特點
1. 剛性攻絲
主軸控制迴路為位置閉環控制,主軸電機的旋轉與攻絲軸(Z軸)進給完全同步,從而實現高速高精度攻絲。
2. 複合加工循環
複合加工循環可用簡單指令生成一系列的切削路徑。比如定義了工件的最終輪廓,可以自動生成多次粗車的刀具路徑,簡化了車床編程。
3. 圓柱插補
適用於切削圓柱上的槽,能夠按照圓柱表面的展開圖進行編程。
4. 直接尺寸編程
可直接指定諸如直線的傾角、倒角值、轉角半徑值等尺寸,這些尺寸在零件圖上指定,這樣能簡化部件加工程式的編程。
5. 記憶型螺距誤差補償 可對絲槓螺距誤差等機械系統中的誤差進行補償,補償數據以參數的形式存儲在CNC的存儲器中。
6. CNC內裝PMC編程功能
PMC對工具機和外部設備進行程式控制
7. 隨機存儲模組
MTB(工具機廠)可在CNC上直接改變PMC程式和宏執行器程式。由於使用的是快閃記憶體晶片,故無需專用的RAM寫入器或PMC的調試RAM。
8. 顯示裝置
系統組成
1. 系統構成
圖6 系統硬體概要
圖6從總體上描述了系統板上應該連線的硬體和應具有的功能。
圖7 FANUC 0i系列控制單元構成及連線
圖7所表示的是FANUC0i控制單元及其所要連線的部件示意圖,每一個文字方框中表示的部件,都按照圖中所列的位置(插座、插槽)與系統相連線。具體的連線方式、方法請參照FANUC連線說明書(硬體)的各章節。
2. 系統連線
系統綜合連線圖
系統的綜合連線詳圖中標示了系統板上的插槽名以及每一個插槽所連線的部件。
3. 系統構成
主軸電動機的控制有兩種接口;模擬和數字(串列傳送)輸出。模擬接口需用其他公司的變頻器及電動機。
(1) 模擬主軸接口
(2) 串列主軸接口
4. 數字伺服
伺服的連線分A型和B型,由伺服放大器上的一個短接棒控制。A型連線是將位置反饋線接到cNc系統,B型連線是將其接到伺服放大器。0i和近期開發的系統用B型。o系統大多數用A型。兩種接法不能任意使用,與伺服軟體有關。連線時最後的放大器JxlB需插上FANUC (提供的短接插頭,如果遺忘會出現#401報警.另外,薦選用一個伺服放大器控制兩個電動機,應將大電動機電摳接在M端子上,小電動機接在L端子上.否則電動機運行時會聽到不正常的嗡聲。
數控車床
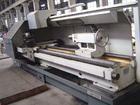
數控車床編程如何確定加工方案
(一)確定加工方案的原則
加工方案又稱工藝方案,數控工具機的加工方案包括制定工序、工步及走刀路線等內容。
在數控工具機加工過程中,由於加工對象複雜多樣,特別是輪廓曲線的形狀及位置千變萬化,加上材料不同、批量不同等多方面因素的影響,在對具體零件制定加工方案時,應該進行具體分析和區別對待,靈活處理。只有這樣,才能使所制定的加工方案合理,從而達到質量優、效率高和成本低的目的。
制定加工方案的一般原則為:先粗後精,先近後遠,先內後外,程式段最少,走刀路線最短以及特殊情況特殊處理。
(1)先粗後精
為了提高生產效率並保證零件的精加工質量,在切削加工時,應先安排粗加工工序,在較短的時間內,將精加工前大量的加工餘量(如圖3-4中的虛線內所示部分)去掉,同時儘量滿足精加工的餘量均勻性要求。
當粗加工工序安排完後,應接著安排換刀後進行的半精加工和精加工。其中,安排半精加工的目的是,當粗加工後所留餘量的均勻性滿足不了精加工要求時,則可安排半精加工作為過渡性工序,以便使精加工餘量小而均勻。
在安排可以一刀或多刀進行的精加工工序時,其零件的最終輪廓應由最後一刀連續加工而成。這時,加工刀具的進退刀位置要考慮妥當,儘量不要在連續的輪廓中安排切人和切出或換刀及停頓,以免因切削力突然變化而造成彈性變形,致使光滑連線輪廓上產生表面劃傷、形狀突變或滯留刀痕等疵病。
(2)先近後遠
這裡所說的遠與近,是按加工部位相對於對刀點的距離大小而言的。在一般情況下,特別是在粗加工時,通常安排離對刀點近的部位先加工,離對刀點遠的部位後加工,以便縮短刀具移動距離,減少空行程時間。對於車削加工,先近後遠有利於保持毛坯件或半成品件的剛性,改善其切削條件。
(3)先內後外
對既要加工內表面(內型、腔),又要加工外表面的零件,在制定其加工方案時,通常應安排先加工內型和內腔,後加工外表面。這是因為控制內表面的尺寸和形狀較困難,刀具剛性相應較差,刀尖(刃)的耐用度易受切削熱影響而降低,以及在加工中清除切屑較困難等。
(4)走刀路線最短
確定走刀路線的工作重點,主要用於確定粗加工及空行程的走刀路線,因精加工切削過程的走刀路線基本上都是沿其零件輪廓順序進行的。
走刀路線泛指刀具從對刀點(或工具機固定原點)開始運動起,直至返回該點並結束加工程式所經過的路徑,包括切削加工的路徑及刀具引入、切出等非切削空行程。
在保證加工質量的前提下,使加工程式具有最短的走刀路線,不僅可以節省整個加工過程的執行時間,還能減少一些不必要的刀具消耗及工具機進給機構滑動部件的磨損等。
最佳化工藝方案除了依靠大量的實踐經驗外,還應善於分析,必要時可輔以一些簡單計算。
上述原則並不是一成不變的,對於某些特殊情況,則需要採取靈活可變的方案。如有的工件就必須先精加工後粗加工,才能保證其加工精度與質量。這些都有賴於編程者實際加工經驗的不斷積累與學習。
(二)加工路線與加工餘量的關係
在數控車床還未達到普及使用的條件下,一般應把毛坯件上過多的餘量,特別是含有鍛、鑄硬皮層的餘量安排在普通車床上加工。如必須用數控車床加工時,則要注意程式的靈活安排。安排一些子程式對餘量過多的部位先作一定的切削加工。
(1)對大餘量毛坯進行階梯切削時的加工路線
(2)分層切削時刀具的終止位置
(三)車螺紋時的主軸轉速
數控車床加工螺紋時,因其傳動鏈的改變,原則上其轉速只要能保證主軸每轉一周時,刀具沿主進給軸(多為Z軸)方向位移一個螺距即可,不應受到限制。但數控車床加工螺紋時,會受到以下幾方面的影響:
(1)螺紋加工程式段中指令的螺距(導程)值,相當於以進給量(mm/r)表示的進給速度F,如果將工具機的主軸轉速選擇過高,其換算後的進給速度(mm/min)則必定大大超過正常值;
(2)刀具在其位移的始/終,都將受到伺服驅動系統升/降頻率和數控裝置插補運算速度的約束,由於升/降頻特性滿足不了加工需要等原因,則可能因主進給運動產生出的“超前”和“滯後”而導致部分螺牙的螺距不符合要求;
(3)車削螺紋必須通過主軸的同步運行功能而實現,即車削螺紋需要有主軸脈衝發生器(編碼器)。當其主軸轉速選擇過高,通過編碼器發出的定位脈衝(即主軸每轉一周時所發出的一個基準脈衝信號)將可能因“過沖”(特別是當編碼器的質量不穩定時)而導致工件螺紋產生亂扣。
因此,車螺紋時,主軸轉速的確定應遵循以下幾個原則:
(1)在保證生產效率和正常切削的情況下,宜選擇較低的主軸轉速;
