概述
產品名稱 軌道板模具 CRTS II型板在中國生產與日本“佐賀工業株式會社”一脈相承的軌道板模具,是目前國內唯一能生產與日本同品質軌道板模具的企業。其特點為:
—— 運用日本NEC公司開發的計算軟體,建立精準的力學模式進行嚴格的科學計算,使軌道板模具的各部強度和剛度及材料的運用都達到最理想的狀態。
—— 設計上採用上下等剛度原理,使軌道板模具焊接後變形上下抵消,從理論上保證模具不變形,並且在使用過程中,由於上下剛度相等不會發生變形。
—— 製造焊接時採用計算機溫度控制系統,在焊接部件上設立溫度控制點,焊接時根據金屬材料的特性使焊接點的溫度不超過300℃。當達到300℃特定值後,此處停止焊接,等溫度降低後再返回焊接,嚴格控制溫度所產生的熱變形。
—— 整體表面不平度不超過±0.1mm。
——套用獲得專利的工藝,使製造出的軌道板模具同一性好,質量高,且模具的製造周期大大縮短。
——軌道板模具焊接後,時效消除應力後表面不平度不超過±0.25mm,機加工後,表面不平度達到±0.025mm,無需熱較正,無熱應力使軌道板製品不會產生內部裂紋。
——操作定位快捷方便,節省施工工期及人力。
模具主梁材料力學模式圖
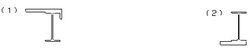
(1)斷面模量 (2)斷面模量
Ix = 3910 cm4 Ix = 3925 cm4
(1)和(2)斷面模量基本相等,所以上下剛度基本保持一樣。
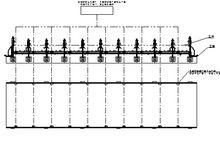
日本制雷射溫度控制儀
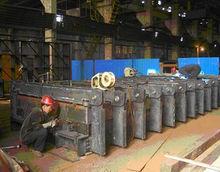
軌道板模具的優勢
1.設計優勢 嚴格的科學計算和超強的CA2ED專業繪圖軟體。
採用上下等剛度原理。
2.製造優勢 製造焊接時採用計算機溫度控制系統和套用獲得專利的工藝工裝。
3.操作簡單 檢查方便
①設計當中考慮到工作人員各種操作動作、人體結構,以減少工人的疲勞為設計理念。
②設計時吸取了德國博格式預埋件定位銷代替了舊日式的軌道板定位銷,操作只需2個人進行開合即可,方便快速,減少操作危險性。
③模具上標有刻度,方便工人檢查精度。
4..質量檢查 建立檔案 ①對於甲方提供的軌道板設計圖紙把關;
②採購原材料:要求原材料證書,川榮重工質檢記錄;
③零部件驗收合格記錄,不合格產品不接收;
④模具組裝前對主要構成板塊進行質量檢查,合格時簽發令;
⑤在工作檯點焊後進行精度測量檢查;
⑥整體拼裝檢查合格,記錄檔案;
⑦出廠前客戶驗收,把理論與實測數據記錄檔案交付客戶;
⑧構件廠安裝調試合格驗收。
5.精度高 壽命長 性能穩 不變形 ①整體表面不平度不超過±0.1mm。(已在博格板製造過程中實現)
②軌道板模具焊接、時效消除應力後表面不平度不超過±0.25mm,機加工後表面不平度能達到±0.025mm(博格板製造實例),無需熱較正,無熱應力使軌道板製品不會產生內部裂紋。
③模具壽命長,可重複使用1200次。
6.密封好 不漏漿 每個活動部件上均設有密封條,密封嚴實,防止漏漿,密封膠條全部原裝進口。
7.附著式振搗器 振搗均實 採用側振式,能節省振搗器數量,振搗器採用專用振搗器,在研製過程中,根據不同的工況要求,設計最佳的振搗器。這種振搗方式,把工人從人工插入棒針對這種危險繁重質量不穩定的落後方式中解放出來。
自動化程度高 技術先進 國際一流 勞動強度低,長期不需要大修,運營成本低。
8. 採用日本原裝進口振動橡膠墊
橡膠墊內有許多孔,振動時更有彈性,充分實現整體振動平台的效果.
