介紹
依據所用塗料的種類而有不同的稱呼,如底漆的塗層稱為底漆層,面漆的塗層稱為面漆層。一般塗料所得塗層較薄,約在20~50微米,厚漿型塗料則一次可得厚達1毫米以上的塗層。
是為了防護,絕緣,裝飾等目的,塗布於金屬,織物,塑膠等基體上的塑膠薄層。
高溫電絕緣塗層
用銅、鋁等金屬做成的導線外面,或有絕緣漆、或有塑膠、橡膠等絕緣包皮。然而,絕緣漆、塑膠、橡膠都怕高溫,一般超過200℃就會集化,失去絕緣性能。而許多電線正需要在高溫下工作,那該怎么辦呢?對,讓高溫電絕緣塗層來幫忙,這種塗層實際上是一種陶瓷塗層,它除了能在高溫下保持電絕緣性能外,還能與金屬導線緊密“團結”在一起,做到“天衣無縫”,任你將導線七繞八彎,它們也不會分離,這種塗層非常緻密,塗上它,兩根電壓差很大的導線碰在一起,也不會發生擊穿現象。
高溫電絕緣塗層根據其化學成分的不同,可分為許多種類。如石墨導體表面上的氮化硼或氧化鋁、氟化銅塗層,到400℃仍有良好的電絕緣性能。金屬導線上的搪瓷到700℃,磷酸鹽為基的無機粘結劑塗層到1000℃,等離子噴塗氧化鋁塗層在1300℃,都仍保持著良好的電絕緣性能。
高溫電絕緣塗層已在電力、電機、電器、電子、航空、原子能、空間技術等方面獲得了廣泛的套用。
分類
依據美國F.N.LONGO對熱噴塗塗層的分類方法,塗層按功能可分為:
1、耐磨損塗層
包括抗粘著磨損、表面疲勞磨損塗層和耐沖蝕塗層。其中有些情況還有抗低溫(<538℃)磨損和抗高溫(538~843℃)磨損塗層之分。
2、耐熱抗氧化塗層
該種塗層包括高溫過程(其中有氧化氣氛、腐蝕性氣體、高於843℃的沖蝕及熱障)和熔融金屬過程(其中有熔融鋅、熔融鋁、熔融鐵和鋼、熔融銅)所套用的塗層。
3、抗大氣和浸漬腐蝕塗層
大氣腐蝕包括工業氣氛、鹽性氣氛、田野氣氛等造成的腐蝕;浸漬腐蝕包括飲用淡水、非飲用淡水、熱淡水、鹽水、化學和食品加工等造成的腐蝕。
4、電導和電阻塗層
該種塗層用於電導、電阻和禁止。
5、恢復尺寸塗層
該種塗層用於鐵基(可切削與可磨削的碳鋼和耐蝕鋼)和有色金屬(鎳、鈷、銅、鋁、鈦及他們的合金)製品。
6、機械部件間隙控制塗層
該種塗層可磨。
7、耐化學腐蝕塗層
化學腐蝕包括各種酸、鹼、鹽,各種無機物和各種有機化學介質的腐蝕。
上述各塗層功能中,與冶金工業生產有密切關係的是耐磨損塗層、耐熱抗氧化塗層和耐化學腐蝕塗層。
套用
蒙皮塗層
能防護鋁合金不受高速飛行時風沙和雨水沖蝕,不受海水和航空燃料的腐蝕並能改善空氣動力學性能。塗層應經得住 200°C左右瞬間溫度變化和強烈的日光輻照。飛機體積很大,烘烤條件受到限制,必須選用自乾固化塗料,如丙烯酸或聚氨酯塗料。
發動機塗層
整台發動機,從風扇到尾噴管的主要部件無不使用塗層。發動機塗層按用途分為抗氧化耐腐蝕塗層、隔熱塗層、耐磨塗層和封嚴塗層。
①抗氧化耐腐蝕塗層:早期發動機因工作時間短而高溫合金又含有足夠的鉻、本身能抗氧化,所以不施加塗層。然而,隨著發動機壽命的延長和溫度的提高,以及高溫鎳基合金中鉻含量降到原有的50%,已不能抵抗高溫氧化和熱腐蝕,需要塗層防護。高溫氧化和熱腐蝕是渦輪葉片損壞的主要原因,可使工作壽命縮短到300小時。塗復塗層後高溫部件工作壽命可延長2~3倍。壓氣機轉子和靜子葉片使用含鋁磷(鉻)酸鹽塗層保護。燃燒室既可使用高溫搪瓷又可塗復含鋁磷(鉻)酸鹽塗層。渦輪轉子和靜子葉片多用加有鉻、鈦、矽、釔等改性元素的鋁化物擴散塗層或擴散障塗層。加力燃燒室使用高溫搪瓷或陶瓷塗層。 發展中的金屬-鉻-鋁-釔包復塗層的使用壽命比擴散塗層增加一倍以上,使用溫度達1100°C。這種塗層常與氧化鋯基隔熱塗層組合使用,可降低溫度50~100°C。
