基本簡介
一種用於壓塑、擠塑、注塑、吹塑和低發泡成型的組合式塑膠模具,它主要包括由凹模組合基板、凹模組件和凹模組合卡板組成的具有可變型腔的凹模,由凸模組合基板、凸模組件、凸模組合卡板、型腔截斷組件和側截組合板組成的具有可變型芯的凸模。模具凸、凹模及輔助成型系統的協調變化。可加工不同形狀、不同尺寸的系列塑件。塑膠加工工業中和塑膠成型機配套,賦予塑膠製品以完整構型和精確尺寸的工具。由於塑膠品種和加工方法繁多,塑膠成型機和塑膠製品的結構又繁簡不一,所以,塑膠模具的種類和結構也是多種多樣的。
隨著塑膠工業的飛速發展和通用與工程塑膠在強度等方面的不斷提高,塑膠製品的套用範圍也在不斷擴大,塑膠產品的用量也正在上升。
塑膠模具是一種生產塑膠製品的工具.它由幾組零件部分構成,這個組合內有成型模腔。注塑時,模具裝夾在注塑機上,熔融塑膠被注入成型模腔內,並在腔內冷卻定型,然後上下模分開,經由頂出系統將製品從模腔頂出離開模具,最後模具再閉合進行下一次注塑,整個注塑過程是循環進行的。
一般塑膠模具由動模和定模兩部分組成,動模安裝在注射成型機的移動模板上,定模安裝在注射成型機的固定模板上。在注射成型時動模與定模閉合構成澆注系統和型腔,開模時動模和定模分離以便取出塑膠製品。
模具的結構雖然由於塑膠品種和性能、塑膠製品的形狀和結構以及注射機的類型等不同而可能千變萬化,但是基本結構是一致的。模具主要由澆注系統、調溫系統、成型零件和結構零件組成。其中澆注系統和成型零件是與塑膠直接接觸部分,並隨塑膠和製品而變化,是塑模中最複雜,變化最大,要求加工光潔度和精度最高的部分。
澆注系統是指塑膠從射嘴進入型腔前的流道部分,包括主流道、冷料穴、分流道和澆口等。成型零件是指構成製品形狀的各種零件,包括動模、定模和型腔、型芯、成型桿以及排氣口等。
我國塑膠模具在高技術驅動和支柱產業套用需求的推動下,形成了一個巨大的產業鏈條,從上游的原輔材料工業和加工、檢測設備到下游的機械、汽車、機車、家電、電子通信、建築建材等幾大套用產業,塑膠模具發展一片生機。
主要分類
按照成型方法的不同,可以劃分出對應不同工藝要求的塑膠加工模具類型,主要有注射成型模具、擠出成型模具、吸塑成型模具、高發泡聚苯乙烯成型模具等。
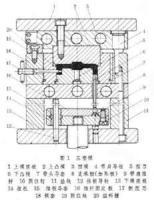
1、塑膠注射(塑)模具
它主要是熱塑性塑膠件產品生產中套用最為普遍的一種成型模具,塑膠注射模具對應的加工設備是塑膠注射成型機,塑膠首先在注射機底加熱料筒內受熱熔融,然後在注射機的螺桿或柱塞推動下,經注射機噴嘴和模具的澆注系統進入模具型腔,塑膠冷卻硬化成型,脫模得到製品。其結構通常由成型部件、澆注系統、導向部件、推出機構、調溫系統、排氣系統、支撐部件等部分組成。製造材料通常採用塑膠模具鋼模組,常用的材質主要為碳素結構鋼、碳素工具鋼、合金工具鋼,高速鋼等。注射成型加工方式通常只適用於熱塑膠品的製品生產,用注射成型工藝生產的塑膠製品十分廣泛,從生活日用品到各類複雜的機械,電器、交通工具零件等都是用注射模具成型的,它是塑膠製品生產中套用最廣的一種加工方法。
2、 塑膠壓塑模具
包括壓縮成型和壓注成型兩種結構模具類型。它們是主要用來成型熱固性塑膠的一類模具,其所對應的設備是壓力成型機。壓縮成型方法根據塑膠特性,將模具加熱至成型溫度(一般在103°—108°),然後將計量好的壓塑粉放入模具型腔和加料室,閉合模具,塑膠在高熱,高壓作用下呈軟化粘流,經一定時間後固化定型,成為所需製品形狀。壓注成型與壓縮成型不同的是有單獨的加料室,成型前模具先閉合,塑膠在加料室內完成預熱呈粘流態,在壓力作用下調整擠入模具型腔,硬化成型。壓縮模具也用來成型某些特殊的熱塑性塑膠如難以熔融的熱塑性塑膠(如聚加氟乙烯)毛坯(冷壓成型),光學性能很高的樹脂鏡片,輕微發泡的硝酸纖維素汽車方向盤等。壓塑模具主要由型腔、加料腔、導向機構、推出部件、加熱系統等組成。壓注模具廣泛用於封裝電器元件方面。壓塑模具製造所用材質與注射模具基本相同。
3、塑膠擠出模具
用來成型生產連續形狀的塑膠產品的一類模具,又叫擠出成型機頭,廣泛用於管材、棒材、單絲、板材、薄膜、電線電纜包覆層、異型材等的加工。與其對應的生產設備是塑膠擠出機,其原理是固態塑膠在加熱和擠出機的螺桿旋轉加壓條件下熔融,塑化,通過特定形狀的口模而製成截面與口模形狀相同的連續塑膠製品。其製造材料主要有碳素結構鋼、合金工具等,有些擠出模具在需要耐磨的部件上還會鑲嵌金剛石等耐磨材料。擠出中工工藝通常只適用熱塑性塑膠品製品的生產,其在結構上與注塑模具和壓塑模具有明顯區別。
