名稱:雙迴路豎噴濕法脫硫技術
定義:在煙氣脫除硫氧化物的過程中,通過吸收塔內高、低速分區脫除過程,以獲得較高脫硫效率的濕法脫硫技術。
所屬學科:電力、鋼鐵、煤炭(一級學科);環境保護(二級學科)
雙迴路豎噴濕法脫硫塔的構成
雙迴路豎噴濕法脫硫塔是由高速湍流吸收管、豎噴噴嘴、低速區噴淋層、除霧器、漿液循環槽、清洗裝置、應急裝置等部分組成,吸收過程分為高速和低速兩個吸收區。
吸收原理
在高速吸收區,來自除塵裝置的原煙氣由塔頂高速進入塔內的高速湍流吸收區,吸收液由處於高速湍流區下部的豎噴噴嘴噴出,與煙氣在湍流吸收區內逆向接觸,當氣、液兩相動量平衡時,形成一段高度湍動的駐波區,在此區域,氣液兩相在短時間內充分接觸、不斷更新,獲得充分的傳熱與傳質效率,吸收液轉向,落向塔體底部,淨化煙氣轉彎,沿塔垂直向上流動。
在低速吸收區,煙氣流速急劇下降並均勻分布,來自吸收塔上部一層噴淋聯管的霧化漿液在塔中均勻噴淋,與均勻上升的煙氣繼續反應,形成二次脫硫。淨化煙氣最後經除霧器除去殘留液滴後排放。
在高速吸收區,經過對煙氣流速、漿液量和噴射高度的有效控制,通過豎噴噴嘴獲得分布均勻的漿液顆粒,氣、液、固三相充分接觸,迅速完成傳質過程,從而達到氣體淨化的目的。
由於湍流傳質技術的作用,通過高速湍流區的煙氣能迅速降溫,有效實現了在沒有GGH情況下對吸收塔防腐層的保護;由於均氣效果的增強,提高了低速吸收區脫硫效果,降低了能耗和材料消耗;由於在高速湍流區已經完成了絕大部分脫硫工作量,減輕了低速吸收區脫硫工作壓力,與空塔相比,降低了循環泵的工作負荷和漿液材料消耗。
建立液膜泡沫區的關鍵是恰當地選擇氣體及液體的流速。
煙氣中的SO2、SO3及HCl 、HF通過泡沫層時被吸收液吸收,生成的吸收產物由於自重收集在吸收塔底部的氧化區,不斷的氧氣鼓入,吸收產物完成氧化,最終形成石膏進行排放。
為了維持系統的PH值並減少吸收劑的耗量,需要不斷地補入吸收液,同時吸收塔內的吸收劑在攪拌器和氧化空氣的攪拌下,加速了其的均布和溶解。
化學反應過程
強制氧化系統的化學過程描述如下:
(1)吸收反應
由上至下的高速煙氣與從噴嘴噴出的垂直向上的循環漿液在吸收塔內的高速湍流吸收管中逆向發生強烈碰撞,循環漿液吸收SO2,生成亞硫酸鈣,並排放出二氧化碳,反應如下:
SO2+H2O→H2SO3
H2SO3 =H+HSO3-
HSO3=H+SO3-
(2)氧化反應
一部分HSO3-在湍流層中被煙氣中的氧所氧化,其它的HSO3-在氧化池中被氧化空氣完全氧化,反應如下:
HSO3-+1/2O2→HSO4-
HSO4-=H+SO4
(3)中和反應
吸收劑漿液被引入吸收塔內中和氫離子,使吸收液保持一定的pH值,中和後的漿液再循環。中和反應如下:
Ca+SO4+2H2O→CaSO4·2H2O
H+OH→H2O
套用案例
在4台75t/h燃煤鍋爐煙氣脫硫項目的套用中,採用兩爐一塔配置,處理煙氣量按鍋爐蒸發量75t/h在BMCR運行工況下的煙氣量設計。
每台鍋爐配製靜電除塵器,除塵效率不低於99.6%,除塵器出口處煙塵排放濃度不大於200mg/Nm3。
FGD裝置設計煤種的含硫量按3.2%考慮,每台鍋爐耗煤量按12.287t/h計算,單台爐煙氣量127860.52 Nm3/h(設計工況),含硫量為6130 mg/Nm3(標態, 濕基,實際O2)。脫硫效率96%,出口排放二氧化硫含量小於400 mg/Nm3。
