白幟燈、日光燈、水銀燈和鈉光燈。可見光的缺點是光能不能保持穩定。如何使光能在一定的程度上保持穩定,是實用化過程中急需要解決的問題。另一方面,環境光有可能影響圖像的質量,所以可採用加防護屏的方法來減少環境光的影響。照明系統按其照射方法可分為:背向照明、前向照明、結構光和頻閃光照明等。其中,背向照明是被測物放在光源和攝像機之間,它的優點是能獲得高對比度的圖像。前向照明是光源和攝像機位於被測物的同側,這種方式便於安裝。結構光照明是將光柵或線光源等投射到被測物上,根據它們產生的畸變,解調出被測物的三維信息。頻閃光照明是將高頻率的光脈衝照射到物體上,攝像機拍攝要求與光源同步。
鏡頭
FOV(Field of Vision)=所需解析度*亞象素*相機尺寸/PRTM(零件測量公差比)
鏡頭選擇應注意:
①焦距②目標高度 ③影像高度 ④放大倍數 ⑤影像至目標的距離 ⑥中心點 /節點⑦畸變
視覺檢測中如何確定鏡頭的焦距
為特定的套用場合選擇合適的工業鏡頭時必須考慮以下因素:
· 視野 - 被成像區域的大小。
· 工作距離 (WD) - 攝像機鏡頭與被觀察物體或區域之間的距離。
· CCD - 攝像機成像感測器裝置的尺寸。
· 這些因素必須採取一致的方式對待。如果在測量物體的寬度,則需要使用水平方向的 CCD 規格,等等。如果以英寸為單位進行測量,則以英尺進行計算,最後再轉換為毫米。
參考如下例子:有一台 1/3” C 型安裝的 CDD 攝像機(水平方向為 4.8 毫米)。物體到鏡頭前部的距離為 12”(305 毫米)。視野或物體的尺寸為2.5”(64 毫米)。換算係數為 1” = 25.4 毫米(經過圓整)。
FL = 4.8 毫米 x 305 毫米 / 64 毫米
FL = 1464 毫米 / 64 毫米
FL = 按 23 毫米鏡頭的要求
FL = 0.19” x 12” / 2.5”
FL = 2.28” / 2.5”
FL = 0.912” x 25.4 毫米/inch
FL = 按 23 毫米鏡頭的要求
註:勿將工作距離與物體到像的距離混淆。工作距離是從工業鏡頭前部到被觀察物體之間的距離。而物體到像的距離是 CCD 感測器到物體之間的距離。計算要求的工業鏡頭焦距時,必須使用工作距離
相機
按照不同標準可分為:標準解析度數字相機和模擬相機等。要根據不同的實際套用場合選不同的相機和高解析度相機:線掃描CCD和面陣CCD;單色相機和彩色相機。
圖像採集
圖像採集卡只是完整的機器視覺系統的一個部件,但是它扮演一個非常重要的角色。圖像採集卡直接決定了攝像頭的接口:黑白、彩色、模擬、數字等等。
比較典型的是PCI或AGP兼容的捕獲卡,可以將圖像迅速地傳送到計算機存儲器進行處理。有些採集卡有內置的多路開關。例如,可以連線8個不同的攝像機,然後告訴採集卡採用那一個相機抓拍到的信息。有些採集卡有內置的數字輸入以觸發採集卡進行捕捉,當採集卡抓拍圖像時數字輸出口就觸發閘門。
視覺處理器
視覺處理器集採集卡與處理器於一體。以往計算機速度較慢時,採用視覺處理器加快視覺處理任務。由於採集卡可以快速傳輸圖像到存儲器,而且計算機也快多了,所以視覺處理器用的較少了。
機器選型
在機器視覺系統中,獲得一張高質量的可處理的圖像是至關重要。系統之所以成功,首先要保證圖像質量好,特徵明顯,。一個機器視覺項目之所以失敗,大部分情況是由於圖像質量不好,特徵不明顯引起的。要保證好的圖像,必須要選擇一個合適的光源。
光源選型基本要素:
