概述
在生產過程中,人們常常對實際加工出來的一批工件進行檢查測量,運用數理統計方法加以處理和分析,從中找出規律,找出解決加工精度問題的途徑,並控制工藝過程的正常進行。人工檢驗和統計分析是質量控制的傳統方法,這是一項精細、單調而且費時的工作。在統計採樣處理中會有少量不合格品漏檢而進入合格品中。實際上,在生產和檢測過程中統計採樣處理經常讓平均不合格率保持在某一百分比以下,這就是說允許工件合格率百分比略低於100%。
傳統質量檢驗的另一個問題是事後檢驗,即零件質量是在加工完後確定的。如果零件不合格,就需要返工或報廢,而返工費用往往比正常加工費用大。
日益激烈的市場競爭和日趨複雜的產品質量需求清楚地表明,必須將信息技術、計算機技術引入到企業質量管理與控制當中,才能真正有效地實現企業現代化質量管理與質量保證.近年來,以計算機技術套用為基礎,以先進的質量控制技術、信息處理手段和現代質量管理方法緊密結合為特點的計算機輔助質量控制(Computer Aided Quality Control) 和計算機輔助質量控制系統(CAQ,Computer Aided Quality System)已經成為企業中的有機組成部分,構成了現代質量管理的新特點.在企業保證產品質量,提高企業素質,贏得市場競爭等方面正發揮著越來越重要的作用。
發展
計算機輔助質量管理顧名思義,是套用現代計算機技術為依據設計和運作的一整套質量管理技術體系。它是現代質量管理和計算機技術相結合的產物。隨著電腦技術和能力的迅猛發展,特別是散電腦/機的問世和普及它的套用延伸到了幾乎所有的領域。例如在製造領域,計算機輔助設計,計算機輔助製造和計算機輔助測試等項技術早巳陸續得到廣泛套用。在管理領域,由於各項管理因素及其影響的複雜性不定性甚至不可知性,在相當長一段時間內計算機的套用停滯不前。
現代模糊技術的突破不但消除了這種障礙,還充分顯示計算機在解決管理性問題上的巨大優勢,產生了計算機輔助信息分析,計算機輔助決策,計算機模擬方案評價等管理技術,並得到日益廣泛的套用。在質量管理領域,人們把控制圖,相關圖和試驗設計等各種質量管理工具與計算機的套用結合起來,大大提高了套用效率。不過那時由於質量管理技術本身的系統性還不是銀強以及計算機硬體普及性的限制等,與其它領域比,計算機在質量管理上的套用顯得有點"零打碎敲",還有快形成系統的技術。8年代中後期質量體系概念的最終形成,特別是ISO9000質量體系國際標準的制訂頒布,為計算機在質量管理方面的系統套用即提供了框架。
關鍵技術
1、研究技術工作
(1)在對抽樣檢驗的理論和套用技術深入研究的基礎上,實現抽樣檢驗方法及套用嚮導的程式化;
(2)對多品種小批量生產模式下的質量管理與控制策略及套用技術進行較為系統地研究,並對部分小批量質量控制方法實現了程式化;
(3)在對控制圖的理論及套用技術深入研究的基礎上,對通用控制圖進行了研究,並實現程式化;
(4)深入研究選控圖的理論及其套用技術;
(5)對實驗設計、可靠性分析的理論及其套用技術進行了研究和探討。
2、抽樣檢驗的研究
