概況
並行工程的歷史
它要求產品開發人員從一開始就考慮到產品全生命周期(從概念形成到產品報廢)內各階段的因素(如功能、製造、裝配、作業調度、質量、成本、維護與用戶需求等等),並強調各部門的協同工作,通過建立各決策者之間的有效的信息交流與通訊機制,綜合考慮各相關因素的影響,使後續環節中可能出現的問題在設計的早期階段就被發現,並得到解決,從而使產品在設計階段便具有良好的可製造性、可裝配性、可維護性及回收再生等方面的特性,最大限度地減少設計反覆,縮短設計、生產準備和製造時間。
研究範圍
一般包括:
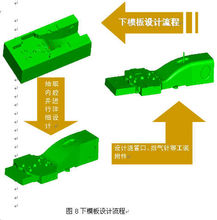
①並行工程管理與過程控制技術,
②並行設計技術,
③快速製造技術。
80年代前,並行工程在中國計畫經濟時代就已經有了很多成功範例,如找石油,核子彈,航天工程等等,並被稱為社會主義優越性的表現之一,只不過當時沒有起名叫並行工程罷了。
並行工程自20世紀80年代提出以來,美國、歐共體和日本等已開發國家均給予了高度重視,成立研究中心,並實施了一系列以並行工程為核心的政府支持計畫。很多大公司,如麥道公司、波音公司、西門子、IBM等也開始了並行工程實踐的嘗試,並取得了良好效果。
進入90年代,並行工程引起中國學術界的高度重視,成為中國製造業和自動化領域的研究熱點,一些研究院、所和高等院校均開始進行一些有針對性的研究工作。1995年“並行工程”正式作為關鍵技術列入863/CIMS研究計畫,有關工業部門設立小型項目資助並行工程技術的預研工作。國內部分企業也開始運用並行工程的思想和方法來縮短產品開發周期、增強競爭能力。但是,無論從技術研究還是企業實踐上,中國都落後於國際先進水平十年左右,許多工作仍處在探索階段。
並行工程的定義
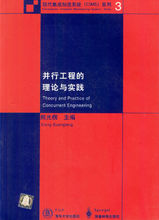
1988年美國國家防禦分析研究所(IDA—Institute of Defense Analyze)完整地提出了並行工程(CE—
Concurrent Engineering)的概念,即“並行工程是集成地、並行地設計產品及其相關過程(包括製造過程和支持過程)的系統方法。這種方法要求產品開發人員在一開始就考慮產品整個生命周期中從概念形成到產品報廢的所有因素,包括質量、成本、進度計畫和用戶要求。並行工程的目標為提高質量、降低成本、縮短產品開發周期和產品上市時間。並行工程的具體做法是:在產品開發初期,組織多種職能協同工作的項目組,使有關人員從一開始就獲得對新產品需求的要求和信息,積極研究涉及本部門的工作業務,並將所需要求提供給設計人員,使許多問題在開發早期就得到解決,從而保證了設計的質量,避免了大量的返工浪費.
-在產品的設計開發期間,將概念設計、結構設計、工藝設計、最終需求等結合起來,保證以最快的速度按要求的質量完成。
-各項工作由與此相關的項目小組完成。進程中小組成員各自安排自身的工作,但可以定期或隨時反饋信息並對出現的問題協調解決。
-依據適當的信息系統工具,反饋與協調整個項目的進行。利用現代CIM技術,在產品的研製與開發期間,輔助項目進程的並行化。
並行工程的特徵
1.並行交叉
它強調產品設計與工藝過程設計、生產技術準備、採購、生產等種種活動並行交叉進行。並行交叉有兩種形式:一是按部件並行交叉,即將一個產品分成若干個部件,使各部件能並行交叉進行設計開發;二是對每單個部件,可以使其設計、工藝過程設計、生產技術準備、採購、生產等各種活動盡最大可能並行交叉進行。需要注意的是,並行工程強調各種活動並行交叉,並不是也不可能違反產品開發過程必要的邏輯順序和規律,不能取消或越過任何一個必經的階段,而是在充分細分各種活動的基礎上,找出各子活動之間的邏輯關係,將可以並行交叉的儘量並行交叉進行。
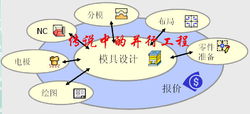
2.儘早開始工作
正因為強調各活動之間的並行交叉,以及並行工程為了爭取時間,所以它強調人們要學會在信息不完備情況下就開始工作。因為根據傳統觀點,人們認為只有等到所有產品設計圖紙全部完成以後才能進行工藝設計工作,所有工藝設計圖完成後才能進行生產技術準備和採購,生產技術準備和採購完成後才能進行生產。正因為並行工程強調將各有關活動細化後進行並行交叉,因此很多工作要在我們傳統上認為信息不完備的情況下進行。