4、塑膠吹塑模具
是用來成型塑膠容器類中空製品(如飲料瓶、日化用品等各種包裝容器)的一種模具,吹塑成型的形式按工藝原理主要有擠出吹塑中空成型、注射吹塑中空成型、注射延伸吹塑中空成型(俗稱“注拉吹”),多層吹塑中空成型,片材吹塑中空成型等。中空製品吹塑成型所對應的設備通常稱為塑膠吹塑成型機,吹塑成型只適用於熱塑膠品種製品的生產。吹塑模具結構較為簡單,所用材料多以碳素多則製造。
5、塑膠吸塑模具
是以塑膠板、片材為原料成型某些較簡單塑膠製品的一種模具,其原理是利用抽真空盛開方法或壓縮空氣成型方法使固定在凹模或凸模上的塑膠板、片,在加熱軟化的情況下變形而貼在模具的型腔上得到所需成型產品,主要用於一些日用品、食品、玩具類包裝製品生產方面。吸塑模具因成型時壓力較低,所以模具材料多選用鑄鋁或非金屬材料製造,結構較為簡單。
6、高發泡聚苯乙烯成型模具
是套用可發性聚苯乙烯(由聚苯乙烯和發泡劑組成的珠狀料)原料來成型各種所需形狀的泡沫塑膠包裝材料的一種模具。其原理是可發聚苯乙烯在模具內能入蒸汽成型,包括簡易手工操作模具和液壓機直通式泡沫塑膠模具兩種類型,主要用來生產工業品方面的包裝產品。製造此種模具的材料有鑄鋁、不鏽鋼、青銅等。
設計要素
模具設計和製造與塑膠加工有密切關係。塑膠加工的成敗,很大程度上取決於模具設計效果和模具製造質量,而塑膠模具設計又以正確的塑膠製品設計為基礎。
![塑膠模具[加工塑膠使其成型的工具]](/img/8/bf0/nBnauM3XyEDM2AjM0IDN4UjM2UTM1QDN5MjM5ADMwAjMwUzLyQzL1QzLt92YucmbvRWdo5Cd0FmL0E2LvoDc0RHa.jpg)
塑膠模具設計要考慮的結構要素有:
①分型面,即模具閉合時凹模與凸模相互配合的接觸表面。它的位置和形式的選定,受製品形狀及外觀、壁厚、成型方法、後加工工藝、模具類型與結構、脫模方法及成型機結構等因素的影響。
②結構件,即複雜模具的滑塊、斜頂、直頂塊等。結構件的設計非常關鍵,關係到模具的壽命、加工周期、成本、產品質量等,因此設計複雜模具核心結構對設計者的綜合能力要求較高,儘可能追求更簡便、更耐用、更經濟的設計方案。
③模具精度,即避卡、精定位、導柱、定位銷等。定位系統關係到製品外觀質量,模具質量與壽命,根據模具結構不同,選擇不同的定位方式,定位精度控制主要依靠加工,內模定位主要是設計者充分去考慮,設計出更加合理易調整的定位方式。
②澆注系統,即由注塑機噴嘴至型腔之間的進料通道,包括主流道、分流道、澆口和冷料穴。特別是澆口位置的選定應有利於熔融塑膠在良好流動狀態下充滿型腔,附在制品上的固態流道和澆口冷料在開模時易於從模具內頂出並予以清除(熱流道模除外)。
③塑膠收縮率以及影響製品尺寸精度的各項因素,如模具製造和裝配誤差、模具磨損等。此外,設計壓塑模和注塑模時,還應考慮成型機的工藝和結構參數的匹配。在塑膠模具設計中已廣泛套用計算機輔助設計技術。
模具配件
沖針、沖頭、導柱、導套、精定位、頂桿、頂針、司筒、滑塊裝置、斜頂裝置、鋼珠套、日期章、塑膠模具彈簧、密封圈、冷卻接頭,水柱塞、定位圈、澆口套、拉料針、拉桿、限位釘、垃圾釘、支撐柱、開閉器、開模順序控制器(鎖模扣組件)等。
結構零件
1、組成
吹塑模、鑄塑模和熱成型模的結構較為簡單。
壓塑模、注塑模和傳塑模結構較為複雜,構成這類模具的零件也較多。
基本零件有:
①成型零件,包括凹模、凸模、各種成型芯,都是成型製品內、外表面或上、下端面、側孔、側凹和螺紋的零件。
②支承固定零件,包括模座板、固定板、支承板、墊塊等,用以固定模具或支承壓力。
③導向零件,包括導柱和導套,用以確定模具或推出機構運動的相對位置。
④抽芯零件,包括斜銷、滑塊等,在模具開啟時用以抽出活動型芯,使製品脫模。
⑤推出零件,包括推桿、推管、推塊、推件板、推件環、推桿固定板、推板等,用以使製品脫模。注塑模多推廣採用標準模架,這種模架是由結構、形式和尺寸都已標準化和系列化的基本零件成套組合而成,其模腔可根據製品形狀自行加工。採用標準模架有利於縮短制模周期。
2、常用模座零件作用
定模座板(面板):將前模固定在注塑機上.
