簡介
爐料是指加入冶煉爐的礦石和其他催化材料,例如,鐵礦石,鋼坯,生鐵,廢鋼鐵,焦煤,鐵合金。將精礦或礦石、熔劑和煙塵等按冶煉要求配製成具有一定化學組成和物理性質的爐料的過程,為現代火法冶金流程的重要組成部分。爐料準備一般包括貯存、配料、混合、爐料乾燥、爐料制粒、爐料制團、煅燒及焙燒等。

將精礦或礦石 、熔劑和煙塵等按冶煉要求配製成具有一定化學組成和物理性質的爐料的過程,為現代火法冶金流程的重要組成部分。爐料準備一般包括貯存、配料、混合、爐料乾燥、爐料制粒、爐料制團、煅燒及焙燒等。除煅燒及焙燒使爐料發生化學變化外,其他過程一般只發生物理變化。
由精礦、返料、煙塵、熔劑等組成的爐料,其物理狀態、化學成分、含水量以及數量,不一定能滿足冶煉工藝的要求。為了保證正常生產,就需要貯存足夠一段時間使用的原料和熔劑等。冶煉廠常處理多個礦山或選廠的礦石及精礦,必須進行配料將各種精礦按一定比例配合使用,並混合成化學成分、物理性比較一致的原料。進廠精礦一般含水8%~15%,而煉前爐料準備、冶煉過程及其煙氣處理都要求精礦含有較低的水分而需經過乾燥處理。某種原料,對於作為某一冶煉過程來說,其粒度可能太細需要配入粘結劑制粒,或其透氣性不夠好,必須配入粘結劑製成團塊。氧化物常比硫化物易於還原,金屬的硫酸鹽、氯化物或氧化物更易從原料中浸出,因而常需要通過煅燒與焙燒的化學方法,將原料中的礦物轉變成所需要的形式。例如:藉助煅燒使CaCO3轉變成CaO和CO2;通過焙燒,使金屬硫化物轉變成金屬氧化物或金屬硫酸鹽。對於某一具體原料而言,究竟需要經過哪些準備過程,則視原料本身情況和冶煉工藝要求而定。
爐料貯存
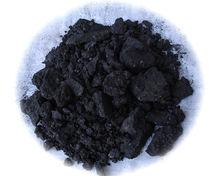
冶煉廠的主要原料,有價金屬含量高,貯存在有蓋倉庫內,防止飛揚和流失,在寒冷地區還要採取保溫防凍措施。在保證正常生產的前提下,確定最少精礦貯存量是一個重要的經濟技術問題。最少精礦貯存量與冶煉廠日處理量和精礦的貯存天數有關。精礦的貯存時間則決定於冶煉工藝及其工作制度,大檢修的配合,交通運輸等條件。一般冶煉廠精礦的貯存時間可取15~20d,連續性強的冶煉工藝精礦貯存時間可適當延長,以便完成配料前的初混、取樣化驗等準備工作,使精礦成分較為穩定,減輕配料工序的負荷。季節性生產的小型冶煉廠,應考慮停產期間精礦的貯存。交通運輸條件較差,如枯水季節不能水運等,則應適當增加貯存時間。
返回處理的煙塵要貯存於貯礦倉庫內,其最少貯存量及貯存時間取決於其產率和配料方法及其制度,常取7~10d。某些富集了稀散金屬的煙塵,送單獨處理工序去貯存。
煉鉛鼓風爐爐料常配入爐渣是為了改善冶煉操作條件,其貯礦倉容量取1~2d即可。當需用石灰配料時,無疑要貯存於貯礦倉內。
冶煉所用石灰石、石英等熔劑常露天貯存,一般依運輸距離和條件,選取1~2周時間的貯量。
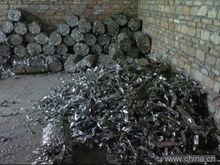
現代火法冶金的另一類爐料是各種二次金屬原料。依據冶煉工藝流程、二次金屬原料來源、性狀及其製備工藝的不同,可選擇其作為某冶煉過程的爐料來考慮其貯存量。
爐料混合
配合料的充分混合,也是爐料準備的一個不可缺少的環節。混合的目的是使配合料的成分均勻。混合可以在圓筒混合機進行,也有在輪式混合機內進行的。迴轉圓筒作圓周運動時,爐料靠它自身與內壁產生的摩擦力被帶到一定高度,然後在重力作用下離開內壁被拋落到筒底,如此往復運動。在拋落過程中物料相互衝擊混合攪拌,成分逐漸均勻。物料在輪式混合機中混合的過程是:當輪子轉動時,物料從一定高度落到混合輪上,被鏇轉的鋼棒打成散亂狀態,得到混勻。
煉鉍冶金爐料
煉鉍冶金爐的爐料包括鉍精礦、氧化鉍渣、煤粉、鐵屑、純鹼、螢石、黃鐵礦、返渣等,根據配料比的要求投入爐內。
一、鉍精礦
鉍精礦包括硫化鉍精礦與氧化鉍精礦,是提鉍的主要原料,在冶金爐熔煉中,鉍精礦參與的反應是複雜的。
二、氧化鉍渣
一般指鉛陽極泥氧化除鉍產出的渣料。根據回收金銀的傳統流程,鉛陽極泥經還原熔煉產出貴鉛,貴鉛在分銀爐氧化吹煉中,脫除砷、銻後繼續吹風氧化,則鉍與鉛皆氧化入渣。氧化渣分為前期渣,中期渣、後期渣,前期渣含鉛高,含鉍低,後期渣含鉍高,含鉛低。三者合稱氧化鉍渣,一般含鉍在35%~55%之間。氧化鉍渣是綜合回收鉍的主要原料之一。
三、煤粉
煤粉用作還原劑。加入煤粉作用如下:
(1)使氧化鉍還原。
(2)起部分脫硫作用:
(3)保持爐內還原性氣氛,防止鉍液氧化,防止爐膛內特別是爐頂耐火材料氧化腐蝕。
(4)防止碲氧化入渣,而使碲富集於粗鉍之中。
煤粉加入量必須恰當,過多過少都會帶來不良的後果。當加煤粉過量時,使其它對氧的親和力較鉍為大的雜質金屬也被還原進入粗鉍,降低粗鉍的品位。同時,由於碳的熔點高(3700℃),碳加入過量,會提高爐料的熔點和粘度,使爐料難熔化。當煤粉不足時,氧化鉍還原不充分,造成部分氧化鉍入渣,提高了渣含鉍,增大鉍的損失,並且,無法維持爐內穩定的還原性氣氛。
鐵合金:
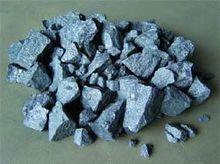
生鐵 :
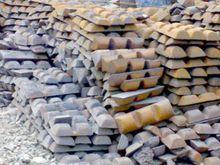
焦煤:
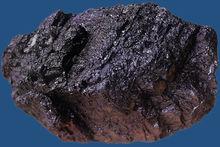
鋼坯:
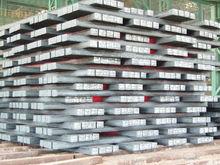
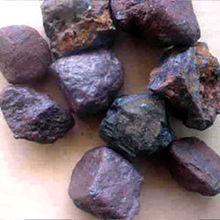
鐵礦石:
廢鋼鐵:
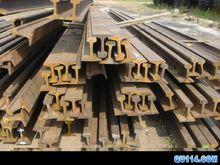