簡介
將每一個具有獨立電氣性能的晶片分離出來的過程叫做劃片或切割(Dicing Saw)。因此,在設計這些切割通道的掩膜時,必須要在鈍化層上留出開口,避免切割金屬或其他材料,在切割通道上只有矽。
常見劃片槽示意圖如下,圖中D1、D2代表劃片街區中保留完整的部分,kerf代表刀痕寬度,scribe width為劃片槽寬度 。
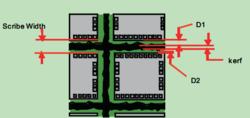
圖1 劃片槽示意圖
劃片槽的作用除了在分離晶片時起到隔離作用,另外也能夠通過測試圖形起到監控工藝的作用。在周邊測試中,測試圖案被放置在劃片街區內。這種將測試圖案放在劃片街區內的方法能夠實現實時監控工藝波動,節約了寶貴的矽片資源。具體可以放進劃片截取的測試圖案的數目取決於在一個掩膜(Reticle)內劃片街區的長度和面積。在一個Reticle內劃片街區上的測試圖案,會隨著步進式光刻的進行,在整個晶圓上得到複製。在Reticle內部,所有的測試圖案都是互不相同的。而在不同的Reticle之間,測試圖案是重複的 。
劃片槽製作技術分類
金剛石劃片
金剛石劃片這是最早出現的劃片方法,是用得最少的方法。這種方法與劃玻璃的原理相同。使用鋒利的金剛石尖端,以50克左右的固定載荷劃出小片的分割線,再加上彎曲力矩使之分成小片。一般來說,金剛石劃片時線條寬度為 6—8μm、深度為 5μm,矽表面發生塑性變形,線條周圍有微裂紋等。如果劃片時出現切屑,掰片時就可能裂開,小片的邊緣又不整齊,分片就不能順利進行。金剛石尖有圓錐形 (l點式) 、四方錐形 (4點式) 等。圓錐形的金剛石尖是採用其十二面體晶格上的 <111>軸, 並將尖端加工成半徑 2-5μm的球面。劃片的成品率在很大程度上取決於金剛石尖端的加工精度及其鋒利性的保持情況。
雷射劃片
第二代劃片的方法是雷射劃片。雷射劃片就是將雷射呈脈衝狀照射在矽片表面上,被雷射照射的那部分矽就會因為吸收雷射而被加熱到 10000℃的高溫,並在一瞬間即氣化或熔化,使矽片留下溝槽,然後再沿溝槽進行分開的方法。雷射劃片時,矽粉會粘在矽片表面上,所以還必須對矽片上的灰塵進行必要的處理。該方法劃矽片比金剛石劃片的成品率高,所以曾經在一個時期內替代了金剛石劃片。但雷射劃片對工藝條件十分敏感。雷射功率、劃片速度、焦點位置、氣流壓力等參數的波動或變化都會影響劃片質量,致使劃片深度尺寸不均勻,導致分片時容易碎片,降低成品率,增加了成本。同時雷射劃片時,高溫對材料也有很大的影響,從而影響到晶片的性能。但雷射劃片相對於其他的劃片技術來說,結構簡單,在切割中和切割後晶片碎裂率少,無論單晶矽片薄厚,切口寬度均小於3μm,切口邊緣平直、精準、光滑,能夠在每片晶圓上製作並切割出更多數量的晶片。
砂輪劃片
第三代劃片機是砂輪劃片機。砂輪劃片機是利用高速運轉的空氣靜壓主軸帶動刀片,通過光柵尺和導軌系統的控制,將刀刃定位在加工材料上,最終形成具有一定深度和寬度的切口。砂輪劃片工藝質量與主軸轉速、切割速度、刀片厚度等都有一定的關係。相對合理的主軸轉速能有效地控制刀片在隨主軸轉動時的相對震動、有利於刀片在切割時的徑向穩定性,從而提高切割質量。刀片的切割速度決定工作效率,如果切割速度不斷變大,在切割的過程中沿溝槽的刀具的速度也會變得不好控制。切割速度會受制於待加工材料的硬度,如矽晶圓表面材料的硬度直接決定切割速度。如果切割超硬材料時切割深度過大都不利於刀片的正常使用,並最終影響到刀片的壽命 。
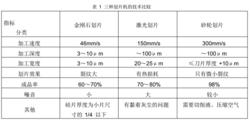
圖2:三中劃片機的技術比較