流道板(水口板):開模時去除廢料柄,使其自動脫落(三板模).
定模固定板(A板):成型產品前模部分.
動模固定板(B板):成型產品後模部分.
墊塊:模腳,它的作用是讓頂板有足夠的活動空間.
推板:開模時通過頂桿、頂塊、斜頂等推出零件將產品從模具中推出.
動模座板(底板):將後模固定在注塑機上.
導柱和導套:起導向定位作用,輔助前後模開模、和模與基本定位.
支撐柱(撐頭):提高B板的強度,有效避免長期生產導致B板變形.
頂板導柱(中托司):導向定位推板,保證頂出順暢.
材料要求
塑膠模具的工作條件與冷沖模不同,一般須在150°C-200°C下進行工作,除了受到一定壓力作用外,還要承受溫度影響。現根據塑膠成型模具使用條件、加工方法的不同將塑膠模具用鋼的基本性能要求大致歸納如下:
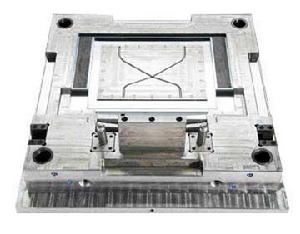
1、足夠的表面硬度和耐磨性
塑膠模的硬度通常在50-60HRC以下,經過熱處理的模具應有足夠的表面硬度,以保證模具有足夠的剛度。模具在工作中由於塑膠的填充和流動要承受較大的壓應力和摩擦力,要求模具保持形狀的精度和尺寸精度的穩定性,保證模具有足夠的使用壽命。模具的耐磨性取決於鋼材的化學成分和熱處理硬度,因此提高模具的硬度有利於提高其耐磨性。
2、優良的切削加工性
大多數塑膠成型模具,除EMD加工外還需進行一定的切削加工和鉗工修配。為延長切削刀具的使用壽命,提高切削性能,減少表面粗糙度,塑膠模具用鋼的硬度必須適當。
3、良好的拋光性能
高品質的塑膠製品,要求型腔表面的粗糙度值小。例如,注塑模型腔表面粗糙度值要求小於Ra0.1~0.25的水平,光學面則要求Ra<0.01nm,型腔須進行拋光,減小表面粗糙度值。為此選用的鋼材要求材料雜質少、組織微細均一、無纖維方向性、拋光時不應出現麻點或桔皮狀缺陷。
4、良好的熱穩定性
塑膠注射模的零件形狀往往比較複雜,淬火後難以加工,因此應儘量選用具有良好的熱穩定性的,當模具成型加工經熱處理後因線膨脹係數小,熱處理變形小,溫度差異引起的尺寸變化率小,金相組織和模具尺寸穩定,可減少或不再進行加工,即可保證模具尺寸精度和表面粗糙度要求。
45、50牌號的碳素鋼具有一定的強度與耐磨性,經調質處理後多用於模架材料。高碳工具鋼、低合金工具鋼經過熱處理後具有較高的強度和耐磨性,多用於成型零件。但高碳工具鋼因其熱處理變形大,僅適用於製造尺寸小、形狀簡單的成型零件。
隨著塑膠工業的發展,塑膠製品的複雜性、精度等要求愈來愈高,對模具材料也提出更高要求。對於製造複雜、精密和耐腐蝕性的塑膠模,可採用預硬鋼(如PMS)、耐蝕鋼(如PCR)和低碳馬氏體時效鋼(如18Ni-250),均具有較好的切削加工、熱處理和拋光性能及較高強度。
此外,在選擇材料時還須考慮防止擦傷與膠合,如兩表面存在相對運動的情況,則儘量避免選擇組織結構相同的材料,特殊狀況下可將一面施鍍或氮化,使兩面具有不同的表面結構。
材料選擇
1、塑膠模的工作條件
由於塑膠及塑膠成型工業的發展,對塑膠的模具的質量要求也越來越高,因而塑膠模具的失效問題及其影響因素已成為重要的研究課題。塑膠模的主要工作零件是成型零件,如凸模、凹模等,它們構成塑膠模的型腔,以成型塑膠製件的各種表面並直接與塑膠接觸,經受壓力、溫度、摩擦和腐蝕等作用。
2 、塑膠模材料失效原因分析
