人物生平
企業先後引進生產大切諾基、帕傑羅、歐藍德、克萊斯勒300C等國際著名品牌。在這一進程中,曾鵬不斷運用精益思想探索班組管理新方法,為四個新產品高質量地投產做出了重大貢獻。他和工友們的智慧和能力,一次又一次創造出“國產”裝配質量超越“原裝”的奇蹟。
質量控制
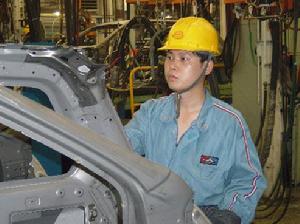
2001年,企業從美國克萊斯勒公司引進生產大切諾基。5月,曾鵬被抽調到大切諾基生產線當班長。大切諾基是世界頂級品牌,它在中國本土生產實現“同一品牌同種品質”的目標並 非易事。從試裝的第一天起,曾鵬和組員們一起摸索,通過測量、記錄成車的關鍵功能數據,初步找到了有效控制產品質量波動源的數據化管理方式,並套用相應的工裝、設備和夾具,快速地控制和解決了很多質量問題,使白車身質量控制走上了數據化管理的道路。 作為班長,作為共產黨員,曾鵬總是身先士卒。在試裝初期,一個工位的加工工人因傷無法操作,曾鵬主動接下了他的工作。這個工位工作強度最大,光焊點就有197個,需要翻轉焊鉗至少10次以上。而且,幹完這個工位的活兒,還得馬上跑到下一個工位,那裡還有80多個焊點等著他完成。 就在大切諾基的試裝工作進行到關鍵時期,曾鵬年僅一歲的小孩卻突然患肺炎住進了醫院。在入院治療的7天裡,他始終撲在試裝現場,發起成立設備技改小組,針對影響工作效率的突出問題,開展技改革新,先後完成了13項技改,為批量生產打下了堅實的基礎。想到在妻子懷孕期間就沒有陪她去過一次醫院,仍然無法守護兒子,他流下了眼淚。“中國製造”的世界頂級產品緩緩駛下生產線,在曾鵬領導的裝焊生產線上,加工焊點合格率達到95%以上,白車身三坐標檢測失分值從試裝階段的95-110分降低到批量生產的35分左右,好於“美國原裝”最低失分值40分的水平。
大切諾基成功了,而曾鵬卻離開了。2002年底,另一個重要崗位在等待著他,公司從日本三菱公司引進的帕傑羅即將上馬了。
目標管理
組織好帕傑羅的生產,遠比大切諾基更複雜。由於裝焊車間已經採用柔性化生產,班組成員是由各工段抽調而來,這給班組管理帶來很大難度。
為了解決這個難題,提高班組的凝聚力,曾鵬總結過去的經驗,研究制定了班組八大員矩陣管理模式,確定安全員、質量員、工藝員、設備員、零件協調員、衛生員、宣傳員、ISO9000記錄員等生產線八大員。同時,他還建立了以培訓為載體的“矩陣管理圖表”控制體系,圍繞影響生產的“人、機、料、法、環”五個因素編制出班組矩陣管理圖表,由八大員根據員工的日常工作狀況進行記錄,從而促進班組整體工作目標的實現。
但是,他的這些想法和做法卻引起了非議,有人說他這是在抖機靈、出風頭。他耐心地與組員們交流溝通,告訴大夥,要想實現“同國際接軌,與世界同步”的戰略,即使是當工人,也必須學會套用科學的管理法。曾鵬的做法最終得到了員工們的認可,大家積極參與到班組的各項管理工作中,分別制定出帕傑羅項目全局發展目標和階段性工作目標。這種“目標管理”方法的實施,使大家能夠根據實際情況及時調整工作重心,有針對性、預見性的開展工作,使班組管理形成了閉環式螺旋上升的態勢。
在質量控制方面,曾鵬在質管組人員的配合下摸索出六個關鍵功能尺寸,每天對全車進行徹底檢查,測量數據,控制波動源。經三坐標數據檢測,白車身功能尺寸最高得分達到86.7分,遠遠超過了日本三菱公司要求的75分標準!
2003年6月,當從日本三菱公司引進的又一個新產品歐藍德計畫將於2004年1月份正式投產之時,人們把擔任班長的最佳人選自然鎖定為曾鵬。
成就與榮譽
攻克瓶頸
有了大切諾基和帕傑羅投產時積累的豐富經驗,曾鵬從事歐藍德生產線的管理,可謂得心應手。但是,他仍然不敢掉以輕心。
歐藍德一投放市場立刻受到了廣大消費者的追捧。曾鵬將提高勞產率、提高產能作為班組工作的重點。他在車間技術人員的協助下,先後開展了一系列工藝改造項目,極大地縮短了腳踏車生產時間,僅用四個月就突破了原設計能力,實現了日產120輛的目標。
在曾鵬的帶動下,班組一年共提出合理化建議147條,開展技改技革項目17項,減少無效工作時間12400分鐘,消除走動浪費15萬米,節約螺栓保護套5萬根,提高工作效率25%。由於受工作區面積限制,一個工位和下道工序相距了18米,組員每送一次零件,往返就要走動36米,一個班下來,無效走動達到近500米,一年就是9萬多米。如果將工裝移位卻要牽扯到水、氣、電等各種專業技術。曾鵬將合理化建議及時向上匯報,在車間技術人員以及維修師傅們的大力支持幫助下實施技改,一舉消除了這個瓶頸工位。
歐藍德市場熱銷,曾鵬的頭腦卻異常冷靜,他深知用戶的評價,公司的命運,就在他的手中。從批量生產開始,他就在班組內大力推行了“質量系統檢查法”,每3輛車一剔試,每輛車一檢查外觀。日方專家是挑剔的,但他們面對的事實是,中國生產的歐藍德,塗膠合格率達到100%,一次交驗合格率平均值達到99%以上,焊接合格率達到99.75%,白車身三坐標全年測量平均值達到82分。他們承認,歐藍德白車身綜合質量已經達到、甚至超過了日本原廠的質量水平。
著書立說
幾年來,曾鵬在新產品的引進投產中認識了很多外國專家,學到了很多知識和先進的工作方法,促進了他的管理能力,但也讓他感到了自身知識水平的不足。為了提高自身和組員們的文化素養,他在班裡先後開展了青年讀書角、青年文化角、裝焊實用英語100句等多項活動。從2001年開始,曾鵬還利用業餘時間報考了大專院校,學習電子信息和英語,進一步開闊了思維。
曾鵬積累了寶貴的經驗和第一手材料,為了把這些經驗和方法總結出來,他和另外一名組員合作編寫了25000餘字的《新產品的柔性化管理》技術資料,將新產品的試裝投產歸納為生產前準備、試裝生產和批量生產三個階段,詳細描述了班組在不同階段的工作目標、工作重點、步驟、注意事項以及每項工作制度和檢查控制的圖表,成為裝焊車間新產品投產平台中的一個重要組成單元。