(2)當螺紋加工程式段中的導入長度δ1和切出長度δ2(如圖所示)考慮比較充裕,即螺紋進給距離超過圖樣上規定螺紋的長度較大時,可選擇適當高一些的主軸轉速;
(3)當編碼器所規定的允許工作轉速超過工具機所規定主軸的最大轉速時,則可選擇儘量高一些的主軸轉速;
(4)通常情況下,車螺紋時的主軸轉速(n螺)應按其工具機或數控系統說明書中規定的計算式進行確定,其計算式多為:
n螺≤n允/L(r/min) 式中n允—編碼器允許的最高工作轉速(r/min);
L—工件螺紋的螺距(或導程,mm)。
FANUC 0-TD系統
G 代碼命令
代碼組及其含義“模態代碼” 和 “一般” 代碼“形式代碼” 的功能在它被執行後會繼續維持,而 “一般代碼” 僅僅在收到該命令時起作用。定義移動的代碼通常是“模態代碼”,像直線、圓弧和循環代碼。反之,像原點返回代碼就叫“一般代碼”。每一個代碼都歸屬其各自的代碼組。在“模態代碼”里,當前的代碼會被載入的同組代碼替換。
G代碼 組別 解釋
G00 定位 (快速移動)
G01 直線切削
G02 順時針切圓弧 (CW,順時鐘)
G03 逆時針切圓弧 (CCW,逆時鐘)
G04 暫停 (Dwell)
G09 停於精確的位置
G20 英制輸入
G21 公制輸入
G22 內部行程限位 有效
G23 內部行程限位 無效
G27 檢查參考點返回
G28 參考點返回
G29 從參考點返回
G30 回到第二參考點
G32 切螺紋
G40 取消刀尖半徑偏置
G41 刀尖半徑偏置 (左側)
G42 刀尖半徑偏置 (右側)
G50 修改工件坐標;設定主軸最大的 RPM
G52 設定局部坐標系
G53 選擇工具機坐標系
G70 精加工循環
G71 內外徑粗切循環
G72 台階粗切循環
G73 成形重複循環
G74 Z 向步進鑽削
G75 X 向切槽
G76 切螺紋循環
G80 取消固定循環
G83 鑽孔循環
G84 攻絲循環
G85 正面鏜孔循環
G87 側面鑽孔循環
G88 側面攻絲循環
G89 側面鏜孔循環
G90 (內外直徑)切削循環
G92 切螺紋循環
G94 (台階) 切削循環
G96 12 恆線速度控制
G97 恆線速度控制取消
G98 每分鐘進給率
G99 每轉進給率
代碼解釋
G00 定位
1. 格式 G00 X_ Z_ 這個命令把刀具從當前位置移動到命令指定的位置 (在絕對坐標方式下), 或者移動到某個距離處 (在增量坐標方式下)。 2. 非直線切削形式的定位 我們的定義是:採用獨立的快速移動速率來決定每一個軸的位置。刀具路徑不是直線,根據到達的順序,機器軸依次停止在命令指定的位置。 3. 直線定位 刀具路徑類似直線切削(G01) 那樣,以最短的時間(不超過每一個軸快速移動速率)定位於要求的位置。 4. 舉例 N10 G0 X100 Z65
G01 直線插補
1. 格式 G01 X(U)_ Z(W)_ F_ ;直線插補以直線方式和命令給定的移動速率從當前位置移動到命令位置。X, Z: 要求移動到的位置的絕對坐標值。U,W: 要求移動到的位置的增量坐標值。
2. 舉例① 絕對坐標程式 G01 X50. Z75. F0.2 ;X100.; ② 增量坐標程式G01 U0.0 W-75. F0.2 ;U50.
圓弧插補 (G02, G03)
1. 格式 G02(G03) X(U)__Z(W)__I__K__F__ ;G02(G03) X(U)__Z(W)__R__F__ ;
G02 – 順時鐘 (CW)G03 – 逆時鐘 (CCW)X, Z –在坐標系裡的終點U, W – 起點與終點之間的距離I, K – 從起點到中心點的矢量 (半徑值)R – 圓弧範圍 (最大180 度)。2. 舉例① 絕對坐標系程式G02 X100. Z90. I50. K0. F0.2或G02 X100. Z90. R50. F02;② 增量坐標系程式G02 U20. W-30. I50. K0. F0.2;或G02 U20. W-30. R50. F0.2;
第二原點返回 (G30)
坐標系能夠用第二原點功能來設定。 1. 用參數 (a, b) 設定刀具起點的坐標值。點 “a” 和 “b” 是工具機原點與起刀點之間的距離。 2. 在編程時用 G30 命令代替 G50 設定坐標系。 3. 在執行了第一原點返回之後,不論刀具實際位置在那裡,碰到這個命令時刀具便移到第二原點。 4. 更換刀具也是在第二原點進行的。
切螺紋 (G32)
1. 格式 G32 X(U)__Z(W)__F__ ; G32 X(U)__Z(W)__E__ ; F –螺紋導程設定 E –螺距 (毫米) 在編制切螺紋程式時應當帶主軸轉速RPM 均勻控制的功能 (G97),並且要考慮螺紋部分的某些特性。在螺紋切削方式下移動速率控制和主軸速率控制功能將被忽略。而且在送進保持按鈕起作用時,其移動進程在完成一個切削循環後就停止了。 2. 舉例 G00 X29.4; (1循環切削) G32 Z-23. F0.2; G00 X32; Z4.; X29.;(2循環切削) G32 Z-23. F0.2; G00 X32.; Z4. 刀具直徑偏置功能 (G40/G41/G42)
1. 格式 G41 X_ Z_;G42 X_ Z_;
在刀具刃是尖利時,切削進程按照程式指定的形狀執行不會發生問題。不過,真實的刀具刃是由圓弧構成的 (刀尖半徑) 就像上圖所示,在圓弧插補和攻螺紋的情況下刀尖半徑會帶來誤差。2. 偏置功能
命令 切削位置 刀具路徑
G40 取消 刀具按程式路徑的移動
G41 右側 刀具從程式路徑左側移動
G42 左側 刀具從程式路徑右側移動
補償的原則取決於刀尖圓弧中心的動向,它總是與切削表面法向里的半徑矢量不重合。因此,補償的基準點是刀尖中心。通常,刀具長度和刀尖半徑的補償是按一個假想的刀刃為基準,因此為測量帶來一些困難。把這個原則用於刀具補償,應當分別以 X 和 Z 的基準點來測量刀具長度刀尖半徑 R,以及用於假想刀尖半徑補償所需的刀尖形式數 (0-9)。這些內容應當事前輸入刀具偏置檔案。
“刀尖半徑偏置” 應當用 G00 或者 G01功能來下達命令或取消。不論這個命令是不是帶圓弧插補, 刀不會正確移動,導致它逐漸偏離所執行的路徑。因此,刀尖半徑偏置的命令應當在切削進程啟動之前完成; 並且能夠防止從工件外部起刀帶來的過切現象。反之,要在切削進程之後用移動命令來執行偏置的取消過
工件坐標系選擇(G54-G59)