一般模具製造中包括模具設計、選用材料、熱處理、機械加工、調試與安裝等過程。根據調查表明:模具失效的因素中,模具所使用的材料與熱處理是影響使用壽命的主要因素。從全面質量管理的角度出發,不能把影響模具使用壽命的諸因素作為多項式之和來衡量,而應該是多因素的乘積,這樣,模具材料與熱處理的優劣在整個模具製造過程中就顯得特別重要。
從模具失效的普遍現象分析,塑膠模具在服役過程中,可產生磨損失效、局部性變形失效和斷裂失效。塑膠模具的重要失效形式可分為磨損失效、局部塑性變形失效和斷裂失效。
3、 塑膠模具鋼性能要求 隨著製造業快速發展,塑膠模具是塑膠成型加工中不可缺少的工具,在總的模具產量中所占的比例逐年增加,隨著高性能塑膠的發展和不斷生產,塑膠製品的種類日益增多,用途不斷擴大,製品向精密化、大型化、複雜化發展。成型生產向高速化發展,模具的工作條件也越趨複雜。
1)型腔表面的磨損和腐蝕
塑膠熔體以一定的壓力在模腔內流動,凝固的塑件從模具中脫出,都對模具成型表面造成摩擦,引起磨損。造成塑膠模具磨損失效的根本原因就是模具與物料間的摩擦。但磨損的具體形式和磨損過程則與許多因素有關,如模具在工作過程中的壓力、溫度、物料變形速度和潤滑狀況等。當塑膠模具使用的材料與熱處理不合理時,塑膠模具的型腔表面硬度低,耐磨性差,其表現為:型腔面因磨損及變形引起的尺寸超差;粗糙度值因拉毛而變高,表面質量惡化。尤其是當使用固態物料進入塑模型腔時,它會加劇型腔面的磨損。加之塑膠加工時含有氯、氟等成分受熱分解出腐蝕性氣體HC1、HF,使塑膠模具型腔面產生腐蝕磨損,導致失效。如果在磨損的同時又有磨損損傷,使型腔表面的鍍層或其他防護層遭到破壞,則將促進腐蝕過程。兩種損傷交叉作用,加速了腐蝕一磨損失效。
2)塑性變形失效
塑膠模型腔表面受壓、受熱可引起塑性變形失效,尤其是當小模具在大噸位設備上工作時,更容易產生超負荷塑性變形。塑膠模具所採用的材料強度與韌性不足,變形抗力低;塑性變形失效另一原因,主要是模具型腔表面的硬化層過薄,變形抗力不足或工作溫度高於回火溫度而發生相變軟化,而使模具早期失效。
3)斷裂
斷裂的主要原因是由於結構、溫差而產生的結構應力、熱應力或因回火不足,在使用溫度下,使殘餘奧氏體轉變成馬氏體,引起局部體積膨脹,在模具內部產生的組織應力所致。
塑膠模具的工作條件與冷沖模不同, 一般須在150℃-200℃下進行工作,除了受到一定壓力作用外,還要承受溫度影響。同一種模具會有多種失效形式,即使在同一個模具上也可能出現多種損傷。從塑膠模的失效形式可知,合理的選用塑膠模具材料和熱處理是十分重要的,因為它們直接關係到模具的使用壽命。所以,塑膠模具用鋼應滿足以下要求:
1)耐熱性能
隨著高速成型機械的出現,塑膠製品運行速度加快。由於成型溫度在200--350℃之間,如果塑膠流動性不好,成形速度又快,會使模具部分成型表面溫度在極短時間內超過400℃。為保證模具在使用時的精度及變形微小,模具鋼應有較高的耐熱性能。
2) 足夠耐磨性
隨著塑膠製品用途的擴大,在塑膠中往往需添加玻璃纖維之類的無機材料以增強塑性,由於添加物的加入,使塑膠的流動性大大降低,導致模具的磨損,故要求其具有良好的耐磨性。
3) 優良的切削加工性
大多數塑膠成型模具,除電火花加工還需進行一定的切削加工和鉗工修配。為延長切削刀具的使用壽命,在切削過程中加工硬化小。為避免模具變形而影響精度,希望加工殘餘應力能控制在最小限度。
