概念
軋輥是軋鋼廠的主要生產工具,它是承受軋制壓力的主要零 件。軋輥在使用中主要因表面磨損報廢,而軋輥表層僅占軋輥總 重的10%左右。用堆焊的方法修復軋輥的磨損部位,使軋輥能重 復使用,從而提高軋輥使用壽命的工藝就叫軋輥堆焊。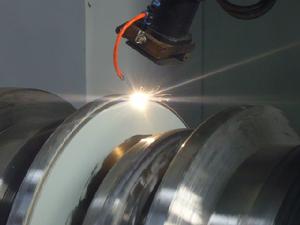
適用範圍
該工藝只 適用於覆蓋厚度為厘米級的鋼軋輥。一般堆焊一次,表面層厚度 可增加35mm。若堆焊軋輥表面約2030mm,則需重複堆焊53546次。經堆焊的軋輥表面硬度(HRC)可達5055,甚至超過 60。用堆焊方法可以對軋輥進行重複修復。軋輥堆焊的工藝簡介
新輥在堆焊前,先對軋輥表層做無損探傷,如果軋輥有裂紋或其他缺陷,及時進行處理。按配輥圖在新輥上車削堆焊預備槽,槽斷面形狀以本道次孔型為準,留出堆焊層及加工餘量。然後用耐腐蝕的鎳電焊條堆焊上“奶油狀”的底層,它可局部地稀釋軋槽表面處的碳,然後用噴丸法消除應力,並對輥身進行加熱,最後用含5%Cr、2%Mo、4%W及其他元素精確配比的實心焊條進行堆焊形成過渡層,堆焊區域的硬度達到HRC55—HRC60。在焊接過渡層時,儘量使材料全部都變成液相,使其晶格結構與鋼輥的的晶格結構相一致相協調,防止在軋制時,堆焊部分剝落。焊接層在軋槽側壁焊接厚度為6mm,圓角及底部處焊接厚度為8mm,因圓角和槽底磨損較大,所以焊接厚度相應大了2mm。焊接結束後,應立即進行退火處理,將軋輥加熱至600—650oC,進行保溫,然後隨爐冷卻至100oC出爐,以消除應力。由於堆焊的材料是經過精確配比而且軋槽堆焊厚度不大,所以堆焊後在提高軋槽強度和硬度的同時,仍然保持鑄鋼軋輥良好的韌性。
軋輥堆焊的實際套用
Φ550車間軋機排列布置為Φ550mm×1開坯機+2立+8平精軋機。開坯後中間坯厚為30mm--34mm之間。開坯的軋制道次為7道,所以Φ550mm開坯軋機軋制負荷較大。在使用鑄鋼軋輥軋制時,由於軋輥硬度只在HRC32--HRC38之間,過鋼量達4000噸軋槽側壁磨損就達2mm--3mm,槽底達4mm--6mm;過鋼量達5000噸時已經無法調整,而末道孔型軋出的鋼料厚度卻已達到了34mm--38mm,而且寬度極不均勻,整條鋼的通條差有時相差6mm,很難保證後道工序所要求的鋼料尺寸,產品質量也難以保證,因此不得不停機頻繁換輥,使軋機的平均作業率僅為70%--80%,嚴重影響軋機產量,且廢品率達到近8%。使用鑄鋼軋輥軋槽表層堆焊的軋輥後,軋槽的耐磨性、抗熱裂紋性能明顯提高。堆焊採用軋輥的軋輥直徑為Φ550mm新輥,這樣連線桿與水平線的夾角趨近於零,使減速機、牙包箱傳遞到軋輥的扭矩非常均勻,軋制速度和軋制力以及鋼料的咬入也都處於最佳狀態,設備運行平穩,軋機在這種狀態下工作效率大大提高,軋制節奏加快。而且新軋輥直徑由未採用堆焊前的585mm改為550mm減少了11.5%的軋輥重量,降低了一次設備投入。軋槽材質硬度達HRC55-60,耐磨性大大提高。
在一個換輥周期內,軋制帶鋼達15000噸,是軋輥軋槽沒有堆焊前的3倍多。而且耐冷熱疲勞性還優於合金軋輥,合金軋輥當溫度過高時,合金的硬度和耐磨性能急劇下降,若長時間冷卻不足,又會造成軋輥表面惡化甚至產生明顯裂紋,影響軋輥使用壽命。而使用鑄鋼軋輥軋槽表層堆焊的軋輥,軋槽堆焊材料性能均勻穩定,軋輥使用一個周期後,軋槽表面較光滑無明顯深溝凸起,無明顯刮痕,無明顯的連續熱裂紋,更無堆焊層剝落、掉塊現象的發生,開坯軋機末道鋼料的料型尺寸精確,且整根鋼的通條差在1.5mm以內,為後道工序的正常生產提供了保證。使軋機的平均作業率達到了90%以上。
另外,在軋輥使用壽命方面,以前使用的鑄鋼軋輥雖有50mm的使用層,但由於軋輥的材質較軟,磨損大,軋制時產生的縱向裂紋較深,軋輥車削三次也就報廢了。而使用表層堆焊軋輥,最多可以使用11個輪次,大大降低了軋輥使用噸鋼成本,使軋輥的使用壽命提高了3倍多。