概念
液體中子吸收體,具有熱中子吸收截面大(或共振吸收大),抗輻照能力強,平穩的燃耗,良好的高溫熱穩定性,與吸收體的包殼相容性好、使用壽命長以及適當的強度和較低的成本等基本要求。
當前國內乏燃料貯存格架已實現自主化設計,但關鍵的中子吸收材料仍然主要依靠進口,大大制約了乏燃料貯存格架的國產化進程。 因此,加快乏燃料貯存用中子吸收材料的研發和生產工作已刻不容緩。
鋁基碳化硼液體中子吸收材料製備
BC 含量以及在基體中是否彌散分布是鋁基BC 複合材料能否獲得優良中子吸收性能的關鍵。當前鋁基 BC 中子吸收材料製備方法主要有粉末冶金法、熔體浸滲法和液態成型法。液態成型法是近年來提出的一種製備鋁基中子吸收材料的新方法。該方法是將碳化硼(BC)顆粒注入到熔融鋁液中並通過真空機械攪拌混合均勻,然後進行澆鑄,再進行擠壓或軋制獲得鋁基 BC複合材料。與傳統的粉末冶金法相比,液態成型法具有生產效率高、工藝流程簡單和適合大規模生產等特點, 被認為是最具前景的生產方法之一。
國外研究概況
當前美國採用粉末冶金法生產的高密度Metamic 材料已商業套用。 BC 質量分數為 31%的 Metamic 材料已被美國核管會批准用於乏燃料濕法貯存設備,在 AP1000 核電廠乏燃料水池的設計中也採用這種材料作為中子吸收材料。
在一般的工藝條件下, BC 與鋁合金基體的潤濕性較差,澆注過程中兩相容易分離,形成的顆粒相易發生團聚。隨著 BC 含量的增加,特別是當 BC 含量達到 30%以上時,如何選擇工藝顯得尤為關鍵。伊朗德黑蘭大學的 H.R. Lashgari 等 通過液態成型法製備出 BC 含量 10 wt%的鋁基複合材料,加拿大 ALCAN 公司成功製備出 BC含量為 16 vol%和 25 vol%的複合板材,並對其微觀結構和力學性能進行了研究。一般來說,商用核電廠乏燃料貯存格架用中子吸收材料中 BC含量需要達到 30 wt%以上。截至當前,採用液態成型法還未進一步製備出 BC 含量更高的鋁基BC 複合材料。
板材製備工藝研究
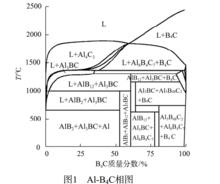
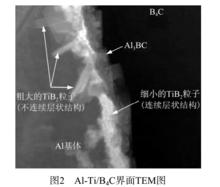
液態成型法製備鋁基 BC 複合材料的關鍵技術:粉體預處理、熔體改性、攪拌分散以及變形控制等。高含量的鋁基 BC 複合材料的製備尤其要關注熔體改性和攪拌分散 2 個環節。液態成型法製備鋁基 BC 時,如不對熔體進行處理,將導致 BC 顆粒與鋁熔體直接接觸發生界面反應(圖 1); 生成的 AlBC 和 AlB將對材料的力學性能和後續加工性能造成不利影響。同時,在攪拌過程中發生的界面反應會導致熔體中顆粒體積分數急劇升高,使熔體粘度增加流動性變差,對後期的攪拌分散和鑄造成型產生不利影響。為阻止界面反應,採用含鈦的鋁熔體, BC顆粒進入熔體後,將與 Al 和 Ti 兩種元素同時發生作用,可在 BC 表面生成保護層,阻止界面反應。從圖 2 可看出,第 1 層是以 AlBC 為主要成分的細晶層,第 2 層是以 TiB為主要成分的細晶層。 TiB細晶層的結構緻密,可有效地阻擋鋁液對 BC 顆粒的侵蝕。隨著BC顆粒的加入, BC顆粒易在鋁熔體中發生團聚,特別是隨著BC質量分數超過25%後,團聚現象更加突出。基於此,在最佳化攪拌系統結構的同時,綜合研究了攪拌溫度、攪拌時間、攪拌速率、葉片角度以及真空度等因素的影響,確定了適合的攪拌分散工藝。含有高質量分數陶瓷相的複合材料坯料難以進行冷/熱軋制和擠壓變形。這是因為此類複合材料中增強相強度高,而且在熔鑄過程中往往已經耗盡了位錯線的滑移和攀移能力,需加熱至較高溫度甚至再結晶處理才能進行軋制變形;而在高質量分數的材料中進行變形甚至可能會使變形抗力高於界面剪下強度,導致複合材料界面全部撕裂,巨觀表現為軋制雙面開片或者擠壓皴裂紋。為解決該複合材料軋制過程中存在的問題,首先套用 Gleeble 模擬試驗得到了最最佳化的加工區域, 通過系統研究單道次壓下量對成型的影響,選定合適的軋制工藝,製備出板材。