宇航石墨簡介
宇航石墨(spacenavigationgraphite)是指用於製造飛彈和太空飛行器部件的特種石墨材料。氣動熱環境是最能體現航天工程特徵的特殊工作環境之一,無論火箭發動機產生的高溫高速燃氣流場,或是飛彈彈頭加熱場,都具有高溫、高壓、高熱的特徵,處於流場區的工程結構材料必須具有有效的防熱措施。其中選用最佳的防熱材料就是不可缺少的技術物質基礎。
宇航石墨性能
石墨之所以能作為各類太空飛行器的防熱材料,主要原因是因為它具有很多優良性能。它密度小,常壓下不熔化,3700℃升華,強度隨溫度的升高而增加,直至2500℃。它具有較高的化學穩定性,良好的抗燒蝕性能和抗沖刷能力以及優越的抗熱衝擊能力。因而在飛彈和太空飛行器上即可用做耐高溫的承力構件。如液體火箭發動機的燃氣舵和固體火箭發動機的噴管喉襯,又可作為高性能的防熱材料,如飛彈端頭體等。此外,石墨材料資源豐富,能夠進行大規模連續化生產。造價低廉,用做先進的防熱材料,在造價上就具有很強的競爭能力。因此.各國都對石墨材料相當重視,相繼研製出石墨防熱材料新品種。
石墨材料的主要缺點是它的脆性,高溫下抗熱應力的能力較低.因而如何提高其斷裂韌性.已成為石墨材料研製工作的重點。一種稱之為高應變石墨材料,就顯著區別於一般石墨製品。
宇航石墨分類
宇航石墨分類和製備工藝按成型工藝來分類,宇航石墨可分如下幾類。
擠壓類石墨
擠壓類石墨工藝流程如下:油焦經預碎、煅燒、粉碎和篩分後與作為黏結劑的煤瀝青按一定配比經混捏製成糊狀料,在擠壓機上擠壓成生坯經多次焙燒浸漬,最後經過石墨化製成石墨製品。擠壓石墨的品種及性能見表1。
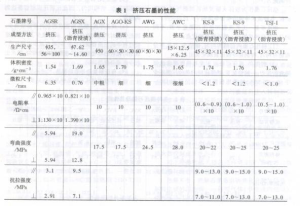
擠壓石墨除體積密度小、線膨脹係數小、彈性模小外,還具有良好的耐化學腐蝕性。抗燒蝕性和抗高。沖刷能力。
(1)模壓石墨內部結構均勻,缺陷少、氣孔率分燒過程中的扭曲和破裂現象,同時也減少內部氣孔。布相對均勻,特別是冷模壓表現更突出。
(2)密度高,模壓可根據密度與強度要求選擇較少形成分層等缺陷。適宜的壓力,般情況下,熱模壓時的單位壓強不少於60~70SPa,冷模壓所需的單位壓強為150~250MPa。隨著單位壓力的增加,毛坯的密度也會增量高。
(3)強度,在保證足夠的單位樂得下,由於材料擠壓石墨作為液體火箭發動機的燃氣舵、熱防內部缺陷少,結構均勻。因此比擠壓成型容易達到護板,各種戰術飛彈的噴管等得到了廣泛的套用。高強度。模壓石墨工藝流程和擠壓石墨差不多,不同
(4)成品率高,模壓所要求的糊料含黏結劑少,的只是擠壓換成模壓。模壓製品的優點:因此焙燒時產品收縮也較小。從而減少了產品在焙成型時顆粒的移動距離小,速度也比較均勻.
(5)可壓制複雜外形的製品,尺寸不受限制。世界宇航用模壓石墨品種及性能見表2。
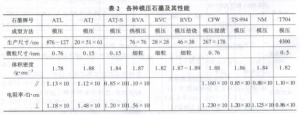
模壓石墨
模壓石墨,由於具有突出的抗燒蝕性能,抗沖刷易獲得較厚的滲矽層,滲矽層與基體結合牢固,滲矽能力和高溫強度。因此它是滿足再入鼻錐所要求的層緻密,其缺點是,滲矽層表面粗糙,由於有游離矽低燒蝕、外形對稱和穩定的有希望的材料。目前模會降低SiC的耐火度,有時滲矽層容易產生裂紋。壓石墨已用做戰略飛彈彈頭的高性能端頭,其使用氣滲是以液體——氧體的滲矽料注入特製的裝性能優於樹脂基防熱材料。同時它還是固體火箭發有被滲矽件的高溫容器中而獲得滲矽效果的。氣滲動機最理想的噴管材料之一。要選擇合理的工藝參數(溫度、壓力)。一般氣滲層滲矽石墨用金屬矽填充石墨內部的孔隙並且面較光滑、均勻緻密,但結合不牢,易發生脫落。使兩者發生化合而成為一個整體。石墨滲矽的工藝浸漬滲矽是將石墨件放人容器中,先抽真空,在方法很多,通常根據產品的特點和工藝設備的具體真空下吸入浸漬液,加壓浸漬,而後乾燥,生成SiO2,情況來選擇。按習慣,常把滲矽料的物態作為滲矽在熱處理過程中(2000℃左右)生成碳化矽。
