高碳錳鐵簡介
高碳錳鐵是由錳、鐵組成的合金。錳鐵根據其含碳量不同分為三類:低碳類:碳不大於0.7%;中碳類:碳不大於0.7%至2.0%;高碳類:碳不大於2.0%至8.0%。
用途
電爐高碳錳鐵主要用於煉鋼作脫氧劑、脫硫劑及合金添加劑,另外隨著中低碳錳鐵生產工藝的進步,高碳錳鐵還可套用於生產中低碳錳鐵。
高爐高碳錳鐵:用於煉鋼作脫氧劑或合金元素添加劑。
生產方法
高碳錳鐵的生產方法有高爐法和電爐生產的,下面分別介紹這兩種方法的特點。
高爐法
高碳錳鐵最早是採用高爐生產的,其產量高,成本低,目前國內外還在廣泛用。我國山西東方資源發展有限公司為高爐生產高碳錳鐵的定點廠家。
高爐法是把錳礦、焦炭和石灰等料分別加入高爐內進行冶煉、得到含錳52%~76%/含磷0.4%~0.6的高爐錳鐵。由於高爐與電爐冶煉高碳錳鐵唯一的區別是熱源不同,所以兩者的爐體結構、幾何形狀及操作方法不一樣,但兩爐子冶煉高碳錳鐵的原理是相同的。
但是,兩種爐子使用同一種錳礦冶煉使得到的產品磷含量不一樣,高爐產品越高於電爐產品0.07%~0.11%。這是由於高爐冶煉的爐料組成中的焦炭配量為電爐冶煉時的5~6陪,因此焦炭中有更多的磷轉入合金內,而且高爐冶煉時的爐膛溫度較低,因而冶煉過程中磷的揮發量較電爐低約10%。
電爐法
電爐法冶煉高碳錳鐵有三種方法。
1)無熔劑法。對於含氧化錳較高的富錳礦,可以用無熔劑法冶煉錳鐵、冶煉時爐料中不配加石灰,設備和操作類似矽鐵,並且是在還原劑不足的條件下採用酸性渣操作,爐膛溫度比熔劑法低約1320~1400 ℃,用這種方法生產既要獲得合格的高碳錳鐵,又要得到含錳大於35%、供冶煉錳合金用的低磷、低鐵富錳渣。此時錳的分配如下:入合金率為58%~60%,入渣率為30%~32%,揮發10%。顯然,用無熔劑法冶煉高碳錳鐵必須使用含錳高的富錳礦,並且要求礦中有頗低的磷含量。該法雖然錳的回收率低,但用富錳渣冶煉錳合金時還可以回收絕大部分的錳,其錳的總回收率比熔劑發高。 無溶劑法冶煉高碳錳鐵的過程是連續的,爐料隨著熔化過程不斷加入爐內,料批可由300kg錳礦、60~70kg焦炭、15~20kg鋼屑組成。無溶劑冶煉時,產品單位電耗很低,並且容易生產出低矽的高碳錳鐵,這是因為大部分矽富集到渣中。
2)溶劑法。溶劑法是冶煉高碳錳鐵普遍採用的一種方法。爐料組成中除錳礦、焦炭外,還有石灰、冶煉時採用高鹼度渣操作鹼度,B=1.3~1.4,使用足夠的還原劑,已儘量降低廢渣中錳含量,提高錳的回收率。這種方法用於以貧、富錳礦搭配冶煉高碳錳鐵,以後還要詳細討論這種方法。
3)少溶劑法。這種方法是採用介於溶劑法和無溶劑法之間的所謂“弱酸性渣法”進行操作。該法是往爐料中配加適量的石灰或石灰石,把爐渣鹼度m(CaO)/m(SiO2)或m(CaO+MgO)/m(SiO20)的比值控制在0.6~0.8之間,藉以既能提高錳的回收率,又能獲得含錳25%~30%和適量含CaO的爐渣,把該渣配入冶煉矽錳合金的爐料中,即可節約石灰,又能減少因石灰潮解而增加的爐料粉塵量,從而改善爐料的透氣性。 國外電爐冶煉高碳錳鐵多採用無溶劑法和少熔劑法的酸性法。我國20世紀50年代也曾採用過無熔劑法冶煉,用含錳46%~47%的富錳礦生產出含錳76%80%碳錳鐵,並同時獲得含錳35%~40%富錳渣。但因我國貧錳礦較多,所以目前多採用溶劑法或少量溶劑法。