並行工程的特點
群組協同
並行工程中突出了人的因素。現代設計越來越複雜,開發過程涉及的學科門類和專業人員是相當多,如何取得開發過程的整體最優,是並行工程的追求目標,其中的關鍵是如何
更好地發揮掌握現代先進技術的人的群體協作,組成集成產品開發團隊和支持團隊進行協同工作(指計算機系統、各種軟體工具、多媒體手段與設計工具在一起的支
持系統等),把產品開發過程看成一個有機系統,消除串列模式中各部門之間的壁壘,使各部門協調一致,提高團體效益。以網路設計為例,在網路設計過程中,涉
及到設計、套用、數據採集、分析、信息處理、軟硬體套用等多學科、多門類人員,如何最大限度地發揮各類人員的作用,是並行工程在其套用中要解決的最大難
題,套用群組協同是解決該難題的最佳方式。
基於集成製造的並行性
並行工程是針對串列工程而提出的一個新概念,它建立在集成框架之上。套用信息集成、功能集成和過程集成的軟體系統是實施並行工程的基礎。產品數據管理
(PDM)是支持並行工程的一種集成框架,它對產品生命周期的全部信息(時間上有先後的信息)進行管理,實現產品數據的統一管理與共享。它能支持異構的計
算機聯網,在企業範圍內為設計與製造建立一個並行化的產品協作環境,方便實現對其套用工具的封裝,便於有效管理套用工具產生的信息,便於套用系統之間的信
息傳遞與交換,並可提供各系統運行過程的全方位管理與監控。
並行有序
並行工程作為一種方法,旨在產品開發的早期階段就能綜合評估產品全生命周期的各種因素,做出正確決策。並行設計是並行工程主體,它利用計算機仿真技術等系
列工具,對產品開發的全生命周期進行並行而有序的設計,使傳統的在生產製造階段才能發現的問題能夠在設計早期予以修正。
面向工程的設計
面向工程的設計(DFX)是支持設計的工具的總稱,它包括面向裝配的設計、面向質量的設計及面向成本的設計等。其概念覆蓋了產品設計、製造、使用及報廢回
收的整個生命周期。使產品在設計階段就能考慮到生產製造階段的問題。面向工程的設計方法提倡在設計中考慮後續階段的問題,即通過各方面信息綜合,使其“第
一次”就能正確的過程,而不是反覆地大循環地修改,直到正確的過程,因此它是實現並行工程的支持工具。
計算機仿真技術
在並行工程中,計算機仿真占有重要的地位。產品開發中的設計、製造等大多靠計算機仿真來描述、檢驗和驗證,主要是指過程仿真(APS)、加工過程仿真(MPS)及生產計畫調度仿真(PPDS)等。
地位作用
承上啟下的作用
並行工程在先進制造技術中具有承上啟下的作用,這主要體現在兩個方面:
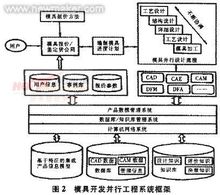
1.並行工程是在CAD、CAM、CAPP等技術支持下,將原來分別進行的工作在時間和空間上交叉、重疊,充分利用了原有技術,並吸收了當前迅速發展的計算機技術、信息技術的優秀成果,使其成為先進制造技術中的基礎。
2.在並行工程中為了達到並行的目的,必須建立高度集成的主模型,通過它來實現不同部門人員的協同工作;為了達到產品的一次設計成功,減少反覆,它在許多部分套用了仿真技術;主模型的建立、局部仿真的套用等都包含在虛擬製造技術中,可以說並行工程的發展為虛擬製造技術的誕生創造了條件,虛擬製造技術將是以並行工程為基礎的,並行工程的進一步發展方向是虛擬製造(VM?/FONT>Virtual Manufacturing)。所謂虛擬製造又叫擬實製造,它利用信息技術、仿真技術、計算機技術對現實製造活動中的人、物、信息及製造過程進行全面的仿真,以發現製造中可能出現的問題,在產品實際生產前就採取預防措施,從而達到產品一次性製造成功,來達到降低成本、縮短產品開發周期,增強產品競爭力的目的
並行工程與面向製造和裝配的產品設計
面向製造和裝配的產品設計(Design for Manufacturing and Assembly,DFMA)是指在產品設計階段充分考慮產品的可製造性和可裝配性,從而以更短的產品開發周期、更低的產品開發成本和更高的產品開發質量進行產品開發。
