簡介
由光管及“附著”在其上的翅片構成的,結構參數主要為翅片管內徑、外徑,翅片管壁厚,翅片節距、翅片厚度及翅片高度等。
低翅片管主要是靠管外肋化 (肋化係數為 2~3 ) 擴大傳熱面積,與光管相比,在消耗金屬材料相同的情況下具有更大的表面積。從直觀看屬於第一次強化傳熱,但實質上是換熱面積增大的同時帶來了傳熱係數的提高,肋片能使傳熱表面剝離流動層,使傳熱表面擾動增加而改善傳熱效果,二次強化了傳熱。影響肋化表面強化傳熱的主 要因素是翅片高度、翅片厚度、翅片片間距以及翅片材料的導熱係數等。此外,由於傳熱壁面的一側被擴展成翅片表面,光滑側的對流換熱、基壁的導熱等對其總傳熱量都產生一定的影響。低翅片管的翅片間距尺寸需要根據液體的表面張力和流動產生的對液膜的剪力來確定 。
實際套用證明低翅片管還具有優良的抗污垢性能,因為污垢往往是沿著波峰邊緣形成平行的垢片,在運行時隨著溫度變化,管子會膨脹和收縮,這種”手風琴“式 的脹縮作用,會阻止污垢生成。而在光管上,污垢將在管子壁面形成一層圓柱體,沒有任何自然機理阻止污垢產生。由於翅片較低,低翅片管的清洗方法及難度與光管完全一 樣。另外,低翅片管是採用普通光管作毛坯,經簡單的滾壓加工而成,其機械強度和耐腐蝕性狀亦不亞於原光管坯,完全可以保證換熱器長期可靠地工作。
性能參數
低翅片管有兩個重要的參數來描述其性能,分別為翅化比 β 和翅片效率η。翅化比用“β”來表示,其定義可由公式引出: β =翅片管總的外表面積/原光管外表面積; β 越大說明翅片管的換熱面積擴大的越厲害,其換熱性能也隨之增強。翅片管在換熱過程中,假設管內流體的溫度高於管外流體的溫度,熱量由管內經管壁從翅片根部沿翅片高度以熱傳導方式向外傳遞,同時翅片還與周圍流體發生對流換熱, 最終使得沿翅高方向翅片溫度逐漸下降,其原理如下圖所示:
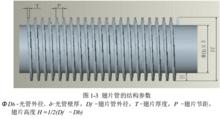
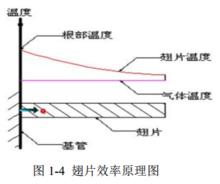
如圖 1-4 所示,沿翅高方向翅片溫度逐漸減小,說明翅片與周圍流體間的溫差在逐漸減小,由對流換熱的熱量公式可知,溫差減小時,翅片單位面積的換熱量也隨之減小。翅片越高,其增加的面積對換熱的強化作用就越小,為此介紹一個新概念——翅片效率 η。
η=Q/Q
式中 Q—翅片表面的實際散熱量; Q—假定翅片表面溫度等於翅根溫度時的理論散熱量。如果翅片效率小於 1,此時增加 1 倍的翅片散熱面積,散熱量卻沒有增加 1 倍,這裡散熱量就打了個“折扣”,此“折扣”就是翅片效率。經驗表明翅片效率受翅片的高度、厚度、形狀等因素影響,其中翅高對其影響最大,翅高越大,翅片效率就越小,由此可見翅片的換熱面積越大,其換熱性能並不是就越理想。
製造工藝
翅片管的加工方法有很多,可通過焊接、套裝、鑲嵌等工藝將翅片"粘接“到基管上,也可通過軋制、滾壓等壓力加工法在光管上加工出翅片來,近年來有學者綜合壓力加工和機械加工的優點創造性的提出了一系列複合加工方法,如夏偉等人提出了“劈切—擠壓”加工方法,吳斌等人提出了“雙面犁法”,李言教授等人提出了“切削—擠壓成形方法”來加工整體翅片管。下面以“劈切—擠壓”法為例,介紹其加工工藝:
