硫的來源
硫是鋼鐵產品中的有害雜質,它使鋼材在加工中產牛熱脆,降低鋼材的強度和力學性能。因此,在鋼鐵冶煉的各個階段都要努力降低它的含量,減少它的危害。由於高爐冶煉中脫硫的條件比煉鋼階段更為有利,所以降低鐵水硫含量便成為煉鐵工作者的一項重要任務。
高爐中的硫來自入爐原燃料。在使用人造富礦時,礦石帶入的硫以FeS形態存在;而天然礦多為FeS,也有以硫酸鹽形態存在的。由於燒結和球團過程有脫硫作用,礦石帶入的硫量已經不多了。高爐燃料中的硫是硫的主要來源,占入爐總硫量的80%以上,焦炭、煤粉中的硫主要以有機物形態存在,而無機物形態的硫不多。冶煉1t生鐵由爐料帶入的硫量稱為硫負荷。通常情況下硫負荷在6~8kg/t,使用硫含量高的焦炭時硫負荷能夠達到10kg/t以上,不過這種情況現時已不多了。
爐內的分布
硫與鐵能生成低熔點的化合物,並與鐵水很好地相溶,故無機物形態的硫都容易進入鐵水之中。焦炭的有機物形態硫在受熱過程中會逐漸釋放出來,其中少部分在高爐中上部以氣態物質進入煤氣,而較多部分及煤粉中硫在風門前碳燃燒時也能反應生成氣態化合物( SiS、HS、CS、COS等),在隨煤氣上升的過程中,與下降的爐料和滴落的渣鐵相遇而被吸收。爐料中鹼性熔劑越多,渣量越大,流動性越好,吸收的硫也越多。被爐料吸收的硫下降到燃燒帶後,將再次燃燒氣化、上升循環。
由高爐解剖資料可知,軟熔帶、滴落帶的硫量多於爐料帶入的硫量,說明爐內高溫及中溫區域之間存在著硫的循環過程。高爐冶煉實踐表明,通常有5%~10%的硫進入煤氣逸出爐外,5%左右的硫進入生鐵,其餘進入爐渣。進入生鐵的硫量是高爐冶煉重要的控制目標。
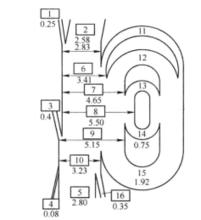
降低負荷措施
1、採用硫含量低的礦石、焦炭,儘量減少硫負荷,這是最為理想的,但要受到高爐所用原料資源條件的限制。在人爐前的準備處理階段,必須努力改善原料的質量。現今的鐵礦石經燒結或球團工藝,礦石硫含量已經很少了,礦石帶進的硫量僅占硫負荷的1/5左右。焦炭(及煤粉)帶進的硫量比礦石多,選用硫含量低的燃料對降低高爐硫負荷是大有作用的。但煤的洗選只能夠減少灰分中的硫,有機物質中的硫去不掉,而這又占煤中硫的絕大部分,在煉焦時轉成焦炭中的硫,所以煉焦用煤的硫含量決定了焦炭的硫含量。
2、增加煤氣帶走的硫量有利於降低生鐵硫含量。煤氣帶走的硫量與許多因素有關,如硫存在的形態、爐內的溫度分布、煤氣的數量、爐渣的鹼度等,不能單純為降低生鐵硫含量而增加煤氣量,或降低爐渣鹼度以求減少爐料攔截吸收硫的機會,實際上煤氣帶走的硫量也是有限的。
3、增加渣量也可以降低生鐵的硫含量,但高爐冶煉也不能為降低生鐵硫含量而增加渣量。因為渣量的增加會消耗更多的熱量,要求有更大的焦比,而焦比的增加會帶進更多的硫量。
因此,要降低生鐵硫含量,需要增大硫在渣、鐵問的分配係數。高爐冶煉實踐表明,努力改善爐渣脫硫的熱力學和動力學條件,增大爐渣的脫硫能力,是降低生鐵硫含量最為有效的措施。