9. 嚴格的工藝流程
本模具特點
1.側模和端模採用抽拉方式,開合僅需2人,快捷方便。
2.側模、端模同底模;芯模和底模之間均採用定位銷,以保證軌道板製品的精度。
3.模具採用固定卡進行固定,快捷方便。
4.模板中心線及軌道中心線均採用暗線,不影響軌道板製品的精度。
5.軌道預埋件定位銷採用固定式(德國博格板式),軌道板起吊後,定位銷留在模具上。省時省力且安全性能高,不用人站在軌道板下面再起出定位銷。
6.根據振搗器振動力的傳遞方式設計模具,使振動力傳遞通暢且振搗均勻。本模具採用側振式,能節省振搗器數量。
7.本模具的側模、底模、端模全部採用數控工具機加工,加工精度高。
8.如有預應力軌道板,本公司將設計製造出非預應力和預應力兼用的軌道板模具。
9.振搗器採用專用振搗器,在研製過程中,根據不同的工況要求,設計最佳的振搗器。
博格式軌道板模板研製報告
京津城際軌道交通工程,是我國引進博格式無碴軌道技術建設的第一條時速350/h的高速鐵路。軌道板模型是軌道板製造生產的關鍵工裝設備,用於軌道板生產中混凝土灌注成型,它在保證軌道板外觀質量、尺寸精度和鋼筋絲位、預埋件位置精度及混凝土密實度等內在質量方面起著決定性或重要作用。
博格式無砟軌道板模型的總體結構
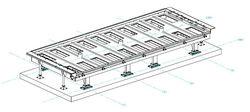
博格式無砟軌道板模板輪廓尺寸為:長*寬*深=6950*2590*861;內腔尺寸:長*寬*深=6450*2550*200。每套模板設有變頻振動器若干(原設計5台)、20個承軌台殼體、9根三角壓條、8條支腿及彈性支座、一根梯形擋板和一根梯形擋板固定用拉桿。每套模板承軌台殼體數量:20件,分兩列,每列10件;每承軌台殼體定位孔數量及孔徑:2-φ10 mm,每套模板承軌台殼體定位孔數量:40個(φ10mm),分4列,每列10個;
主要技術要求
模板輪廓尺寸為:長*寬*深=6950mm*2590mm*861mm;
模板內腔尺寸:長*寬*深=6450mm *2550mm *200mm;
模板底板上平面平面度:誤差≤2 mm;
模板內腔未注公差尺寸精度:誤差≤1.5 mm;
承軌台殼體定位孔孔距精度:誤差≤0.2 mm;
承軌台殼體安裝平面度:誤差≤0.15mm;
軌台殼體未注尺寸(形位)公差各部技術要求:精度誤差≤0.5mm;各曲面過渡圓滑,無明顯稜角、突起、褶皺;無劃痕、裂紋;
每模板20件承軌台殼體安裝平面機加工後平面度:誤差≤0.2 mm;
每模板20件承軌台殼體安裝後平面平面:誤差≤0.3 mm;
每列承軌台殼體定位孔直線度:誤差≤0.2 mm;
四列承軌台殼體定位孔中心線平行度:誤差≤0.3 mm;
每列承軌台殼體安裝後直線度:誤差≤0.2 mm;
兩列承軌台殼體安裝後中心線平行度:誤差≤0.3 mm;
每列尼龍套管定位裝置中心線直線度:誤差≤0.2 mm;
四列尼龍套管定位裝置中心線平行度:誤差≤0.3 mm;
三角壓條表面光潔度:6.3 μm;
三角壓條直線度:誤差≤1 mm;
三角壓條安裝孔距精度:誤差≤0.5 mm;
上擋板縱、側向直線度:誤差≤1.5 mm;
上擋板預應力鋼筋定位孔距精度:誤差≤0.5 mm;
上擋板預應力鋼筋定位孔與板縱、側向垂直度:誤差≤0.3 mm;
上擋板拉桿掛板間距尺寸公差:≤1 mm;
上擋板拉桿掛板孔位尺寸公差:≤0.5 mm;
下擋板縱、側向直線度:誤差≤1 mm;
下擋板預應力鋼筋定位孔距精度:誤差≤0.5 mm;
支座彈性體硬度:邵氏硬度58-60度;符合設計給定的應力應變曲線。
主要技術難點
十多家鋼結構專業生產廠家先後歷時三個月、千方百計想盡辦法加工出來的模板,經博格公司專家檢測無一合格,全部予以否定。它比常規混凝土構件模板的加工精度、製造難度高得多。模板主體結構、承軌台殼體、梯形擋板、三角壓條、彈性支座等,都是技術難度很高的科研課題。在這一點上,我們的認識初期並不充足,而是在研製過程中隨著工作進展和技術難點、要點的一個個暴露,一個個解決而逐漸深入和不斷提高的。