4) 良好的熱穩定性
塑膠注射模的零件形狀往往比較複雜,淬火後難以加工,因此應儘量選用具有良好的熱穩定性的材料。
5)鏡面加工性能
型腔表面光滑,成型面要求拋光成鏡面,表面粗糙度低於Ra0.4μm,以保證塑膠壓製件的外觀並便於脫模。
6)熱處理性能
在模具失效事故中,因熱處理造成的事故一般是52.3%,以致熱處理在整個模具製造過程中占有重要的地位,熱處理工藝的好壞對模具質量有較大的影響。一般要求熱處理變形小,淬火溫度範圍寬,過熱敏感性小,特別是要有較大的淬硬性和淬透性等等。
7) 耐腐蝕性
在成形過程中可能放出腐蝕氣受熱分解出具有腐蝕性的氣體,如HC1、HF等腐蝕模具,有時在空氣流道口處使模具鏽蝕而損壞,故要求模具鋼有良好的耐蝕性。
4 、新型塑膠模具鋼
一般塑膠模具常採用正火態的45鋼或40Cr鋼經調質製造。硬度要求較高的塑膠模具採用CrWMn或Crl2MoV等鋼製造。對工作溫度較高的塑膠模具,可以選擇用韌性高的熱作模具鋼。為了滿足塑膠型腔對尺寸精度和表面質量的更高要求,新近又研製一系列新型模具鋼。
1)滲碳型塑膠模具鋼
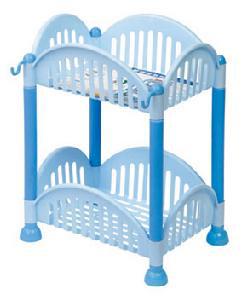
滲碳型塑膠模具鋼主要用於冷擠壓成型型腔複雜的塑膠模具,這類鋼的含碳量較 低,常加元素Cr,同時加入適量Ni、Mo和v,作用是提高淬透性和滲碳能力,為了便於冷擠壓成形,這類鋼在退火狀態須有高的塑性和低的變形抗力,退火硬度≤1 00HBS。在冷擠壓成形後進行滲碳和淬火回火處理,表面硬度可達58---62HRC。此類鋼國外有專用鋼種,如瑞典的8416、美國的P2和P4等。國內常採用12CrNi3A和12Cr2Ni4A鋼、20Cr2Ni4A,耐磨性好,無塌陷及表面剝落現象,模具壽命提高。鋼中元素cr,Ni、Mo、V增加滲碳層的硬度和耐磨性及心部的強韌性。
2)預硬型塑膠模具鋼
這類鋼的含碳量為0.3% -O.55%,常用合金元素有Cr、Ni、Mn、v等。為了改善其切削性,加入s、ca等元素.通過研製、引進又發展了幾種典型塑膠模具鋼Y55CrNiMn-MoVS(SMI)是中國研製的含S系易切削塑膠模具鋼,其特點是預硬態交貨硬度為35_40 HRC,有較好的切削加工性,加工後不再熱處理,可直接使用。加人Ni固溶強化並增加韌性,加入Mn與S形成易切削相MnS;加入Cr、Mo、V,增加鋼的淬透性 8Cr2S鋼就足屬於易切削精密模具用鋼。
3)時效硬化型塑膠模具鋼
開發了低鈷、無鈷、低鎳的馬氏體時效鋼,MASI是一種典型的馬氏時效鋼。經8150C固溶處理後,硬度為28—32HRC,叮進行機械加工,再經4800C時效,時效時折出Ni3Mo、Ni3Ti等金屬間化合物,使硬度達到48—52 HRC。鋼的強韌性高、時效時尺寸變化小、焊補性能好,但鋼的價格昂貴、在國內不太受歡迎。
4)耐蝕塑膠模具鋼
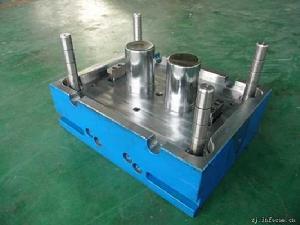
以聚氯乙烯(Pvc)及ABS加抗燃樹脂為原料的塑膠製品,在成形過程中分解產 生腐蝕性氣體,會腐蝕模具。因此,要求塑膠模具鋼具有很好的耐蝕性能。國外常用耐蝕塑模鋼有馬氏體不鏽鋼和析出硬化型不鏽鋼兩類。國外的有如瑞典ASSAB公司的STVAX(4Crl3)和A SSAB一8407等。