對抽樣檢驗的研究,創始於20世紀20年代。抽樣檢驗的目的是“通過樣本判斷總體”,而其期望則在於“用儘量少的樣本量來儘可能準確的判斷總體(批)的質量”。統計抽樣檢驗的優越性體現在可以儘可能低的檢驗費用(經濟性),有效的保證產品質量水平(科學性),且對產品質量檢驗或評估結論可靠(可靠性),而且實施過程又很簡便(可用性)。目前,抽樣檢驗的套用領域已深入到機械、電子等國民經濟的各個部門。 本論文在對抽樣檢驗的理論及系列標準的深入研究的基礎上,進一步剖析了常用抽樣檢驗方法的特點以及相關規律性,基於C++Builder的面向對象技術以及Access資料庫開發技術等,實現了常用的抽樣檢驗標準及套用嚮導的程式化,建立了計算機輔助抽樣檢驗及套用嚮導的模組及系統,並提供系統 的線上幫助功能,不僅填補了國內對此類研究的一項空白,而且方便用戶使用 抽樣檢驗標準,提高產品的生產質量,促進抽樣檢驗的推廣套用。
3、多品種小批量生產模式下質量管理與控制的研究
市場競爭日趨激烈,顧客對產品的需求日益呈現出多樣化和個性化的發 展趨勢,促進企業打破傳統的單一品種、大批量生產模式,轉向了多品種、小批量生產。 針對多品種小批量的生產特點:加工零件少,樣本數據量少,不足以構 成足夠的數據進行質量控制,如繪製控制圖等,在本論文中提出生產加工過程 數據繼承的觀點。根據成組技術的原理,利用加工過程的相似性,將加工零件分類成族,測量得到同一加工族的產品數據。如果本次加工的零件的數據量不 足,就採用繼承的方法,從歷史的數據中調取一部分數據進行補充,使單件小 批量的生產模式可以採用大批大量生產模式下的各種質量控制方法。 在利用成組技術構建數據模型的基礎上,對小批量控制圖的理論及其應 用技術進行了研究,並利用面向對象技術對其實現程式化。
4、控制圖的理論及其套用技術研究
在對控制圖的原理及其作用深入研究的基礎上,進一步最佳化控制圖套用技術,實現了通用控制圖的變換處理及其程式化。所謂的通用控制圖, 就是利用統計學的方法,對質量控制數據進行標準變換,以此改變控制圖界限 非直線的問題,使控制圖更加簡潔、方便、直觀。 在對控制圖套用特點進行全面系統分析的基礎上,對其套用嚮導也進行 了研究開發。車間製造過程是產品質量管理的重要環節,是產品質量問題的主要來源之一。傳統的車間製造過程質量管理存在質量體系不健全、質量數據有效性差、過程統計技術套用不夠、質量監督和質量責任追究不力以及質量決策滯後等問題。這些問題給企業造成了嚴重的質量損失,因此,企業質量管理部門迫切地希望採用一種新的質量管理方法來輔助車間質量管理,提高車間製造過程的質量管理水平。
數據採集
1、 數據採集技術
製造過程質量數據主要來自兩個方面:對零件和產品的檢測和對製造過程的監控。開展質量管理,就是要用數據來提出和解決產品質量的問題,用數據來反映或描述產品質量的變化規律,因此及時準確地獲取質量數據是質量管理取得成功的關鍵。基於MES的車間製造過程動態質量管理系統充分考慮了先進的數據採集技術和工廠的實際情況,採用具有高度適應性和可擴充性數據採集方式,包括自動採集、手工錄入和數據轉換與共享。
(1) 自動採集
系統設有各種接口與不同的數據採集裝置(如計量器、測量器、條碼讀卡機、無線射頻掃瞄器與各類儀器儀表等)相連線,完成各種質量數據(包括外購原材料及零/部件檢測數據、零件加工過程中線上檢測和序後檢測數據、過程狀態監測數據、零件最終檢測數據、裝配過程檢測數據和成品試驗數據等)的自動採集及處理,還可以將分析結果自動反饋到生產設備的控制裝置,實現閉環的質量控制。
(2)手工錄入
考慮到設備、現場條件和成本等因素,並不是所有的產品質檢數據和生產線運行狀態數據都能夠做到自動採集和實時監控,這就需要利用各種手動計量儀或“目測”的方式來進行檢測。系統設定相關質量信息錄入功能,檢測人員“目測”計量儀的讀數,然後通過電腦或信息互動終端進行數據的錄入、處理、傳輸和存儲。
(3)數據轉換與共享
