簡介
在現代製造業的發展進程中,模具的地位及其重要性日益受到人們的重視。因此研究汽車零配件的模具設計具有重要的現實意義,以下內容將以汽車後視鏡殼體模具為例,結合Solidworks平台上的3DQuickMold模具設計模組。並通過對汽車後視鏡殼體模具進行,工藝分析、結構分析、抽芯機構設計、前模和後模的設計,來介紹汽車後視鏡殼體注射模具的設計過程及工作過程。
工藝分析
圖1為汽車後視鏡殼體,為了美觀,殼體外表面為流線型曲面,造型複雜,其他各面多由曲面構成,中間還有兩個用於安裝的空心圓柱孔和多根加強筋。
注塑件的壁厚要求均勻。不均勻的壁厚會導致塑膠件產生內應力、翹曲、縮凹等各種缺陷。若壁厚過小,成型時流動阻力大,複雜製品就難以充滿型腔;若壁厚過大,不但會造成用料過多增加成本,還會增加塑件成型的冷卻時間。使用"工具/厚度分析"命令,可對塑膠件進行厚度檢測。
為了順利地使塑件從汽車後視鏡殼體模具型腔中取出或從塑件中抽出型芯,必須考慮內外壁有足夠的拔模斜度。使用"視圖/顯示/拔模分析"命令,設定拔模條件。
塑件材料選用具有良好綜合性能的工程塑膠ABS,它有較好的加工和成型性能,低蠕變性能和優異的尺寸穩定性,還有高抗衝擊強度和良好的外觀特性,適當提高汽車後視鏡殼體模具溫度可提高塑件光潔度。材料密度為1.02-1.05 g/cm3(注射級密度取1.05 g/cm3),理論計算收縮率為0.5%,溢料值為0.03 mm。
結構分析
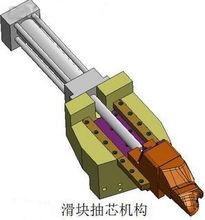
塑件的總體尺寸為中型大小的尺寸,尺寸精度不高,為中等批量生產。為了降低成型費用,本設計採用一模一腔。根據零件的結構分析,分型面選在最大輪廓處,上部用整體式前模型腔,下部用整體式後模,再嵌人幾個小型芯。本塑件的各面均為曲面,分型面設計在塑膠件的最大輪廓處。此塑膠件側向部位有一個大的開口,需要做滑塊抽芯機構,另外後模部分的2個加強筋處有倒扣,需要做成斜頂抽芯機構,綜合分析塑件的特點,汽車後視鏡殼體模具設計的設計的關鍵在於抽芯機構的設計。
抽芯機構
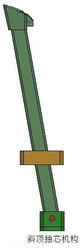
側向分型和抽芯機構是注射模設計中的一個重要組成部分,汽車後視鏡殼體模具的斜頂抽芯和滑塊抽芯如下圖2和圖3所示。
前模和後模
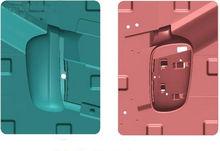
在注射成型過程中,汽車後視鏡殼體模具的型腔將受到高壓的作用,因此汽車後視鏡殼體模具型腔應該具有足夠的強度和剛度。強度不足將導致塑性變形,甚至開裂;剛度不足將導致彈性變形,導致型腔向外膨脹,產生溢料間隙。由於汽車後視鏡殼體模具型腔尺寸較大,型腔在發生大的彈性變形前,其內應力往往超過許用應力,因此應對型腔強度進行校核。由於該塑件屬於中等批量生產,因此為了便於加工,降低汽車後視鏡殼體模具成本,動模和定模材料選用國產718鋼,本設計在經過校核後,前模和後模採用整體式結構,如圖4。
工作過程
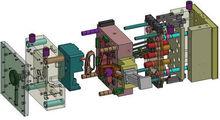
圖5為汽車後視鏡殼體模具總裝圖,汽車後視鏡殼體模具閉合後,注塑機開始向型腔內注人ABS,然後經過一段時間的保壓成型後,後模隨注塑機開始與前模分開,待前模開啟到終點位置時,在拉料桿的作用和型芯包緊力的作用下,塑件和流動中的凝料留在動模上,此時抽芯機構開始在液壓油缸的作用下帶動側滑塊完成側向抽芯,在頂出機構的作用下,塑件從動模上分離開來,在復位桿和復位彈簧的作用下,頂桿回復到汽車後視鏡殼體模具閉合時所在的位置,最後汽車後視鏡殼體模具閉合,至此,汽車後視鏡殼體模具完成了一個工作循環。