很顯然,要順利地實施和開展並行工程,離不開面向製造和裝配的產品設計,只有從產品設計入手,才能夠實現並行工程提高質量、降低成本、縮短開發時間的目的。可以說,面向製造和裝配的產品開發是並行工程的核心部分,是並行工程中最關鍵的技術。掌握了面向製造和裝配的產品開發技術,並行工程就成功了一大半。
技術要求
1. 一個完整的公共資料庫,它必須集成並行設計所需要的諸方面的知識、信息和數據,並且以統一的形式加以表達。
2. 一個支持各方面人員並行工作、甚至異地工作的計算機網路系統,它可以實時、線上地在各個設計人員之間溝通信息、發現並調解衝突。
3. 一套切合實際的計算機仿真模型和軟體,它可以由一個設計方案預測、推斷產品的製造及使用過程,發現所隱藏的問題。此問題是實施並行工程的“瓶頸”。
發展套用
國外發展

·1988 年,美國防禦分析研究所以武器生產為背景,對傳統的生產模式進行了分析,首次提出了並行工程的概念。特別是美國國防部高級房屋研究項目局與 1988 年 7 月在西維吉尼亞大學投資 4~5 億美元組建 CERC ,致力於設計、開發和推廣 CE 使能技術,以提高產品的開發能力。
·1986 年 -1992 年,是並行工程的研究與初步嘗試階段。美國國防部支持的 DARPA/DICE 計畫,歐洲的 ESPRIT II&III 計畫,日本的 IMS 計畫等都進行了並行工程的研究。
·1995 年至今是新的發展階段。從理論向實用化方向發展並取得了明顯的成效。
國外套用
並行工程已從理論向實用化方向發展,越來越多的涉及航空、航天、汽車、電子、機械等領域的國際知名企業,通過實施並行工程取得了顯著效益。
如美國洛克希德 (Lockheed) 飛彈與空間公司 (LMSC) 於 1992 年 10 月接受了美國國防部 (DOD) 用於“戰區高空領域防禦” (Thaad) 的新型號飛彈開發,該公司的飛彈開發一般需要 5 年時間,而採用並行工程的方法,最終將產品開發周期縮短 60%。具體的實行如下:
·改進產品開發流程。在項目工作的前期, LMSC 花費了大量的精力對 Thaad 開發中的各個過程進行分析,並最佳化這些過程和開發過程支持系統。採用集成化的並行設計方法。
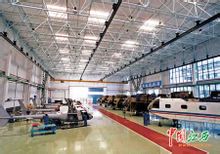
·實現信息集成與共享。在設計和實驗階段,一些設計、工程變更、試驗和實驗等數據,所有相關的數據都要進入資料庫。並各套用系統之間必須達到有效的信息集成與共享。
·利用產品數據管理系統輔助並行設計。LMSC 採用了一個成熟的工程數據管理系統輔助並行化產品開發。通過支持設計和工程信息及其使用的 7 個基本過程 ( 數據獲取、存儲、查詢、分配、檢查和標記、工作流管理及產品配置管理 ) ,來有效地管理它的工程數據。
CE 帶來的效益:飛彈開發周期由過去的 5 年縮短到 24 個月,產品開發周期縮短 60%。大大縮短了設計評審與檢查的時間 ( 一般情況下僅需 3h) ,並且提高了檢查和設計的質量。
另外,像 Siemens 重型雷達設備也採用並行工程來改進產品質量及縮短開發周期。其實施有 6 個方面的要求:
·建立“一次開發成功”團隊和技術中心 ;
·開發一種新的設計過程控制工具來跟蹤循環中的時間延遲,消除無效的等待時間 ;
·引入 IDEF建模系統,使工程師在建模過程中質疑並改進 ;
·過程控制工具。其軟體包含獲得每個通過設計中心的設計檔案的歷史資料以及記錄 DCI 的根本原因 ;
·採用 1 個線上系統要求對取消 DCI 負責的工程管理員寫出詳細原因 ;
·將產品設計小組和產品測試小組合併為數字小組,並在以後負責開發測試,測試考慮則將成為設計過程的一部分。
ABB(瑞士) 火車運輸系統建立了支持 CE 的計算機系統、可互操作的網路系統和一致的產品數據模型,組織了設計和製造過程的團隊,並套用仿真技術。套用並行工程後大大縮短了產品開發的周期。過去從契約簽訂到交貨需 3~4 年,僅用 3~18 個月,對於東南亞的顧客,可在 12 個月內交貨。整個產品開發周期縮短 25%~33% ,其中從用戶需求到測試平台需 6 個月,縮短了 50%。
另外,像雷諾 (Renauld) 、通用電力 (GE) 等著名企業通過實施並行工程並取得了顯著效益。
