正文
早期氰化法 1898年,德國A.弗蘭克等人發現空氣中的氮能被碳化鈣固定而生成氰氨化鈣(又稱石灰氮),進一步與過熱水蒸氣反應即可獲得氨:CaCN2+3H2O─→2NH3+CaCO3
1905年,德國氮肥公司建成世界上第一座生產氰氨化鈣的工廠,這種制氨方法稱為氰化法。第一次世界大戰期間,德國、美國主要採用該法生產氨,滿足了軍工生產的需要。氰化法固定每噸氮的總能耗為153GJ,由於成本過高,到30年代被淘汰。合成氨法 利用氮氣與氫氣直接合成氨的工業生產曾是一個較難的課題。合成氨從實驗室研究到實現工業生產,大約經歷了150年。直至1909年,德國物理化學家F.哈伯用鋨催化劑(見金屬催化劑)將氮氣與氫氣在17.5~20MPa和500~600℃下直接合成,反應器出口得到6%的氨,並於卡爾斯魯厄大學建立一個每小時80g合成氨的試驗裝置(圖1)。
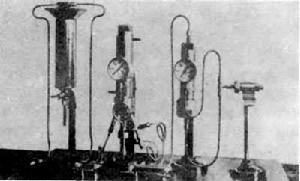
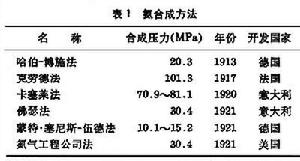
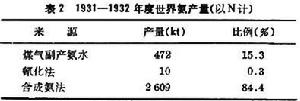
原料構成改變 自從合成氨工業化後,原料構成經歷了重大的變化。
①煤造氣時期 第一次世界大戰結束,很多國家建立了合成氨廠,開始以焦炭為原料。20年代,隨著鋼鐵工業的興起,出現了用焦爐氣深冷分離制氫的方法。焦炭、焦爐氣都是煤的加工產物。為了擴大原料來源,曾對煤的直接氣化進行了研究。1926年,德國法本公司採用溫克勒爐氣化褐煤成功。第二次世界大戰結束,以焦炭、煤為原料生產的氨約占一半以上。
②烴類燃料造氣時期 早在20~30年代,甲烷蒸汽轉化制氫已研究成功。50年代,天然氣、石油資源得到大量開採,由於以甲烷為主要組分的天然氣便於輸送,適於加壓操作,能降低氨廠投資和制氨成本,在性能較好的轉化催化劑(見無機化工催化劑)、耐高溫的合金鋼管相繼出現後,以天然氣為原料的制氨方法得到廣泛套用。接著抗積炭的石腦油蒸汽轉化催化劑研製成功,缺乏天然氣的國家採用了石腦油為原料。60年代以後,又開發了重質油部分氧化法制氫。到1965年,焦、煤在世界合成氨原料中的比例僅占5.8%。從此,合成氨工業的原料構成由固體燃料轉向以氣、液態烴類燃料為主的時期。
裝置大型化 由於高壓設備尺寸的限制,50年代以前,最大的氨合成塔能力不超過日產200t氨,60年代初不超過日產400t氨。隨著由汽輪機驅動的大型、高壓離心式壓縮機研製成功,為合成氨裝置大型化提供了條件,大型合成氨廠的數目也逐年增多(圖2)。合成氨廠大型化通常指規模在日產540t(600sh.t)以上的單系列裝置。1963和1966年美國凱洛格公司先後建成世界上第一座日產540t和900t氨的單系列裝置,顯示出大型裝置具有投資少、成本低、占地少和勞動生產率高等顯著優點。從此,大型化成為合成氨工業的發展方向。近20多年來,新建裝置大多為日產1000~1500t氨,1972年建於日本千葉的日產1540t(1700st.t)氨廠是目前世界上已投入生產的最大單系列裝置。
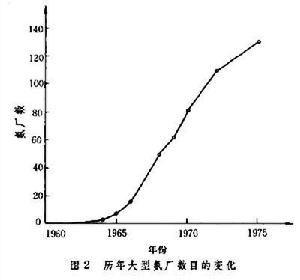
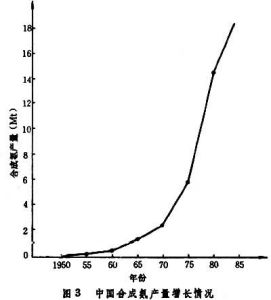