對比度:對比度對機器視覺來說非常重要。機器視覺套用的照明的最重要的任務就是使需要被觀察的特徵與需要被忽略的圖像特徵之間產生最大的對比度,從而易於特徵的區分。對比度定義為在特徵與其周圍的區域之間有足夠的灰度量區別。好的照明應該能夠保證需要檢測的特徵突出於其他背景。
亮度:當選擇兩種光源的時候,最佳的選擇是選擇更亮的那個。當光源不夠亮時,可能有三種不好的情況會出現。第一,相機的信噪比不夠;由於光源的亮度不夠,圖像的對比度必然不夠,在圖像上出現噪聲的可能性也隨即增大。其次,光源的亮度不夠,必然要加大光圈,從而減小了景深。另外,當光源的亮度不夠的時候,自然光等隨機光對系統的影響會最大。
魯棒性:另一個測試好光源的方法是看光源是否對部件的位置敏感度最小。當光源放置在攝像頭視野的不同區域或不同角度時,結果圖像應該不會隨之變化。方向性很強的光源,增大了對高亮區域的鏡面反射發生的可能性,這不利於後面的特徵提取。
好的光源需要能夠使你需要尋找的特徵非常明顯,除了是攝像頭能夠拍攝到部件外,好的光源應該能夠產生最大的對比度、亮度足夠且對部件的位置變化不敏感。光源選擇好了,剩下來的工作就容易多了。具體的光源選取方法還在於試驗的實踐經驗。
套用案例
在布匹的生產過程中,像布匹質量檢測這種有高度重複性和智慧型性的工作只能靠人工檢測來完成,在現代化流水線後面常常可看到很多的檢測工人來執行這道工序,給企業增加巨大的人工成本和管理成本的同時,卻仍然不能保證100 %的檢驗合格率(即“零缺陷”)。對布匹質量的檢測是重複性勞動,容易出錯且效率低。
流水線進行自動化的改造,使布匹生產流水線變成快速、實時、準確、高效的流水線。在流水線上,所有布匹的顏色、及數量都要進行自動確認(以下簡稱“布匹檢測”)。採用機器視覺的自動識別技術完成以前由人工來完成的工作。在大批量的布匹檢測中,用人工檢查產品質量效率低且精度不高,用機器視覺檢測方法可以大大提高生產效率和生產的自動化程度。
特徵提取辨識
一般布匹檢測(自動識別)先利用高清晰度、高速攝像鏡頭拍攝標準圖像,在此基礎上設定一定標準;然後拍攝被檢測的圖像,再將兩者進行對比。但是在布匹質量檢測工程中要複雜一些:
1. 圖像的內容不是單一的圖像,每塊被測區域存在的雜質的數量、大小、顏色、位置不一定一致。
2. 雜質的形狀難以事先確定。
3. 由於布匹快速運動對光線產生反射,圖像中可能會存在大量的噪聲。
4. 在流水線上,對布匹進行檢測,有實時性的要求。
由於上述原因,圖像識別處理時應採取相應的算法,提取雜質的特徵,進行模式識別,實現智慧型分析。
Color檢測
一般而言,從彩色CCD相機中獲取的圖像都是RGB圖像。也就是說每一個像素都由紅(R)綠(G)籃(B)三個成分組成,來表示RGB色彩空間中的一個點。問題在於這些色差不同於人眼的感覺。即使很小的噪聲也會改變顏色空間中的位置。所以無論我們人眼感覺有多么的近似,在顏色空間中也不盡相同。基於上述原因,我們需要將RGB像素轉換成為另一種顏色空間CIELAB。目的就是使我們人眼的感覺儘可能的與顏色空間中的色差相近。
Blob檢測
根據上面得到的處理圖像,根據需求,在純色背景下檢測雜質色斑,並且要計算出色斑的面積,以確定是否在檢測範圍之內。因此圖像處理軟體要具有分離目標,檢測目標,並且計算出其面積的功能。
Blob分析(Blob Analysis)是對圖像中相同像素的連通域進行分析,該連通域稱為Blob。經二值化(Binary Thresholding)處理後的圖像中色斑可認為是blob。Blob分析工具可以從背景中分離出目標,並可計算出目標的數量、位置、形狀、方向和大小,還可以提供相關斑點間的拓撲結構。在處理過程中不是採用單個的像素逐一分析,而是對圖形的行進行操作。圖像的每一行都用遊程長度編碼(RLE)來表示相鄰的目標範圍。這種算法與基於象素的算法相比,大大提高處理速度。
結果處理和控制
應用程式把返回的結果存入資料庫或用戶指定的位置,並根據結果控制機械部分做相應的運動。
根據識別的結果,存入資料庫進行信息管理。以後可以隨時對信息進行檢索查詢,管理者可以獲知某段時間內流水線的忙閒,為下一步的工作作出安排;可以獲知內布匹的質量情況等等。
套用現狀
在國外,機器視覺的套用普及主要體現在半導體及電子行業,其中大概40%-50%都集中在半導體行業。具體如PCB印刷電路:各類生產印刷電路板組裝技術、設備;單、雙面、多層線路板,復銅板及所需的材料及輔料;輔助設施以及耗材、油墨、藥水藥劑、配件;電子封裝技術與設備;絲網印刷設備及絲網周邊材料等。SMT表面貼裝:SMT工藝與設備、焊接設備、測試儀器、返修設備及各種輔助工具及配件、SMT材料、貼片劑、膠粘劑、焊劑、焊料及防氧化油、焊膏、清洗劑等;再流焊機、波峰焊機及自動化生產線設備。電子生產加工設備:電子元件製造設備、半導體及積體電路製造設備、元器件成型設備、電子工模具。機器視覺系統還在質量檢測的各個方面已經得到了廣泛的套用,並且其產品在套用中占據著舉足輕重的地位。除此之外,機器視覺還用於其他各個領域。
2000年來,零售商和消費者對可導致健康風險或增加零售商成本的不合格產品越來越沒有忍耐力。如果視覺檢測機制正確執行和管理,就可成為強大的工具用於:
-保護製造商、零售商和消費者的利益,不會出現貼錯標籤和無法識別過敏原標籤的包裝
-有助於保護品牌聲譽
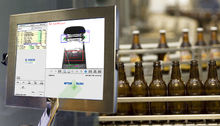
-遵守行業最佳實踐指南和零售商標準
研究顯示,65%的消費者在購買產品時會參考包裝。如果包裝貼錯標籤或標籤被損壞,隱藏潛在的有害成分,這會導致產品召回、罰款、甚至是法律訴訟。有調查表明食品行業中55%的召回都是由不正確的標籤所導致的,食品過敏原就是一個十分普遍的例子。
視覺檢測是計算機學科的一個重要分支,它綜合了光學、機械、電子、計算機軟硬體等方面的技術,涉及到計算機、圖像處理、模式識別、人工智慧、信號處理、光機電一體化等多個領域。自起步發展至今,已經有20多年的歷史,其功能以及套用範圍隨著工業自動化的發展逐漸完善和推廣,其中特別是目前的數字圖像感測器、CMOS和CCD攝像機、DSP、FPGA、ARM等嵌入式技術、圖像處理和模式識別等技術的快速發展,大大地推動了機器視覺的發展。簡而言之,機器視覺解決方案就是利用機器代替人眼來作各種測量和判斷。
發展歷史
1950年代,圖像處理成為機械工業的一個檢測項目,視覺檢測作為一項生產檢測機制誕生了;
1960-1970年代,飛彈和航天工業興起,人工檢測無法實現對飛彈等精密工業品的檢測,視覺檢測機開始出現;
1980年代,機械視覺檢測被套用於當時方興未艾的半導體工業;
1990年代,智慧型相機的出現使視覺檢測技術得到飛速發展,推動了製造業的視覺套用;
2000年,數位相機的發明和普及,使得老式的幀式抓取相機被淘汰,視覺檢測的成本大大降低;
2005年,梅特勒-托利多公司推出了世界上首台人機界面良好的視覺檢測機。從此,工人在生產線上操作視覺檢測設備就像操作電腦一樣簡單。
今天,歐盟、美國等國家已通過法規明確規定了產品製造商應該進行的視覺檢測項目及標準。國內外也有很多廠商設計出了高度智慧型的視覺檢測解決方案。越來越多的企業也開始在自己的生產線上安裝視覺檢測系統 。總之,視覺檢測技術和機制已經得到了廣泛的推廣。
工作原理
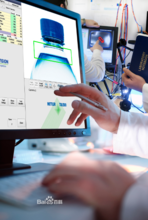
視覺檢測涉及拍攝物體的圖像,對其進行檢測並轉化為數據供系統處理和分析,確保
符合其製造商的質量標準。不符合質量標準的對象會被跟蹤和剔除。
掌握視覺檢測系統的工作原理對評估該系統對公司運作所做的貢獻十分重要。必須充分在設定視覺檢測系統時所涉及到的變數。正確設定這些變數,採用合適的容差,這對確保在動態的生產環境中有效而可靠地運行系統而言至關重要。如果一個變數調整或設計不正確,系統將連續出現錯誤剔除,證明使用不可靠。
結構組成
圖像部件
攝像機捕捉被檢測物體的電子圖像,然後將其傳送到處理器進行分析。電子圖像被轉換成數字,表示圖像最小的部分,即像素。圖像顯示的像素數量稱作解析度。圖像的解析度越高,包含的像素數量越多,進行檢測時,圖像的像素數量越多,檢測結果越準確。
攝像機
視覺檢測系統的攝像機有三個變數需要調整,以最佳化捕捉到的圖像。它們是光圈、對比度和快門速度。
照明部件
正確的照明對幫助創建有效檢測所需的對比度很關鍵。當對一件產品的正確係統設定進行評估時,設計師會花費相當多的時間用來確定檢測所需的最佳照明。照明解決方案的類型、幾何形狀、顏色和強度應當提供儘可能強的對比。
軟體工具
視覺檢測系統使用軟體處理圖像。軟體採用算法工具幫助分析圖像。視覺檢測解決方案使用此類工具組合來完成所需要的檢測。常用的包括,搜尋工具,邊界工具,特徵分析工具,過程工具,視覺列印工具等。
解決過程
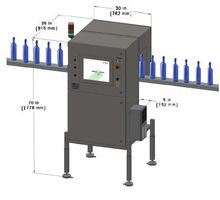
1、工件定位檢測器探測到物體已經運動至接近攝像系統的視野中心,向圖像采
集部分傳送觸發脈 沖,可分為連續觸發和外部觸發。
2、圖像採集部分按照事先設定的程式和延時,分別向攝像機和照明系統發出啟動脈衝。
3、攝像機停止目前的掃描,重新開始新的一幀掃描,或者攝像機在啟動脈衝來到之前處於等待狀態,啟動脈衝到來後啟動一幀掃描。
4、攝像機開始新的一幀掃描之前打開曝光機構,曝光時間可以事先設定。
5、另一個啟動脈衝打開燈光照明,燈光的開啟時間應該與攝像機的曝光時間匹配。
6、攝像機曝光後,正式開始一幀圖像的掃描和輸出。
7、圖像採集部分接收模擬視頻信號通過A/D將其數位化,或者是直接接收攝像機數位化後的數字視頻數據。
8、圖像採集部分將數字圖像存放在處理器或計算機的記憶體中。
9、處理器對圖像進行處理、分析、識別,獲得測量結果或邏輯控制值(合格或不合格)。
10、處理結果控制流水線的動作、進行定位、糾正運動的誤差等。
11、通過Excel等方式列印缺陷輸出結果(生產批號、缺陷位置、坐標、面積、類別、產生時間等信息)
從上述的工作流程可以看出,機器視覺解決方案是一種比較複雜的系統。因為大多數系統監控對象都是運動物體,系統與運動物體的匹配和協調動作尤為重要,所以給系統各部分的動作時間和處理速度帶來了嚴格的要求。在某些套用領域,例如機器人、飛行物體導制等,對整個系統或者系統的一部分的重量、體積和功耗都會有嚴格的要求。
視覺檢測的內容
所有自動生產線的目標都是零剔除。鑒於當今的高速技術和潛在的人為錯誤,這個目標很難實現。視覺檢測可以識別的典型缺陷包括:
標籤缺陷
封口和蓋頂缺陷
產品與包裝完整性缺陷
列印缺陷
容器缺陷
一個完善的視覺檢測機制應該包括以下檢測項目:
檢測項目 | 檢測內容描述 |
全瓶檢測 | 合適的填充量;蓋存在與否、高度、顏色、是否歪斜;標籤 存在與否、位置以及識別。 |
裝箱內部檢測 | 產品存在與否、放置、方向、計數和蓋的正確性。 |
裝箱外部檢測 | 箱子裝飾、ID和封蓋位置;列印產品代碼和日期/批號。 |
正確的蓋位置檢測 | 蓋檢測:存在與否、高度、傾斜度、顏色、安全帶完整性。 |
產品ID驗證 | 確保任何產品的 ID 代碼存在、可讀、正確。 |
瓶頸測量 (邊到邊、高度和螺紋寬度) | 檢測玻璃瓶頸的寬度(E–邊到邊)、高度(H)和螺紋寬度(T)。 |
平面度檢測 | 檢查容器頂部是否在微調過程中因不均勻切割而導致出現頭髮、絲線或波浪狀平面。 |
污染物檢測 | 檢測容器側壁上的任何缺陷,包括在注塑成型過程中堆積產生的灰塵、傷痕、污點以及內置或表面顆粒物質。 |
破碎的頂部檢測 | 驗證玻璃容器頂部沒有空洞、晶片、丟失的玻璃和碎片。還可確定軟木的存在。 |
其他檢測 | 條碼/二維碼驗證、標籤控制號(LCN)驗證、傾斜標籤檢測、 折角標籤檢測、標籤存在檢查等 |
視覺檢測的優勢
1、非接觸測量,對於觀測者與被觀測者都不會產生任何損傷,從而提高系統的可靠性。
2、具有較寬的光譜回響範圍,例如使用人眼看不見的紅外測量,擴展了人眼的視覺範圍。
3、長時間穩定工作,人類難以長時間對同一對象進行觀察,而機器視覺則可以長時間地作測量、分析和識別任務。
4、利用了機器視覺解決方案,可以節省大量勞動力資源,為公司帶來可觀利益。柯能自動化科技有限公司(KEN),是一家專注於機器視覺、工業自動化檢測、運動控制與視覺一體化領域,全力打造高端視覺設備。產品套用 柯能自動化提供的視覺設備,廣泛運用於多個行業: 電子行業:半導體元件表面缺陷特徵監測、字元印刷殘缺檢測、晶片引腳封裝完整檢測、元件破損檢測、端子引腳尺寸檢測、編帶機元件極性識別、鍵盤字元檢測等; 製造行業:零件外形檢測、表面劃痕檢測、漏加工檢測、表面毛刺檢測等; 印刷行業:印刷質量檢測、印刷字元檢測、條碼識別、色差檢測等; 汽車電子:面板印刷質量檢測、字元檢測、SPI檢測系統、色差檢測等; 醫療行業:藥瓶封裝缺陷監測、藥品封裝缺漏檢測、膠囊封裝質量檢測等; 食品行業: 外觀封裝檢測、食品封裝缺漏檢測、外觀和內部質量檢測、顏色質量檢測、食品包裝定位等; 五金行業:微小金屬正反面判別、零件表面檢測、零件尺寸檢測等
視覺檢測的套用
1. 視覺檢測在印刷行業的套用
利用線上/離線的視覺系統發現印刷過程中的質量問題,如堆墨、飛墨、缺印/淺印、套印不準、顏色偏差等,同時線上設備可將顏色偏差和墨量多少的檢測結果反饋給PLC,控制印刷設備的供墨量,對供墨量進行線上調節,提高印刷質量和效率。
2. 視覺檢測在PCB板檢測中的套用
利用視覺系統對PCB裸板進行檢測,檢測板上的導線和元件的位置和間距錯誤、線路和元件的尺寸錯誤、元件形狀錯誤、線路的通段、板上污損等。
3. 視覺檢測在零件檢測中套用
機器視覺檢測可以輕鬆應對金屬零件生產的質量控制,如硬幣、汽車零部件、連線器等。通過圖像處理的方法,發現金屬零件表面的劃傷、殘缺、變色、黏膜等缺陷,並指導機械傳動系統將殘缺品剔除,大大提高了生產效率。同時對缺陷類型的統計分析能夠指導生產參數的調整,提高產品質量。
4、視覺檢測在汽車安全中的套用