1、模型主體結構部分,其難點在整體平面度的控制、20個承軌台模型安裝面平面工的控制、20個承軌台模型的定位孔位置工控制;
2、承軌台模型部分,其難點在於選擇適宜的金屬材料、選擇合適的設備、製造合適的模具、合適的壓制工藝、檢測手段的工具;
3、上檔板的製做其難點在於軌道生產線為預應力長線台座法布置,每個上檔板上有6個預應力鋼筋定位槽,一條生產線上有27套模型、有54塊檔板,必須保證每個定位槽在一條直線上;
4、三角壓條,其難度在於數量大,採用機加工的方法速度太慢、成本太高,採用熱撥壓制進行加工;
研發的技術路線
博格式軌道板模型組成複雜、技術要求高、製造精度要求高,其質量控制的好壞直接對軌道板的生產質量、數控磨床的打磨進度產生影響,是極為複雜的系統中的一個關鍵子系統。經認真分析研究,制定了如下研究路線:
1、認真對博格公司專家進行學習,理解、領會德國專家對模型各編細部設計的意義和目的,對各部製造精度要求的依據和原因,不放過任何一個小的環節。
2、根據模型的組成和相互關係情況,先對模型進行大的條塊分割,從而找出保證模型質量的各個關鍵環節,分別進行專項攻關。根據對模型的條塊分割,對各條塊進行細部分析,找出保證各主要部分質量的控制要點。
3、根據中國國家標準,對博格公司提供模型圖進行重新設計,主要原材料國內選擇,以國內相近且主要性能指標不低於原使用材料;局部最佳化設計,
4、採用專業協作與自主研發相結合的方式,聯合國內外專業技術單位聯合進行研製。
5、先保證製造精度,再進行、對模型進行堆沙震動試驗,確定電機數量。
模型加工工藝制定
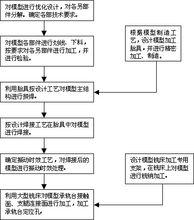
根據對模型加工進行分析,確定了模型製造總的加工工藝過程,方框圖如下:
關鍵部件的製造工藝
模板主體結構拼焊
模板主體是鋼結構組件,每件模板由27件事先加工成型後的型鋼和鋼板再焊接而成。為保證模板長期使用中,能夠經受混凝土灌注成型時劇烈振動的嚴酷作業要求,德方設計焊逢厚且長且模板各部尺寸精度及批量產品的互換性要求非常高,超出一般鋼結構產品精度要求,使得模板主體焊接變形很難控制。如底板,材料為厚度10mmQ235鋼板,焊後6450mm*2550mm範圍內平面度精度要求2mm,常規焊接工藝方法難以保證。
在認真分析失敗教訓基礎上,川榮重工日本工程技術人員經過反覆研究,在徵得博格公司認可後,對軌道板模板原設計進行最佳化,將兩模板側邊板下方各增加一水平筋板,適當加強了模板垂向剛度;借鑑隧道管片模具製作方法,自行設計並採用了博格式軌道板模板拼焊專用胎具(見模板拼焊專用胎具示意圖);實施軌道板模板拼;摸索並制定出整體振動時效方案和最佳變頻振動時效工藝(振動頻率、振動幅度、振動時間匹配控制程式)。成功地解決了軌道板模板焊接變形控制問題。套用此工裝及加工方法拼焊成型的軌道板模板比德國博格公司模板的質量(各部尺寸精度及批量產品的一致互換性)還要高出很多。
利用大型數控銑床對模型進行加工,確保20個與承軌台成型殼體接觸面的平面誤在0.20mm以內,需設計專門的模架來固定待加工的模板主體加工。
承軌台安裝平面及定位孔加工
為保證模板精度要求,每件模板上的20個承軌台安裝平面和40個安裝定位孔,首先必須選用加工範圍不小於6500*2500的大型數控加工工具機進行,以保證在一次裝卡下加工完成。其次,要選擇低磨耗、高耐用度、高精度等級的合金加工刀具。加工過程中要經常檢測刀具磨耗情況,刀具磨耗到一定程度時應及時更換——但更換要儘量避免在加工過程之中進行。如非在加工過程之中更換不可時,則該模板機械加工工作需重新從頭做起。
由於模板是一種板式結構,面積大、豎向剛度低,必須設計適用的、具有足夠剛度的、可以防止工具機進行切削加工時切削力使工件變形造成加工精度損失、裝卡牢靠而又不致因裝卡使模板產生變形的專用工裝。我們設計的機械加工專用裝卡工裝採用了20點定靠、8處測力絲槓框架式結構,配合以3m大型鑄鐵彎板一併使用,效果很好。