1. 格式 G54 X_ Z_; 2. 功能 通過使用 G54 – G59 命令,來將工具機坐標系的一個任意點 (工件原點偏移值) 賦予 1221 – 1226 的參數,並設定工件坐標系(1-6)。該參數與 G 代碼要相對應如下: 工件坐標系 1 (G54) ---工件原點返回偏移值---參數 1221 工件坐標系 2 (G55) ---工件原點返回偏移值---參數 1222 工件坐標系 3 (G56) ---工件原點返回偏移值---參數 1223 工件坐標系 4 (G57) ---工件原點返回偏移值---參數 1224 工件坐標系 5 (G58) ---工件原點返回偏移值---參數 1225 工件坐標系 6 (G59) ---工件原點返回偏移值---參數 1226 在接通電源和完成了原點返回後,系統自動選擇工件坐標系 1 (G54) 。在有 “模態”命令對這些坐標做出改變之前,它們將保持其有效性。 除了這些設定步驟外,系統中還有一參數可立刻變更G54~G59 的參數。工件外部的原點偏置值能夠用 1220 號參數來傳遞。
精加工循環(G70)
1. 格式 G70 P(ns) Q(nf) ns:精加工形狀程式的第一個段號。 nf:精加工形狀程式的最後一個段號 2. 功能 用G71、G72或G73粗車削後,G70精車削。
外園粗車固定循環(G71)
1. 格式 G71U(△d)R(e)G71P(ns)Q(nf)U(△u)W(△w)F(f)S(s)T(t)N(ns)…………….F__從序號ns至nf的程式段,指定A及B間的移動指令。.S__.T__N(nf)……△d:切削深度(半徑指定)不指定正負符號。切削方向依照AA’的方向決定,在另一個值指定前不會改變。FANUC系統參數(NO.0717)指定。e:退刀行程本指定是狀態指定,在另一個值指定前不會改變。FANUC系統參數(NO.0718)指定。ns:精加工形狀程式的第一個段號。nf:精加工形狀程式的最後一個段號。△u:X方向精加工預留量的距離及方向。(直徑/半徑)△w: Z方向精加工預留量的距離及方向。
2. 功能如果在下圖用程式決定A至A’至B的精加工形狀,用△d(切削深度)車掉指定的區域,留精加工預留量△u/2及△w。
端面車削固定循環(G72)
1. 格式 G72W(△d)R(e) G72P(ns)Q(nf)U(△u)W(△w)F(f)S(s)T(t) △t,e,ns,nf, △u, △w,f,s及t的含義與G71相同。 2. 功能 如下圖所示,除了是平行於X軸外,本循環與G71相同。
成型加工複式循環(G73)
1. 格式 G73U(△i)W(△k)R(d)G73P(ns)Q(nf)U(△u)W(△w)F(f)S(s)T(t)N(ns)…………………沿A A’ B的程式段號N(nf)………△i:X軸方向退刀距離(半徑指定), FANUC系統參數(NO.0719)指定。△k: Z軸方向退刀距離(半徑指定), FANUC系統參數(NO.0720)指定。d:分割次數這個值與粗加工重複次數相同,FANUC系統參數(NO.0719)指定。ns: 精加工形狀程式的第一個段號。nf:精加工形狀程式的最後一個段號。△u:X方向精加工預留量的距離及方向。(直徑/半徑)△w: Z方向精加工預留量的距離及方向。
2. 功能本功能用於重複切削一個逐漸變換的固定形式,用本循環,可有效的切削一個用粗加工段造或鑄造等方式已經加工成型的工件。
端面啄式鑽孔循環(G74)
1. 格式 G74 R(e); G74 X(u) Z(w) P(△i) Q(△k) R(△d) F(f) e:後退量 本指定是狀態指定,在另一個值指定前不會改變。FANUC系統參數(NO.0722)指定。 x:B點的X坐標 u:從a至b增量 z:c點的Z坐標 w:從A至C增量 △i:X方向的移動量 △k:Z方向的移動量 △d:在切削底部的刀具退刀量。△d的符號一定是(+)。但是,如果X(U)及△I省略,可用所要的正負符號指定刀具退刀量。 f:進給率: 2. 功能 如下圖所示在本循環可處理斷削,如果省略X(U)及P,結果只在Z軸操作,用於鑽孔。
外經/內徑啄式鑽孔循環(G75)
1. 格式 G75 R(e); G75 X(u) Z(w) P(△i) Q(△k) R(△d) F(f) 2. 功能 以下指令操作如下圖所示,除X用Z代替外與G74相同,在本循環可處理斷削,可在X軸割槽及X軸啄式鑽孔。
螺紋切削循環(G76)
1. 格式 G76 P(m)(r)(a) Q(△dmin) R(d)G76 X(u) Z(w) R(i) P(k) Q(△d) F(f)m:精加工重複次數(1至99)本指定是狀態指定,在另一個值指定前不會改變。FANUC系統參數(NO.0723)指定。r:到角量本指定是狀態指定,在另一個值指定前不會改變。FANUC系統參數(NO.0109)指定。a:刀尖角度:可選擇80度、60度、55度、30度、29度、0度,用2位數指定。本指定是狀態指定,在另一個值指定前不會改變。FANUC系統參數(NO.0724)指定。如:P(02/m、12/r、60/a)△dmin:最小切削深度本指定是狀態指定,在另一個值指定前不會改變。FANUC系統參數(NO.0726)指定。i:螺紋部分的半徑差如果i=0,可作一般直線螺紋切削。k:螺紋高度這個值在X軸方向用半徑值指定。△d:第一次的切削深度(半徑值)l:螺紋導程(與G32)
2. 功能螺紋切削循環。
內外直徑的切削循環(G90)
1. 格式 直線切削循環:G90 X(U)___Z(W)___F___ ;按開關進入單一程式塊方式,操作完成如圖所示 1→2→3→4 路徑的循環操作。U 和 W 的正負號 (+/-) 在增量坐標程式里是根據1和2的方向改變的。錐體切削循環:G90 X(U)___Z(W)___R___ F___ ;必須指定錐體的 “R” 值。切削功能的用法與直線切削循環類似。
2. 功能外園切削循環。1. U<0, W<0, R<02. U>0, W<0, R>03. U<0, W<0, R>04. U>0, W<0, R<0
切削螺紋循環 (G92)
1. 格式 直螺紋切削循環: G92 X(U)___Z(W)___F___ ; 螺紋範圍和主軸 RPM 穩定控制 (G97) 類似於 G32 (切螺紋)。在這個螺紋切削循環里,切螺紋的退刀有可能如 [圖 9-9] 操作;倒角長度根據所指派的參數在0.1L~ 12.7L的範圍里設定為 0.1L 個單位。 錐螺紋切削循環: G92 X(U)___Z(W)___R___F___ ; 2. 功能 切削螺紋循環
台階切削循環 (G94)
1. 格式 平台階切削循環: G94 X(U)___Z(W)___F___ ; 錐台階切削循環: G94 X(U)___Z(W)___R___ F___ ; 2. 功能 台階切削 線速度控制 (G96, G97)
NC車床用調整步幅和修改 RPM 的方法讓速率劃分成,如低速和高速區;在每一個區內的速率可以自由改變。 G96 的功能是執行線速度控制,並且只通過改變RPM 來控制相應的工件直徑變化時維持穩定的切削速率。 G97 的功能是取消線速度控制,並且僅僅控制 RPM 的穩定。