一般浸工藝方法的區別,有固滲、氣滲、浸漬等方法。所謂漬次數控制在3次左右。固滲就是以固體的滲矽料(SiO2+C+SiC)埋著被滲對於飛彈和太空飛行器的熱環境來說,滲矽可以提的石墨件置於爐內加熱而獲得滲矽效果。一般低溫高石墨材料(噴管、燃氣舵等)的抗氧化和沖刷性能。下生成辟SiC,如果需要a-SiC需加熱到2100℃以熱解石墨熱解石墨是由碳氫化合物氣體熱分上。解而生成的固態碳。
一般用氣體(甲烷或丙烷等),固滲的優點是:操作簡單,滲矽層增長速度大,使氣流通過基體物質(石墨),在加熱條件下,使氣體熱解,放出氫氣,而碳在基體表面上沉積。這種急流氣體使碳原子按一定方向緊貼在基體表面上,構成均勻緊密的石墨晶體。
熱解石墨
熱解石墨的結構特徵決定了它除具備普通石墨的耐高溫、密度小、強度隨溫度升高及良好的機械加工性等優點之外,
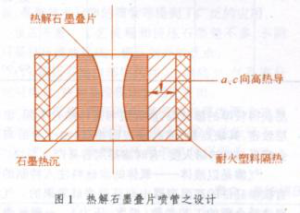
在宇航方面,利用熱解石墨a、c向上的各向異性,耐高溫、耐腐蝕及高的比強度等優點,做飛彈、飛船的再人頭錐和防熱罩。固體火箭發動機噴管喉襯等部件。美國通用電氣公司、高溫材料公司等設計出的疊片或墊圈結構的喉襯(圖1)。其特點:避開了熱解石墨塗層喉襯的殘餘應力問題,這樣的結構設計利用了熱解石墨a向高的導熱能力把喉部所產生的熱迅速導出,使喉襯處於較低溫度,從而提高了抗沖蝕能力。
熱壓石墨
所謂熱壓石墨就是用粉末冶金方法製得的高密高強石墨。又叫再結晶石墨(ZTA)。一般成型工藝可分兩種,一種是將塊石墨裝入石墨模具內,放在熱壓機上,經高壓處理而成。另一種是採用油焦粉或中間相小球體裝入石墨模具內,將模具放在熱壓機上,經高溫高壓而成。特別是中間相小球體,兼有固相和液相兩種成分,亦即具有自燒結性,因此用它作原料,無需用黏結劑,可直接壓制。一般成型溫度達到3000℃左右。
因炭質中間相小球體本身為超細粉,故可直接用作壓粉,而且不需要黏結劑,可以省去傳統工藝中破碎、磨粉、混合、軋輥、磨壓粉等備料工序,生產周期大為縮短,生產成本亦大幅度降低。熱壓石墨的特點是高密高強,其密度可達2左右,具有優良的抗燒蝕性能和抗沖蝕能力,是火箭飛彈噴管與彈頭的重要候選材料。均衡壓制石墨該石墨是採用超短炭纖維(2~250μm)與瀝青或樹脂均勻混合,進行澆鑄成型,在1000℃下炭化,然後將其裝入鋼製包套內,灌滿瀝青,把包套放進熱靜壓機內,在34×103MPa壓力下,升溫至1000~1500℃,使其密度達到規定要求,進行石墨化處理,纖維含量從25.5%變至52.5%。該材料特點由於纖維的高度無序排列.各向同性較好,密度高,具有低的燒蝕性能和優良的抗沖蝕能力。
宇航石墨特性
宇航石墨具有抗燒蝕性能和抗熱震能力。抗燒蝕性能石墨材料所含的惟一元素是碳,它的燒蝕過程與很多因素有關,大體上可分為熱化學燒蝕和機械剝蝕兩類。所謂熱化學燒蝕,就是炭材在熱環境下發生氧化和升華兩種化學耗炭過程,而機械剝蝕是指在嚴重的氣動加熱情況下,由於氣動剪力、熱應力等機械力的作用而發生物理破壞。在較高的駐點壓力時。機械剝蝕最為嚴重。顆粒剝蝕是石墨機械剝蝕的典型形式,由於兩種炭(填料與黏結劑)的密度不同,使燒蝕過程不同步,在氣動力和剪力作用下,填料呈顆粒離開燒蝕表面,從而形成粗糙的表面。
石墨的抗熱震能力在高溫部件上套用的石墨材料,要求具有良好的抗熱震能力(或稱抗熱衝擊能力),特別是作發動機噴管和燃氣舵,使用過程中石墨材料表面突然受熱(或冷卻),產生嚴重的溫度梯度而引起熱應力足以使石墨破壞。通常用熱震因子R或R’值的大小來評定各類材料抗熱衝擊能力的強弱。
R=σtλ/α*E
式中σt為抗拉強度;λ為熱導率;a為線膨脹係數;E為瞬時溫度應變值。