為保證承軌台安裝平面及定位孔機械加工精度不損失,不能在機械加工後再對模板主體進行任何熱加工;吊運及碼放時須防止模板主體水平方向受力不均,產生變形。
上擋板製作
上擋板是一種上底寬60mm,下底寬50mm,高96mm梯形截面、長6449mm拼焊成型後進行機械加工的細長桿件。德國原設計每件上擋板需要用71個零件組裝拼焊成型。由於零件眾多,組裝、拼焊時各零件定位精度很難保證。經博格公司認可同意,我們對原圖紙進行了最佳化設計,在保證使用功能和外觀尺寸不變的前提下,大大減少了零件數量,增加了工件的整體性,降低了組裝、拼焊時各零件定位精度的保證難度。
由於工件細長比大,縱、側向剛度很低,因此,下料、拼焊及加工過程中的工件變形非常難以控制。為保證上擋板製作精度,我們逐漸在下料、拼焊、消除焊接應力、機械加工各工序環節摸索出如下有效控制措施:
a.各主要工件採用等離子切割方法下料。
b.設計製作了上擋板專用組裝拼焊胎、卡具進行組裝拼焊。
c.制定出嚴格精細、科學合理的焊接工藝方法,並嚴格貫徹執行。
d.採用人工整體時效方法在上擋板組裝拼焊後、胎卡具放鬆之前對工件進行嚴格的時效處理。
f.精確下料、精確組裝拼焊、有效減少焊接變形,減少了機械加工的加工餘量,再採用半自由裝卡狀態下進行機械加工,防止加工變形。
三角壓條製作
每套模板設9根三角壓條,其作用是為了軌道板預裂縫成型。三角壓條實際形狀為長2.5m;截面為頂寬4mm、底寬28mm、高38mm的等腰梯形;兩端為與底邊呈28°角的斜面;底面有9個φ10mm的裝配用螺栓孔。三角壓條所有表面光潔度要求6.3μmm,直線度誤差≤1 mm;材質Q235。
如用常規銑、刨等機械加工方法製作,不僅加工時間長、費用高,材料浪費大,而且由於切削量大,切削熱使工件產生變形,很難保證工件直線度要求,成品率很低 。我們經過幾十次反覆實驗,採用冷拔成型方法很好的解決了這個問題。
變頻振動電機選型、布置與控制方式
博格式軌道板是採用在模板設定附著式變頻振動電機使混凝土振動成型的。振動電機激振力大小、振動頻率高低、振動電機設定的數量多少、在模板各處位置設定的不同,對混凝土成型的密實程度、氣泡多少、振實效率高低及最終混凝土產品質量具有重要影響。
由於對模型按國內標準進行了重新設計,模型的重量、剛度等與博格公司原設計均有變化,經採用多次堆砂震動試驗,確定每套模板設定震動電機數量、位置,最終確定每套模型設9隻ZKF150型高頻快裝附著式振動電機,其參數為:功率1.5Kw、振幅1.3mm、激振力9KN、變頻範圍50-150Hz、電源240V。
我們實施的振動電機控制方式為:將每條生產線27套模板的變頻振動電機的控制電路組成一個網路、共用一條電源線路和一台變頻器。在每套模板一側池壁上安裝滑觸線,將控制按扭設定在混凝土澆注設備操作檯面上,由混凝土澆注操作人員進行控制。克服了博格公司的每9套模板為一組,每組模板各振動電機各自配備一台變頻器耦合在一起,由一套控制裝置進行操作的控制方式帶來的投資大、控制單元和控制線路過多,維修、操作困難等問題。
使用情況
現在,德國博格板模具承擔的京津城際鐵道工程軌道板預製任務已順利完成。經過一年生產實用檢驗,研製的模板生產出的軌道板外觀尺寸準確,成型漂亮,混凝土密實氣孔少,內在質量好。模板自身耐用、無故障,至今狀態完好。
由於在軌道板模板研製過程中,不是簡單地照圖施工,而是在認真學習、消化、吸收的基礎上對原設計進行了較大的最佳化、改進;採用或創新了大量新技術、新工藝,不僅使模板質量得到充分保證,製造成本也降低了近30%,創造出巨大的經濟效益。
通過此次軌道板模板研製過程,使我們深入掌握了博格式軌道板模具的製造技術;全面領會了德國先進的混凝土模板設計思路、開闊了視野;提升了國內製造大型、複雜模型的能力,為其它類型板式無碴軌道模型的製做打下了堅實的基礎。