中國的發展與套用
中國製造業要想進入世界競爭,必須增強自身的產品開發能力,並行工程是一個非常重要的選擇。CE 在中國的研究與套用分為以下幾個階段:
一、1992 年前是並行工程的預研階段, 863/CIMS 年度計畫和國家自然科學基金資助了一些並行工程相關技術的研究課題,如面向產品設計的智慧型 DFM ,並行設計方法研究,產品開發過程建模與仿真技術研究等。
·1993 年, 863/CIMS 主題組織清華大學、北航、上海交大、華工和航天 204 所等單位,組成 CE 可行性論證小組,提出在 CIMS 實驗工程的基礎上開展 CE 的攻關研究。
·1995 年 5 月, 863/CIMS 主題重大關鍵技術攻關項目“並行工程”正式立項,投入大量資金開展 CE 方法、關鍵技術和套用實施的研究。
·1995 年 5 月 -1997 年 12 月,進行了“並行工程”項目的攻關研究。
二、1998 年至今,“並行工程”已有攻關成果並進一步深入研究,套用於航天等領域。
國內對 CE 的研究也已發展到了一定的高度,以下是幾個成功套用並行工程的典型範例。
西安飛機工業 ( 集團 ) 有限公司 在已有軟體系統的基礎上,開發支持飛機內裝飾並行工程的系統工具,包括:適用於飛機內裝飾的 CAID 系統、 DEA 系統和模具的 CAD/CAE/CAM 系統。如 Y7-200A 內裝飾設計製造並行工程。通過了過程建模與 PDM 實施,工業設計, DFA ,並行工程環境下的模具 CAD/CAM ,飛機客艙內裝飾數位化定義等技術手段。Y7-700A 飛機內裝飾工程中,研製周期從 1.5 年縮短到 1 年,減少設計更改 60% 以上,降低產品研製成本 20% 以上。
三、以波音 737-700 垂直尾翼轉包生產為例,研製周期縮短 3 個月 ; 節約工裝引進費用 370 萬美元 ; 減少樣板 1165 塊,合計人民幣 50 萬元 ; 減少標工、二類工裝 23 項,合計人民幣 125 萬元 ; 減少過渡模 136 項,合計人民幣 68 萬元 ; 提高數控編程速度 4~6 倍,減少數控零件試切時間 40%; 工藝設計效率提高 1.5 倍等。
齊齊哈爾鐵路車輛並行工程中改進後的棚車開發流程。其改進的措施包括:在產品開發的早期階段,就能夠充分考慮衝壓件、鑄鋼件等零件的可製造性問題和鐵路貨車的結構強度、剛度及動力學品質等產品性能問題,從而能夠儘量減少設計錯誤,提高設計質量; 同時增加 DFX ,使得在產品設計階段即可考慮產品加工、裝配和工藝等問題,提高一次設計成功的可能性。實現工藝和工裝的並行開發,精簡設計過程 ; 製造系統與產品開發過程不構成大循環,從而縮短產品開發周期,提高產品質量與水平。
並行工程在房地產企業管理中的套用研究
並行工程理論所體現的哲學思想運用廣泛,這裡把這種思想主要運用到房地產企業管理的以下幾個方面:
一、生產管理方面
按照並行工程的思想,房地產開發從一開始就考慮影響整個過程的所有因素,使每個過程的所有階段都協調起來,並行地開展工作。將開發過程中內部外部,有形無形的因素都加以考慮,增強管理對象的交融度,並形成一種互補、匹配的整體結構。
並行工程的房地產開發T作實質上體現了開發工作的系統性——前期策劃、設計、建造、銷售、管理等過程已不再是一個個相互獨立的單元,而被納入一個完整的系統中進行考慮。前期策劃工作將產品設計、投資估算、開發計畫、建築施工、質量控制、銷售實現等因素一同納入系統。在策劃的同時就可以進行設計及施工準備,有助於提前發現問題,並及時調整。
房地產開發項目的壽命周期一般分為五個階段:投資決策和項目前期策劃階段;項目的設計和計畫階段;施工階段;項目的銷售階段;使用階段。每個階段內和各個階段之間都存在一些非串列工作,如:投資決策階段做的市場調研工作與設計階段的產品理念設計可以並行;施工圖設計工作與採購準備工作可以並行。
1.投資決策和項目前期策劃階段的並行套用
在投資決策和項目前期策劃階段要把管理、策劃、設計、施工、銷售、客戶、物業、行業專家等各方人員組合在一起,通過會議、問卷調查等方式對所策劃項目的目的、過程、結果做全方位的考慮。
