介紹
結晶器振動是連鑄技術的一個基本特徵。連鑄過程中,結晶器和坯殼間的相互作用影響著坯殼的生長和脫膜,其控制因素是結晶器的振動和潤滑。連鑄在採用固定結晶器澆注時,連鑄直接從結晶器向下拉出,由於缺乏潤滑,易與結晶器發生粘結,從而導致出現拉不動或者拉漏事故,很難進行澆注。結晶器振動對於改善鑄坯和結晶器界面間的潤滑是非常有效的,振動結晶器的發明引進,工業上大規模套用連鑄技術才得以實現。可以說,結晶器振動是澆注成功的先決條件,十年來發展的重要里程碑。近年來,冶金工業的迅速發展,要求連鑄提高拉速和增加連鑄機的生產能力,人們對結晶器振動的認識也在不斷深入和發展。
連鑄機結晶器振動的目的是防止拉坯時坯殼與結晶器黏結,同時獲得良好的鑄坯表面。結晶器向上運動時,減少新生坯殼與銅壁產生黏著,以防止坯殼受到較大的應力,使鑄坯表面出現裂紋;而當結晶器向下運動時,藉助摩擦,在坯殼上施加一定的壓力,癒合結晶器上升時拉出的裂痕,要求向下運動的速度大於拉坯速度,形成負滑脫。結晶器壁與運動坯殼之間存在摩擦力,此摩擦力被認為是撕裂坯殼進而限制澆注速度的基本因素。在初生坯殼與結晶器壁之間存在液體渣膜,此處的摩擦為黏滯摩擦,即摩擦力大小正比於相對運動速度,渣膜黏度,反比於渣膜厚度。在結晶器振動正滑脫期間摩擦力及其引起的對坯殼的拉應力就較大,可能將初生坯殼拉裂,為此開發了採用負滑脫的非正弦振動技術來減小這一摩擦力。理論研究及模擬實驗表明,適當選擇非正弦振動參數(偏斜率)可減小摩擦力50% ~60%。
在結晶器液壓伺服非正弦振動出現之前都是採用機械式振動裝置的,機械式的振動裝置由直流電動機驅動,通過萬向聯軸器,分兩端傳動兩個渦輪減速機,其中一端裝有可調節軸套,渦輪減速機後面再通過萬向聯軸器,連線兩個滾動軸承支持的偏心軸,在每個偏心輪處裝有帶滾動軸承的曲柄,並通過帶橡膠軸承的振動連桿支撐振動台,產生振動。機械振動一般採用正弦曲線振動,振動波形、振幅固定不變。
與機械振動相比,板坯連鑄機的液壓振動裝置具有一系列優點:振動力由兩點傳入結晶器,傳力均勻;在高頻振動時運動平穩,高頻和低頻振動時不失真,振動導向準確度高;結構緊湊、簡單,傳遞環節少,與結晶器對中調整方便,維護也方便;採用高可靠性和高抗干擾能力的PLC控制,可長期保證穩定的振動波形;可改變振動曲線,並可線上設定振動波形等,增加了連鑄機可澆鋼種;改善鑄坯表面與結晶器銅壁的接觸狀態,提高鑄坯表面質量並減少黏結漏鋼。
在20世紀30年代連續鑄鋼發展初期,最先使用的是固定式結晶器。在試驗過程中,由於金屬與內壁粘結,使拉坯過程不斷出現拉漏(鋼)事故。為了防止坯殼與內壁粘結,要解決對結晶器內壁的潤滑。經多種試驗,如採用間斷拉坯,不斷往結晶器中注油;採用石墨結晶器等都未取得明顯效果。直到40年代初,容漢斯(S.Junghans)和羅西(I.Rossi)把有色金屬連鑄中套用的結晶器振動方式引入到連續鑄鋼,才得以試驗成功,並使在工業中大規模套用連鑄技術成為現實。結晶器振動首先是確定結晶器的振動方式,再據此選定結晶器振動機構和振動參數。
振動原理及方式
無論是立式連鑄機還是弧形連鑄機,按結晶器振動的發展過程均採用過同步振動、負滑脫振動和正弦振動等振動方式。結晶器振動的運動動力在早期是採用凸輪機構實現,相應的振動方式為同步式和負滑式。由於凸輪加工困難,且同步式和負滑式振動有較大的衝擊,因之發展了依靠偏心輪機構實現的正弦式振動方式。偏心輪加工容易,並可調節振幅和頻率,而得以廣泛使用。隨著對連鑄工藝要求的提高,又發展了非正弦式振動,它是採用液壓缸來實現的。液壓振動的優點是可靠、靈活,可根據澆鑄條件選擇所需的振動方式。