劈切—擠壓加工方法 這是一種結合無屑切削與擠壓的複合加工方法,此法是按通常的切削加工方式在普通車床上加工翅片管;在專用刀具將管表面金屬劈切開後,隨著擠壓量的增加,金屬沿徑向和軸向流動,通過徑向和軸向擠壓使金屬塑性變形形成翅片。
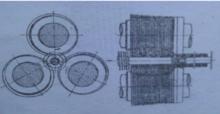
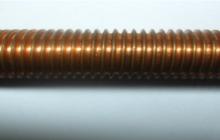
低翅片管則是運用滾軋法(三輥斜軋)加工生產的,其工作原理為:在光管內襯一芯棒,管料在軋輥刀片的帶動下做螺旋直線運動,通過軋輥軋槽與芯棒組成的孔型在其外表面上逐漸加工出翅片。為了更利於翅片成型,軋件在變形過程中採用咬入、輾軋、整形三個階段,使加工出來的翅片完整、光滑、規則,這種方法生產出來的翅片管因基管與外翅片是一個有機的整體,因而沒有接觸熱阻損失和電腐蝕的問題,具有良好的傳熱效率且抗變形能力較強。
強化傳熱
翅片管是以對流換熱的形式進行熱量傳遞的,由對流換熱的數學表達式Q=hAΔT 可知,對流換熱量與換熱面積 A、溫度差△T 及對流換熱係數 h 成正比,擴大換熱面積以提高傳熱量是一有效途徑,但如果只是簡單的增大設備體積來獲得更多的換熱面積,這種方法在工程運用中不可取,實際運用中只能通過最佳化換熱表面的結構,以增大單位體積的換熱面積,從而使換熱器緊湊、高效,現在經常使用翅片管、螺紋管及板翅式換熱面等形式來擴展表面傳熱。當換熱元件確定了,換熱面積 A 及溫差△T 基本都已確定下來,提高換熱量就可通過提升對流換熱係數 h 來實現,在翅片管換熱器穩定運行時,且翅片管壁厚較小的情況下,對流傳熱係數 h 可近似表述為:
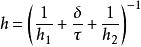
式中: h—管內流體的換熱係數; δ-管壁厚度;h—管外流體的換熱係數; τ-管材的導熱係數。
對於翅片式傳熱管,其管材基本為銅、鋁等導熱係數很大的金屬,且管壁厚度δ 相對而言很小,故右式中的第二項的值很小,可忽略不計,上述的對流傳熱係數可整理簡化為 h=(1/ h+1/ h) ,由此可知若要提高對流換熱係數h ,可通過提升管內及管外的流體換熱係數h、 h,當 h、 h的數值大小相差很大時,總的換熱係數h的值主要取決於較小的那個換熱係數h ,這說明提升更小的那個傳熱係數對翅片管的換熱具有十分明顯的強化作用。
對流換熱係數主要由以下因素決定:一是流體的種類及其物理性質,不同的流體(液體或氣體)其換熱係數相差很大;二是換熱過程中流體是否發生相變,若有相變發生,其換熱係數將會明顯提高;三是流體的流速和換熱表面的形狀。以空氣加熱器為例,管內流通熱水,管外流通空氣,由於管外空氣側的換熱係數遠低於管內水側的換熱係數,這阻礙了水側換熱“能力”的發揮,由此可看出換熱過程的“瓶頸”是在管外空氣側,限制了換熱量的增幅。為克服這種“瓶頸”效應,在空氣側的管外加裝翅片,大幅增加管外換熱面積,以此彌補空氣側換熱係數低的不足,極大提高了換熱量,其原理如圖 1-9 所示:

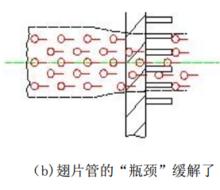
影響因素
結構參數主要為翅片管內徑、外徑,翅片管壁厚,翅片節距、翅片厚度及翅片高度等。
一般用於管內給熱係數比管外給熱係數大1倍以上的場合,最典型的套用場合是油換熱器。對於管外冷凝及沸騰,由於表面張力作用,也有較好的強化傳熱作用困。其加工已工業化,且設計關聯式已於長嶺煉油廠等廠驗證。