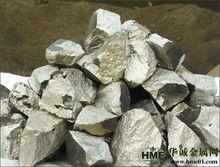
技術情況
現代大型錳鐵還原電爐容量達40000~75000千伏安,一般為固定封閉式。熔劑法的冶煉電耗一般為2500~3500千瓦·時/噸,無熔劑法的電耗為2000~3000千瓦·時/噸。錳矽合金用封閉或半封閉還原電爐冶煉。一般採用含二氧化矽高、含磷低的錳礦或另外配加矽石為原料。富錳渣含磷低、含二氧化矽高是冶煉錳矽合金的好原料。冶煉電耗一般約3500~5000千瓦·時/噸。入爐原料先作預處理,包括整粒、預熱、預還原和粉料燒結等,對電爐操作和技術經濟指標起顯著改善作用。
電爐精煉 中、低碳錳鐵一般用1500~6000千伏安電爐進行脫矽精煉,以錳矽、富錳礦和石灰為原料,其反應為:MnSi+2MnO+2CaO─→3Mn+2CaO·SiO2
採用高鹼度渣可使爐渣含錳降低,減少由棄渣造成的錳損失。聯合生產中採用較低的渣鹼度(CaO/SiO2小於1.3)操作,所得含錳較高(20~30%)的渣用於冶煉錳矽合金。爐料預熱或裝入液態錳矽合金有助於縮短冶煉時間、降低電耗。精煉電耗一般在1000千瓦·時左右。中、低碳錳鐵也用熱兌法,通過液態錳矽合金和錳礦石、石灰熔體的相互熱兌進行生產。
吹氧精煉 用純氧吹煉液態碳素錳鐵或錳矽合金可煉得中、低碳錳鐵。此法經過多年試驗研究,於1976年進入工業規模生產。
設備節能
參數選擇
在原材料和操作工藝相同的條件下,不同的設備參數就會出現不同的冶煉效果,高碳錳鐵的還原溫度較低。爐渣的流動性能較好,一般認為大直徑電極,大極心圓、大爐膛和深爐膛是冶煉高碳錳鐵爐型的特點。
水冷設備
電極水冷系統運轉正常十分重要。電極大套、銅瓦、導電銅管都採用水冷卻。冷卻水進口溫度要儘量低些,出水溫度不宜過高。冶煉廠冷卻水的水質硬度大,水中泥沙容易沉積在大套底部,嚴重影響大套冷卻效果,可考慮採用磁水器軟化處理。應加強備品備件的管理,爭取縮短熱停時間。採用石棉高壓橡膠水管,相比於以前使用普通膠管,大大減少了普通膠管燒壞而漏水故障,每年至少比使用普通膠管減少熱停100 h。再如1號爐爐罩水冷立柱,由於結構不盡合理,剛投產時因上部缺水而頻繁漏水,在2012年和2013年改為磚包柱後問題便得以解決,大大減少了熱停時間。
爐襯
爐襯是爐體重要的部分,因為在使用過程中要承受1 400~1 800攝氏度的高溫,還要承受爐料、高溫爐氣和熔融鐵水的機械沖刷和爐渣的物理化學侵蝕,因而易被熔化、軟化、熔蝕甚至崩裂。若絕熱性能不好,還會增加電能消耗。所以爐襯要用特殊耐火材料和絕緣材料來砌築。
自焙電極
自焙電極的質量取決於電極殼製作、電極糊和電極焙燒。當這3方面質量不能保證時便會發生各種電極事故,如電極欠燒、漏糊、硬斷、軟斷等。輕則降低負荷,重則造成熱停。不僅影響冶煉時間和生產作業率,更重要的是爐底溫度降低。產量明顯下降而電耗上升。因此電極是電爐設備節能的重要方面,必須引起足夠重視 。