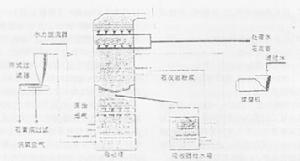
發展情況
芬蘭LIFAC(爐內噴鈣及未反應氧化鈣活化)是一種先進的煙氣脫硫工藝,自八十年代以來,在世界各地的燃煤電廠得到了廣泛的套用。芬蘭Tampella和IVO公司開發的這種脫硫工藝,於1986年首先投入商業運行。LIFAC工藝的脫硫效率一般為60%~85%。加拿大最先進的燃煤電廠Shand電站採用LIFAC煙氣脫硫工藝,8個月的運行結果表明,其脫硫工藝性能良好,脫硫率和設備可用率都達到了一些成熟的SO2控制技術相當的水平。我國下關電廠引進LIFAC脫硫工藝,其工藝投資少、占地面積小、沒有廢水排放,有利於老電廠改造。
目前,中芬電氣通過下關電廠和浙江錢清電廠的125MW機組煙氣脫硫工程已經具體地掌握了芬蘭的LIFAC技術,再加上有多年獨立研究開發的基礎,國內在大中型機組實施噴鈣脫硫成套技術有成功的把握。在國內LIFAC噴鈣脫硫成套技術開發的攻關成果得到了有關部門的充分肯定,1996年獲國家環保局科學進步三等獎,國家計委、國家科委、國家財務部“八五”科技攻關重大科技成果獎,國家環保局示範工程榮譽證書,1997年獲國家環保局環保科技成果轉化項目證書,1998年獲得國家環保總局環保實用技術推廣計畫項目證書,機械工業部科學技術進步三等獎等。
“九五”以來,(原)國家科委,國家環保總局支持進行電站鍋爐噴鈣脫硫成套技術工程化開發,不但進行了有關工程化問題的物理模擬試驗,而且開發了一系列計算機數值模擬程式,對35t/h、130t/h、420t/h煤粉鍋爐實施噴鈣脫硫成套技術進行了可行性研究,並做出設計方案。與此同時,國內還配合南京下關電廠引進同類型的芬蘭LIFAC技術專門開發了新型的420t/h鍋爐。
工藝系統
(1)石灰石粉系統包括石灰石粉的製備、計量、運輸、貯存、分配和噴射等設備。
(2)水利化反就器系統包括水利化水霧化、煙氣與水混合反應、下部碎渣與除渣、器壁防垢等設備。
(3)脫硫灰再循環系統包括電除塵器下部集灰、貯存、輸送等裝置。
(4)煙氣再熱系統包括煙氣再熱裝置和主煙氣混合用噴嘴等。
脫硫原理
爐膛內噴鈣脫硫的基本原理:石灰石粉藉助氣力噴入爐膛內850~1150度(攝氏)煙溫區,石英鐘灰石煅燒分解成CaO和CO2,部分CaO與煙氣中的SO2。爐膛內噴入石灰石後的SO2。反應生成CaSO4,脫除煙氣中一部分SO2。爐膛內噴入石灰石後的SO2脫除率隨煤種、石灰石粉特性、爐型及其空氣動力場和溫度場特性等因素而改變,一般在20%~50%。
活化器內脫硫的基本原理:煙氣增濕活化售硫反應的機理主要是由於脫硫劑顆粒和水滴相碰撞以後,在脫硫劑顆粒表面形成一層水膜,脫硫劑及SO2氣體均向其中溶解,從而使脫硫反應由原來的氣-固反應轉化成水膜中的離子反應,煙氣中大部分未及時在爐膛內參與反應的CaO與煙氣中的SO2反應生成CaSO3和CaSO4。活化反應器內的脫硫效率通常在40%~60%,其高低取決於霧化水量、液滴粒徑、水霧分布和煙氣流速、出口煙溫,最主要的控制因素是脫硫劑顆粒與水滴碰撞的機率。
由於活化反應器出口煙氣中還有一部分可利用的鈣化物,為了提高鈣的利用率,可以將電除塵器收集下來的粉塵返回一部分到活化反應器中再利用,即脫硫灰再循環。活化器出口煙溫因霧化水的蒸發而降低,為避免出現煙溫低於露點溫度的情況發生,可採用煙氣再加熱的方法,將煙氣溫度提高至露點以上10~15度(攝氏)加熱工質可用蒸氣或熱空氣,也可用未經活化器的煙氣。
整個LIFAC工藝系統的脫硫效率η為爐膛脫硫效率η和活化器脫硫效率η之和,即η=η1+(1-η1)η2,一般為60%~85%。LIFAC脫硫方法適用於燃用含硫量為0.6%~2.5%的煤種、容量為50~300MW燃煤鍋爐。與濕式煙氣脫硫技術相比,投資少,占地面積小,適合於現有電廠的改造。
脫硫過程
LIFAC脫硫的主要工藝有三個階段:爐內噴鈣 活化及乾灰再循環 灰漿再循環
第一步、爐內噴鈣
其主要特徵為在爐膛上部恰當的高溫區域噴脫硫劑石灰石粉,使之與煙氣中的 SO2 進行化學反應。
第二步、活化及乾灰再循環
在爐膛中未反應的石灰粉和 SO2 進入到布置在鍋爐後面的煙氣增濕--活化反應塔內作進一步的化學反應,大大提高了脫硫效率。(按電廠的實際情況,推薦採用前面兩個脫硫階段,即可獲得滿意的效率。)在捷克2×362MW的電廠中,只運用第二步就可穩定經濟地實現85%的脫硫效率。
第三步、灰漿再循環
是把ESP和活化器下面灰斗中部分的灰加水成灰漿後,再循環到活化器中脫除SO2,以進一步提高脫硫效率,使脫硫效率可達90% 。
主要設備有:
噴鈣設備、活化反應器、灰處理設備及顆粒收集器。