內容簡介
並不是所有的企業都適合導入JIT,但每個企業一定都能導入TOC的生產及供應鏈解決方案,尤其是中小企業。中小企業一方面需要滿足下游成品客戶的JIT要求,另一方面也是為了迎頭趕上JIT的營運績效。TOC特別適合產品少量多樣的經營環境。TOC是除了JIT方式能達到精益生產的另一個可選的途徑,企業透過精益TOC及供應鏈解決方案就可以達到精益生產的目標。
TOC將成為未來生產管理的主流方法,因為它簡單易行,可以在短時間內部署運行,並大幅降低庫存、降低營運資金需求、縮短交期、提高交期達成率及提高生產力,是企業不失去賺錢機會的生產系統。
高德拉特博士所著《目標》、《絕不是靠運氣》和《仍然不足夠》均是暢銷小說,讀者受到故事情節的激勵,可能想導入基於TOC的管理、生產系統,但缺乏實施細節的指引,特別是關於如何做、實際操作的指引,而《精益TOC實務指南》的目標即在提供實踐所需的細節。《精益TOC實務指南》是企業導入TOC的指導性書籍,具體說明如何實施TOC生產及供應鏈解決方案,如何利用價值流圖、品質工具、IE手法及如何結合LEAN及6sigma,最終達到精益生產境界。
作者簡介
趙智平,作者畢業於中國台灣聖約翰科技大學機械工程科系,通過了品質學會CQT品管技術師考試,參加過中國生產力中心(CPC)第二屆TQA顧問師班。
早年任職台灣國勝企業製程及研發工程師;
台灣迪吉多計算機品管工程師及質量總監生產副總等職務;
歷任智嘉軟體科技(深圳)有限公司總經理,
深圳麥金士企業管理諮詢有限公司生產管理研究院院長,TOC技術研發中心總經理
現任:自由講師,獨立TOC生產管理諮詢項目顧問,中國人民大學MBA研修班TOC生產管理授課講師,香港亞洲商學院EMBA和MBA研修班生產運營管理課程授課講師。眾多企管顧公司生產管理類課程專業老師。
主要著作 精益TOC實務指南(2009-12-1) 出版社: 深圳出版發行集團,海天出版社
主要專長:
ISO 9000、ISO/TS 16949質量管理系統規劃;基於TOC的生產管理系統(DBR/SDBR);基於TOC的供應鏈解決方案(TOCR);CCPM項目管理;TLS(TOC-Lean-6Sigma)生產系統;流程管理(BPM)/流程改善(BPI)/流程再造(BPR)
諮詢項目經驗
野寶車料(深圳)有限公司生產、品質、供應鏈流程改善專職特聘諮詢顧問2年
斯比泰電子(深圳)有限公司生產、品質、供應鏈流程專職特聘諮詢顧問2年
力野精密工業(深圳)有限公司 生產、品質、IE、供應鏈流程職特聘諮詢顧問2年
東莞富華電子有限公司; 績效、生產、品質、IE、供應鏈流程職特聘諮詢顧問2年。
佛山奧美鋁業有限公司績效、生產、品質、IE、供應鏈流程職特聘諮詢顧問4年。
主講課程:
基於TOC技術的套用課程:
基於TOC的生產管理套用實戰
基於TOC的供應鏈管理實戰
基於TOC的準交期管理培訓
基於TOC的精益生產與規劃
關鍵鏈項目管理(CCPM)
質量管理工具類課程
FMEA-潛在失效模式分析
DOE-實驗設計與田口方法
G8D-福特問題分析與解決技巧
田口實驗計畫法(TM)
製程質量規劃流程
變異、管制圖與製程能力分析
七步QIP質量改善法(品管七大手法)
IE改善系列課程
MOST-工時測定與預定工時法
高效生產規劃與價值流管理
TPM-全面生產設備與全員維護
生產廠線分析與平衡管理