模具產品
介紹
我們日常生產、生活中所使用到的各種工具和產品,大到工具機的底座、機身外殼,小到一個胚頭螺絲、紐扣以及各種家用電器的外殼,無不與模具有著密切的關係。模具的形狀決定著這些產品的外形,模具的加工質量與精度也就決定著這些產品的質量。因為各種產品的材質、外觀、規格及用途的不同,模具分為了鑄造模、鍛造模、壓鑄模、衝壓模等非塑膠模具,以及塑膠模具。
技術套用

1、如:家用電器、儀器儀表,建築器材,汽車工業、日用五金等眾多領域,塑膠製品所占的比例正迅猛增加。一個設計合理的塑膠件往往能代替多個傳統金屬件。工業產品和日用產品塑膠化的趨勢不斷上升。
2、模具的一般定義:在工業生產中,用各種壓力機和裝在壓力機上的專用工具,通過壓力把金屬或非金屬材料制出所需形狀的零件或製品,這種專用工具統稱為模具。
3、注塑過程說明:模具是一種生產塑膠製品的工具。
4、模具的一般分類:可分為塑膠模具及非塑膠模具:
⑴非塑膠模具有:鑄造模、鍛造模、衝壓模、壓鑄模等。
A.鑄造模——水龍頭、生鐵平台
B.鍛造模——汽車身
C.衝壓模——計算機面板
D.壓鑄模——超合金,汽缸體
⑵塑膠模具根據生產工藝和生產產品的不同又分為:
A.注射成型模——電視機外殼、鍵盤按鈕(套用最普遍)
B.吹氣模——飲料瓶
C.壓縮成型模——電木開關、科學瓷碗碟
D.轉移成型模——積體電路製品
E.擠壓成型模——膠水管、塑膠袋
F.熱成型模——透明成型包裝外殼
G.旋轉成型模——軟膠洋娃娃玩具
◆ 注射成型是塑膠加工中最普遍採用的方法。該方法適用於全部熱塑性塑膠和部分熱固性塑膠,製得的塑膠製品數量之大是其它成型方法望塵莫及的,作為注射成型加工的主要工具之一的注塑模具,在質量精度、製造周期以及注射成型過程中的生產效率等方面水平高低,直接影響產品的質量、產量、成本及產品的更新,同時也決定著企業在市場競爭中的反應能力和速度。
◆注塑模具是由若干塊鋼板配合各種零件組成的,基本分為:
A 成型裝置(凹模,凸模)
B 定位裝置(導柱,導套)
C 固定裝置(工字板,碼模坑)
D 冷卻系統(運水孔)
E 恆溫系統(加熱管,發熱線)
F 流道系統(唧咀孔,流道槽,流道孔)
G 頂出系統(頂針,頂棍)
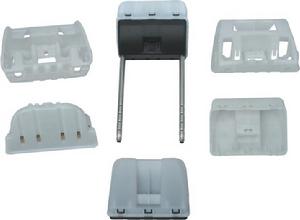
5、根據澆注系統型制的不同可將模具分為三類:
⑴ 大水口模具:流道及澆口在分模線上,與產品在開模時一起脫模,設計最簡單,容易加工,成本較低,所以較多人採用大水口系統作業。
⑵ 細水口模具:流道及澆口不在分模線上,一般直接在產品上,所以要設計多一組水口分模線,設計較為複雜,加工較困難,一般要視產品要求而選用細水口系統。
⑶熱流道模具:此類模具結構與細水口大體相同,其最大區別是流道處於一個或多個有恆溫的熱流道板及熱唧嘴裡,無冷料脫模,流道及澆口直接在產品上,所以流道不需要脫模,此系統又稱為無水口系統,可節省原材料,適用於原材料較貴、製品要求較高的情況,設計及加工困難,模具成本較高。
熱流道系統,又稱熱澆道系統,主要由熱澆口套,熱澆道板,溫控電箱構成。我們常見的熱流道系統有單點熱澆口和多點熱澆口二種形式。單點熱澆口是用單一熱澆口套直接把熔融塑膠射入型腔,它適用單一腔單一澆口的塑膠模具;多點熱澆口是通過熱澆道板把熔融料分枝到各分熱澆口套中再進入到型腔,它適用於單腔多點入料或多腔模具.