在對顧客的需求方面運用質量功能配置(QFD,Quality Function Deployment)的方法,對顧客的需求進行分析。從廣義上講,QFD是一種採用矩陣圖解將用戶對產品和服務的要求全面反映到產品開發、設計、製造的各個階段的設計方法,它通過對產品開發過程的基本元素、事件和活動的分析以及它們之問關係的描述、轉換,實現對產品開發過程的管理、指導和控制,以保證最大限度地滿足客戶的需求,從而把客戶需求轉換成一系列可檢測、可操作的事件和活動。
2.項目的設計和計畫階段的並行套用
根據對顧客需求的分析全面指導項目的設計,運用並行工程的思想使後續階段的工作可行性和合理性作為一種設計約束條件,儘量減少後期施工過程中的設計變更和施工計畫變更。
設計和計畫階段應以以下5條為行動指導:①項目發展團隊(project development team)作為一個整體對整個設計負責。②項目發展團隊應該階段性的比較最佳化設計目標,剔除無附加價值的功能。③設計利用CAD系統網路以利於信息共享。④設計必須同時考慮施工的可操作性,例如:施工方法、技術、設備,施工順序和不同承包商之間的配合。⑤設計應該使施工可以在設計部分完成的情況下開始,而無需等到整個設計完成。
3.施工階段的並行套用
施工階段房地產企業一般通過招標交與專業的施工企業去完成,在策劃階段就應有專業的施工人員參與項目的策劃和設計,後來的施工過程中也要注意以下四個方面的並行套用:①應該降低傳統現場作業中個工序的相互依賴性,使儘可能多的工序能能同時開展。② 應該使所有工人了解整個項目,清楚自己在整個計畫中作用。③工程質量和質量檢查方法、標準應該公布在施工現場可見處。④定期將反饋意見送交跨部門小組以提高剩餘部分的設計。
二、組織管理方面
1.並行團隊的建立
並行團隊的建立是企業為了完成特定的產品開發任務而組成的多功能型團隊,包括來自市場、設計、施工、採購、銷售、維修、服務、顧客、供應商、協作單位的代表。通過團隊成員的共同努力能夠產生積極的協同作用,使團隊的績效水平遠大於個體成員的績效總和。團隊成員技能互補,致力於共同的績效目標,並且共同承擔責任。大大提高產品生命周期各階段人員之間的相互信息交流。
2.團隊的管理手段
①計畫和控制。就計畫和控制的內容來說,一般包括進度、成本、質量等。具體方法和技術有:網路分析技術、基於活動的成本控制、全面質量管理等。
②領導和激勵。從具體操作的角度來說,領導風格基本有四種:指示、參與、授權、推銷。選擇風格時,主要隨任務結構和員工素質的變化而變化。激勵的方法主要有:目標管理、行為校正、員工參與方案和浮動工資方案。
③溝通和協調。對於密切配合的團隊協同工作模式來說,信任、溝通和協調尤為重要。溝通有四種功能:控制、激勵、情緒表達和信息。而協調在具體的操作時,既可化解衝突以避免組織功能失調,也可在保證組織功能正常的前提下激發衝突以達到提高群體工作效能的作用。
3.團隊的決策模式和方法
工作團隊在做出決策時,一般採取群體決策的方式。其主要優點有:更完全的信息和知識、增加觀點的多樣性、提高了決策的可接受性、增加合法性。其不足之處:浪費時間、從眾壓力、少數人控制和責任不清。總的來說,群體決策更準確,質量更優。但就速度和效率而言,群體決策劣於個體決策。
4.衝突的協調解決
在實施並行工程的過程中,由於在初始階段就套用了並行方式綜合考慮整個生命過程中各環節的影響,因此,並行工程強調多學科專家的協作。由於各專家的知識面,背景等的不同,由他們組成的目標各異,它們之間相互作用、相互制約,可能隨時發生衝突,如何協調好這些衝突,是實施並行工程的關鍵問題。從某種意義上講,並行工程的實施過程就是衝突不斷產生、發展、解決的過程。衝突的產生可以使設計人員及早發現問題、解決問題,保證設計方案的最佳化。
三、輔助管理方面
1.建立有利於並行工程實施的文化氛圍
並行工程最為重要的一方面在於他代表了一種不同的文化,而不僅僅是一個方法或技術。事實上,一些組織己經在他們對並行工程的定義中承認了這一點。變文化是不容易的,主要方法是通過教育培訓。從高層管理部門開始,組織中所有成員都要意識到並行工程方法的好處以及它需要的條件。組織中每一層和中的每一個成員都必須完全意識到並行工程是什麼,以及不是什麼,並行工程可能在這一步沒有完成之前進行。