現場管理IE操作實務
工廠布置與精益生產
工作抽樣與IE改善流程
生產管理幹部技能系列課程
生產管理幹部能力培訓
TWI-傑出班組長管理技能培訓
管理問題思考與衝突解決
授課方式:以工作坊的形式展開,啟發式講授、互動式教學、小組討論、真實實戰案例分析、角色扮演、情景模擬、實戰管理指導和經驗分享、導師多年的工作運營工作經驗和從事職業顧問案例開放式與您分享。趙老師更多角色是教練及輔導者,引導學員利用課堂知識解決問題。
講師風格:講師行業經驗豐富,可針對實際狀況進行解析;授課講師豐富的實務經驗與操作手法使學員能即學即用。針對個案進行分析與研究,理論與實務能充分結合,授課嚴謹務實專業。
客戶點評:台灣實戰生產管理運營-TOC套用專家,案例全來自親自指導和輔導的真實案例,是一位非常專業和務實嚴謹的資深台灣老師,善於對實際問題提出解決方案的專家,在諮詢輔導方面以追求實際效果為唯一目標,部分諮詢項目可以按照諮詢效果付費,專注為客戶創造價值。
輔導及授課企業上百家
鞋業:宏業鞋業、港台鞋業、創信鞋業、君穎橡塑、中力鞋材、裕元鞋業
印刷電路板:鴻達印刷電路、永昌益、聯橋電子、光翔電子
電器行業: 國潤電器、翠寧電子、大雅電機
五金製品 :建興五金塑膠、富瑋五金
電子組件:國巨電子、詠得電子、正和電子、誠信電子、高智電子、
梅記精密、海韻電子、藝昌電業、天祥電子、惠達電子、大來電子、
上海飛利浦電磁、恆忻電子
3C及外圍 產業:東聚電業、致伸科技、奇聯電子、百升電子、
深圳富士康、崑山微星電子(MSI)、深圳全錄
化工 行業:立邦漆、南璋塗料、東洲油脂煉油廠
製衣/手袋: 三暉綜合、寶島手袋、中威日用品
機械設備製造行業 :旺昌機械、馬利新菱
玻璃產業: 深圳信義玻璃
五金機械加工行業:野寶車料、力野精密、澳美鋁業
汽車製造及配件 行業:方浩汽車配件;正新輪胎
家電製造:廣東萬家樂 電力設備:海興電力科技股份有限公司
圖書目錄
第1章 在瓶頸作業中獲得最大的產出報酬
企業的目標只有一個,就是“賺錢”
賺錢的公式,利潤=售價-成本
消除匕大浪費
導入JIT及時生產制的條件(門檻)
我們需要一套能夠在短時間內迎頭趕上的方法
賺錢的策略地圖
和賺錢有關的決策與慨念
降低成本還是增加產出/收入為為先
TOC的產出觀
TOC財務指標
TOC作業指標與財務指標的關係
產出會計的套用例:在瓶頸中獲取最大的報酬
以TOC的生產及供應鏈解決方案,獲取客戶芳心
可行願景
第2章 訂單資源規劃
訂單審查的目的及重要性
建立訂單資源規劃模型的影響因素
了解顧客的交貨前置期
以小批量移轉縮短製造周期
製造周期效能
儲備庫存以縮短交貨前置期
負荷審查
計畫負荷
交期審查
限制理論簡介
限制理論,五個聚焦步驟
系統限制損失一小時,整個系統損失一個小時的產出
掌握了系統的限制,就掌握了系統的槓桿點
從局部最佳化轉變為全局最佳化的步驟
TOCF廣泛地在不同領域存在不同的套用
第3章 DBR是TOC生產管理的解決方案
DBR生產管理體系在短時間內的改進績效
DBR模型
DBR解決方案的目標
DBR管理模型
構建DBR生產管理系統
步驟一:確認——系統的限制(最弱的環節)
步驟二:剝削——充分利用系統的限制
步驟三:全力配合——保護系統的限制
步驟四:鬆綁——提升系統限制的能力
步驟五:如果限制在步驟四被打破,則重回步驟一,而不要讓惰性成為系統的限制。不要停止!