同步振動
最早採用的一種振動方式,按其同步振動的曲線形狀稱為雲崗式振動。其振動曲線如圖1中曲線1所示。若設v為拉坯速度,v為結晶器的振動速度,v為結晶器的上升速度,v為結晶器的下降速度,則同步式振動時應滿足:
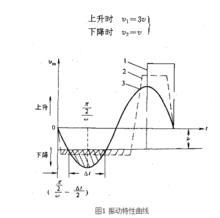
也即是說,結晶器下降時與鑄坯同步,然後以3倍的拉速上升,如此往復振動。這種振動方式的優點是能夠滿足連鑄工藝要求,實現同步運動;缺點是用機械連鎖或用電氣控制來實現嚴格的同步要求,裝置都比較複雜,速度變化時機構中衝擊力也較大。
負滑脫振動
同步振動的一種改進型式,也稱“負滑脫”(圖1中曲線2)即 v=v(1+ε)式中ε是負滑率。採用凸輪機構時取ε=10%左右,v1=(2.8~3.2)v;採用偏心輪時取ε=20%~40%。採用負滑動振動,結晶器下降時對坯殼有壓合作用,有利於拉裂坯殼的癒合,並可適當提高拉速。 正弦式振動 其振動速度按正弦規律變化。(圖1中曲線3)這種振動方式的速度變化平穩、無衝擊;能有效實現負滑動,可適當提高拉速;易於改變振動頻率和振幅,實現高頻率小振幅的要求,以改善鑄坯表面質量;用偏心輪實現振動,結構簡單,易於製造且安裝、維修方便。 非正弦式振動 這種振動方式的結晶器上振動速度慢,上升時間長,下降速度快,下降時間短。其效果是對坯殼的壓合時間短,結晶器與坯殼間的摩擦阻力小。非正弦式振動,用液壓振動機構實現。振動方式確定之後,要選擇結晶器振動的結構型式。任何振動機構都必須滿足兩個基本條件:(1)使結晶器準確地沿著一定的軌跡振動;(2)使結晶器按要求的振動方式振動。 結晶器的振動與潤滑的關係 結晶器振動的重要影響主要是對潤滑和振動痕跡形成的作用。振動的同時要求提供結晶器潤滑,兩者的共同作用是減小坯殼和結晶器壁間的摩擦力,以得到最好的表面質量和防止粘結漏鋼的最佳安全性。如前所述,結晶器振動對於改善結晶器壁間的潤滑是非常有效的,但對於結晶器振動如何影響結晶器保護渣的消耗和保護渣的潤滑作用,其機理並不十分清楚。早期的研究曾提出一個負滑脫期間保護渣流入量的模型,但是隨後的試驗結果表明,保護渣消耗量是正滑脫時間的增函式,圖4示出了保護渣消耗量與正滑脫時間的關係。可見,對於振動結晶器,正滑脫時間越長,保護渣消耗量越大,由此也引起了大量的爭論。反映振動參數對保護渣消耗的影響。 結晶器振動參數設定 結晶器振動的主要參數有兩類:一類為基本參數,包括振頻、振幅與波形偏斜率;另一類為工藝參數,包括負滑脫時間、負滑脫時間率和正滑脫時間。 結晶器振動參數的影響:結晶器振動的負滑脫時間控制鑄坯表面的振痕深度,兩者呈函式關係。負滑脫時間越長,振痕越深; 保護渣的消耗量與結晶器振動的正滑脫時間呈正函式關係,正滑脫時間越長,保護渣消耗量越大; 結晶器振動的負滑脫時間率、負滑動量、結晶器上振的最大速度都反映結晶器振動的工藝效果但它們不是獨立的參數,而且隨著結晶器振動形式的確定,一般以其正、負滑脫時間來判定結晶器振動的工藝效果。 設定不同的參數可以得到不同的振動曲線,為獲得良好的結晶器振動工藝效果,同時考慮到振動裝置所承受的衝擊力,保證振動裝置的穩定性和使用壽命。振動波形的設定具體原則是在一定的振幅、振頻及波形斜率的條件下:第 結晶器下振的最大速度V儘可能大; 結晶器上振的最大速度儘可能小; 結晶器的加速度應連續變化,且最大加速度a應儘可能小; V/a應儘可能大,即儘可能小的a實現儘可能大的Vm。