塑件分析
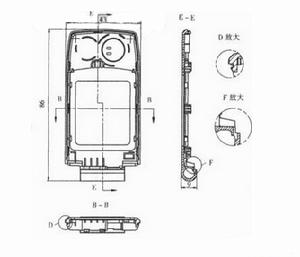
設計方案
手機翻蓋外形尺寸小,結構複雜,需多個抽芯結構。另外塑件對外觀質量要求較高,而所用的材料流動性較差,注射壓力應保證充分,因此採用1 模1腔的模具結構,且使用熱流道澆注系統。為了節省成本和減小加工難度,成型零件的型腔和型芯均採用整體嵌入式的結構。對於產品周邊的內凹搭扣和轉軸孔,需要設計斜導柱抽芯機構來滿足成型要求。對於轉軸下面的由內向外凹的結構,可以採用斜滑塊內抽芯機構來解決。
設計步驟
澆注系統由於手機翻蓋材料為PC + ABS ,材料的流動性較差,而壁厚僅為1. 2 mm, 如果採用普通的澆注系統成型較為困難,且容易出現凹陷、縮孔甚至充模不足的現象。該模具主流道選用直澆口形式,一方面減小了壓力損失, 提高了質量,另一方面還可節省材料,提高效率,縮短注射周期。
根據塑件的結構特點, 分流道開設在顯示屏的碰穿面上, 採用2 點進澆, 平衡式布置, 以保證塑膠熔體能夠在減少熔接痕的情況下,流程儘可能短,充模儘可能快。
因為塑件外觀質量要求較高, 所以進料位置不能開設在塑件的外表面, 可以採用潛伏式澆口將進料位置設在塑件內表面。一方面可以保證不影響塑件的外觀, 另外還可以實現在頂出時澆口的自動斷開, 避免人工清理, 提高了效率。為了方便製造, 將澆口開設在2 個對開的鑲件17 上。
因為手機翻蓋尺寸小,設計的斜滑塊尺寸也小,如果採用普通的斜滑塊結構,將不能保證斜滑塊的強度。因此模具的斜滑塊內抽芯機構設計如圖3 所示,由導桿14、導板15 和斜滑塊16 構成。其中,導桿14 通過螺釘, 穿過調整塊13 ,固定在推板12 上,在導桿的頂端開設T形槽,而在斜滑塊底端加工出和T形槽相配合的結構,使得斜滑塊可以在T形槽內自由滑動。為了保證導桿運動精確而又想降低加工難度,在導桿頂端的外圍,增設了1 塊導板15 ,作為導桿上下運動時的導向板。為了防止導桿超行程運動,在推桿固定板11 上方還增設了2 塊限位塊10。
導柱設計因為手機翻蓋在3 個方向均有內凹的搭扣, 頂部的轉軸孔也需要側向抽芯, 於是模具在3 個方向設定了斜導柱抽芯機構。這3 個斜導柱抽芯機構均採用斜導柱在定模,滑塊在動模的結構,其成型型芯用螺釘固定在滑塊的相應孔中,分布如圖4 所示。對於轉軸通孔處,由於轉軸孔既有尺寸要求,又有同軸度要求, 為了保證模具閉合和注射時轉軸孔的兩碰穿型芯不發生傾斜變形, 轉軸孔型芯在結合處採用了如圖4 放大處所示結構, 在小型芯末端增加1 個圓錐型的小凸台, 對凸台頂面邊緣倒圓角以方便導入,而在大型芯上, 加工出一個與小型芯凸台基本尺寸相同的圓錐孔, 二者之間採用一定的間隙配合。模具工作時, 小型芯前面凸台插入大型芯相應孔中,實現碰穿處結合的穩固。
工作過程
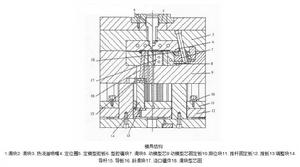