S—DBR
S—DBR的交期審查
DBR生產系統的精簡法則
POOGI
對系統限制的持續改善循環
分析緩衝進行持續改善
強迫壓縮緩衝進行持續改善
如何運行POOGI
第4章 TOC的供應鏈解決方案
訂單執行資源規劃
儲備庫存的衝突
化解衝突
原物料庫存解決方案——補給(REPLENISHMENT)
補給方式
原材料採購的困境與因應
補給的管理模型
補給的配置
緩衝存量的構成
補給的緩衝管理
庫存緩衝狀態
原材料/外購品補給小結
庫存製造MTS的解決方案補給製造MTR
庫存製造(MAKE-TO-STOCK,MTS)
工廠及供應鏈的關係
補給製造(MAKE-TO-REPLENISH,MTR)
補給製造的模型
補給製造的配置(CONFIGURATION)
補給製造的緩衝管理(BUFFERMANAGEMENT,BM)
兩個衡量指標
產出一元天(THROUGHPUT-DOLLAR—DAYS,IDD)
庫存一元天等待(INVENTORY-DOLLAR-DAYS,IDD)
立可得製造(MAKE-TO-AVAILABILlTY,MTA)
分銷系統
供應鏈管理的挑戰
補給是TOC在分銷中的解決方案
第5章 TOC生產管理體系在不同製造業的套用例
單面PCB印刷電路板廠的套用例
PCB單面板的製造流程
工廠布置型態:零工式布置
訂單資源配置
改善前問題描述
聚焦五步驟
邁向精益之路
注塑廠帶成品組裝線的套用例
從注塑到成品組裝的製造流程
……
第6章 TOC與價值流分析
第7章 TOC與品質規劃
第8章 TOC、一個流與產線平線
第9章 TOC的履單流程
第10章 TLS-TOC-LEAN-6SIGMA
參考文獻
序言
精益生產(LeanManufacturing),以JIT的路數,是目前各大企業爭相引入的生產系統,但JIT的門檻高且對少量多樣的產業其適合性有待討論。並不是所有的企業均能或適合導入JIT,但每個企業一定都能導入TOC的生產及供應鏈解決方案,尤其中小企業更應導入TOC的生產及供應鏈解決方案,一方面因應下游成品客戶的JIT要求,另一方面讓我們迎頭趕上JIT的營運績效。TOC特別適合少量多樣的經營環境。TOC是除了JIT方式能達到精益生產的另一個可選的路數,透過精益TOC生產及供應鏈解決方案達到精益生產的境界。
筆者以顧問師的角度指出,TOC將成為未來生產管理的主流方法,因為它簡單易行,可以在短時間內部署運行,大幅降低庫存自系統釋放現金、降低營運資金需求、縮短交期、提高交期達成率及提高生產力,是企業不失去賺錢機會的生產系統。
高德拉特博士所著《目標》、《絕不是靠運氣》和《仍然不足夠》均是暢銷小說,讀者受到故事情節的激勵,或想導入基於TOC的管理、生產系統,但缺乏實施細節的指引,即,如何做、實做的指引,而本書的目標即在提供實踐所需的細節。本書是企業導入TOC的指導性書籍,以顧問師指導企業的角度,具體說明如何實施TOC生產及供應鏈解決方案,如何利用品質工具、IE手法及如何結合LEAN及6Sigma,最終達到精益生產境界,甚至不用聘請外部顧問即可按本書的內容自行實施,建立所需的流程。
所以,筆者從企業本質“獲取利潤”出發(第一章),說明TOC是一個以“獲取利潤”為導向的生產、供應鏈管理系統,並以策略地圖的財務構面目標來佐證,Toc和策略地圖及TD—ABC(以時間驅動的作業基本成本制)三者對賺錢的想法是一致的:在瓶頸作業中獲取最大的利潤。
文摘
這不禁令人想起並歸功於豐田式生產系統(Toyola’s Production svstem TPS)或精益生產(Lean Manufacturing,LM),我們稱之為現今成本最低的生產系統及其致力消除七大浪費所做出的努力。
消除七大浪費
我們必須消除的七大浪費:
1.生產過量:比你所需要還要多的產出、空間、產能等。
2.存貨過多:比你所需要還要多的物料、在制品(WIP)等。
3.搬運:一個步驟結束與下一步驟開始之間的距離過長。
4.等待:瓶頸,事情未準備好。
5.不必要的動作:長距離的伸取、複雜的移動、無效率的步伐。
6.過程太多:不必要的步驟,無謂的儀式。
7.矯正:不良品的重作、報廢與丟棄、補救措施。
在七大浪費的基礎下,我們另外增加兩種必須消除的浪費:
1.複雜化:第一次沒做對時,所牽涉的所有浪費。
2.層級化:加在現場上無用的、不必要的限制。
導入JIT及時生產制的條件(門檻)
但是,導人豐田式生產系統或精益生產是有門檻的,世界級改善專家今井正明在其著作《現場改善》一書中明確指出導入JIT及時生產制的條件(門檻):
1.各站的製程與良率要穩定,才能保持整條線的堪用率。
2.設備的可靠度要穩定,設備故障所損失的時間,是無法彌補的。
如圖表1.1所示,我們計畫將零工式布置的腳踏車生產線布置成U型單件流(One Piece Flow)生產線,八個工作站的專用線,在成線之前每一工作站的首次良率(FTT)要在99.999%以上,如此,才能維持整條線在99.992%的堪用率(如果是99%時,則只有92%的堪用率)。
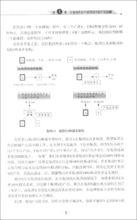
插圖: