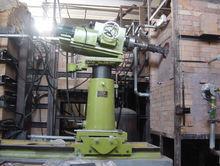
1902年,沃爾克(Voelker)獲準了一個基本專利,其內容是利用電流通過玻璃配合料產生的熱來熔化玻璃。隨著熔窯設計和電極的不斷改進和發展,這種電熔方法得到廣泛套用。1920~1925年,挪威的雷德(Raeder)使用石墨電極,成功地實現了玻璃的全電熔。1925年,瑞典的科尼利磯斯(Corneljus)用這種電熔窯生產琥珀色玻璃和綠色玻璃。該電熔窯採用薄層加料法,配合料浮在玻璃液表面。在電熔窯投產時,配以臨時性的爐蓋,當玻璃液位蓋過電極,便撤去爐蓋。所用的電極是大鐵塊,由於鐵電極使玻璃著色,所以這種熔窯只能用於熔化有色玻璃,效果頗好。當時可達到1.40kWh/kg玻璃,所以這種作業在電能價格低的地區是可行的。這種電熔窯有些一直運行到最近幾年。弗格森(Ferguson)在1932~1940年這一時期,採用“T”形電熔窯積極從事電熔的研究。
第二次世界大戰期間,瑞士的波來耳 (Borel)在電熔方面做了大量的研究發展工作,旨在解決燃料短缺的問題。波來耳的工作獲得了成功,並由法國·聖哥本 (St.Gobain)公司加以推廣,該公司還對電助熔做了實際的工作。
二戰以後人們開始對鉬電極感興趣,佩恩伯瑟(Penberthy)設計的電極系統使用鉬棒,1952年玻璃工業開始廣泛用於電助熔和全電熔。另一種是英國的格耳(Gell)和漢恩(Hann)於1956年提出的板狀鉬電極。
近20年來,玻璃電熔獲得迅速推廣。美國的瓶罐玻璃熔窯大約一半配備有電助熔,並且仍在不斷增大,從早期的300kW增大到目前的800~1500kW。發展趨勢仍未停止,現已有了超級電助熔。
目前全世界至少有100座全電熔窯,規模從4t/d至120t/d。每年都要增加若干座,其規模在電助熔和全電熔這兩個方面都在擴展。
近20年來,一種新概念即“混合熔化”,已日益受到重視。這種概念是:先在熔融的配合料內部通電加熱生產大約一半產量的玻璃,再在配合料上方用燃料加熱生產另一半產量的玻璃。其目的是要降低每噸玻璃所需熱量的總成本,與此同時仍保持如電熔窯玻璃那樣的質量。
另一項主要的新發展是用電熔窯熔化鉛晶質玻璃,供機器和手工生產高級餐具使用。大約在1964年棒狀氧化錫電極投入工業套用,而且為這種電極發明了性能良好的電接觸系統,為鉛玻璃電熔建立了良好的基礎。
近20年來的第三項發展,是推廣了電加熱料道。
第四項新發展是採用了“微型電熔窯”,用來生產優質玻璃,其熔化量可低到10kg/h。
近20年來的第五項發展,是日益重視對環境污染的控制。從這方面來講,電熔工藝具有相當重要的意義。
電熔方法有許多突出的優點,熱效率可以高達80%~85%,節省能源,沒有污染,消除公害,改善勞動條件。熔制出的玻璃液成分均勻,產品質量高。生產過程便於實現自動化操作。因此,在國外玻璃電熔得到迅速的推廣。
已開發國家,玻璃電熔化已廣泛套用於光學玻璃、硼矽酸鹽玻璃、鉛玻璃、氟化物玻璃、瓶罐玻璃以及纖維玻璃的生產,其工藝已趨成熟。
據魯塞爾·布艾曼(Russel Burman)1979年估計,世界上將近半數的玻璃熔窯都將採用電熔技術。
上個世紀60年代初期,我國玻璃纖維行業從研究池窯拉絲和代鉑爐開始研究電熔工藝,至今已有幾十年的歷程。目前在製造平板玻璃、特種儀器玻璃、器皿玻璃的火焰池窯中採用電助熔,耗電量不多,但對提高產品質量,增加產量,改善勞動條件諸方面都有良好的效果,發展前途廣闊。預計在今後幾十年內許多火焰池窯將廣泛採用電助熔。隨著我國電力工業的發展,全電熔工藝的套用也會逐年增加。
玻璃電熔與傳統的火焰加熱熔融爐相比有著很大的優勢。由於利用玻璃液直接作為焦耳熱效應的導電體,所以玻璃電熔化的熱效率遠高於火焰熔融爐。日出料量60t以上的玻璃電熔窯的熱效率大於80%。另外,電熔窯的爐型結構簡單,占地面積小,控制平穩且易操作,並減少了原料中某些昂貴氧化物的飛散與揮發,降低噪聲和改善環境污染,穩定熔化工藝和提高產品質量等,這些都是燃料爐難以比擬的。
我國擁有豐富的水力資源,加上新建的核電站,為玻璃電熔技術的推廣套用提供了能源基礎。因此玻璃電熔是今後的發展方向之一。
工作原理:
玻璃高溫導電,產生焦耳熱進行玻璃熔化
電極進行電加熱,電極:有錫電極、鉬電極、石墨電極;不同的玻璃品質及種類選用不同的電極
操作所需知識:
1、玻璃工藝
2、基本的電學知識
注意事項:
1、必須配備發電機
2、影響窯爐壽命的因素:窯爐的砌築材料、電極、粉料成分、操作人員的操作