工作原理
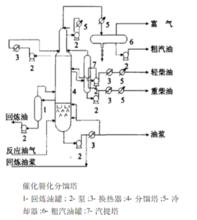
催化裂化分餾塔的基本原理是利用氣液相中各組分的相對揮發度的不同進行分離。在塔中,蒸氣從塔底向塔頂上升,液體則從塔頂向塔底下降。在每層板上氣液兩相相互接觸時,氣相產生部分冷凝,液相產生部分氣化。由於液體的部分氣化,液相中輕組分向氣相擴散,使蒸氣中輕組分增多;而蒸氣的部分冷凝,使蒸氣中重組分向液相擴散,液相中重組分增多,進而使同一層板上互相接觸的氣液兩相趨向平衡。
基本條件
(1)必須有能夠使氣液充分接觸,進行相間傳熱和傳質的場所,即塔盤(或填料)。
(2)每層塔盤上必須同時存在著組成不平衡的氣(上升油氣)液(下降回流)兩相。為了保證精餾每層塔盤上都有上升油氣,就需要提供熱源;為了使塔盤上有下降回流,塔頂及各全抽出斗的下方均需有外回流打入,以使其他塔盤上有內回流。
(3)為了達到精餾的目的,不僅要有塔盤,而且要有一定的塔盤數;不僅要有回流,而且要有合適的回流量。
分餾效果
分離精確度在精餾過程中也叫分餾精確度,用來表示分餾塔的分餾效果。
對二元系來說,指的是輕、重兩組分間是否達到有效的分離。對多元系,則是指輕、重關鍵組分之間的分離程度。
對複雜系來說,兩個相鄰餾分之間的分餾精確度,通常用這兩餾分的餾分組成或蒸餾曲線的相互關係來表示。倘若較重餾分的初餾點高於較輕餾分的終餾點,則稱這兩個餾分之間有一定的“間隙”;反之稱為“重疊”。重疊意味著一部分輕餾分進入到重餾分里去了,或者是一部分重餾分進入到輕餾分里去了。其結果,既降低了輕餾分的收率又損害其質量。顯然,重疊是由於分餾精確度較差所造成的,而間隙則意味著較高的分離精確度。間隙愈大,說明分餾精確度愈高。
影響因素
1、混合物氣液兩相的物理性質。
主要有溫度、相對揮發度、擴散係數、表面張力和重度等。
液體粘度高,傳質困難,板效率則低;相時揮發度大,液相傳質阻力大,使效率降低。氣液相的擴散係數及表面張力對板效率均有一定影響。
2、精餾塔的結構
主要有出口堰高度、液體在板上的流程長度、板間距、降液部分大小及結構,還有閥、篩孔、或泡帽的結構、排列與開孔率。
1)出口液流堰高度
出口液流堰高度增高使板上的液層高度及滯液量增加,增大兩相接觸時間和傳質面積,有利於板效率提高:但出口液流堰高度的增高,將使蒸氣流經塔板阻力增大,霧沫夾帶也有所增加。
2)塔板上液流流程長度
塔板上液流流程長度增大,將減少板上的返混,使板效率增高:但進出口堰間的液面落差增大,特別對液流量大,結構複雜的塔板尤其如此,必將惡化氣流均勻分布。
3、操作變數
主要有氣速、回流比、溫度及壓力等。
1)蒸氣速度
它對於板效率產生複雜的影響。一方面,隨氣速的增高,傳質係數、傳質界面增大,漏液可以消除,有利於效率的提高;另一方面,隨氣速的增高,霧沫夾帶,板上流體混合程度的增強,兩相接觸時間變短,對效率起不利的影響。
2)液體流率(單位塔截面的液流量)
對板效率也產生複雜的影響。隨液體流率增大,液體與氣體接觸時間減小,塔板上液體進口與出口處產生液面落差增大將影響氣流均勻分布,隨液流夾帶入下面塔板的泡沫量可能增多,這些將使板效率惡化;但液體流率的增大,返混情況將有所改善,傳質係數和傳質面積將有所增大。
工藝特徵
1)分餾塔底設有脫過熱段,處理物料為複雜混合物;
2)塔頂多採用循環回流,有側線抽出;
3)大量採用中部循環回流來控制各段溫度;
4)從塔底進料,進料為過熱油氣。
與其他分餾塔區別
(1)有脫過熱和洗滌粉塵的油漿換熱段
催化裂化分餾塔的進料是高溫的,帶有催化劑粉塵的過熱油氣。因此在塔底設油漿循環回流以冷卻過熱油氣並洗滌催化劑。
(2)全塔餘熱敏大
催化分餾塔的進料是450℃以上的高溫過熱油氣。因此,在滿足分離要求的前提下,儘量減少頂部回流的取熱量,增加溫度較高的油漿及中段循環回流的取熱量,以便於充分利用高能位熱量換熱和發生蒸汽。
(3)系統壓降要求小
為提高氣壓機入口壓力,降低氣壓機的能耗,提高氣壓機處理能力,應儘量減少分餾系統的壓降,包括大油氣管線的壓降、各塔盤的壓降、分頂油氣管線和冷凝冷卻器以及從油氣分離器到氣壓機入口的壓降。努力減少系統壓降可表現在以下幾個方面:
①採用固舌形塔盤。
②不宜過多增加塔盤數。因為催化裂化產品的分離要求比較容易滿足,因此不必增加塔盤。一般在28~32層。
③減少分餾塔頂油氣管線及冷凝冷卻器的壓降。因為伴隨再生催化劑帶入反應系統的惰性氣體以及反應產生的低分子量的氣體,在分餾塔頂冷凝冷卻器的操作條件下不能冷凝下來,因此如果採用冷回流而不是頂循環回流,將不僅降低冷凝冷卻效果,而且使這部分及塔中的壓降增加。採用頂循環回流還可以使塔頂冷卻面積減小,水、電等消耗降低,並回收部分低溫位的熱能。
④有吸收油流程。在吸收穩定系統巾要用輕柴油或相當於輕柴油的餾分,在再吸收塔內對吸收解吸塔頂的貧氣進行吸收,以減少隨乾氣帶走的汽油量。吸收後的富吸收油再返回分餾塔。