流道系統的優勢
⑴無水口料,不需要後加工,使整個成型過程完全自動化,節省工作時間,提高工作效率。
⑵壓力損耗小。熱澆道溫度與注塑機射嘴溫度相等, 避免了原料在澆道內的表面冷凝現象,注射壓力損耗小。
⑶水口料重複使用會使塑膠性能降解,而使用熱流道系統沒有水口料,可減少原材料的損耗,從而降低產品成本。在型腔中溫度及壓力均勻,塑件應力小,密度均勻,在較小的注射壓力下,較短的成型時間內,注塑出比一般的注塑系統更好的產品。對於透明件、薄件、大型塑件或高要求塑件更能顯示其優勢,而且能用較小機型生產出較大產品。
⑷熱噴嘴採用標準化、系列化設計,配有各種可供選擇的噴嘴頭,互換性好。獨特設計加工的電加熱圈,可達到加熱溫度均勻,使用壽命長。熱流道系統配備熱流道板、溫控器等,設計精巧,種類多樣,使用方便,質量穩定可靠。
熱流道系統套用的不足之處
⑴整體模具閉合高度加大,因加裝熱澆道板等,模具整體高度有所增加。
⑵熱輻射難以控制,熱澆道最大的毛病就是澆道的熱量損耗,是一個需要解決的重大課題。
⑶存在熱膨脹,熱脹冷縮是我們設計時要考慮的問題。
⑷模具製造成本增加,熱澆道系統標準配件價格較高,影響熱澆道模具的普及。
常用軟體
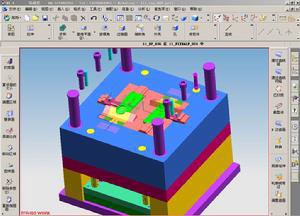
PTC的EMX,Siemens的NX Mold Wizard,CimatronE,Topsoi ld,Delcam Moldmaker,Missler 的Topsolid Mold,Think3的Mold Design,Manusoft的IMOLD,R&B的MoldWorks,Solidworks,Pro-e,UG(後三種主要是產品設計,但是可以做到模具設計集成)等。
拋光過程
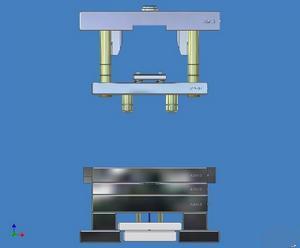
塑膠模具拋光基本程式 要想獲得高質量的拋光效果,最重要的是要具備有 高質量的油石、砂紙和鑽石研磨膏等拋光工具和輔助品。
塑膠模具拋光的一般過程如下:
1、精拋
精拋主要使用鑽石研磨膏。若用拋光布輪混合鑽石研磨粉或研磨膏進行研磨的話,則通常的研磨順序是9μm(#1800)~ 6μm(#3000)~3μm(#8000)。9μm的鑽石研磨膏和拋光布輪可用來去除#1200和#1500號砂紙留下的髮狀磨痕。接著用粘氈和鑽石研磨膏進行拋光,順序為1μm(#14000)~ 1/2μm(#60000)~1/4μm(#100000)。精度要求在1μm以上(包括1μm)的拋光工藝在模具加工車間中一個清潔的拋光室內即可進行。若進行更加精密的拋光則必需一個絕對潔淨的空間。灰塵、煙霧,頭皮屑和口水沫都有可能報廢數個小時工作後得到的高精密拋光表面。
2、粗拋
經銑、電火花、磨等工藝後的表面可以選擇轉速在35 000—40 000 rpm的旋轉表面拋光機或超音波研磨機進行拋光。常用的方法有利用直徑Φ3mm、WA # 400的輪子去除白色電火花層。然後是手工油石研磨,條狀油石加煤油作為潤滑劑或冷卻劑。一般的使用順序為#180 ~ #240 ~ #320 ~ #400 ~ #600 ~ #800 ~ #1000。許多模具製造商為了節約時間而選擇從#400開始。
3、半精拋
半精拋主要使用砂紙和煤油。砂紙的號數依次為:#400 ~ #600 ~ #800 ~ #1000 ~ #1200 ~ #1500。實際上#1500砂紙只用適於淬硬的模具鋼(52HRC以上),而不適用於預硬鋼,因為這樣可能會導致預硬鋼件表面燒傷。
⒋精拋
用研磨膏進行精拋,8000,10000就達到鏡面了。
拋光方法
機械拋光
機械拋光是靠切削、材料表麵塑性變形去掉被拋光後的凸部而得到平滑面的拋光方法,一般使用油石條、羊毛輪、砂紙等,以手工操作為主,特殊零件如迴轉體表面,可使用轉台等輔助工具,表面質量要求高的可採用超精研拋的方法。超精研拋是採用特製的磨具,在含有磨料的研拋液中,緊壓在工件被加工表面上,作高速旋轉運動。利用該技術可以達到Ra0.008μm的表面粗糙度,是各種拋光方法中最高的。光學鏡片模具常採用這種方法。
化學拋光