系統之間高度數據共享,可以方便地將產品的CAD、CAPP等各類信息轉換至本系統,或通過共享數據的方式實現對產品質量的全面管理和監控。全面高效的數據轉換與共享能力,可實時地將產品數據存入指定的資料庫,或從資料庫直接讀取所需信息,數據存取時間周期由用戶根據實施需要自行設定。
1)質量參數獲取:在車間製造過程中,要系統地識別、分析產品或零/部件工藝流程,找出影響產品質量的因素,並根據各工序對最終產品質量影響程度的大小及相互關係,繪製關鍵工序流程圖;根據該圖確定質量控制點及關鍵參數,繪製工序質量管理網路圖,對影響產品質量的關鍵工序實施監控。在確定了關鍵工序及其參數後,就要對這些參數進行及時準確地採集和處理,為後續計算、控制和分析診斷做準備。
2)繪製控制圖:根據控制圖使用的目的不同,可分為分析用和控制用兩個階段,因此要分別繪製分析用和控制用控制圖。一道工序的初期或進行系統改進後,總存在不穩定因素,因此,先要繪製分析用控制圖來判斷過程是否受控。在分析用控制圖階段,點出萬方數據界說明過程有異因存在,應積極採取措施分析原因,調整過程,直到剔除所有異因,過程受控。如果過程能力充足,就用穩態下控制圖的控制線控制生產過程;如果過程能力不充足,則要採取措施分析原因,調整過程,然後重新進行過程判斷和過程能力評價。
控制方法
產品質量是其質量特徵滿足顧客需求的程度,質量控制就是採取一定的方法使產品的質量特徵在規定的標準範圍內。對於機械加工系統而言,常用的質量控制方法包括過程改進,線上質量控制和序後質量控制三種。下面對這三種方法作一個介紹和比較。
過程改進是一種消除產生質量缺陷的可能性的質量控制方法。它是通過消除引起過程變化的原因,使過程始終穩定,來保證產品質量特徵在規定的範圍內,達到質量控制的目的。過程改進是控制產品質量的積極方法,也是控制產品質量的最直接的途徑。因為它消除了產生過程變化的根源。一般對於經過改進的過程,不必再進行線上質量控制或序後質量控制。
上述的過程改進是進行質量控制的最佳途徑,但並不是所有的過程變化都可以通過過程改進被消除。對於不能消除的過程變化而言,為了達到優良的質量特徵,往往需要採用線上質量控制技術對過程變化並行控制。所謂線上質量控制就是在生產過程中控制產品質量,即線上地監測過程參數和檢測質量特徵,線上地調整過程參數,使產品的質量特徵在一定的範圍之內。對於經過線上質量控制的過程一般不再需要序後質量控制。
所謂序後質量控制就是序後檢驗和測試,它是在工序完成後對零件進行檢測,剔除不合格品來保證產品質量的控制方法。
線上質量控制方法中,最關鍵的是線上質量數據的採集和過程參數的線上調整。線上質量數據採集完成過程信息和產品信息的收集,經過信號的預處理和數據接口送入控制計算機。計算機根據質量特徵和過程參數的關係,做出對過程參數進行調整的決策,然後控制器通過執行元件完成過程參數調整,實現線上質量控制。線上質量控制系統的框圖6-6所示。
線上質量數據採集方法包括過程參數的監測和線上產品質量檢驗。過程參數監測是通過測量與產品質量特徵有關的參數來實現的,線上產品質量檢驗是在加工過程中或加工工步間隔直接測量產品的質量特徵來實現的。常見的過程測量參數包括切削力,溫度,主軸電機電流變化,振動噪聲信號等。對於線上質量控制一般應建立過程參數和最終產品質量特徵之間的相互關係,通過參數的調整,來保證最終的產品質量。
舉例
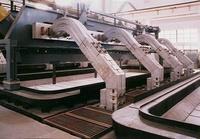