(1) 就傳熱效果而言,低翅片管各結構參數對其影響的主次關係為:翅距→翅高→翅厚,且翅距在 1~2 mm 內,翅片管的換熱性能隨翅距的增大而增強,翅距超過 2mm 時,換熱性能隨之增大而減弱;換熱性能隨翅厚增大而減弱,隨翅高的增大而增強。
(2) 翅片管外的壓降受翅高的影響異常顯著,壓降隨翅高的增大呈幾何倍數增長,翅距對壓降的影響也較明顯,壓降隨翅距的增大而變大,壓降幾乎不受翅厚的影響。
(3) 管內外的流體流速增大時,翅片管的換熱量與壓降也隨之增大,管外流體流速增大時,其壓降增幅明顯大於換熱量的增幅,而管內流速增大時,管外壓降不變,管內壓降增幅較小。
研究現狀
許多學者以翅片管外側(即有翅片一側)的換熱跟壓降在不同工況下的性能為切入點,研究了翅片的結構參數對換熱性能的影響;管內外的流體流動狀態對換熱性能的影響;析濕工況下翅片效率的計算方法。
析濕工況下在翅片管換熱器中,當管外來流氣體的露點溫度高於翅片表面溫度時,在翅片表面易析出露水,俗稱結露,此時翅片管換熱器的壓降與換熱特性比干工況的要複雜多,且傳熱過程中伴隨著傳質,空氣流動模式也有了很大的變化,此時從理論方面研究翅片表面的熱質交換非常困難,故一般以實驗研究的形式探究其機理。對平片翅片管在濕工況的研究主要集中在乾、濕翅片效率,翅距對傳質傳熱的影響及入口相對濕度對換熱設備換熱性能的影響這幾方面。國內外學者對此有許多的發現, Wang et al 通過對九個平片換熱器樣本的研究,發現摩擦係數在濕工況下要比在乾工況下的提高 60~120 %,而換熱係數在乾、濕工況下的變化微小, Wang etal 根據多個樣本的實驗數據推算出了換熱器壓降關聯式,並總結出了熱質比擬關係的關聯式。 Pirompugd et al 對平片換熱器樣本的實驗數據處理分析時發現,全濕工況下,換熱效果不受入口相對濕度的影響,因為冷凝水干擾了空氣流場,翅距對換熱性能的影響幾乎可以忽略。北京交通大學的賈力、管鵬等人通過對水平翅片管外冷凝傳熱的可視化研究,對翅片管的對流冷凝換熱機制及翅片管上的液膜理論計算作了探索性的研究。
國內眾多研究者分別從翅片管的用材、翅片的結構外形和管束的排列方式等方面對螺旋翅片管的換熱影響進行研究,以此最佳化翅片管的結構參數及其布置參數。例如曹家甡通過大量實驗確定了尺寸、管束節距均不一樣的錯列整體式螺旋翅片管的阻力和傳熱計算方程式,研究了溫度在翅片上的分布情況及翅頂溫度的計算方法。潘宏偉等運用數值計算的方法計算了管內外壁面的對流換熱係數,得出了以下結論:換熱係數受管外煙氣和管內空氣的流速影響非常顯著,同樣翅片管的外形尺寸對翅片管的溫度分布也有較大影響。 Kuntysh 等人對分別由黃銅、紫銅和鋼製成的五排錯列放置翅片管束進行了傳熱實驗,實驗結果表明:若其它條件不變,三種翅片管束的換熱係數差異很小,因為翅片管的傳熱熱阻主要存在於翅片表面與流體間,其大小由管外流體的流動狀況決定。Brauer 與 Zozulya 等人還研究了翅片管束的布置方式(順列和錯列)對其換熱性能的影響,研究發現布置型式對翅片管的換熱影響很大。結果表明:螺旋翅片管束的換熱性能在錯列布置的情況下要優於順列布置。在傳熱量跟管外壓降相同的情況下,錯列管束的換熱面積可以比順列減小 30%。