2.爭取企業領導的大力支持以及各部門主管的理解
採用並行工程方法實施工程管理,必定會涉及到組織的變革,權力分配的變化,各種獎勵政策的變化,人際關係的變化。而企業對權力分配、責任和利益關係的確定是極為敏感的。因此必須有企業最高層主管的支持。而在中國建築企業的現狀下,一般企業高層主管很難對其下屬實施強有力的影響,他必須得到其下屬的理解與支持。按照並行工程思想,他必須要賦予各負責人對各部門資源的支配權,那么顯然會削弱各部門主管的權力,因而需要對各部門主管做大量思想工作。企業領導人的決心、威望、影響力和領導藝術,是贏得各部門主管密切配合的關鍵。
3.搭建並行工程信息化模型和數據平台
隨著計算機、通信技術的快速發展,使得並行工程在企業管理能夠更好的實施。一般包括以下的幾種信息系統的建立完成來輔助項目的完成及企業管理的順暢。
①項目管理系統。在並行產品開發中,多學科團隊一般是以項目為單位組建的,其管理方式也基本是按項目管理的思想進行。項目管理軟體的功能一般包括:任務分解、進度安排和跟蹤、資源分配、成本核算、分析功能。
②工作流管理系統。工作流管理WFM是人與計算機共同工作的自動化協調、控制和通信,在計算機化的業務過程上,通過在網上的運行軟體,使所有命令的執行都處於受控狀態。在工作流管理下,工作量可以被監督,使分派工作到不同的用戶的工作量達到平衡。
③群體決策支持系統。小組的決策過程因時間、地點的不同,可有四種情況發生:同時— — 同地、同時—— 異地、異時— — 同地、異時——異地。與此相對應也有四種類型的群體決策支持系統工具:決策室(支持同地—— 同時的互動作用);工程室(支持同地— — 異時的互動作用);遠程會議系統(支持同時— — 異地的互動作用);電子郵件系統和語音郵件系統(支持異時——異地的互動作用)。
④信息共享系統。信息共享是並行小組工作的一個基本要素,信息在小組內的透明化並且溝通要及時,通過計算機輔助項目管理信息系統,可以保證信息傳遞的準時性,有助於各方參與者及時進行溝通,迅速反應。
並行工程在以上三個房地產企業管理方面的套用實際上是解決了房地產企業普遍存在的項目策劃、定位不準確,設計理念不符合實際情況,項目開發用時過長,項目建設過程混亂,後期服務跟不上等方面的問題。
並程工程在汽車工業中的運用
汽車工業是一個技術與資金高度密集的成熟產業,是當今許多高新技術的載體,產品開發是汽車工業技術的核心,其本身也是一項重要的技術。工藝裝備
汽車開發是一項複雜的系統工程。它的開發流程包括創意、造型、設計、工程分析、樣車實驗、工裝設計及加工、調試、生產、裝配等工作。如果不能很好地協調各環節,汽車開發必然是費時費力的浩大工程。尤其是這幾年國內汽車業迅猛發展,各汽車廠競爭空前激烈,汽車開發的周期、質量、成本顯得尤為重要。由於對產品研究開發的投入力度不夠,新產品開發全過程的實踐不夠,中國與國外高水平的汽車開發技術相比還有很大差距。特別是在產品開發的組織體系及人員、產品開發工作的組織、產品開發過程等環節上。下面將探討採用並行工程在汽車的開發過程中如何實現縮短產品開發周期、提高產品質量、降低產品開發成本。
一般來講,汽車產品開發期共有4個階段,即策劃階段、設計階段、樣品試製階段、小批試製階段。汽車企業實施產品開發並行工程,就應該在這四個階段運用。
1.並行工程在策劃階段的運用
在策劃階段汽車企業決策層首先應該考慮:開發的產品是否能為企業帶來經濟效益;開發的產品是否具有的先進性、可行性、經濟性、環保性等優點;開發的產品是否具有潛在市場;競爭對手是否也在開發的同類型產品他們的水平如何;開發產品是否符合國內外法律法規和專利要求等方面的可行性。
如果通過論證認為可行,則立即組建產品開發並行工程項目小組。企業應從與產品開發相關的部門,選定有一定技術專長和管理能力的產品設計、產品工藝、質量管理、現場施工、生產管理等人員(如有必要還可邀請產品的使用客戶代表參加)組成並行工程項目小組,同時明確小組成員的工作職責。
2.並行工程在設計階段的運用
並行工程要求產品開發人員在制定產品設計的總體方案時就考案產品生命周期中的所有因素,解決好產品的T、Q、C、S難題,即以最快的上市速度、最好的質量、最低的成本及最優的服務來滿足顧客的不同需求和社會可持續發展的需求。總體方案的設計與論證作為以後詳細設計的依據,必須從總體上保證最優,包括最佳化設計、降低成本、縮短研製周期。