CNC工具機的線上循環測量大部分的CNC工具機都安裝有閉環的位置反饋控制系統,即由安裝在導軌或移動部件的位置感測器測量實際的移動位置,然後反饋到工具機的控制器。如果存在偏差,控制器將自動調節驅動電機的脈衝信號,消除位置誤差。初看起來,這似乎是一種自動過程控制。在每次程式運行中,都能保證零件的正確尺寸。切削刀具的位置,尺寸,形狀也是引起加工質量的主要因素。因此有關刀具狀況的信息也應該及時進入工具機控制器,並進行及時的刀具補償,如果做不到這一點,那么由於刀具磨損,破損,切削力引起的變形等因素產生的影響將導致零件的尺寸誤差。
為了保證生產合格的零件,人們採用了不同的線上質量檢測與控制方法。例如:切削過程的振動和噪聲信號可以用來判定刀具的磨損狀況和破損的產生;主軸電流的變化也可以用作決定刀具狀況的過程參數;也許最有用的是直接測量工件或刀具的尺寸的線上循環測量技術,它是線上質量控制的一個典型實例。
線上循環測量是利用安裝在CNC機應酬上的三維測頭來進行線上質量數據測量和質量控制的。三維測頭是一種表面接觸測量裝置,控制器根據工具機的三個方向的位置移動坐標,得到被測工件的測量結果。圖6-7是安裝在CNC工具機上的三維測頭,三維測頭就像數控工具機的刀具一樣,平時放在工具機的刀庫中,需要檢測時,由機械手取出,安裝在主軸孔中,進行檢測。
線上循環質量控制的原理是在每次關鍵的切削之前,首先測量工件的位置,然後把測量結果送入控制器,控制器根據比較,通過宏指令修改工具機存儲器中的補償表,達到線上補償的目的。線上循環測量利用CNC工具機的坐標控制功能,把零件的加工和檢測集成在一起,可以實現在加工間隔進行線上測量,並可根據測量結果,進行加工補償,實現線上質量控制。
三維測頭除了可以進行線上質量補償控制外,還可以在序前決定工作在工具機上的精確定位和工件的位姿,測量毛坯的餘量,決定加工過程的進給量。
線上循環測量的缺點是加工和檢測套用相同的坐標系統,對於由於工具機定位誤差產生的加工誤差難以檢測。此外,在加工過程中增加檢測工步,因而增加了加工循環的時間。
CNC工具機的熱變形線上補償控制對於CNC工具機而言,熱變形是引起工具機加工誤差的最主要因素之一。據統計,由於熱變形引起的加工誤差占工具機總誤差的40%~70%。消除減小熱變形誤差 的方法包括改進工具機結構,增加複雜熱源控制裝置,選用熱穩定性高的材料和採用先進電機和軸承等等。這些方法一般需要對工具機進行大的改進,投資很大。另一種方法是軟體創成精度方法,即在工具機的硬體結構不變的情況下,通過檢測工具機的熱狀況,並通過軟體的方式對由於熱變形引起的工具機加工誤差進行補償。
補償工具機的熱變形誤差目前前沒有完全被工業界所接收,這是因為目前的CNC工具機的控制器一般不具備複雜的實時誤差補償能力,另一方面要進行工具機熱誤差的線上測量和建立工具機的熱誤差模型都是十分複雜困難的問題。
近年來,人們通過增加外部微機來線上測量工具機的熱狀態,並通過軟體創成精度的方法實現了工具機熱變形誤差的補償控制。
線上熱變補償控制原理是首先測量工具機的熱狀況,把測量結果送入計算機,根據熱誤差模型計算熱變形補償量,然後把補償信號送入工具機的控制器,通過執行檔案完成熱變形誤差補償控制。熱變形補償控制的實施主要有兩種方法,一是通過模擬量直接修改工具機伺服系統迴路的模擬電壓信號,另一種方法是通過CNC的數字串列口修改工具機的數控程式。 它是通過分布在工具機上的熱電偶線上實時測量工具機的熱狀況,並建立基於神經網路的熱誤差模型來進行熱誤差補償控制的。實驗證明,該熱變形線上補償系統取得了較好的補償效果。