設定位移量 (G98/G99)
切削位移能夠用 G98 代碼來指派每分鐘的位移(毫米/分),或者用 G99 代碼來指派每轉位移(毫米/轉);這裡 G99 的每轉位移在 NC 車床里是用於編程的。 每分鐘的移動速率 (毫米/分) = 每轉位移速率 (毫米/轉) x 主軸 RPM
軸類零件綜合車削加工——數控車床編程實例40
編製圖所示零件的加工程式。工藝條件:工件材質為45#鋼,或鋁;毛坯為直徑Φ54mm,長200mm的棒料;刀具選用:1號端面刀加工工件端面,2號端面外圓刀粗加工工件輪廓,3號端面外圓刀精加工工件輪廓,4號外圓螺紋刀加工導程為3mm,螺距為1mm 的三頭螺紋。
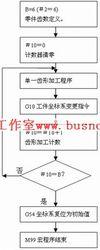
N10 G90 G54 T0101 (設立工件坐標系,,確定其坐標系,換一號端面刀,取1號刀補)N20 M03 S500 (主軸以500r/min正轉)
N30 G00 X100 Z80 (到程式起點或換刀點位置)
N40 G00 X60 Z5 (到簡單端面循環起點位置)
N50 G81 X0 Z1.5 F100 (簡單端面循環,加工過長毛坯)
N60 G81 X0 Z0 (簡單端面循環加工,加工過長毛坯)
N70 G00 X100 Z80 (到程式起點或換刀點位置)
N80 T0202 (換二號外圓粗加工刀,取2號刀補)
N90 G00 X60 Z3 (到簡單外圓循環起點位置)
N100 G80 X52.6 Z-133 F100 (簡單外圓循環,加工過大毛坯直徑)
N110 G01 X54 (到複合循環起點位置)
N120 G71 U1 R1 P16 Q32 E0.3(有凹槽外徑粗切複合循環加工)
N130 G00 X100 Z80 (粗加工後,到換刀點位置)
N140 T0303 (換三號外圓精加工刀, 取3號刀補)
N150 G00 G42 X70 Z3 (到精加工始點,加入刀尖園弧半徑補償)
N160 G01 X10 F100 (精加工輪廓開始,到倒角延長線處)
N170 X19.95 Z-2 (精加工倒2×45°角)
N180 Z-33 (精加工螺紋外徑)
N190 G01 X30 (精加工Z33處端面)
N200 Z-43 (精加工Φ30外圓)
N210 G03 X42 Z-49 R6 (精加工R6圓弧)
N220 G01 Z-53 (精加工Φ42外圓)
N230 X36 Z-65 (精加工下切錐面)
N240 Z-73 (精加工Φ36槽徑)
N250 G02 X40 Z-75 R2 (精加工R2過渡圓弧)
N260 G01 X44 (精加工Z75處端面)
N270 X46 Z-76 (精加工倒1×45°角)
N280 Z-84 (精加工Φ46槽徑)
N290 G02 Z-113 R25 (精加工R25圓弧凹槽)
N300 G03 X52 Z-122 R15 (精加工R15圓弧)
N310 G01 Z-133 (精加工Φ52外圓)
N320 G01 X54 (退出已加工表面,精加工輪廓結束)
N330 G00 G40 X100 Z80 (取消半徑補償,返回換刀點位置)
N340 M05 (主軸停)
N350 T0404 (換四號螺紋刀,取4號刀刀補)
N360 M03 S200 (主軸以200r/min正轉)
N370 G00 X30 Z5 (到簡單螺紋循環起點位置)
N380 G00 X19.3
N390 G32Z-20E1C2P120F3(加工兩頭螺紋,吃刀深0.7)
N400 G00 X30
N410 Z5
N420 X18.9
N430 G32Z-20E1C2P120F3(加工兩頭螺紋,吃刀深0.4)
N440 G00 X30
N450 Z5
N460 X18.7
N470 G32Z-20E1C2P120F3(加工兩頭螺紋,吃刀深0.2)
N480 G00 X30
N490 Z5
N500 X18.7
N510 G32Z-20E1C2P120F3(光整加工螺紋)
N520 G00 X30
N530 Z5
N540 G76C2R-3E1A60X18.7Z-20 K0.65U0.1V0.1Q0.6P240F3 (螺紋切削精加工)
N550 G00 X100 Z80 (返回程式起點位置)
N560 M05 (主軸停轉)
N570 M30 (主程式結束並復位)
1.子程式的定義
在編制加工程式中,有時會遇到一組程式段在一個程式中多次出現,或者在幾個程式中都要使用它。這個典型的加工程式可以做成固定程式,並單獨加以命名,這組程式段就稱為子程式。
2.使用於程式的目的和作用
使用於程式可以減少不必要的編程重複,從而達到減化編程的目的。其作用相當於一個固定循環。
3. 子程式的調用
在主程式中,調用於程式的指令是一個程式段,其格式隨具體的數控系統而定,FANUC—6T系統子程式調用格式為
M98 P———L———
式中 M98--子程式調用字;
p--子程式號;
L--子程式重複調用次數。
由此可見,子程式由程式調用字、子程式號和調用次數組成。
4.子程式的返回
子程式返回主程式用指令M99,它表示子程式運行結束,請返回到主程式。
5.子程式的嵌套
子程式調用下一級子程式稱為嵌套。上一級子程式與下一級子程式的關係,與主程式與第一層子程式的關係相同。子程式可以嵌套多少層由具體的數控系統決定,在FANUC—6T系統中,只能有兩次嵌套。
加工中心
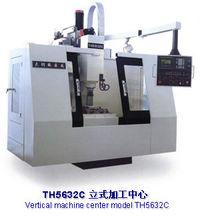
數控加工中心的對刀方法
"數控工藝基礎中"“加工坐標系設定”的內容中,已介紹了通過對刀方式設定加工坐標系的方法,這一方法也適用於加工中心。由於加工中心具有多把刀具,並能實現自動換刀,因此需要測量所用各把刀具的基本尺寸,並存入數控系統,以便加工中調用,即進行加工中心的對刀。加工中心通常採用機外對刀儀實現對刀。
圖5.29 對刀儀的基本結構
對刀儀的基本結構如圖5.29所示。圖5.29中,對刀儀平台7上裝有刀柄夾持軸2,用於安裝被測刀具,如圖5.30所示鑽削刀具。通過快速移動單鍵按鈕4和微調旋鈕5或6,可調整刀柄夾持軸2在對刀儀平台7上的位置。當光源發射器8發光,將刀具刀刃放大投影到顯示螢幕1上時,即可測得刀具在X(徑向尺寸)、Z(刀柄基準面到刀尖的長度尺寸)方向的尺寸。
鑽削刀具的對刀操作過程如下:
1.將被測刀具與刀柄聯接安裝為一體;
2.將刀柄插入對刀儀上的刀柄夾持軸2,並緊固;
3.打開光源發射器8,觀察刀刃在顯示螢幕1上的投影;
4.通過快速移動單鍵按鈕4和微調旋鈕5或6,可調整刀刃在顯示螢幕1上的投影位置,使刀具的刀尖對準顯示螢幕1上的十字線中心,如圖5.31;