在設計階段產品開發並行工程項目小組應根據用戶要求確定所開發產品的設計目標。要確保所開發產品能使用戶滿意,就必須以用戶關注的項目開發周期、項目開發成本和預定的最優效果作為所開發產品的設計目標。
設計目標是並行工程項目小組的行動綱領,這些目標都是充分研究國內外經濟形勢、顧客合理要求、市場總體需求、國家法律法規要求和企業內部客觀條件,並在全面收集競爭對手有關資料的基礎上確定的。設計目標確定後,要採用既合理又簡便的方法,根據用戶要求,找出關鍵目標,並將設計目標分解為若干個分類目標。這樣,並行工程項目小組就能白上而下地把設計目標層層展開,企業各部門並行地開展工作。並按關鍵目標要求,對產品開發過程進行評價得出最優設計結果。
3.並行工程在樣品試製階段的運用
並行工程在樣品試製階段的工作重點是實現產品各方面的最佳化。並行工程項目小組應建立典型產品的設計模型。汽車企業進行典型產品設計、可靠性設計和可靠性試驗的目的,就是為了建立典型產品的設計資料庫,並通過現代計算機的套用技術,將設計數據實現信息收集、編制、分配、評價和延伸管理,確立典型產品設計模型。並通過對確立的典型產品設計模型的研究,利用信息反饋系統進行產品壽命估算,找出其產品設計和產品改進的共性要求,實現產品的最最佳化設計。要使開發的汽車產品設計最最佳化,還必須了解同類產品的失效規律及失效類型,尤其是對安全性、可靠性、耐久性有重要影響的產品設計時,要認真分析資料庫內同類產品的失效規律及失效類型作用,採取成熟產品的積累數據,通過增加安全係數、降低承受負荷、強化試驗等方法,來進行產品最最佳化設計。
4.並行工程在小批量試製階段的運用
並行工程在小批量試製階段的工作重點是實現生產能力的最佳化。應按產品質量要求對生產能力進行合理配置。生產過程的“人員、設備、物料、資金、信息等”諸要素的最佳化組合,是實現用最少投入得到最大產出的基礎,尤其是在產品和技術的更新速度不斷加快、社會化大生產程度日益提高的今天,要實現產品快速投放市場,就更需要對工藝流程、工序成本、設備能力、工藝裝備有效性、檢測能力及試驗能力的最佳化分析,實現生產能力的合理配置。同時對生產出來的產品,應站在用戶的立場上,從加工完畢、檢驗合格的產品中抽取一定數量,評價其質量特性是否符合產品圖紙、技術標準、法律法規等規定要求;並以質量缺陷多少為依據,評價產品的相應質量水平,並督促有關部門立即制定改進措施,對投入試用的產品還應把用戶反饋回來的信息進行分析,對用戶提出的合理和可行的建議,也應拿出改進措施,實現客戶滿意。另外,由於汽車這個產品對安全要求的特殊性,企業還必須對汽車進行安全可靠性試驗。
汽車產品的安全可靠性試驗的目的,主要是考核產品是否達到規定的安全要求。產品設計改進和產品質量改進是貫穿於產品壽命周期的一項經常性工作,持續改進是使企業管理水平不斷提升的基該方法,更是追求顧客滿意、企業獲利的永恆動力。
圖書信息
基本信息
書 名: 面向製造和裝配的產品設計指南
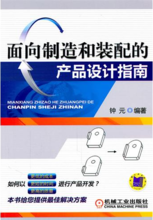
作者:鍾元
出版社:機械工業出版社
出版時間:2011-5-1
ISBN: 978-7-111-34008-9
開本:A5
定價: 28.00元
內容簡介
面向製造和裝配的產品設計是企業以“更低的開發成本、更短的開發周期、更高的產品質量”進行產品開發的關鍵。本書詳細介紹了面向製造和裝配的產品設計指南,包括面向裝配的設計指南、塑膠件設計指南、鈑金件設計指南和壓鑄件設計指南等,輔以圖形和真實案例,並提供面向製造和裝配的產品設計檢查表,具有非常高的實用價值。
本書適合從事產品開發的工程師閱讀,也可供高等院校機械類專業學生學習。
前言
產品開發如同奧林匹克競技。更低的產品開發成本、更短的產品開發周期、更高的產品質量,永遠是企業追求的最高境界。在全球化的背景下,企業之間的競爭日益加劇,在產品開發中任何一個環節稍有落後,就可能被競爭者超越,甚至被淘汰出局。