對於大多數人來說,還是在靠主觀思想和意識判斷開車過程中的突發事件,隨著安全事故頻頻多發,安全理念已備受人們關注,數位化被用作汽車安全監測系統成為主流,也備受業內熱議。
具不完全統計,50%的交通安全事故起源駕駛員意識不清醒從而釀成車禍。構想有沒有一種能基於物聯網的檢測系統,即:檢測駕駛員是否意識清醒,並提出警告,提前阻止安全事故發生呢?答案是肯定的,目前業內已經有採用物聯網數位化技術實現駕駛員精神狀況的檢測系統,它基於車聯網套用的,以適應行駛安全檢測的新需求。這種數位化的系統的套用融合姿態信息的多姿態人臉檢測方法,基於生物特徵的頭部姿態估計方法,融合駕駛員自身多種生物特徵的疲勞駕駛模型,將極大提高疲勞駕駛檢測的準確性和可靠性。
這類數位化系統的工作原理就是通過視覺感測器對人的眼瞼眼球的幾何特徵和動作特徵、眼睛的凝視角度及其動態變化、頭部位置和方向的變化等進行實時檢測和測量,建立駕駛人眼部頭部特徵與疲勞狀態的關係模型,研究疲勞狀態的多參量綜合描述方法;同時研究多元信息的快速融合方法,提高疲勞檢測的可靠性和準確性,從而研製穩定可靠的駕駛員疲勞監測系統。它檢測的方法很多,比如:人臉快速檢測方法、疲勞程度檢測方法、疲勞駕駛問題檢測等等。
目前,國內汽車安全數位化服務商很多,但開發基於物聯網數位化的視覺疲勞檢測系統,武漢華信數據系統有限公司首次填補國內基於車聯網的駕駛員疲勞檢測系統的空白,並與多家知名汽車製造商進行合作。汽車行業的安全保障始終是一個不變的話題,只有想顧客之所想,順應汽車行業發展的,才是汽車行業未來發展的宏源理念!
套用案例
歐萊雅實現產品包裝過程標籤零缺陷
巴黎歐萊雅的行銷和包裝專家的目標是使進入市場的歐萊雅包裝達到零缺陷目標。了解歐萊雅是如何利用我們的標籤視覺成像檢測解決方案實現這一目標的。
遺漏、錯誤、受損和外觀不美觀的標籤不僅會影響產品的展示形象,而且會對品牌持有者在市場中的形象造成長期損害。歐萊雅行銷與包裝專家的目標是使進入市場的歐萊雅包裝實現零缺陷目標。公司試圖通過利用多種灰度檢測解決方案實現這一目標,但是結果卻不盡如人意,尤其是對於諸如其 Vive Pro® 系列優質洗髮精和護髮素之類的產品。
這些產品採用具有“無標籤效果”的透明標籤材料進行貼標。但這卻使得灰度系統難以準確尋找到標籤的邊緣,從而無法檢測其是否位置不當和起皺,結果導致系統出現誤允許缺陷瓶子流入市場的結果。
於是公司向梅特勒-托利多 CI-Vision 求助,幫助尋找這一問題的解決方案。CI-Vision 推薦使用完美的雙攝像機彩色解決方案,這套解決方案使用彩色攝像機及其隨配軟體更清晰地識別與檢測透明標籤,以及檢查每隻瓶子上列印的日期/批號。此外,一台條形碼閱讀器可確認每個包裝上的代碼,這樣可無需使用附加攝像機。歐萊雅包裝生產線經理要求歐萊雅市場部在設計包裝時,將各個品牌的標籤與代碼放置在一致的位置,從而幫助簡化了檢測工作。
CI-Vision 解決方案還包括培訓功能: 操作人員只需將樣品包放在攝像機前方,然後激活“培訓”功能,即可將用於檢測新包裝的系統準備好。這樣,當歐萊雅多產品高速生產線進行轉換時,無需停機即可完成照相機移動或系統調節。
針對這一項目,梅特勒-托利多CI-Vision 提供了一種完整的視覺成像檢測解決方案,其中包括設備安裝和調試、培訓、檔案記錄與維護支持。
歐萊雅通過採用這種新型檢測解決方案,不僅可實現其質量目標,而且可通過大幅縮短轉換時間提升生產線工作效率。公司現已將視覺檢測從最初的Vive Pro 生產線擴大套用至不同生產廠的其他許多生產線中。