簡介
塑膠成型是將各種形態(粉料、粒料、溶液和分散體)的塑膠製成所需形狀的製品或坯件的過程。成型的方法多達三十幾種。它的選擇主要決定於塑膠的類型(熱塑性還是熱固性)、起始形態以及製品的外形和尺寸。加工熱塑性塑膠常用的方法有擠出、注射成型、壓延、吹塑和熱成型等,加工熱固性塑膠一般採用模壓、傳遞模塑,也用注射成型。層壓、模壓和熱成型是使塑膠在平面上成型。上述塑膠加工的方法,均可用於橡膠加工。此外,還有以液態單體或聚合物為原料的澆鑄等。在這些方法中,以擠出和注射成型用得最多,也是最基本的成型方法。
工藝特性
收 縮 率
塑件自模具中取出冷卻到室溫後,發生尺寸收縮這種性能稱為收縮性。由於收縮不僅是樹脂本身的熱脹冷縮,而且還與各成形因素有關,所以成形後塑件的收縮應稱為成形收縮。
1、成形收縮的形式成形收縮主要表現在下列幾方面:
(1)塑件的線尺寸收縮由於熱脹冷縮,塑件脫模時的彈性恢復、塑性變形等原因導致塑件脫模冷卻到室溫後其尺寸縮小,為此型腔設計時必須考慮予以補償。
(2)收縮方向性成形時分子按方向排列,使塑件呈現各向異性,沿料流方向(即平行方向)則收縮大、強度高,與料流直角方向(即垂直方向)則收縮小、強度低。另外,成形時由於塑件各部位密度及填料分布不勻,故使收縮也不勻。產生收縮差使塑件易發生翹曲、變形、裂紋,尤其在擠塑及注射成形時則方向性更為明顯。因此,模具設計時應考慮收縮方向性按塑件形狀、流料方向選取收縮率為宜。
(3)後收縮塑件成形時,由於受成形壓力、剪下應力、各向異性、密度不勻、填料分布不勻、模溫不勻、硬化不勻、塑性變形等因素的影響,引起一系列應力的作用,在粘流態時不能全部消失,故塑件在應力狀態下成形時存在殘餘應力。當脫模後由於應力趨向平衡及貯存條件的影響,使殘餘應力發生變化而使塑件發生再收縮稱為後收縮。一般塑件在脫模後10小時內變化最大,24小時後基本定型,但最後穩定要經30-60天。通常熱塑性塑膠的後收縮比熱固性大,擠塑及注射成形的比壓塑成形的大。
(4)後處理收縮有時塑件按性能及工藝要求,成形後需進行熱處理,處理後也會導致塑件尺寸發生變化。故模具設計時對高精度塑件則應考慮後收縮及後處理收縮的誤差並予以補償。
2、收縮率計算塑件成形收縮可用收縮率來表示,如公式(1-1)及公式(1-2)所示。
(1-1)Q實=(a-b)/b×100
(1-2)Q計=(c-b)/b×100
式中:Q實—實際收縮率(%)
Q計—計算收縮率(%)
a—塑件在成形溫度時單向尺寸(mm)
b—塑件在室溫下單向尺寸(mm)
c—模具在室溫下單向尺寸(mm)
實際收縮率為表示塑件實際所發生的收縮,因其值與計算收縮相差很小,所以模具設計時以Q計為設計參數來計算型腔及型芯尺寸。
3、影響收縮率變化的因素在實際成形時不僅不同品種塑膠其收縮率各不相同,而且不同批的同品種塑膠或同一塑件的不同部位其收縮值也經常不同,影響收縮率變化的主要因素有如下幾個方面。
(1)塑膠品種各種塑膠都有其各自的收縮範圍,同種類塑膠由於填料、分子量及配比等不同,則其收縮率及各向異性也不同。
(2)塑件特性塑件的形狀、尺寸、壁厚、有無嵌件,嵌件數量及布局對收縮率大小也有很大影響。
(3)模具結構模具的分型面及加壓方向,澆注系統的形式,布局及尺寸對收縮率及方向性影響也較大,尤其在擠塑及注射成形時更為明顯。
(4)成形工藝擠塑、注射成形工藝一般收縮率較大,方向性明顯。預熱情況、成形溫度、成形壓力、保持時間、填裝料形式及硬化均勻性對收縮率及方向性都有影響。
