概況
UO陶瓷是人們熟知的核燃料,已廣泛、成功地套用於水冷堆中。它有許多眾所周知的優點,但它有兩個主要的缺點:低熱導和在熱衝擊下破碎。因此為了克服UO陶瓷的上述缺點,就產生了關於UO的金屬陶瓷設計概念,如UO-不鏽鋼金屬陶瓷板燃料元件,已在幾個特小型動力隊中成功使用。由於鋯-錫合金不僅有良好的綜合性能,而且中子吸收載面僅為不鏽鋼的1/19左右,這類特種小型動力堆也宜採用UO-Zr-2(或Zr-4)代替UO-不鏽鋼。使用金屬陶瓷燃料的缺點是必須採用高濃鈾。同時,使用UO-Zr-2金屬陶瓷所存在的一個主要問題是,在大約700℃溫度下,Zr-2與UO發生反應,生成Zr-2合金和Zr-U合金反應層,後者輻照穩定性差,其過度擴散還將使金屬陶瓷設計概念失效。雖然在核反應堆中使用時不會達到上述反應溫度,但壓力加工溫度要高於此溫度。為防止發生這種現象。可在UO顆粒表面塗敷幾微米的第三種材料。
與單一化的燃料相比,金屬陶瓷核燃料(彌散型燃料)有幾個突出的優點:①由於燃料顆粒很小,所以裂變產物損傷效應被局限在很小的地域內,因此從輻照損傷觀點來看,這種燃料可做成長壽命元件使用;②由於裂變產物被局限在燃料顆粒內或金屬基體中,所以裂變氣體釋放份額極小,相當於增加了一道燃料屏障,因此由彌散型燃料做成的燃料元件更安全可靠;③由於基體金屬和燃料相有多種選擇,所以彌散型燃料的組合方式是多種多樣的。如果選擇具有良好機械性能、抗腐蝕性能和熱導性能的金屬或合金做基體材料,並且有恰當的燃料相含量的話,那么這種金屬陶瓷燃料就能基本保留金屬或合金的上述優良性能。
金屬陶瓷核燃料設計依據
金屬陶瓷核燃料輻照理論
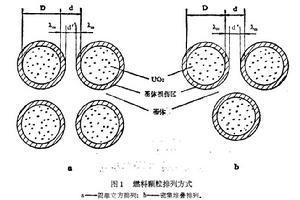
金屬陶瓷核燃料,就是要把裂變產物損傷限制在UO顆粒附近基體內,從而使它因輻照產生的性能變化很小。金屬陶瓷中的彌散狀態,則由UO顆粒尺寸及其在彌散體中的體積含量而確定下來。一般假設UO顆粒是等直徑的球形,並且均勻分布在金屬基體中,其排列方式有兩種:一種是簡單立方排列;一種是密集堆疊排列,即正四面體排列。前者排列鬆散,但顆粒間距緊湊,它對於稀疏的燃料顆粒排列是適當的模型;後者排列緊密,但顆粒間距較大。
從金屬陶瓷燃料輻照理論出發,在整個燃料使用壽期內,使包圍UO顆粒的未受裂變產物損傷的金屬基體始終形成連續的網路。這就要求數據基體的體積份額占優勢以及UO顆粒尺寸應比裂變碎片在UO中的反衝行程大得多,即UO顆粒間距要大到使受到裂變產物損傷的基體區域既不相碰,更不重迭。在滿足這一要求的前提下,往往可以允許UO顆粒之間存在低濃度的裂變產物。因為這樣來修正關於未受損傷的基體金屬形成連續網路的概念,即所謂連續網路,不是以是否存在裂變產物為依據,而是以裂變產物對基體金屬的物理和機械性能的有害影響在允許程度以下為依據,即允許有較小的顆粒間距和較大的燃料相體積份額。同時,如果受裂變產物損傷的基體區域中裂變產物含量過高的話,該損傷區將發生局部破壞,因此裂變產物從UO顆粒中逸出的份額應低於10%。還應把單位體積基體中的平均裂變產物濃度作為金屬陶瓷核燃料性能變化的另一個適當度量,這個觀點是認為基體局部損傷不受限制。
綜上所述,從金屬陶瓷核燃料輻照理論出發,在燃料相含量和燃料顆粒尺寸設計中,應同時滿足顆粒排列、裂變產物濃度,單位體積基體中的平均裂變產物濃度等要求。
金屬陶瓷核燃料壓力加工要求
在UO相含量和顆粒尺寸設計中,除依據金屬陶瓷輻照理論外,還要考慮壓力加工中的一些因素:
(1) 首先,UO顆粒愈小,愈容易做到均勻分散,通常要求顆粒尺寸為100~200 μm;
(2) 其次,由於這類燃料元件由熱軋加工做成,熱軋中,為保證燃料芯體有良好的流動性,防止UO顆粒嵌入包殼,又要求UO顆粒直徑上限滿足80~100 μm;
(3) UO顆粒尺寸很大或很小時都會使燃料芯體強度急劇下降,為此宜取50~100 μm;