5. 測得X為20,即刀具直徑為φ20mm,該尺寸可用作刀具半徑補償;
6.測得Z為180.002,即刀具長度尺寸為180.002 mm,該尺寸可用作刀具長度補償;
7.將測得尺寸輸入加工中心的刀具補償頁面;
8.將被測刀具從對刀儀上取下後,即可裝上加工中心使用。
加工中心指令
代碼 內容 備註
G00 定位(快速進給) B *
G01 直線插補(切削進給) B *
G02 圓弧插補/螺旋線(CW) B
G03 圓弧插補/螺旋線(CCW) B
G04 暫停 B
G05.1 預讀(預先讀出多個程式段) B
G07.1 圓柱插補 O
G08 預讀控制 B
G09 準確停止 B
G10 加工程式參數輸入 B
G11 加工程式參數輸入刪除 B
G15 取消極坐標指令 B
G16 極坐標指令 B
G17 X&Y平面選擇 B *
G18 Z&X平面選擇 B
G19 Y&Z平面選擇 B
G20 英寸輸入 B
G21 毫米輸入 B
G22 存儲行程檢查 O
G23 存儲行程檢查刪除 O
G27 返回參考點檢測 B
G28 返回參考點 B
G29 從參考點返回 B
G30 返回第2.3.4參考點 B
G31 跳躍功能 O
G33 螺旋切削 O
G37 自動刀具長度測量 O
G39 拐角偏置圓弧插補 B
G40 刀具徑補償取消 B *
G41 刀具左側補償 B
G42 刀具右側補償 B
G40.1 法線方向控制取消 O
G41.1 法線方向控制左側打開 O
G42.1 法線方向控制右側打開 O
G43 +方向刀具長度補償 B
G44 -方向刀具長度補償 B
G49 刀具長度補償取消 B *
G50 取消比例縮放 B
G51 比例縮放 B
G50.1 G指令鏡像功能刪除 B
G51.1 G指令鏡像功能 B
G52 局部坐標設定 B
G53 工具機坐標選擇 B
G54 工件坐標系1選擇 B *
G54.1 附加工件坐標系選擇 B
G55 工件坐標系2選擇 B
G56 工件坐標系3選擇 B
G57 工件坐標系4選擇 B
G58 工件坐標系5選擇 B
G59 工件坐標系6選擇 B
G60 單方向定位 B
G61 準確定位方式 B
G62 自動拐角倍率 B
G63 攻絲方式 O
G64 切削方式 O *
G65 宏程式調用 B
G66 宏程式模式調用 B
G67 宏程式模式調用取消 B
G68 坐標系旋轉 B
G69 取消坐標系旋轉 B
G73 步進深孔鑽循環 B
G74 輪廓攻絲循環 B
G76 精鏜孔 B
G80 固定循環取消 B *
G81 鑽孔或鑽定位孔循環 B
G82 鑽孔或鏜孔循環 B
G83 深孔鑽循環 B
G84 攻牙循環 B
G85 鏜孔循環 B
G86 鏜孔循環 B
G87 反鏜削循環 B
G88 鏜孔循環 B
G89 鏜孔循環 B
G90 絕對坐標輸入 B *
G91 增量輸入 B *
G92 坐標系設定 B
G92.1 預置工件坐標 O
G94 每分進給 B
G95 每轉進給 O
G96 恆端面切削速度控制 O
G97 取消恆端面切削速度控制 O
G98 返回初始平面 B
G99 返回R點平面 B
上面如果有不對的地方請各位指點,謝謝!
FANUC 0-MD的輔助功能代碼及其含義(M代碼)
M代碼 說明
M00 程式停
M01 選擇停止
M02 程式結束(復位)
M03 主軸正轉 (CW)
M04 主軸反轉 (CCW)
M05 主軸停
M06 換刀
M08 切削液開
M09 切削液關
M16 刀具入刀座
M28 刀座返回原點
M30 程式結束(復位) 並回到開頭
M48 主軸過載取消 不起作用
M49 主軸過載取消 起作用
M60 APC 循環開始
M80 分度台正轉(CW)
M81 分度台反轉 (CCW)
M98 子程式調用
M99 子程式結束
數控銑削加工順序的安排
加工順序通常包括切削加工工序、熱處理工序和輔助工序等,工序安排的科學與否將直接影響到零件的加工質量、生產率和加工成本。切削加工工序通常按以下原則安排:
(1)先粗後精 當加工零件精度要求較高時都要經過粗加工、半精加工、精加工階段,如果精度要求更高,還包括光整加工等幾個階段。
(2)基準面先行原則 用作精基準的表面應先加工。任何零件的加工過程總是先對定位基準進行粗加工和精加工,例如軸類零件總是先加工中心孔,再以中心孔為精基準加工外圓和端面;箱體類零件總是先加工定位用的平面及兩個定位孔,再以平面和定位孔為精基準加工孔系和其他平面。
(3)先面後孔 對於箱體、支架等零件,平面尺寸輪廓較大,用平面定位比較穩定,而且孔的深度尺寸又是以平面為基準的,故應先加工平面,然後加工孔。
(4)先主後次 即先加工主要表面,然後加工次要表面。
固定循環功能套用實例
使用刀具長度補償功能和固定循環功能加工如圖5.13所示零件上的12個孔。
圖5.13 零件圖樣
1、分析零件圖樣,進行工藝處理
該零件孔加工中,有通孔、盲孔,需鑽、擴和鏜加工,故選擇鑽頭T01、擴孔刀T02和鏜刀T03,加工坐標系Z向原點在零件上表面處。由於有三種孔徑尺寸的加工,按照先小孔後大孔加工的原則,確定加工路線為:從編程原點開始,先加工6個φ6的孔,再加工4個φ10的孔,最後加工2個φ40的孔。T01、T02的主軸轉數S=600r/min,進給速度F=120mm/min;T03主軸轉數S=300r/min,進給速度F=50mm/min。
2、加工調整
T01、T02和T03的刀具補償號分別為H01、H02和H03。對刀時,以T01刀為基準,按圖5.13中的方法確定零件上表面為Z向零點,則H01中刀具長度補償值設定為零,該點在G53坐標系中的位置為Z-35。對T02,因其刀具長度與T01相比為140-150=-10mm,即縮短了10mm,所以將H02的補償值設為-10。對T03同樣計算,H03的補償值設定為-50,如圖5.14所示。換刀時,採用O9000子程式實現換刀。
根據零件的裝夾尺寸,設定加工原點G54:X=-600,Y=-80,Z=-35。
3、數學處理
在多孔加工時,為了簡化程式,採用固定循環指令。這時的數學處理主要是按固定循環指令格式的要求,確定孔位坐標、快進尺寸和工作進給尺寸值等。固定循環中的開始平面為Z=5,R點平面定為零件孔口表面+Z向3mm處。
4、編寫零件加工程式
N10 G54 G90 G00 X0 Y0 Z30 //進入加工坐標系
N20 T01 M98 P9000 //換用T01號刀具
N30 G43 G00 Z5 H01 //T01號刀具長度補償
N40 S600 M03 //主軸起動
N50 G99 G81 X40 Y-35 Z-63 R-27 F120 //加工#1孔(回R平面)
N60 Y-75 //加工#2孔(回R平面)