如上所述模具設計時應根據各種塑膠的說明書中所提供的收縮率範圍,並按塑件形狀、尺寸、壁厚、有無嵌件情況、分型面及加壓成形方向、模具結構及進料口形式尺寸和位置、成形工藝等諸因素綜合地來考慮選取收縮率值。對擠塑或注射成形時,則常需按塑件各部位的形狀、尺寸、壁厚等特點選取不同的收縮率。
另外,成形收縮還受到各成形因素的影響,但主要決定於塑膠品種、塑件形狀及尺寸。所以成形時調整各項成形條件也能夠適當地改變塑件的收縮情況。
流動性
塑膠在一定溫度與壓力下填充型腔的能力稱為流動性。這是模具設計時必須考慮的一個重要工藝參數。流動性大易造成溢料過多,填充型腔不密實,塑件組織疏鬆,樹脂、填料分頭聚積,易粘模、脫模及清理困難,硬化過早等弊病。但流動性小則填充不足,不易成形,成形壓力大。所以選用塑膠的流動性必須與塑件要求、成形工藝及成形條件相適應。模具設計時應根據流動性能來考慮澆注系統、分型面及進料方向等等。熱固性塑膠流動性通常以拉西格流動性(以毫米計)來表示。數值大則流動性好,每一品種的塑膠通常分三個不同等級的流動性,以供不同塑件及成形工藝選用。一般塑件面積大、嵌件多、型芯及嵌件細弱,有狹窄深槽及薄壁的複雜形狀對填充不利時,應採用流動性較好的塑膠。擠塑成形時應選用拉西格流動性150mm以上的塑膠,注射成形時套用拉西格流動性200mm以上的塑膠。為了保證每批塑膠都有相同的流動性,在實際中常用並批方法來調節,即將同一品種而流動性有差異的塑膠加以配用,使各批塑膠流動性互相補償,以保證塑件質量。常用塑膠的拉西格流動性值詳見表1-1,但必須指出塑膠的流動性除了決定於塑膠品種外,在填充型腔時還常受各種因素的影響而使塑膠實際填充型腔的能力發生變化。如粒度細勻(尤其是圓狀粒料),濕度大、含水分及揮發物多,預熱及成形條件適當,模具表面光潔度好,模具結構適當等則都有利於改善流動性。反之,預熱或成形條件不良、模具結構不良流動阻力大或塑膠貯存期過長、超期、貯存溫度高(尤其對氨基塑膠)等則都會導致塑膠填充型腔時實際的流動性能下降而造成填充不良。
比容及壓縮率
比容為每一克塑膠所占有的體積(以厘米3/克計)。壓縮率為塑粉與塑件兩者體積或比容之比值(其值恆大於1)。它們都可被用來確定壓模裝料室的大小。其數值大即要求裝料室體積要大,同時又說明塑粉內充氣多,排氣困難,成形周期長,生產率低。比容小則反之,而且有利於壓錠,壓制。各種塑膠的比容詳見表1-1。但比容值也常因塑膠的粒度大小及顆粒不均勻度而有誤差。
硬化特性
熱固性塑膠在成形過程中在加熱受壓下轉變成可塑性粘流狀態,隨之流動性增大填充型腔,與此同時發生縮合反應,交聯密度不斷增加,流動性迅速下降,融料逐漸固化。模具設計時對硬化速度快,保持流動狀態短的料則應注意便於裝料,裝卸嵌件及選擇合理的成形條件和操作等以免過早硬經或硬化不足,導致塑件成形不良。
硬化速度一般可從保持時間來分析,它與塑膠品種、壁厚、塑件形狀、模溫有關。但還受其它因素而變化,尤其與預熱狀態有關,適當的預熱應保持使塑膠能發揮出最大流動性的條件下,儘量提高其硬化速度,一般預熱溫度高,時間長(在允許範圍內)則硬化速度加快,尤其預壓錠坯料經高頻預熱的則硬化速度顯著加快。另外,成形溫度高、加壓時間長則硬化速度也隨之增加。因此,硬化速度也可調節預熱或成形條件予以適當控制。
硬化速度還應適合成形方法要求,例注射、擠塑成型時應要求在塑化、填充時化學反應慢、硬化慢,應保持較長時間的流動狀態,但當充滿型腔後在高溫、高壓下應快速硬化。
水分及揮發物含量
各種塑膠中含有不同程度的水分、揮發物含量,過多時流動性增大、易溢料、保持時間長、收縮增大,易發生波紋、翹曲等弊病,影響塑件機電性能。但當塑膠過於乾燥時也會導致流動性不良成形困難,所以不同塑膠應按要求進行預熱乾燥,對吸濕性強的料,尤其在潮濕季節即使對預熱後的料也應防止再吸濕。