②耐磨塗層:影響發動機壽命的另一個因素是高溫磨損,包括撞擊磨損和微振磨損。爆炸噴塗或等離子噴塗碳化鎢-鈷、碳化鉻-鎳鉻塗層最為有效。塗復後,零件的耐磨損壽命可延長7~100倍,已在大型運輸機的發動機上廣泛使用。
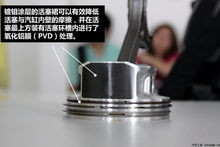
③封嚴塗層:塗復在發動機氣流通道的間隙部分。渦輪的徑向間隙每增大0.13毫米,發動機單位耗油量約增加0.5%;反之,減少0.25毫米,渦輪效率提高1%。另外,減少壓氣機的徑向間隙還可以提高發動機的抗喘振能力,從而改善飛行安全性。常用的封嚴塗層要求硬度適中,既有強度又便於刮削。滑石粉塗層和鎳-石墨塗層已獲套用。正在研製中的氧化鋯塗層能承受1300°C的高溫。
溫控塗層
太空飛行器在太空的熱環境十分惡劣,背陽面溫度可達-100°C,向陽面可達+120°C左右。為保證航天員的生命安全和儀器設備的正常運轉,在太空飛行器表面塗敷溫控塗層可以平衡與空間的熱交換,維持艙內的正常溫度。已經獲得套用的溫控塗層有有機矽氧化鋅、矽酸鉀氧化鋯和氧化鋁塗層。
火箭發動機塗層
液體火箭發動機一般採用再生冷卻,不需要塗層保護,但有時為了增加溫降,在燃燒室內壁噴塗氧化鋁或氧化鋯隔熱塗層。姿態控制火箭發動機多使用鈮、鉬等難熔合金,必須有防氧化塗層的保護才能工作。“阿波羅”號飛船指揮艙和登月艙的姿態控制火箭採用塗有二硫化鉬塗層的小型鉬合金髮動機。
偽裝塗層
用以隱蔽軍事目標。現代偵察儀器探測能力已大大提高,偽裝塗料不僅要求顏色和外形與背景協調,而且要有與背景接近的光譜反射性能。偽裝塗層按適用的波段分為:反紫外、反可見光、反近紅外、反中紅外、反無線電波以及發展中的反多光譜照相偽裝塗料。飛行器可用單色保護迷彩偽裝,為使輪廓在複雜背景地區更難辨別,常採用變形迷彩。
紡織塗層
是一種均勻塗布於織物表面的高分子類化合物。它通過粘合作用在織物表面形成一層或多層薄膜,不僅能改善織物的外觀和風格,而且能增加織物的功能,使織物具有防水,耐水壓,通氣透濕,阻燃防污以及遮光反射等特殊功能。
硬質合金塗層
在切削加工中,刀具性能對切削加工的效率、精度、表面質量有著決定性的影響。硬質合金刀具性能的兩個關鍵指標—硬度和強度之間總存著矛盾,硬度高的材料強度低,而提高強度往往是以硬度的降低為代價。為了解決硬質合金材料中存在的這種矛盾,更好地提高刀具的切削性能,比較有效的一種方法是採用各種塗層技術在硬質合金基體上塗復上一層或多層高硬度、高耐磨損性能的材料。硬質合金刀具表面上的塗層作為一個化學屏障和熱屏障,減少了硬質合金刀具的月牙窪磨損,可以顯著地提高加工效率、提高加工精度、延長刀具使用壽命、降低加工成本。
塗層的特點是塗層薄膜與刀具基體相結合,提高刀具的耐磨性而不降低基體的韌性,從而降低刀具與工件的摩擦因素,延長刀具的使用壽命。此外,由於塗層自身的熱傳導係數比刀具基體和加工材料低的多,能有效減少摩擦所產生的熱量,形成熱屏障,改變熱量的散失途徑,從而降低刀具與工件、刀具與切削之間的熱衝擊和力衝擊,有效地改善刀具的使用性能。刀具磨損機理研究表明,在高速切削時,刀刃溫度最高可達900℃,此時刀具磨損不僅是機械摩擦磨損(刀具後面磨損),還有粘結磨損、擴散磨損、摩擦氧化磨損(刀具刀刃磨損及月牙窪磨損)和疲勞磨損,這5種磨損直接影響刀具的使用壽命。
刀具塗層
刀具塗層技術通常可分為化學氣相沉積(CVD)技術和物理氣相沉積(PVD)技術兩大類,分別評述如下。
