提出和發展
濕式燃燒最初由美國的Zimmermann於1958年研究提出,用於處理造紙黑液,其工作條件是控制反應溫度為150-350 ℃ ,壓力為5-20MPa,處理後廢水COD去除率可達90%以上。
在20世紀70年代以前,濕式燃燒主要用於城市污泥的處置、造紙黑液中鹼液的回收、活性炭的再生等。
進入70年代以後,濕式燃燒得到迅速發展,套用範圍從回收有用化學品和能量進一步擴展到有毒有害廢棄物的處理,尤其是在處理含酚、磷、氰等有毒有害物質方面已有大量文獻報導,研究內容也從初始的適用性和摸索最佳工藝條件深入到反應機理及動力學,而且裝置數目和規模也有所增大。
國內從80年代才開始進行濕式燃燒工藝的研究。
分類
已經開發的濕式燃燒有酸煮解和過氧化氫催化氧化兩種類型。
酸煮解
酸煮解(acid digestion)又稱酸消化,是用熱濃硫酸和硝酸(250℃)浸煮可燃固體廢物,將有機物分解成簡單的氣體組分,把大部分無機物轉變為硫酸鹽和氧化物。有機物的化學分解包括有機物碳化和碳化物進一步氧化兩個步驟,其化學化應是很複雜的。
1、硫酸的作用
硫酸的主要作用有兩個:
一是把有機物碳化;二是為硝酸的氧化提供高溫介質。
硫酸雖然也能把碳氧化,但反應速度較慢,因此需要加入硝酸。碳化物的氧化主要是靠硝酸來完成的。硝酸還把硫酸分解有機物形成的SO氧化成SO。破壞分解聚氯乙烯、聚乙烯、有機玻璃、橡膠等物質,需要較高的溫度,但溫度超過270℃會產生大量的SO氣溶膠,使尾氣處理變得困難,並使聚四氟乙烯密封填圈發生軟化,導致漏氣,因此反應溫度控制在250℃為宜。
2、工藝過程
酸煮解工藝由四部分組成:
(1)預處理(包括廢物的監測、分類和切割),這是類同乾法氧化焚燒的進料準備。
(2)酸浸煮:浸煮器的作用類似於焚燒爐的燃燒室。要求廢物同酸密切接觸,迅速而完全氧化。
(3)尾氣處理:尾氣主要組成是CO、SO、SO、NO、N、HCI、Cl、NOCI、CO和水蒸氣。尾氣淨化主要設備為:
霧沫分離器——回收硫酸;
鹼洗滌塔——氧化和吸收SO、NO和HCl;
HEPA過濾器。
(4)殘渣處理:用蒸餾法去除HSO,殘渣可回收Pu。回收方法是用稀硝酸浸漬出Pu,然後用TBP/正十二烷或用三乙基甲基胺萃取。分離出來的殘渣需要固化處理後才能處置。
3、優點
酸浸煮法有以下優點:
(1)減容比大,對含氯量30%(質量分數)廢物約80,對廢離子交換樹脂約70。
一個每天生產100kg混合氧化物燃料工廠,一年產生大約1200桶(( 200 L/桶)固體可燃性α廢物,用本法處理後只有24桶殘渣;
(2)能處理聚氯乙烯、聚乙烯、橡膠、纖維、樹脂、木材等多種廢物,尤其可處理高氯廢物;
(3)大於95%鈽能被回收,適於處理含鈽量高的廢物;
(4)大於95%HSO,70%~80%HNO能回收再用,二次廢液少;
(5)操作溫度和壓力低,容易控制和調節,易啟動和停車。不產生焦油、煙良和塵埃。
4、缺點
(1)對α廢物必須重視臨界安全,浸煮器中需加中子毒物,受臨界限制,處理量小。但處理β/γ廢物,不存在臨界問題,浸煮器體積和形狀可自由選擇,處理量可大大提高;
(2)腐蝕性大,對設備材料要求高。
酸煮解處理α固體廢物是美國、西德、日本、英國在20世紀70年代和80年代初開發研究的技術,在比利時已用它處理過前歐化公司積存的α廢物。
過氧化氫催化氧化
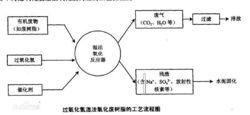
過氧化氫催化氧化(HO-catalyst oxidation)是20世紀80年代開發研究的技術,主要為了處理廢離子交換樹脂。離子交換樹脂的過氧化氫催化氧化反應的特點是自由基鏈式反應。
日本原研、東電、日揮聯合開發的HO(Fe )濕式燃燒工藝,採用35%HO,催化劑為500 ppm的Fe 。反應介質為水,反應時間2~5h,總有機物分解率95%,反應溫度100℃,常壓下進行,放射性物質進入尾氣系統少,反應器材料為鈦,冷凝器材料為不鏽鋼。廢樹脂分解成二氧化碳、水和少量無機殘液。無機殘液經濃縮後可水泥固化。
比較
幾種濕式燃燒中,酸煮解主要用來處理α廢物(超鈾廢物),己用它完成比利時歐化公司的處理任務。日本日揮公司(JGC)和中國清華大學開發的過氧化氫催化氧化法,主要為處理放射性廢樹脂。JGC開發的濕法氧化技術早已完成了工程驗證。幾種濕法氧化處理廢樹脂方法比較如下表所示。由表可以看出,過氧化氫催化氧化具有更多的優點。
氧化介質 | 溫度/℃ | 樹脂分解率/% | 廢氣主要成分 | 設備材質 |
雙氧水-二價鐵離子 | 100 | ~95 | 二氧化碳、水 | 鈦鋼 |
硫酸-雙氧水 | 230 | ~90 | 硫化物 | 鉭 |
硫酸-硝酸 | 230~250 | ~80 | 氮化物、硫化物 | 鉭 |