N70 G98 Y-115 //加工#3孔(回起始平面)
N80 G99 X300 //加工#4孔(回R平面)
N90 Y-75 //加工#5孔(回R平面)
N100 G98 Y-35 //加工#6孔(回起始平面)
N110 G49 Z20 //Z向抬刀,撤消刀補
N120 G00 X500 Y0 //回換刀點,
N130 T02 M98 P9000 //換用T02號刀
N140 G43 Z5 H02 //T02刀具長度補償
N150 S600 M03 //主軸起動
N160 G99 G81 X70 Y-55 Z-50 R-27 F120 //加工#7孔(回R平面)
N170 G98 Y-95 //加工#8孔(回起始平面)
N180 G99 X270 //加工#9孔(回R平面)
N190 G98 Y-55 //加工#10孔(回起始平面)
N200 G49 Z20 //Z向抬刀,撤消刀補
N210 G00 X500 Y0 //回換刀點
T220 M98 P9000 //換用T03號刀具
N230 G43 Z5 H03 //T03號刀具長度補償
N240 S300 M03 //主軸起動
N250 G76 G99 X170 Y-35 Z-65 R3 F50 //加工#11孔(回R平面)
N260 G98 Y-115 //加工#12孔(回起始平面)
N270 G49 Z30 //撤消刀補
N280 M30 //程式停
參數設定:
H01=0,H02=-10,H03=-50;
G54:X=-600,Y=-80,Z=-35。
宏程式
用戶宏功能是提高數控工具機性能的一種特殊功能。使用中,通常把能完成某一功能的一系列指令像子程式一樣存入存儲器,然後用一個總指令代表它們,使用時只需給出這個總指令就能執行其功能。
用戶宏功能主體是一系列指令,相當於子程式體。既可以由工具機生產廠提供,也可以由工具機用戶自己編制。
宏指令是代表一系列指令的總指令,相當於子程式調用指令。
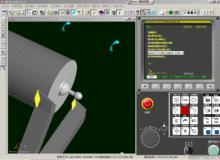
用戶宏功能的最大特點是,可以對變數進行運算,使程式套用更加靈活、方便。用戶宏功能有A、B兩類。
在常規的主程式和子程式內,總是將一個具體的數值賦給一個地址。為了使程式更具通用性、更加靈活,在宏程式中設定了變數,即將變數賦給一個地址。
(1)變數的表示
變數可以用“#”號和跟隨其後的變數序號來表示:#i(i=1,2,3......)
例:#5, #109, #501。
(2)變數的引用
將跟隨在一個地址後的數值用一個變數來代替,即引入了變數。
例:對於F#103,若#103=50時,則為F50;
對於Z-#110,若#110=100時,則Z為-100;
對於G#130,若#130=3時,則為G03。
(3)變數的類型
0MC系統的變數分為公共變數和系統變數兩類。
1)公共變數
公共變數是在主程式和主程式調用的各用戶宏程式內公用的變數。也就是說,在一個宏指令中的#i與在另一個宏指令中的#i是相同的。
公共變數的序號為:#100~#131;#500~#531。其中#100~#131公共變數在電源斷電後即清零,重新開機時被設定為“0”;#500~#531公共變數即使斷電後,它們的值也保持不變,因此也稱為保持型變數。
2)系統變數
系統變數定義為:有固定用途的變數,它的值決定系統的狀態。系統變數包括刀具偏置變數,接口的輸入/輸出信號變數,位置信息變數等。
系統變數的序號與系統的某種狀態有嚴格的對應關係。例如,刀具偏置變數序號為#01~#99,這些值可以用變數替換的方法加以改變,在序號1~99中,不用作刀偏量的變數可用作保持型公共變數#500~#531。
接口輸入信號#1000~#1015,#1032。通過閱讀這些系統變數,可以知道各輸入口的情況。當變數值為“1”時,說明接點閉合;當變數值為“0”時,表明接點斷開。這些變數的數值不能被替換。閱讀變數#1032,所有輸入信號一次讀入
用戶宏程式套用舉例 FANUC-0MC
例1:用宏程式和子程式功能順序加工圓周等分孔。設圓心在O點,它在工具機坐標系中的坐標為(X0,Y0),在半徑為r的圓周上均勻地鑽幾個等分孔,起始角度為α,孔數為n。以零件上表面為Z向零點。見圖4.35。
使用以下保持型變數:
#502:半徑r;
#503:起始角度α;
#504:孔數n,當n>0時,按逆時針方向加工,當n<0時,按順時針方向加工;
#505:孔底Z坐標值;
#506:R平面Z坐標值;
#507:F進給量。
使用以下變數進行操作運算:
#100:表示第i步鑽第i孔的記數器;
#101:記數器的最終值(為n 的絕對值);
#102:第i個孔的角度位置θi的值;
#103:第i個孔的X坐標值;
#104:第i個孔的Y坐標值;
用用戶宏程式編制的鑽孔子程式如下:
O9010
N110 G65 H01 P#100 Q0 //#100 = 0
N120 G65 H22 P#101 Q#504 //#101 = │#504│
N130 G65 H04 P#102 Q#100 R360 //#102 = #100 ×360
N140 G65 H05 P#102 Q#102 R#504 //#102 = #102 / #504
N150 G65 H02 P#102 Q#503 R#102 //#102 = #503 + #102當前孔角度位置θi =α+ (360×i) / n
N160 G65 H32 P#103 Q#502 R#102 //#103 = #502 ×COS(#102)當前孔的 X坐標
N170 G65 H31 P#104 Q#502 R#102 //#104 = #502 ×SIN(#102) 當前孔的Y坐標
N180 G90 G00 X#103 Y#104 //定位到當前孔(返回開始平面)
N190 G00 Z#506 //快速進到R平面
N200 G01 Z#505 F#507 //加工當前孔
N210 G00 Z#506 //快速退到R平面
N220 G65 H02 P#100 Q#100 R1 //#100 = #100+1孔計數
N230 G65 H84 P-130 Q#100 R#101 //當#100 < #101時,向上返回到130程式段
N240 M99 //子程式結束
調用上述子程式的主程式如下:
O0010
N10 G54 G90 G00 X0 Y0 Z20 //進入加工坐標系
N20 M98 P9010 //調用鑽孔子程式,加工圓周等分孔
N30 Z20 //抬刀
N40 G00 G90 X0 Y0 //返回加工坐標系零點
N50 M30 程式結束
設定G54:X=-400,Y=-100,Z=-50。
變數#500~#507可在程式中賦值,也可由MDI方式設定。