1、本套脫硫裝置的工藝系統包括以下子系統:
l 煙氣系統
l 吸收劑製備及輸送系統
l SO2吸收系統
l 石膏處理系統
l 工藝水系統
l 壓縮空氣系統
l 排空系統
脫硫島還包括:
l 電氣系統
l 儀表及控制系統
2、工藝流程簡述
煙氣中SO2的脫除在吸收塔內進行。吸收塔包括高速吸收區和低速吸收區。高速吸收區包括降溫系統、逆噴管、以及四個專用噴嘴,低速區包括塔體、一層噴淋裝置和兩級除霧裝置。高速區對應循環A泵,低速區對應循環B泵。
煙氣經過靜電除塵器和引風機,從引風機後部新增的FGD入口煙道經增壓風機引入FGD裝置,同時,煙氣還可從旁路擋板門經原有磚混煙道引入煙囪,直接排入大氣,即旁路運行。兩塔設定兩台增壓風機。
煙氣進入脫硫系統後,首先通過高速吸收區,高速吸收區為管內漿液向上噴射與煙氣逆向接觸,形成湍流泡沫反應區,實現高效氣液傳質,然後煙氣進一步進入低速反應區,低速吸收區為傳統的漿液向下噴淋與煙氣逆向接觸,從而進一步脫除煙氣中的SO2。經過脫硫區域後,煙氣被冷卻並達到飽和,此時攜帶有漿液小霧滴的煙氣,進入兩級布置的除霧器中進行去除,自吸收塔出口淨煙道引入煙囪,排入大氣。除霧器採用工藝水定時沖洗以防止沾污、結垢。
落入塔內的漿液進入吸收塔底部漿液池,在此進行氧化反應,生成石膏。氧化空氣系統提供吸收塔內化學反應所需氧氣,按兩用一備設計。吸收塔底部漿池內的漿液通過石膏排出泵送入石膏漿液鏇流器系統,通過鏇流器鏇流分離出的漿液中較細的固體顆粒從鏇流器溢流自流入脫水系統地坑。濃縮的大顆粒石膏漿液自流至真空脫水皮帶機脫水,皮帶脫水機分離的含少量固體顆粒的水也進入脫水系統地坑。脫水系統地坑內的漿液分別送至吸收塔、吸收劑製備系統和電廠沖渣處。
脫水後的石膏經大傾角皮帶輸送機輸至石膏庫存放,定期外運。
吸收塔漿池部分採用碳鋼襯膠/玻璃鱗片內襯進行防腐,高速吸收區和低速吸收區採用玻璃鋼製作。
為正常運行,在FGD入口設定降溫噴嘴,防止事故發生,在煙溫高於180°C情況下,可能損壞設備,FGD裝置切入旁路運 行。相關擋板的調整時間在正常情況時為75秒,在事故情況下為15~20秒,滿足保護吸收塔等設備的要求。
本期工程不設定脫硫廢水處理車間,脫硫產生的廢水直接送至鍋爐車間沖渣。詳見工藝流程圖。
3、 主要設備
此工藝的核心設備為吸收塔高速吸收區的設計,包括塔體、事故降溫系統、逆噴管以及專用噴嘴,本工程高速吸收區塔體採用玻璃鋼材質,專用噴嘴採用大口徑斜齒菊花形,材質為F4。
煙氣通過脫硫島的壓降≤4500Pa。
4、主要技術指標
脫硫裝置進口煙氣參數(單塔)
煙氣量: 187162Nm/h (標況、濕態、實際O2 )
煙氣量: 171254Nm/h (標況、乾態、實際O2 )
煙氣O2含量: 6.598% (標況、乾態、實際O2 )
煙氣SO2含量: 6130mg/ Nm(標況、濕態、實際O2 )
煙氣粉塵含量: <200 mg/ Nm (標況、濕態、實際O2 )
煙氣溫度: 100 ℃
脫硫裝置出口煙氣參數:
煙氣SO2含量: 296mg/ Nm (標況、濕態、實際O2 )
煙氣粉塵含量: 50 mg/ Nm (標況、濕態、實際O2 )
煙氣溫度: 48 ℃
脫硫效率: 95 %
鈣硫比: 1.05mol/mol
石膏量: 3.325t/h (10%含水率):
1~4號機組脫硫系統指標:(4台機組耗量)
石灰石耗量: 2 t/h
脫硫裝置電耗: 1755kW
工藝水量(工業水): 16t/h
年利用小時數: 7800 小時
系統配置特點及優勢
除了吸收塔設計不同外,雙迴路豎噴濕法脫硫系統配置與空塔配置基本相同,系統包含製漿系統、吸收系統、工藝水系統、脫水系統等,根據業主的要求不同,系統配置可相應調整,因為液氣比小、大口徑霧化噴嘴設計等技術優勢,雙迴路豎噴濕法脫硫具有如下特點。
1、占地面積小,適合於老廠改造
該脫硫系統占地面積小、高度低、布置緊湊、安裝簡便,特別適合預留空間小、現場位置有限的已建電廠脫硫技術改造項目。
2、 結構簡單,便於運行和維修保養
系統的故障主要就是噴淋系統故障,反映在噴淋管道和噴嘴的堵塞。本系統高速湍流吸收區只使用3—5隻大口徑噴嘴,安裝方式為套管抽拉式,一旦系統出現故障,可從外側將噴淋管抽出更換;低速吸收區採用大口徑球形噴嘴,也採用套管抽拉式安裝方式,大大降低了維修難度,減少維修時間,有效解決了系統維護對主機運行的影響。
3、採用新型複合材料防腐和耐高溫是吸收塔設計需要重點克服的兩個難點,特別是在吸收塔的煙氣入口和出口處,往往需要採用高性能不鏽鋼作為煙道內襯,價格昂貴且施工和維護困難。本系統在煙氣入口的高速湍流區採用耐溫玻璃鋼為主材、內襯高分子耐磨、耐高溫、耐腐蝕材料,具有使用壽命長的特點,可以處於基本免維護工作狀態。
4、技術優勢
目前世界上研發的煙氣脫硫技術有200多種,進入大規模商業套用的只有10餘種。從雙迴路豎噴濕法脫硫的研究實驗及套用上來看,技術上有如下優勢:
(一) 脫硫劑選擇性強
在脫硫劑的使用上,除石灰石粉外,可以根據當地的資源條件靈活選擇,包括化工企業的鹼性廢料、石灰、燒鹼溶液、電廠沖渣水、電石渣、白雲石、蘇打、氧化鎂/氫氧化鎂溶液、廢鋼渣、廢液氨、紙廠黑液等鹼性物質,可以大大降低系統的運行成本。
(二) 工藝方案選擇靈活
針對每個項目的具體情況,可採用並聯、串聯組合設計,即:對場地小、幾台小機組同時脫硫,可選擇“幾爐一塔”的工藝方案;在場地充裕、機組較大、脫硫改造工程資金不太充裕的情況下,可選擇“一爐兩塔”工藝方案;真正做到“度身定做”,最大限度滿足政府和企業的客觀需求。
(三) 對工況變化的適應能力強
煙氣脫硫系統的設計依據,來源於業主的設計條件。設計條件要求脫硫系統有一定的設計餘量,以適應主機系統、煤種變化等運行環境的變化。主機系統運行負荷、煤種、煤的二氧化硫含量變化,都對脫硫子系統提出了適應性的要求。但預留太大能力,會造成投資的大幅度增加;能力預留不夠,滿足不了實際運行的需要。
本系統在工藝設計上,在投資增加不多前提下,充分考慮了脫硫系統的適應能力,根據煙氣量和煙氣中二氧化硫含量的變化,對系統進行分級控制,保證系統在滿足設計要求前提下,可以上下浮動30%。在調試過程中,含硫量小於1.2%,只需運行高速吸收區的循環泵,脫硫效率即可達到90%以上。
5、經濟優勢
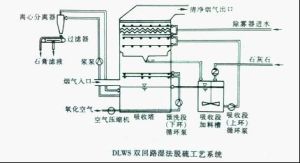