刻蝕工藝
正文
基本工藝要求 理想的刻蝕工藝必須具有以下特點:①各向異性刻蝕,即只有垂直刻蝕,沒有橫向鑽蝕。這樣才能保證精確地在被刻蝕的薄膜上複製出與抗蝕劑上完全一致的幾何圖形;②良好的刻蝕選擇性,即對作為掩模的抗蝕劑和處於其下的另一層薄膜或材料的刻蝕速率都比被刻蝕薄膜的刻蝕速率小得多,以保證刻蝕過程中抗蝕劑掩蔽的有效性,不致發生因為過刻蝕而損壞薄膜下面的其他材料;③加工批量大,控制容易,成本低,對環境污染少,適用於工業生產。
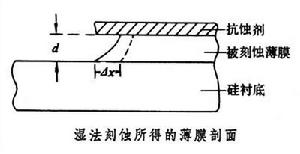
對於採用微米級和亞微米量級線寬的超大規模積體電路,刻蝕方法必須具有較高的各向異性特性,才能保證圖形的精度,但濕法刻蝕不能滿足這一要求。
乾法刻蝕 70年代末研究出一系列所謂乾法刻蝕工藝。乾法刻蝕有離子銑刻蝕、等離子刻蝕和反應離子刻蝕三種主要方法。
① 離子銑刻蝕:低氣壓下惰性氣體輝光放電所產生的離子加速後入射到薄膜表面,裸露的薄膜被濺射而除去。由於刻蝕是純物理作用,各向異性程度很高,可以得到解析度優於 1微米的線條。這種方法已在磁泡存儲器、表面波器件和集成光學器件等製造中得到套用。但是,這種方法的刻蝕選擇性極差,須採用專門的刻蝕終點監測技術,而且刻蝕速率也較低。
② 等離子刻蝕:利用氣壓為10~1000帕的特定氣體(或混合氣體)的輝光放電,產生能與薄膜發生離子化學反應的分子或分子基團,生成的反應產物是揮發性的。它在低氣壓的真空室中被抽走,從而實現刻蝕。通過選擇和控制放電氣體的成分,可以得到較好的刻蝕選擇性和較高的刻蝕速率,但刻蝕精度不高,一般僅用於大於4~5微米線條的工藝中。
③ 反應離子刻蝕:這種刻蝕過程同時兼有物理和化學兩種作用。輝光放電在零點幾到幾十帕的低真空下進行。矽片處於陰極電位,放電時的電位大部分降落在陰極附近。大量帶電粒子受垂直於矽片表面的電場加速,垂直入射到矽片表面上,以較大的動量進行物理刻蝕,同時它們還與薄膜表面發生強烈的化學反應,產生化學刻蝕作用。選擇合適的氣體組分,不僅可以獲得理想的刻蝕選擇性和速度,還可以使活性基團的壽命短,這就有效地抑制了因這些基團在薄膜表面附近的擴散所能造成的側向反應,大大提高了刻蝕的各向異性特性。反應離子刻蝕是超大規模積體電路工藝中很有發展前景的一種刻蝕方法。
現代化的乾法刻蝕設備包括複雜的機械、電氣和真空裝置,同時配有自動化的刻蝕終點檢測和控制裝置。因此這種工藝的設備投資是昂貴的。