由於各種塑膠中含有不同成分的水分及揮發物,同時在縮合反應時要發生縮合水分,這些成分都需在成形時變成氣體排出模外,有的氣體對模具有腐蝕作用,對人體也有刺激作用。為此在模具設計時應對各種塑膠此類特性有所了解,並採取相應措施,如預熱、模具鍍鉻,開排氣槽或成形時設排氣工序。
方法
塑膠製品是以合成樹脂和各種添加劑的混合料為原料,採用注射、擠壓、壓制、澆注等方法製成的。塑膠產品在成型的同時,還獲得了最終性能,所以塑膠的成型是生產的關鍵工藝。
注射成形
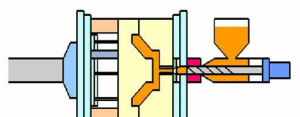
注射成形機常用的有柱塞式和螺桿式兩種,右圖為螺桿式注射成形示意圖。注射成形原理:將粉粒狀原料從料斗加入料筒,柱塞推進時,原料被推入加熱區,繼而經過分流梭,通過噴嘴將熔融塑膠注入模腔中,冷卻後開模即得塑膠製品。注塑膠製件從模腔中取出後通常需進行適當的後處理,以消除塑膠製件在成形時產生的應力、穩定尺寸和性能。此外,還有切除毛邊和澆口、拋光、表面塗飾等。
擠出成形

右圖為螺鏇擠出成形示意圖,粒狀塑膠從料斗送入螺鏇推進室,然後由鏇轉的螺桿送到加熱區熔融,並受到壓縮;在螺鏇力的作用下,迫使其通過具有一定形狀的擠出模具,得到與口模截面形狀相一致的型材;落到輸送機皮帶後用噴射空氣或水使它冷卻變硬得到固化的塑膠製件。
壓製成形
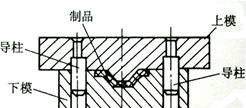
下圖為壓製成形示意圖,一般壓製成形過程可以分為加料、合模、排氣、固化和脫模幾個階段。塑膠製件脫模後應進行後處理,處理方法與注射成形塑膠製件方法相同。
吹塑成形
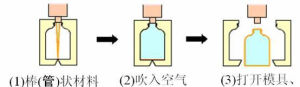
右圖為中空製件的擠吹成形示意圖,將具有一定溫度的擠出或注射的管狀型坯置於對開吹塑模中,合上模具,通過吹管吹入壓縮空氣,將型坯吹脹後使之緊貼模壁,經保壓、冷卻定型後開模取出中空製件。
澆鑄成型
塑膠的澆鑄成形類似於金屬的鑄造成形。即將處於流動狀態的高分子材料或單體材料注入特定的模具中,在一定條件下使之反應、固化,並成形得到與模具形腔相一致的塑膠製件的加工方法。這種成形方法設備簡單,不需或稍許加壓,對模具強度要求低,生產投資少,可適用於各種尺寸的熱塑性和熱固性塑膠製件。但塑膠製件精度低,生產率低,成形周期長。
氣體輔助注塑成形
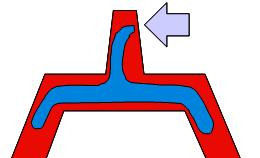
氣輔工藝包括如下四個階段:第一階段,塑膠注射。熔體進入型腔,遇到溫度較低的模壁,形成一個較薄的凝固層;第二階段:氣體入射。惰性氣體進入熔融的塑膠,推動中心未凝固的塑膠進入尚未充滿的型腔;第三階段:氣體入射。氣體繼續推動塑膠熔體流動直到熔體充滿整個型腔;第四階段:氣體保壓。在保壓狀態下,氣道中的氣體壓縮熔體,進行補料確保製件的外觀質量。
氣輔成形具有如下優點:消除產品表面縮痕,改善產品表面質量;減少翹曲變形,減少流動條痕;降低產品內應力,提高產品強度;節省塑膠原料,減輕製品重量(一般可減輕20%-40%);改善材料在制品斷面上的分布,改善製品的剛性;縮短成型時間,提高生產效率;延長模具使用壽命。
使用設備
塑膠成型通常使用注塑機,又名注射成型機或注射機。它是將熱塑性塑膠或熱固性料利用塑膠成型模具製成各種形狀的塑膠製品的主要成型設備。分為立式、臥式、全電式。注塑機能加熱塑膠,對熔融塑膠施加高壓,使其射出而充滿模具型腔。日常塑膠製品一般由注塑機進行注塑成型的。