企業如何才能以“更低的成本、更短的時間、更高的質量”進行產品開發呢?面向製造和裝配的產品設計正是這樣的一個有效手段。它從提高產品的可製造性和可裝配性入手,在產品開發階段就全面考慮產品製造和裝配的需求,同時與製造和裝配團隊密切合作,通過減少產品設計修改、減少產品製造和裝配錯誤、提高產品製造和裝配效率,從而達到降低產品開發成本、縮短產品開發周期、提高產品質量的目的。
本書首先介紹了面向製造和裝配的產品開發;然後重點介紹了面向製造和裝配的設計指南,其中包括面向裝配的設計指南、塑膠件設計指南、鈑金件設計指南、壓鑄件設計指南和公差分析等;最後提供了面向製造和裝配的產品設計檢查表,用於系統化地檢查產品設計是否滿足產品製造和裝配的需求。
本書根據作者多年產品開發實際經驗編寫,並結合了國內外先進的產品開發理念和產品設計思想,具有以下特色:
1.詳細介紹面向裝配的設計指南
同產品的製造一樣,產品的裝配處於同等重要甚至更為重要的地位,但長期被忽視。本書詳細介紹了面向裝配的設計指南,以確保產品設計符合產品裝配的要求,減少裝配錯誤,降低裝配成本,提高裝配效率和裝配質量。
2.實用性強
本書沒有複雜的理論,而是從產品開發的實際套用著手,介紹了面向製造和裝配的設計指南。每一條設計指南都來源於真實的產品開發經驗和教訓總結,違反其中任何一條設計指南都可能會造成產品開發成本的增加、產品開發周期的延長和產品質量的降低。
另外,本書提供的產品設計檢查表能夠幫助機械工程師系統化地檢查產品設計,確保產品設計符合製造和裝配的要求,其有非常高的實用性。
3.實例豐富、強調實踐
本書的設計指南輔以圖形和真實案例,簡單易懂。作者從一個機械工程師的角度來分析和講述每一條設計指南對產品開發的影響,指導機械工程師利用每一條設計指南來提高產品開發的質量。
圖書目錄
前言
第1章面向製造和裝配的產品開發
1.1緒論
1.1.1產品開發模式的進化
1.1.2產品設計的重要性
1.1.3產品設計的要求
1.2傳統產品開發模式
1.2.1傳統產品開發流程
1.2.2傳統產品開發模式的弊端
1.3面向製造和裝配的產品開發模式
1.3.1面向製造和裝配的產品開發流程
1.3.2面向製造和裝配的產品開發的優點
1.3.3面向製造和裝配的產品開發與並行工程
1.4面向製造和裝配的產品開發的實施
1.4.1實施的障礙
1.4.2實施的關鍵
第2章面向裝配的設計指南
2.1面向裝配的設計
2.1.1裝配的定義
2.1.2最好和最差的裝配工序
2.1.3面向裝配的設計的定義
2.1.4面向裝配的設計的目的
2.1.5面向裝配的設計的歷史
2.2設計指南
2.2.1減少零件數量
2.2.2減少緊固件的數量和類型
2.2.3零件標準化
2.2.4模組化產品設計
2.2.5設計一個穩定的基座
2.2.6設計零件容易被抓取
2.2.7避免零件纏繞
2.2.8減少零件裝配方向
2.2.9設計導向特徵
2.2.10先定位後固定
2.2.11避免裝配干涉
2.2.12為輔助工具提供空間
2.2.13為重要零部件設計裝配止位特徵
2.2.14防止零件欠約束和過約束
2.2.15寬鬆的零件公差要求
2.2.16防錯的設計
2.2.17裝配中的人機工程學
2.2.18線纜的布局
第3章塑膠件設計指南
3.1塑膠
3.1.1塑膠的定義
3.1.2塑膠的特性
3.1.3注射成型
3.2塑膠材料選擇
3.2.1塑膠材料的分類
3.2.2常用塑膠材料性能
3.2.3塑膠材料選擇原則
3.3設計指南
3.3.1零件壁厚
3.3.2避免尖角
3.3.3脫模斜度
3.3.4加強肋的設計
3.3.5支柱的設計
3.3.6孔的設計
3.3.7提高塑膠件強度的設計
3.3.8改善塑膠件外觀的設計
3.3.9降低塑膠件成本的設計
3.3.10注射模具可行性設計
3.3.11注射模具討論要點
3.4塑膠件的裝配方式
3.4.1卡扣裝配
3.4.2機械緊固
3.4.3超音波焊接
第4章鈑金件設計指南
4.1鈑金
4.2設計指南
4.3鈑金常用裝配方式
第5章壓鑄件設計指南
5.1壓鑄簡介
5.2常用壓鑄材料介紹
5.3設計指南
第6章公差分析
6.1公差分析簡介
6.2公差分析的步驟
6.3公差分析指南
6.4利用Excel進行公差分析
第7章面向製造和裝配的設計檢查表
7.1和諧的設計
7.2設計檢查表