簡介
渦輪發動機葉片一般承受較大的工作應力和較高的工作溫度, 且應力和溫度的變化也較頻繁和劇烈,此外還有腐蝕和磨損問題 ,其對工作條件的要求非常苛刻 , 因此要求葉片的加工精度很高。同時 ,為提高渦輪效率,渦輪葉片的表面形狀通常設計成扭曲的變截面曲面, 形狀複雜。因而 , 渦輪葉片的精確幾何造型就成了渦輪加工的必要前提。渦輪葉片幾何造型實質就是要找到一種既能有效地滿足形狀表示和幾何設計要求 ,又便於形狀信息和產品數據交換的數學方法來描述渦輪葉片曲面。
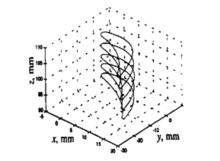
幾何造型用的渦輪葉片原始數據為根據流體動力學原理計算出來的沿葉高方向上的截面型值點數據 。在圖一中給出了葉片在葉高方向的5個截面 。
大型燃氣渦輪葉片冷卻技術
近年來,隨著大型燃氣輪機性能的不斷提高,為進一步減少有效氣體的消耗.提出了汽霧兩相流冷卻方案,即渦輪葉片由空氣冷卻逐漸轉向空氣和蒸汽雙工質冷卻,現已日益成為研究的熱點。大量研究表明,汽霧冷卻具有冷卻快、冷效高、流阻小和結構簡單等優點,將在下一代高性能燃氣輪機的渦輪葉片冷卻中發揮重要作用。通過對帶衝擊氣膜結構冷卻的數值模擬,平均冷卻效率明顯提高,且低溫區明顯延長。
燃氣輪機作為大型動力裝置,廣泛套用於發電及各種工業領域。其主要性能指標為系統循環熱效率和輸出功率,均隨渦輪轉子燃氣進口溫度的增加而增加;據計算,RIT在1073—1273 K範圍內每提高100度。燃氣輪機的輸出功率將增加20%~25%,節省燃料6%一7%。燃氣輪機性能的不斷提高,關鍵在於RIT的提高,而RIT的增加要考慮燃氣輪機熱端部件材料的耐溫程度和低NO戈排放量。RIT遠高於渦輪葉片金屬材料的熔點,尤其下一代燃氣輪機將以氫氣和人造氣為燃料,RIT將會更高,所以冷卻必不可少。先進的冷卻技術可使熱端部件能承受更高的工作溫度,提高燃氣輪機的循環熱效率,延長燃氣輪機的使用壽命,提高了系統工作的安全可靠性。據推算,如果無冷卻導向葉片材料的使用溫度能達到1470 K,則該導向葉片採用內部對流冷卻時,可使渦輪進口溫度提高到2200 K。由此可見,開展葉片冷卻技術的研究具有十分重要的意義。
輪葉片冷卻技術發展
早期的渦輪葉片沒有採用冷卻技術,由於受葉片材料的限制,RIT難以超過1323 K。隨著冷卻技術和耐高溫複合材料的發展,20世紀50年代有冷卻的RIT最高為1203 K,到了60年代,採用了氣冷式渦輪後R1T突破了1273 K,到60年代末R1T達到1423 K,十年內R1T提高493 K,70年代和80年代初的RIT增加到1643 K,十年內又增加了493K,如圖l所示。隨著冷卻技術的日益成熟。已形成了多種基本的渦輪葉片空氣冷卻技術引。
航空發動機渦輪葉片的多學科設計最佳化
在傳統渦輪葉片設計中,一般遵循以下一個過程先由總體性能部門定出葉片所要達到的性能指標,然後由結構設計部門進行設計,設計出達到氣動性能要求的葉片後,移交強度計算部門進行強度~振動~壽命計算,如合格,則葉片設計就告一段落,如不合格,則由設計部門重新進行設計,然後由強度部門進行計算,如此循環,達到要求為止,這樣的設計不僅僅周期長,而且也很難找到葉片最佳設計形狀,不符合現代航空發動機研製發展要求。
本文 提出採用多學科設計最佳化方法(MDO)進行單級實心渦輪動葉設計,多學科設計最佳化是一門新興的交叉科學,是航空航天科技飛速發展的產物,將MDO開闢為一個新的研究領域是近二十年的事情,九十年代國際上,尤其是美國在MDO領域展開了積極的探索研究,每年都有大量與該領域相關的研究論文發表;當前,MDO是國際上飛行器設計方法研究中的一個最新~最活躍的領域,但在航空發動機領域的研究和套用非常少,對航空發動機渦輪葉片,由於工作環境非常惡劣,不僅承受高速旋轉的離心力,同時還承受氣流流場~溫度場等的作用力,因此,其分析將涉及到氣動\傳熱\結構\強度\振動等多個學科,是典型的多學科設計問題,有必要藉助多學科設計最佳化方法進行設計G多學科設計最佳化方法可同時考慮各學科的影響,藉助現代計算機技術,在短時間內分析比較成百上千個設計方案,預先淘汰絕大多數非優方案,一步步逼近多學科整體最優解,從而有效的提高設計質量並大大加快設計進度。