原理
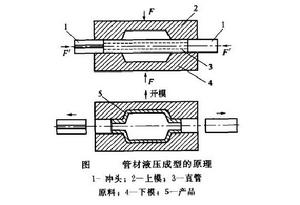
管材液壓成型的原理如圖所示,首先將原料(直 管或預先彎曲成型的鋼管)放入下模,然後管件兩端的沖頭在液壓缸的作用下壓入,將管件內部密閉,沖頭內有液體通道,液體不斷流人管件,此時上模向下移動,與下模共同形成封閉的模腔,最後高壓泵與閥門控制液體壓力不斷增大,沖頭向內推動管件, 管壁逐漸貼近模具變形,最終得到所需形狀的產品。
常見缺陷及影響因素
管材液壓成型中,常見的缺陷主要是折曲、起鈹和破裂。影響成型質量的因素有載入方式、載入大小、液體流動及液體壓力的控制等。除此之外,還有其他因素,如潤滑條件、工件和模具材料的性能以及表面質量等。提高工件和模具的表面質量,再加上良好的潤滑條件可以減小材料流動的摩擦力,有助於成型。
套用
液壓成型工藝在汽車、航空、航天和管道等行業有著廣泛的套用。主要適用於沿工件軸線變化的圓形、矩形或異形截面空心結構件,如汽車的排氣系統異形管件;非圓截面空心框架,如發動機托架、儀錶盤支架、車身框架(占汽車質量的11%~15%);空心軸類件和複雜管件等。