維修維護
例1.刀庫不停轉的故障維修
故障現象:一台配套FANUC 0MC系統,型號為XH754的數控工具機,刀庫在換刀過程中不停轉動。
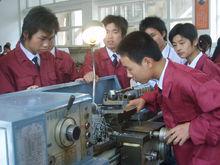
分析及處理過程:拿螺釘旋具將 刀庫伸縮電磁閥手動鈕擰到刀庫伸出位置,保證刀庫一直處於伸出狀態,復位,手動將刀庫當前刀取下,停機斷電,用扳手擰刀庫齒輪箱方頭軸,讓空刀爪轉到主軸位置,對正後再用螺釘旋具將電磁閥手動鈕關掉,讓刀庫回位。再查刀庫回零開關和刀庫電動機電纜正常,重新開機回零正常,MDI方式下換刀正常。懷疑係干擾所致,將接地線處理後,故障再未出現過。
例2.刀庫位置偏移的故障維修
故障現象:一台配套FANUC 0MC系統,型號為XH754的數控工具機,在換刀過程中,主軸上移至刀爪時,刀庫刀爪有錯動,拔插刀時,有明顯聲響,似乎卡滯:
分析及處理過程:主軸上移至刀爪時,刀庫刀爪有錯動,說明刀庫零點可能偏移,或是由於刀庫傳動存在間隙,或者刀庫上刀具重量不平衡而偏向一邊。因為插拔刀別勁,估計是刀庫零點偏移;將刀庫刀具全部卸下將主軸手搖至Y軸第二參考點附近,用塞尺測刀庫刀爪與主軸傳動鍵之間間隙,證實偏移;用手推拉刀庫,也不能利用間隙使其回正;調整參數7508直至刀庫刀爪與主軸傳動鍵之間間隙基本相等。開機後執行換刀正常。
例3.刀庫轉動中突然停電的故障維修
故障現象:一台配套FANUC 0MC系統,型號為XH754的數控工具機,換刀過程中刀庫旋轉時突遇停電,刀庫停在隨機位置。
分析及處理過程:刀庫停在隨機位置,會影響開機刀庫回零。故障發生後儘快用螺釘旋具打開刀庫伸縮電磁閥手動鈕讓刀庫伸出,用扳手擰刀庫齒輪箱方頭軸,將刀庫轉到與主軸正對,同時手動取下當前刀爪上的刀具,再將刀庫電磁閥手動鈕關掉,讓刀庫退回。經以上處理,來電後,正常回零可恢復正常。
例4.換刀過程有卡滯的故障維修
故障現象:一台配套FANUC 0MC系統,型號為XH754的數控工具機,換刀過程中,刀時有卡滯,同時聲響大。
分析及處理過程:觀察刀庫無偏移錯動,故懷疑主軸定向有問題,主軸定向偏移會影響換刀。將磁性表吸在工作檯上,將百分表頭壓在主軸傳動鍵上平面,用手搖脈衝發生器,移動X軸,看兩鍵是否等高。通過調整參數6531,將兩鍵調平;再換刀,故障排除。
維修技巧
由於現代數控系統的可靠性越來越高,數控系統本身的故障越來越低,而大部分故障主要是由系統參數的設定,伺服電機和驅動單元的本身質量,以及強電元件、機械防護等出現問題而引起的。
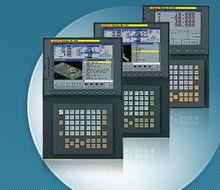
設備調試和用戶維修服務是數控設備故障的兩個多發階段。設備調試階段是對 數控工具機控制系統的設計、PLC編制、系統參數的設定、調整和最佳化階段。用戶維 修服務階段,是對強電元件、伺服電機和驅動單元、機械防護的進一步考核,以下是數控工具機調試和維修的幾個例子 :例 1 一台數控 車床採用FAGOR 80 2 5控制系統,X、Z軸使用半閉環控制,在用戶中運行半年後發現Z軸每次回參考點,總有 2、3mm的誤差,而且誤 差沒有規律,調整控制系統參數後現象仍沒消失,更換伺服電機後現象依然存在,後來仔細分析後估計是絲槓末端沒有備緊,經過螺母備緊後現象消失。
例 2 一台數控工具機採用SIEMENS 81 0T系統,工具機在中作中PLC程式突然消失,經過檢查發現保存系統電池已經沒電,更換電池,將 PLC傳到系統後,工具機可以正常運行。由於SIEMENS 81 0T系統沒有電池方面的報警信息,因此,SIEMENS 81 0T系統在用戶 中廣泛存在這種故障。
例 3 一台數控車床配FANUCO -TD系統,在調試中時常出現CRT閃爍、發亮,沒有字元出現的現 象,我們發現造成的原因主要有 :①CRT亮度與灰度旋鈕在運輸過程中出現震動。②系統在出廠時沒有經過初始化調整。③系統的主機板和存儲板有質量問題。 解決辦法可按如下步驟進行 :首先,調整CRT的亮度和灰度旋鈕,如果沒有反應,請將系統進行初始化一次,同時按RST鍵和DEL鍵,進行系統啟動,如 果CRT仍沒有正常顯示,則需要更換系統的主機板或存儲板。
例 4 一台加工中心TH6 2 40,採用FAGOT80 55控 制系統,在調試中C軸精度有很大偏差,機械精度經過檢查沒有發現問題,經過FAGOR技術人員的調試發現直線軸與旋轉軸的伺服參數的計算有很大區別,經過 重新計算伺服參數後,C軸回參考點,運行精度一切正常。對於數控工具機的調試和維修,重要的是吃透控制系統的PLC梯形圖和系統參數的設定,出現問題後,應 首先判斷是強電問題還是系統問題,是系統參數問題還是PLC梯形圖問題,要善於利用系統自身的報警信息和診斷畫面,一般只要遵從以上原則,小心謹慎,一般 的數控故障都可以及時排除。
日本公司
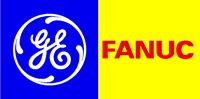
日本FANUC簡介
日本發那科公司(FANUC)是當今世界上數控系統科研、設計、製造、銷售實力最強大的企業,總人數4549人(2005年9月數字),科研設計人員1500人。2005年9月銷售額1827.8億日元(約合15.6億美元),9月每人平均銷售額9萬美元。FANUC目前數控系統月生產能力超過7000套,大量出口,銷售額在世界市場上占50%,在日本國內占70%。2005年數控系統在中國銷售約1.6萬台套,主要為中檔產品。目前Fanuc 32i加工中心已採用windows作業系統。
掌握數控工具機發展核心技術的FANUC,不僅加快了日本本國數控工具機的快速發展,而且加快了全世界數控工具機技術水平的提高。FANUC能夠在今天具有世界首位的實力與先進性,占領廣大市場,決非偶然。
遠見卓識,引進技術、自主創新
早在1956年,日本技術專家預見到未來3c(Communication、Computer、Contr01)時代即將到來,一方面集聚有關人才,另一方面即著手開展這方面的發展工作。當時富士通信製造株式會社(即現在的富士通公司)立即挑選出稻葉右衛門(1946年東京大學機械系畢業)負責控制科研組的工作。
1972年,數控富士通公司獨立出來,成為富士通FANUC,1982年7月改名為FANUC株式會社,稻葉一生領導FANUC公司,直至1995年退休。在稻葉領導下,控制研究組從1957年的幾個人不斷壯大。
稻葉回憶,1959年研製成功電液脈衝馬達,1 960年完成連續切削用開環數控的1號工具機。但是,1973年世界石油危機背景下,電液脈衝馬達的液壓閥效率低,加上隨動性能較差,FANUC組織人力研究開發新的電液脈衝馬達不成,稻葉當機立斷,做出引進美國蓋迪(Gette)直流伺服電機來代替的決定,三天內飛往美國簽訂了契約,全力投入製造,2個月完成。稻葉認為,石油危機給FANUC一個發展的好機會,其關鍵在於遠見卓識,當機立斷,在引進此技術時不斷消化創新。
