概念
加料倉是冶煉時加工爐的一部分,如圖a所示,左邊是VOD爐簡圖,右邊是真空機組簡圖,其中5一加料倉,另有1一真空罐,2一罐蓋l,3一鋼桶蓋I,4一氧槍,6一鋼桶,7一滑動水口,8一吹氬口,9一蒸汽,10一級泵,11—二級泵,12一三級泵,1 3一冷凝器,14一四級泵,15一冷凝器,16一五級泵,17一六級泵
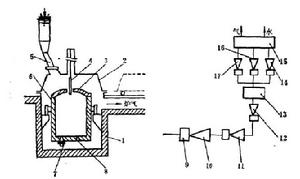
檢測
以閃速煉銅為例:檢測系統中,對於WIQA341060加料倉料量的檢測,檢測儀表是料斗稱,量程是0~4 t。安裝在加料倉料斗上。
設計問題
(1)儲存物料量
(2)工作效率
(3)生產工藝複雜度
(4)安裝操作
還有設備的連線、有效地保證物料在設備倉體內部的均勻分布以及減少物料在流動過程中對設備的磨損,增加設備的使用壽命都是料倉設計時需要考慮的問題。
設計意義
隨著石油市場價格的快速上揚 ,國內電石行業出現了快速增 長的勢頭 ,根據《電石行業準入條件》的要求,電石行業 25.5MVA及以上容量的電石爐的大量需求已漸呈趨勢。爐頂料倉是電石爐生產工藝過程必不可少 的組成部分 ,其容量的確定對電石爐的建設成本及運行起著一定的影響作用。
控制
隨著國內大型 電爐 的不斷改進 、研發 ,爐頂加料系統也隨之加大、加多。而 PLC及計算機技術的套用 ,其現場信號監控、中央控制器對信號及過程數據的快速處理能力 ,實現了電石生產過程和乾法冶煉工藝下的最重要的工序——加料系統全過程的自動化檢測和控制。即電石生產中爐頂料倉原料加料統計實現了按批次 、按種類統計電爐生產中每個班組每個料倉的原料消耗 ,它對於了解爐內每個落料點的吃料情況 、各出爐口的出爐情況 、分析各班組原料消耗及成品產量具有重要的指導意義。
加料系統包括原料稱量加料控制系統 、原料卸料控制系統 、原料皮帶輸送控 制系統 、爐頂料倉刮板分料控制系統、爐頂料倉雷達料位檢測系統及原料統計系統 。
在控制信號配置PLC控制的物料稱重裝置中,加料控制門打開時,物料從加料倉進入料斗,隨著料斗中物料的增加,在重力作用下光電編碼器旋轉的角度增大,光電編碼器將重量角位移信號轉變為高速脈衝信號,通過PLC高速計數器連線埠輸入PLC,使用高速計數器HSCl對脈衝進行計數,從而實現對料斗中物料重量的測量。當達到設定的重量時,PLC控制電磁閥,執行元件驅動加料控制門關閉,停止加料。空料斗放置到位後,加料控制門打開,重新開始加料。
套用舉例
溫山冶煉廠1992年4月建設的QSL鉛廠,用Ausmelt技術處理QSL爐渣,處理的原料為鉛精礦和濕法煉鋅過程產生的鉛—銀渣組成的混合物料。
該廠有兩個加料倉,一個是作還原劑用的煤倉,另一個是提供水淬固體渣的料倉。當QSL反應器因需要維修而不生產液態渣時,臨時將固態渣加入Ausmeh爐內。給料量控制在1.2-12t/h。用做還原劑的塊狀煤篩分成粒度5—20mm,其給料速度控制在100~1000kg/h。兩種物料用給料秤稱量後,用皮帶輸送機和盤式輸送機送往爐頂的加料口。