化學拋光是讓材料在化學介質中表面微觀凸出的部分較凹部分優先溶解,從而得到平滑面。這種方法的主要優點是不需複雜設備,可以拋光形狀複雜的工件,可以同時拋光很多工件,效率高。化學拋光的核心問題是拋光液的配製。化學拋光得到的表面粗糙度一般為數10μm。
電解拋光
電解拋光基本原理與化學拋光相同,即靠選擇性的溶解材料表面微小凸出部分,使表面光滑。與化學拋光相比,可以消除陰極反應的影響,效果較好。電化學拋光過程分為兩步:⑴巨觀整平 溶解產物向電解液中擴散,材料表面幾何粗糙下降,Ra>1μm。⑵微光平整 陽極極化,表面光亮度提高,Ra<1μm。
超音波拋光
將工件放入磨料懸浮液中並一起置於超音波場中,依靠超音波的振盪作用,使磨料在工件表面磨削拋光。超音波加工巨觀力小,不會引起工件變形,但工裝製作和安裝較困難。超音波加工可以與化學或電化學方法結合。在溶液腐蝕、電解的基礎上,再施加超音波振動攪拌溶液,使工件表面溶解產物脫離,表面附近的腐蝕或電解質均勻;超音波在液體中的空化作用還能夠抑制腐蝕過程,利於表面光亮化。
流體拋光
流體拋光是依靠高速流動的液體及其攜帶的磨粒沖刷工件表面達到拋光的目的。常用方法有:磨料噴射加工、液體噴射加工、流體動力研磨等。流體動力研磨是由液壓驅動,使攜帶磨粒的液體介質高速往複流過工件表面。介質主要採用在較低壓力下流過性好的特殊化合物(聚合物狀物質)並摻上磨料製成,磨料可採用碳化矽粉末。
磁研磨拋光
磁研磨拋光是利用磁性磨料在磁場作用下形成磨料刷,對工件磨削加工。這種方法加工效率高,質量好,加工條件容易控制,工作條件好。採用合適的磨料,表面粗糙度可以達到Ra0.1μm。2 機械拋光基該方法 在塑膠模具加工中所說的拋光與其他行業中所要求的表面拋光有很大的不同,嚴格來說,模具的拋光應該稱為鏡面加工。它不僅對拋光本身有很高的要求並且對表面平整度、光滑度以及幾何精確度也有很高的標準。表面拋光一般只要求獲得光亮的表面即可。鏡面加工的標準分為四級:AO=Ra0.008μm,A1=Ra0.016μm,A3=Ra0.032μm,A4=Ra0.063μm,由於電解拋光、流體拋光等方法很難精確控制零件的幾何精確度,而化學拋光、超音波拋光、磁研磨拋光等方法的表面質量又達不到要求,所以精密模具的鏡面加工還是以機械拋光為主。
基本程式
要想獲得高質量的拋光效果,最重要的是要具備有高質量的油石、砂紙和鑽石研磨膏等拋光工具和輔助品。而拋光程式的選擇取決於前期加工後的表面狀況,如機械加工、電火花加工,磨加工等等。
模具發展
中國全年塑膠模具產值達534億元人民幣左右?你相信嗎?由於中國經濟的高速發展對塑膠模具工業的要求是越來越嚴格,因此為塑膠模具工業的發展提供了巨大的動力。據準確數據統計,中國全年塑膠模具產值達534億元人民幣,這是一個已經存在的事實。
隨著汽車製造業和IT製造業的飛速發展,國內模具工業取得了飛速發展,據了解,我國模具行業中塑膠模具的占比可達30%,預計在未來模具市場中,塑膠模具占模具總量的比例仍將逐步提高,且發展速度將快於其他模具。
據悉,模具工業2000年以來以每年20%的速度飛速增長,拉動了模具檔次的提高,精良的模具製造裝備為模具技術水平的提升提供了保障。
分析認為,由於進口模具中,精密、大型、複雜、長壽命模具占多數,所以,從減少進口、提高國產化率角度出發,這類高檔模具在市場上的份額也將逐步增大。建築業的快速發展,使各種異型材擠出模具、PVC塑膠管材接頭模具成為模具市場新的經濟成長點,高速公路的迅速發展,對汽車輪胎也提出了更高要求,因此子午線橡膠輪胎模具,特別是活絡模的發展也將高於總平均水平;以塑代木,以塑代金屬使塑膠模具在汽車、機車工業中的需求量巨大;家用電器行業在“十二五”期間將有較大發展,特別是電冰櫃、空調器和微波爐等的零配件的塑膠模需求很大
同時,塑膠模具行業結構調整步伐在不斷加快,面向市場的專業塑膠模具廠家得數量及能力也在較快增長。根據對塑膠模具製造行業的生產、銷售、市場情況、行業結構、產品以及進出口等情況分析,參考塑膠模具相關行業發展趨勢,預測未來我國塑膠模具製造行業的發展方向究竟在哪裡,到底我國塑膠模具製造行業有多大的發展潛力,這些都是需要去驗證的。