一、CVD技術的發展
二十世紀六十年代以來,CVD技術被廣泛套用於硬質合金可轉位刀具的表面處理。由於CVD工藝氣相沉積所需金屬源的製備相對容易,可實現TiN、TiC、TiCN、TiBN、TiB2、Al2O3等單層及多元多層複合塗層的沉積,塗層與基體結合強度較高,薄膜厚度可達7~9μm,因此到八十年代中後期,美國已有85%的硬質合金工具採用了表面塗層處理,其中CVD塗層占到99%;到九十年代中期,CVD塗層硬質合金刀片在塗層硬質合金刀具中仍占80%以上。
儘管CVD塗層具有很好的耐磨性,但CVD工藝亦有其先天缺陷:一是工藝處理溫度高,易造成刀具材料抗彎強度下降;二是薄膜內部呈拉應力狀態,易導致刀具使用時產生微裂紋;三是CVD工藝排放的廢氣、廢液會造成較大環境污染,與目前大力提倡的綠色製造觀念相牴觸,因此自九十年代中期以來,高溫CVD技術的發展和套用受到一定製約。
八十年代末,Krupp.Widia開發的低溫化學氣相沉積(PCVD)技術達到了實用水平,其工藝處理溫度已降至450~650℃,有效抑制了η相的產生,可用於螺紋刀具、銑刀、模具的TiN、TiCN、TiC等塗層,但迄今為止,PCVD工藝在刀具塗層領域的套用並不廣泛。九十年代中期,中溫化學氣相沉積(MT-CVD)新技術的出現使CVD技術發生了革命性變革。MT-CVD技術是以含C/N的有機物乙腈(CH3CN)作為主要反應氣體、與TiCL4、H2、N2在700~900℃下產生分解、化學反應生成TiCN的新工藝。採用MT-CVD技術可獲得緻密纖維狀結晶形態的塗層,塗層厚度可達8~10μm。這種塗層結構具有極高的耐磨性、抗熱震性及韌性,並可通過高溫化學氣相沉積(HT-CVD)工藝在刀片表面沉積Al2O3、TiN等抗高溫氧化性能好、與被加工材料親和力小、自潤滑性能好的材料。MT-CVD塗層刀片適於在高速、高溫、大負荷、乾式切削條件下使用,其壽命可比普通塗層刀片提高一倍左右。目前,CVD(包括MT-CVD)技術主要用於硬質合金車削類刀具的表面塗層,塗層刀具適用於中型、重型切削的高速粗加工及半精加工。採用CVD技術還可實現α-Al2O3塗層,這是PVD技術目前難以實現的,因此在乾式切削加工中,CVD塗層技術仍占有極為重要的地位。
二、PVD技術的發展
PVD技術出現於二十世紀七十年代末,由於其工藝處理溫度可控制在500℃以下,因此可作為最終處理工藝用於高速鋼類刀具的塗層。由於採用PVD工藝可大幅度提高高速鋼刀具的切削性能,所以該技術自八十年代以來得到了迅速推廣,至八十年代末,工業已開發國家高速鋼複雜刀具的PVD塗層比例已超過60%。
PVD技術在高速鋼刀具領域的成功套用引起了世界各國製造業的高度重視,人們在競相開發高性能、高可靠性塗層設備的同時,也對其套用領域的擴展尤其是在硬質合金、陶瓷類刀具中的套用進行了更加深入的研究。研究結果表明:與CVD工藝相比,PVD工藝處理溫度低,在600℃以下時對刀具材料的抗彎強度無影響;薄膜內部應力狀態為壓應力,更適於對硬質合金精密複雜刀具的塗層;PVD工藝對環境無不利影響,符合現代綠色製造的發展方向。隨著高速切削加工時代的到來,高速鋼刀具套用比例逐漸下降、硬質合金刀具和陶瓷刀具套用比例上升已成必然趨勢,因此,工業已開發國家自九十年代初就開始致力於硬質合金刀具PVD塗層技術的研究,至九十年代中期取得了突破性進展,PVD塗層技術已普遍套用於硬質合金立銑刀、鑽頭、階梯鑽、油孔鑽、鉸刀、絲錐、可轉位銑刀片、異形刀具、焊接刀具等的塗層處理。