(4) 壓力加工要求燃料芯體及其包殼材料間的流動性能差別儘可能小,除使燃料芯體的基體金屬與包殼材料相同外(為使其界面冶金結合),還要求燃料相含量不能太高。儘管國外已做出UO相體積含量達50%的UO-不鏽鋼金屬陶瓷板元件,但在幾個核反應堆中正式使用的UO-不鏽鋼金屬陶瓷板,其UO相質量含量均在30%(相當於24.5%體積含量)之內;相關文獻認為,高於40%體積含量的金屬陶瓷核燃料難度較大。
綜上所述,從壓力加工方面考慮,UO顆粒直徑宜取為100 μm以下。
套用前景
與路上核電站相比,金屬陶瓷核燃料多用於浮動式核電站的套用,具有較大的經濟實用性,核反應堆在正常工況和異常工況下具有更高的可靠性和安全性。具有耐用性高、可靠性好、較低的換料頻率,產生更多電能的同時產生更少的乏燃料。套用於浮動式核反應堆的金屬陶瓷核燃料主要分為以下幾種:
(1)改良的UO芯塊燃料
通過改進UO的導熱性可以提高UO芯塊的套用性能,添加BeO、SiC等可增加 UO芯塊的熱導率。BeO 是具有最高熱導率的陶瓷材料之一,輻照環境下,即使在 2200 ℃不與 UO反應,良好的中子慢化特徵,在發生 (n,2n) 核反應時釋放一個中子,使中子平衡得到改善。添加到UO中的BeO形成連續網狀的結構,可將燃料芯塊中心的熱量有效的導出。研究人員開發了一種“共燒結”技術製備UO-BeO芯塊,製備芯塊的標準過程是使UO形成小的顆粒,然後一同燒結。在燒結前引入BeO粉到顆粒狀的UO,顆粒周圍被高熱導率BeO包圍,BeO從中心導出熱量。因此產生同樣的熱功率,與傳統的UO芯塊相比,這種燃料有更低的中心線溫度,減少了與包殼的相互作用,減少因不均勻的熱膨脹導致的芯塊開裂。
(2)UO-Zr彌散燃料
為了增加UO燃料的熱導率同時提高燃耗,俄羅斯採用毛細管浸漬技術製備 UO彌散棒狀燃料,以改進的低熔點(1063K-1133K)的鋯合金為基體,這種棒狀燃料可以增加燃料中鈾的含量,降低燃料元件芯體內部溫度,擴大燃耗和增強燃料元件在運行瞬態的耐受性。毛細管浸漬技術可以製備高鈾含量的燃料,燃料相的體積分數可達55%~65%,基體體積分數為10%~20%,包含15%~30% 的氣孔率。通過毛細管浸漬法製備的燃料元件鈾含量可達 9~10 g/cm,高的熱導率 18~22 WmK,這種燃料用於PWR和BWR時,燃料的溫度低至723K~773K,同時內部顯著的氣孔特徵可協調燃料的腫脹。由於毛細管浸漬技術製備的彌散型燃料,具有的高鈾裝載量、高耐用性,可靠性、增大燃耗,高熱導率等特點。這種類型的燃料元件正在考慮用於浮動式反應堆。
(3)UO-AlSi彌散燃料
UO-AlSi 燃料的高質量已在核動力破冰船堆芯中得到了檢驗。俄羅斯正在基於核動力破冰船的燃料元件,製造用於浮動式核電機組和小型反應堆破冰船堆芯採用燃料棒。這種燃料以鋁矽合金為基體,UO彌散在基體中,235U的富集度不超過20%,並且已將這種燃料成功套用在KLT-40C浮動式核反應堆上。UO-AlSi 彌散棒狀燃料包殼為鋯合金,採用雙金屬共擠壓工藝製造。這種燃料元件具有固體金屬型燃料的中心溫度低、包容裂變產物性能好、抗衝擊性好等特點。
(4)U-Zr合金燃料
美國Lightbridge公司正在開發一種套用於輕水堆的改良型U-Zr金屬燃料,它能夠在比傳統UO燃料高 30% 的功率密度下運行。這種新燃料可以使壓水堆在更高的輸出功率下運行並且延長運行周期,從而提高經濟性、安全性和燃料性能。這種合金燃料使用富集度高達19.7 wt%的235U。燃料棒沿著其長度方向呈螺旋形結構,這種獨特的幾何形狀與合金熱性能的結合,大大提高了向冷卻劑的傳熱。燃料棒的製造過程是粉末冶金同時擠壓使燃料棒的三部分之間形成冶金結合,增強了燃料的導熱性能。燃料棒獨特的十字形結構比標準的圓柱形燃料棒多提高了40%的表面積,這種十字形結構的燃料具有良好的套用前景,是未來浮動式輕水反應堆可選擇的燃料。