加強科研、堅持商品開發三原則
稻葉認為:加強科研,是公司成功的秘訣。FANUC很早就成立兩個研究所,一為基礎研究所,一為商品開發研究所。在基礎研究所,進行的是5年、10以後商品開發所需之技術基礎研究,並希望縮短到3年拿出技術成果。
商品化目標一旦決定,立即轉到商品開發研究所,這是戰場上的精銳部隊,在一年內拿出成果。商品開發研究所是FANUC的“頭腦”,管理異常嚴格,非研究人員不能地去,對外絕對保密。商品開發三原則貼在入口大門上,人人皆知,依照執行。這三原則為:①提高商品的可靠性(Reliability up);②比同類商品降低成本(Cost cut);③用最少零件制出商品(Weniger Teile,德文)。
在FANUC,商品開發研究所是一支精銳部隊,天天都在展開激烈決戰的戰場上戰鬥。基礎研究所要的是有理論與經驗的專家人才,三不問:不問國別;不問年齡;不問性別,但要求必須是學識淵博,專業精通,教授以上水平。
FANUC所指商品,是具有超群競爭力,能開發商品有嚴格步驟:①調查世界市場,作徹底了解;②充分看清商品市場性的基礎上,決定銷售價格,在與對手競爭中,能戰勝他們;③價格必須考慮利潤,研究人員發源按照規定成本進行設計,同時必須考慮製造工藝;④設計完了,開發負責人進入工廠去當“臨時製造部長”,按預定要求抽出商品,然後才能回研究所。
成套的人才培養制度
稻葉認為,FANUC之產生、成長、發展,有今天的輝煌成績,最根本的是人才。稻葉本人是研究開發數控系統一輩子的專家,多次榮獲世界獎章榮譽。在FANUC有一整套先進的培養人才方法制度。
公司規定,從事技術工作的技術人員,必須從事過銷售工作,有經營的經驗和體會——技術工作比較死板,搞銷售工作深入用戶,與各種人接觸,了解用戶市場需求,思想方法不同。
FANUC在任命幹部之前,必須從事銷售工作,稻葉本人就是搞過經營,由前社長培訓3年後才當社長。
管理人員必須參加研究工作,這是鐵的原則,也是管理者的基本功,惟有這樣,才能勝任管理工作,對各種新技術進行綜合與管理。
稻葉認為:數控技術是21世紀最新的綜合性技術,只有各專業結合,才能開花結果。機電液氣各種專業人才,為開發具有競爭力的商品集合成科研小組,全心全意投入商品的科研開發中去,既發揮各人專長,又融為一個戰鬥整體。
構築全球性體制
FANUC不僅有公司本身發展壯大的完整戰略戰術,且有完整的占領世界市場的國際戰略。
FANUC目前在歐美亞,已先後成立許多合作公司、服務中心、各種事務所。
例如,1986年12月就在美國維吉尼亞成立了GE-FANUC自動化股份公司,持50%股份,占領了美國數控系統的市場。在韓國、中國、中國台灣、法國、義大利、瑞典、新加坡、香港、泰國及許多地方、城市建立了眾多的公司網路,到處都有發那科的商品銷售。
用FANUC的零部件,雇本地技術人員進行裝配,在當地銷售,形成FANUC本地供應服務機構。在中國的北京FANUC機電有限公司,約有160人左右,2005年在中國銷售6萬台套左右的數控系統,在中國市場上占居於首位。據FANUC調查,在2005年CIMT上,總計615台NC工具機展品,裝發那科系統的284台,占46.5%,其他德國SIEMENS系統有141台,占22.9%,MITSUBISHI電機系統有45台,占7.3%。
不斷創新產品線
FANUC以其正確的戰略戰術,發展世界廣大市場急需的數控系統,在規格系列上是當今世界上最完整的,並基於其強大的科研實力和嚴密步驟,努力不斷開發高端商品。
透徹了解用戶、世界市場需求,不斷開發新商品,占領市場,也是發那科成功的重要經驗。
例如,FANUC1990年開始出新的“系列16”在1990年9月美國芝加哥IMTS(美國國際工具機展)上展出,一時造成沸騰。“系列16”新NC系統的出現,在世界市場上掌握了主動權。又如:針對中國市場需求量大、中檔、價廉物美的數控工具機,需要量大面廣之數控系統配套,發那科於1985年開發出O系列,後又不斷改進,占領了中國的廣大市場,並通過北京FANUC機電有限公司,在中國大量推銷,獲取了巨大利潤。《2》FANUC系統介紹 FANUC系統是日本富士通公司的產品,通常其中文譯名為發那科。FANUC系統進入中國市場有非常悠久的歷史,有多種型號的產品在使用,使用較為廣泛的產品有FANUC 0、FANUC16、FANUC18、FANUC21等。在這些型號中,使用最為廣泛的是FANUC0系列。
系統在設計中大量採用模組化結構。這種結構易於拆裝、各個控制板高度集成,使可靠性有很大提高,而且便於維修、更換。FANUC系統設計了比較健全的自我保護電路。
PMC信號和PMC功能指令極為豐富,便於工具機廠商編制PMC控制程式,而且增加了編程的靈活性。系統提供串列RS232C接口,乙太網接口,能夠完成PC和工具機之間的數據傳輸。
FANUC系統性能穩定,操作界面友好,系統各系列總體結構非常的類似,具有基本統一的操作界面。FANUC系統可以在較為寬泛的環境中使用,對於電壓、溫度等外界條件的要求不是特別高,因此適應性很強。
鑒於前述的特點,FANUC系統擁有廣泛的客戶。使用該系統的操作員隊伍十分龐大,因此有必要了解該系統的一些軟、硬體上的特點。
北京公司
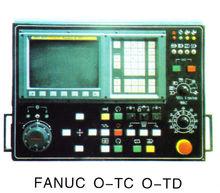
北京發那科機電有限公司是由北京工具機研究所與日本FANUC公司於1992年共同組建的合資公司,專門從事工具機數控裝置的生產、銷售與維修。註冊資金1130萬美元,美國GE-Fanuc和北京實創開發總公司各參股10%,中外雙方股比各占50%。
日本FANUC公司是世界上最大的專業生產數控裝置和機器人、智慧型化設備的著名廠商。該公司技術領先,實力雄厚,為當今世界工業自動化事業做出了重要貢獻。FANUC為日本合資公司提供了全方位技術支持。
北京工具機研究所是中國工具機工業最大的研究開發基地,國內第一台數控工具機在該所誕生,1980年引進FANUC技術,成立了國內第一家數控裝置生產廠,為中國數控工具機的發展奠定了基礎,並在數控技術及其套用方面具有領先的優勢。
北京發那科成立以來,本著“用戶至上、服務為本、品質第一”的理念,定位於“您身邊的數控專家”,致力於為中國的數控工具機提供品質卓越,服務貼心的產品和服務。公司經過近三個五年的發展,陪同中國數控工具機行業一起走過起步、發展的階段。中國數控工具機行業的發展潛力仍然很巨大,中國數控工具機的發展必將經歷騰飛的過程,而北京發那科是否還能保持在中國數控行業中的領先地位?北京發那科已逐漸認識到光依靠FANUC的技術優勢是不能長久保持北京發那科的增長勢頭的,只有形成北京發那科自己的獨特的產品和服務才能擁有長久的競爭力。